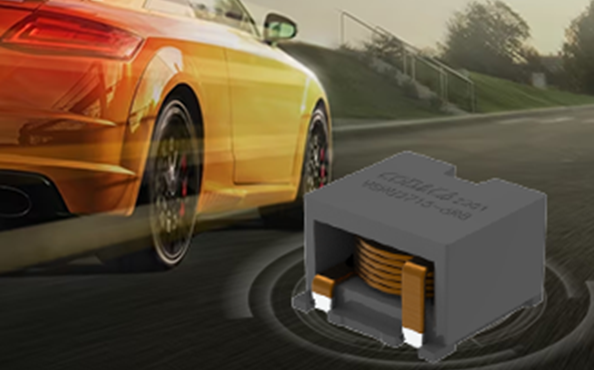
As APEC 2024 comes together for February in Long Beach, California, overseas-based specialty manufacturers of inductors and other magnetic components for power electronics are heading to America. This article highlights the products and capabilities of several: Shenzen Codaca Electronic of China, which recently linked up with Digi-Key as a distribution partner, MaxEcho Technology of Taiwan, Core Electronic of Turkey, and Prax Power from Barcelona. As usual, Magnetics Magazine serves as a media partner for the event.
Codaca inductor with flat wire & EE-shaped magnetic core to minimize losses
Codaca has recently developed a new automotive grade high current power inductor VSRU27 series with 8 inductance values and saturation currents ranging from 23 to 101.5 amps. Due to a recent distribution deal, the company’s products are now available through the Digi-Key Electronics online marketplace. Flat wire-wound with an extremely low DC and AC resistance helps to achieve very high current capability, low-temperature rise, and minimized losses. The EE-shaped magnetic core is made with symmetrical air gap maximizing the utilization of gap area which greatly boosts the DC bias current and anti-saturation ability, says Codaca. They can can be widely used in DC-DC converters, POL converters, high current switching power supplies, photovoltaic inverters and VRM modules.
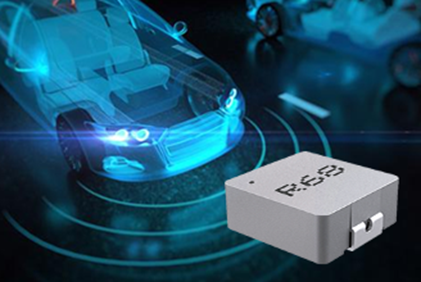
Another product recently developed by the company is a small, ultra-low loss molded power inductor for ADAS camera power supply. The CSEB0420H series is available with inductance values from 0.047μH to 2.10μH and current ratings as high as 50 Amps with size as small as 4.3 x 4.3 x 2.0mm. Die-cast with low loss alloy powder, it features rugged and composite construction that provides magnetic shielding to reduce the magnetic core losses and minimizes audible buzzing. Flat coil design reduces the AC losses caused by the coil skin effect in high-frequency applications.
Focused on developing and manufacturing magnetic components such as power inductors and coils, Shenzhen Codaca Electronic Co., Ltd, was established in 2001 and has more than 900 employees. See www.codaca.com.
Core Electronics of Turkey
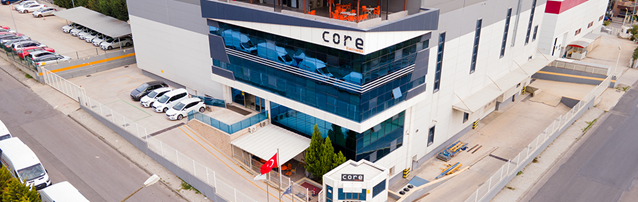
Core Electronics of Turkey will be highlighting its capabilities in manufacturing custom electronic components. Located in a modern facility in Kocaeli east of Istanbul, Core specializes in the production of customized wound circuit elements including toroidal inductors and pot magnets.
