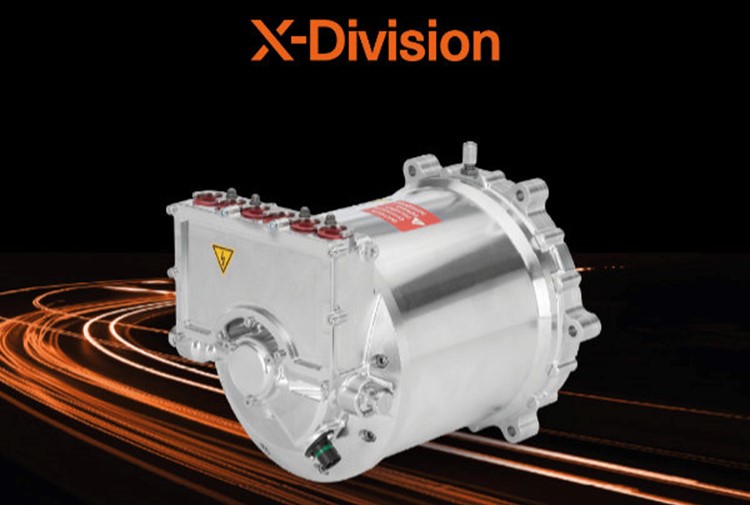
Designers of high-performance products for e-mobility are getting to know the Helix brand, launched in 2022 to spread the electric propulsion technology of Integral Powertrain Ltd of the UK to more automotive and motorcycle OEMs while also positioning into aviation, marine and aerospace markets. From its roots in designing propulsion systems for motorsports, Helix has emerged as an established series manufacturer of the power-dense motors, inverters and e-powertrains that it develops.
Its hallmark Scaleable Core Technology (SCT) platform has three product levels — stock, configured and custom. But its X-Division, focused on developmental projects in automotive, motorsport, aerospace and marine applications, leads the push into new electric powertrain designs. In two recent projects, Helix has designed a direct drive scaleable aerospace electric propulsion demonstrator and developed a revolutionary 650kW continuous output low-inductance motor for a new hypercar project. Both are based upon the company’s core technology in radial-flux motor topology and specialized inverters.
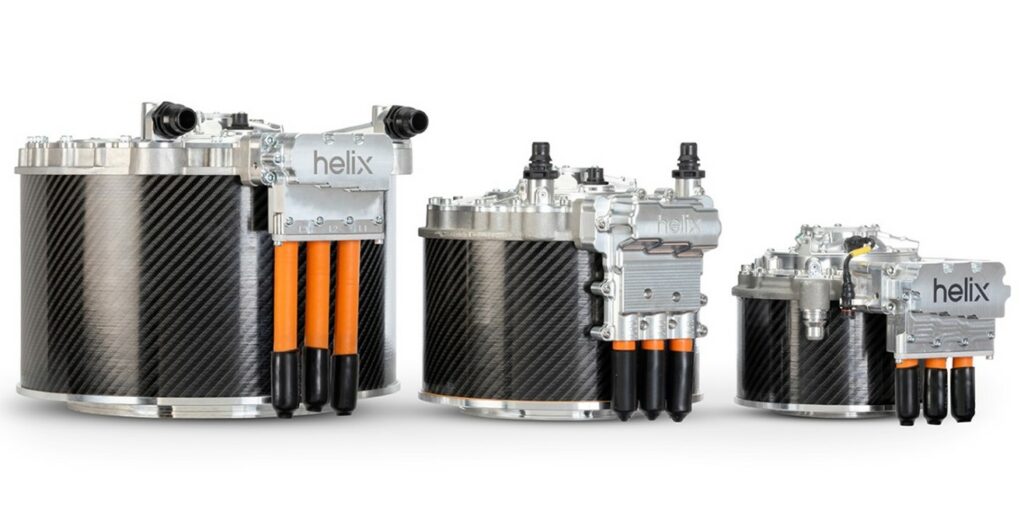
The demonstrator came out of a collaboration with the Midlands Aerospace Alliance and the University of Nottingham, Helix designed, built and tested the Direct Drive Scaleable Aerospace Electric Propulsion Demonstrator. Known internally as XBS, the project involved the company’s X-Division which focuses on taking its Scalable Core Technology (SCT) in three product levels –Stock, Configured and Custom — a step further, developing innovative solutions that push performance beyond established boundaries.