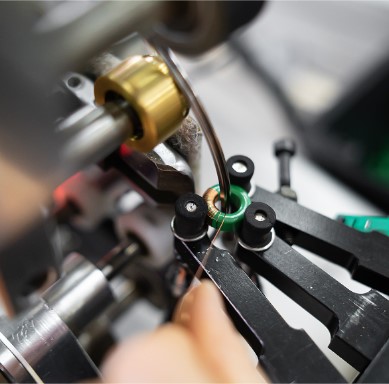
Flexible production systems and automated equipment give it the capability to fabricate a broad variety of components for power electronics such as toroidal inductors, axial inductors, current transformers, rfid coils and pot magnets.
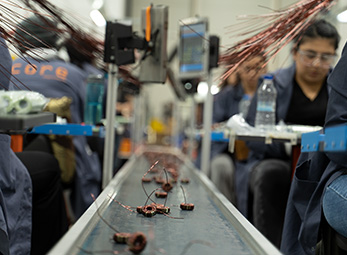
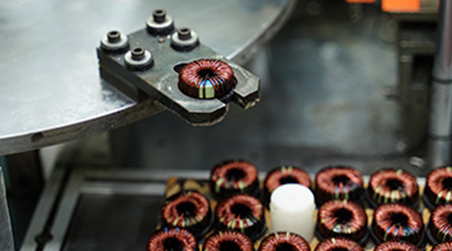
Founded in 1983 as NASA Elektronik in Turkey, Core has become a significant provider in Eurasian markets and internationally. See www.corewinders.com.
Max Echo Technology of Taiwan
Another component manufacturer coming from overseas will be Max Echo Technology, based in Taichung, Taiwan. Founded in 1992, it has been producing electronic components for more than thirty years. With its factory now located in Taichung Precision Science Park, the company is committed to the research and development of magnetic materials, ceramic materials, multilayer printing and low-temperature co-firing, providing customers with inductors, magnetic beads, and related magnetic or ceramic components.
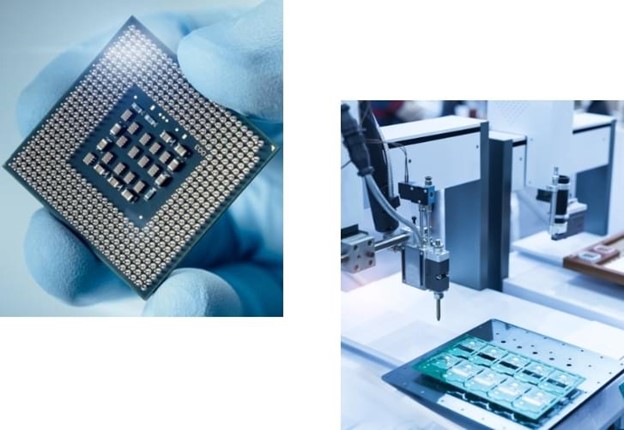
Its product capabilities include inductors, ferrite chip beads, common mode filters, flexible sintered ferrite sheet and wireless charging coils. Ferrite, metal alloy and ceramic material can be designed and manufactured with its capability in precision multilayer processing. For wire wound products, the company can manufacture material and ferrite core in-house, enabling the production of high-quality inductors and related power electronic components. See www.maxecho.com.tw.
X-Gap technology from Prax Power of Barcelona
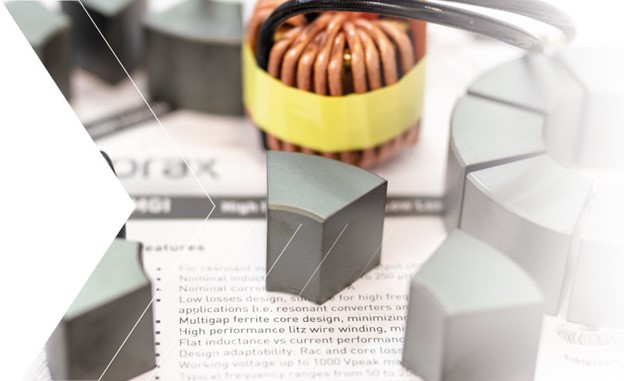
From Spain, Prax Power will be demonstrating its X-Gap technology and its capabilities for the development and production of a wide range of chokes, inductors and transformers. Prax is headquartered in Barcelona and has its primary manufacturing site in China.
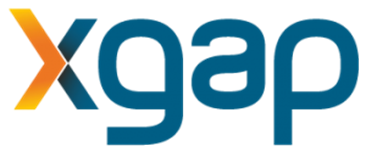
The company’s X-Gap technology is a multi-gap core approach for transformers and inductors developed in-house to reduce AC losses in the windings that allows for the creation of cost-effective solutions for maximum power densities. It allows a large air gap to be evenly distributed on a toroid to minimize fringing effect by splitting the gap into smaller gaps. With these evenly distributed gaps (up to 12 or 15 on a single toroid), losses are reduced exponentially because of the reduction in winding resistance.
It can be applied to transformers and chokes, and as a multi-gap core solution with triple-insulated Litz wire. It enables the creation of cost-effective solutions with maximum power density thanks to the reduction of core volume around 30%, while overall size reductions up to 20%. It also minimizes losses and offers optimal heat dissipation of windings in all type of cooling systems. The attributes make the approach suitable for magnetic components in demanding applications such as EV chargers or resonant converters.
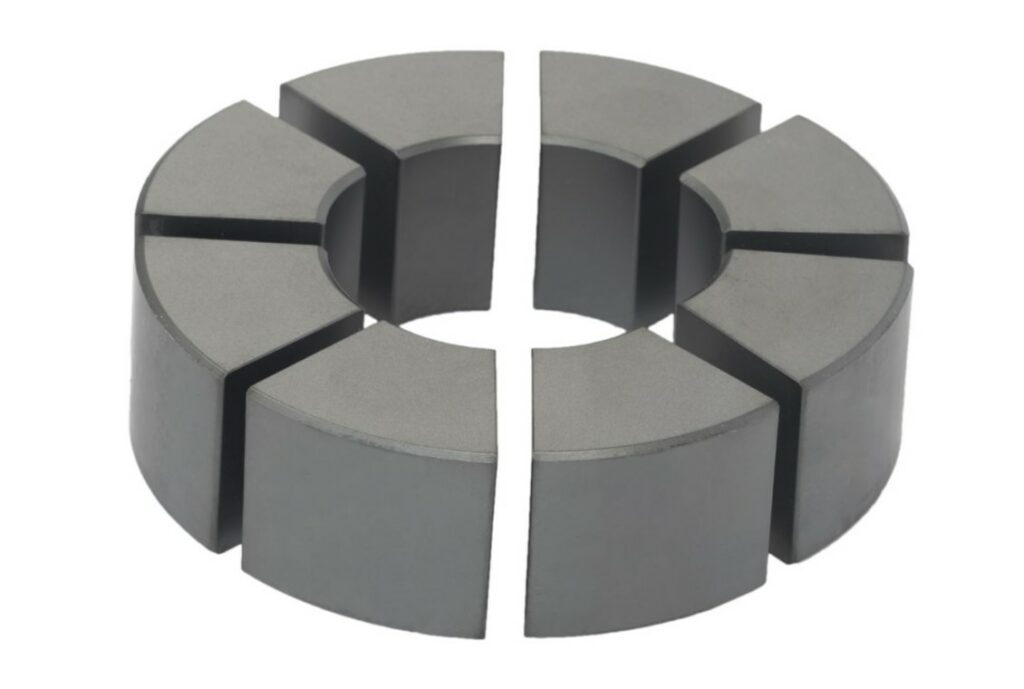
Prax gives this explanation of the technology: A gap is a portion of air inside a magnetic core path. It is used for two main purposes. One is energy storage in inductors or chokes such that the energy stored in an inductor depends on current and inductance factor. A gap or distributed airgap is commonly needed in cores to store such energy. The other purpose is for inductance value and tolerance reduction. Introducing a gap decreases magnetic core permeability, which reduces its inductance factor.