Helix’ participation in the project was guided by Chief Engineer Derek Jordanou-Bailey, whose back story includes seven years at Integral Powertrain, from which Helix evolved in 2022, before a stint at Mercedes-AMG High Performance Powertrains working on F1 power units. He returned to IP, now Helix, in 2018. The XBS project took an existing SCT motor configuration and adapted it to suit a 38mm through-shaft. The through-shaft architecture enables considerable versatility and optimization for multiple aerospace applications. Mounted to a piston engine, for example, the motor could augment engine power in a parallel hybrid arrangement.
Alternatively, a propeller could be driven from one end of the motor via a gearbox, while the other provided an auxiliary drive to generators, pumps and other ancillaries. Integrated mechanical cooling pump and advanced sealing technology further enhanced the XBS demonstrator. The integrated mechanical cooling pump removed any requirement for a separate motor, cables, brackets and other items associated with an external cooling pump, while X-Division employed advanced sealing technology to retain Helix’s patented rotor cooling in the design.
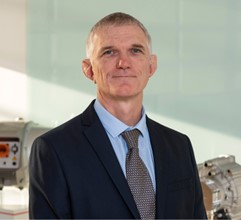
“With our seal technology the demonstrator ran up to 15,000rpm, developing high power from a relatively small package diameter,” says Jordanou-Bailey. “We could easily adapt it to drive a gearbox, gearing down to propeller speed. We ran it at 310kW continuous, 380kW peak – geared to drive a shaft at 2,500rpm that means huge torque suitable for driving a large-diameter propeller and a significant mass saving over a larger direct drive motor of the same power.”
At the conclusion of a robust test program, the demonstrator had proven its reliability and performance. Compared to a piston aeroengine or turbine delivering power in a similar range, the XBS was an order of magnitude lighter, considerably smaller and virtually maintenance free.
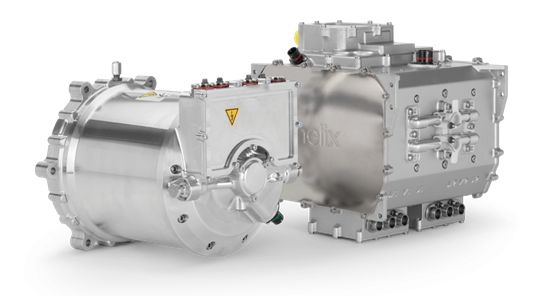
The hypercar project led to development of the company’s SPX177 motor. Weighing only 28kg and capable of delivering 650kW of continuous power, it is the most powerful pure battery electric vehicle motor the company has ever produced.
High power density is the standout feature. The radial flux configuration, differing from the conventional axial flux configuration, aligns the magnetic field perpendicular to the rotation axis. Their compact form factor makes them an impeccable fit for applications in the marine, aerospace and automotive sectors. But that’s just the tip of the iceberg. The motors flaunt efficient power transfer, ensuring that a significant portion of electrical energy is converted into mechanical energy. The optimized magnetic flux paths in the radial design further enhance their efficiency. This results in a motor that delivers robust performance, providing reliable torque generation and smooth operation across a range of speeds.
“The SPX177 motor uses the ‘top end’ in materials and reaches back into our motorsport heritage,” says Jordanou-Bailey. “Our SCT is intended to deliver products that are tailored to customer requirements and easily manufactured in large production runs, but for this the focus was on ultimate performance, accepting that the machine would be more demanding to manufacture in anything more than smaller batches. In those terms, it is like an F1 or Formula E unit.”
“It’s small and weighs just 41kg, including the 13kg inverter. It is a 2x 3-phase motor, so its current is shared across two inverters, a necessary approach to meet the phase current demands at ‘normal’ DC voltages at this extremely high power level. Both the motor and inverter have extremely high power density.”
“We needed an architecture that minimizes losses and the heat generated, especially at high-speed, and that meant quite a change in the way the motor was wound, since minimizing resistance losses results in a very low inductance machine. The switching in the inverter can generate lots of noise and harmonics and this is more challenging with a low inductance motor. The software team did a great job developing a new way of controlling the phase currents in the SPX177 motor.”
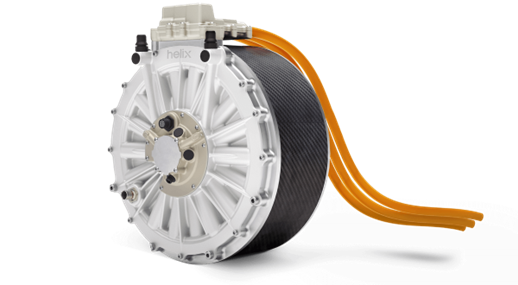
Scaleable Core Technology at Helix is based on its proprietary permanent magnet rotor designed for maximum magnet flux density to generate maximum performance at minimum weight. Patented rotor cooling is achieved by using strong magnets but with low heavy rare earth content. Key features include high pole-count with minimum ripple torque and high continuous rating and smoothness. Proprietary winding in construction is designed for durability under voltage, thermal and vibration stress. Carbon composite magnet containment supports the high-speed rotor and high power.
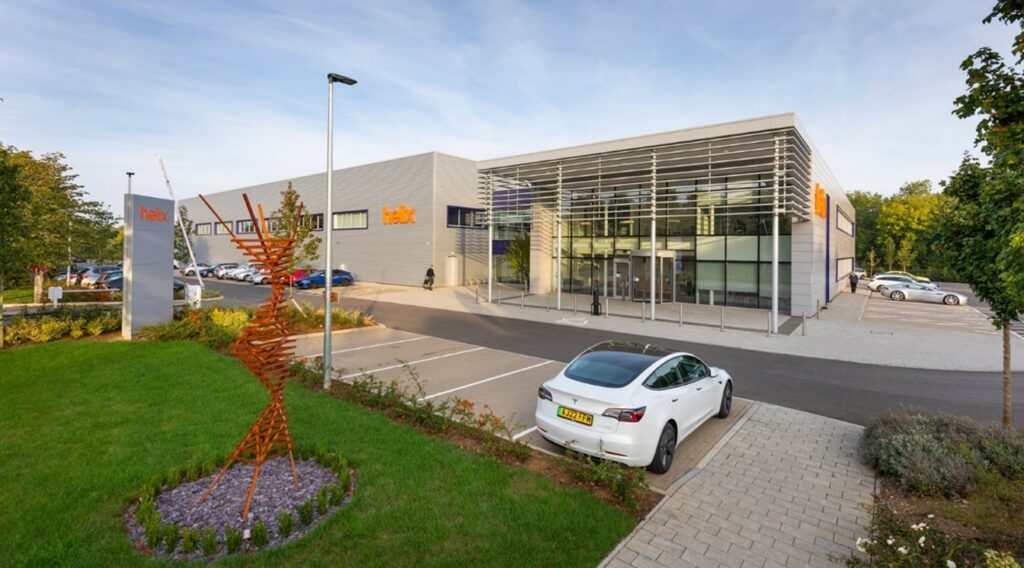
In 2021, Helix moved into its new state-of-the-art Technical Centre at Shenley Wood, Milton Keynes. The 47,000 sq ft facility was built to house the company’ expanding e-drive business. For more info, see www.ehelix.com.