Non-gapped cores inductance tolerance is around ±25%, while gapped cores can be reduced to ±10%
Main effects generating losses due to high frequency in windings are, first, skin effect — an isolated round conductor carrying AC current generates a concentric alternating magnetic field which induces Eddy Currents. These currents oppose normal current flow in the center of the conductor, increasing the effective current closer to the conductor surface. The overall effect is that total current flows in a smaller perimetral area. This effect intensifies as frequency increases. Current flow concentrates in an equivalent perimetral cylinder at the surface of the conductor. This cylinder thickness δ is known as skin depth.
Secondly is proximity effect which appears when the distribution of current in one layer of a winding influences the distribution in another layer, always in the same winding. Such proximity effect, therefore, increases winding resistance (Rac).
A third factor is fringing effect which happens when a magnetic flux near a core airgap bends out. The distance over which these flux fringes out is basically proportional to the length of the airgap. One single gap can be split into several smaller gaps, preserving total volume and length. By doing so, effective permeability and energy storage capabilities are still the same, but the flux fringing is significantly reduced.
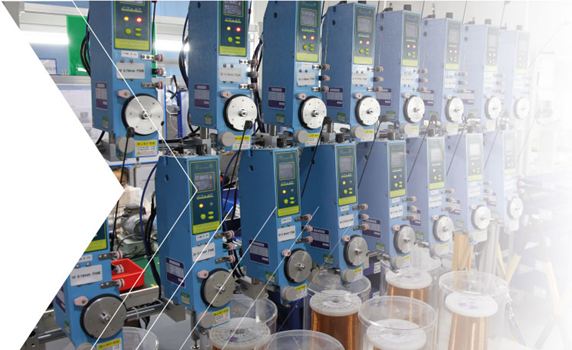
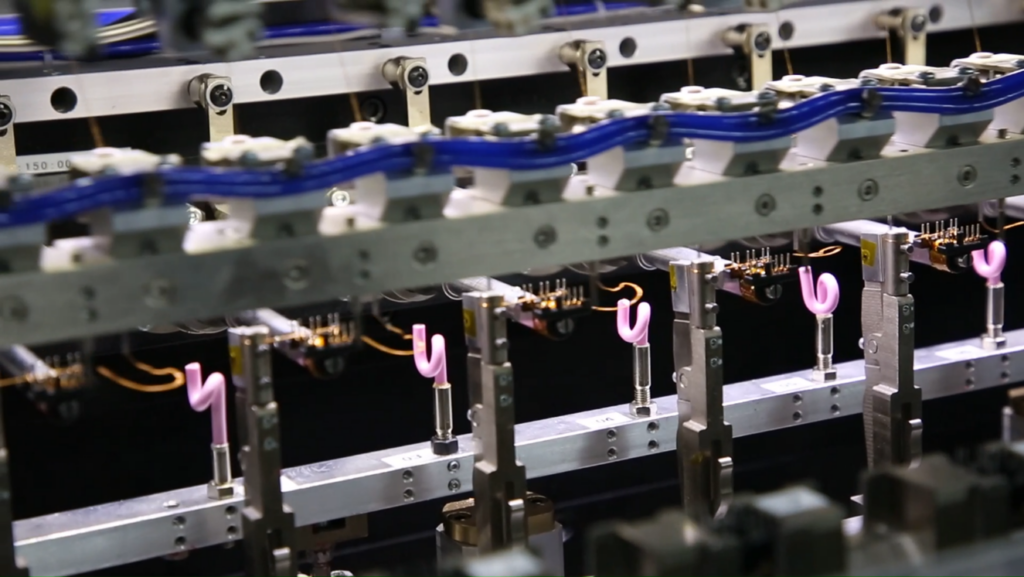