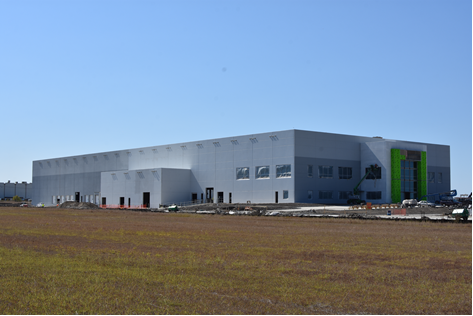
Freshly arisen from the flat, arid countryside of central Texas, a modern 130,000 square foot industrial facility is taking shape that the leaders and investors of Urban Mining Co. are eager to blossom into a pioneering, closed-loop magnet recycling and manufacturing operation. It is designed to recover rare-earth magnetic materials from end-of-life products and turn them into neodymium-iron-boron magnetic materials and products that will be a unique, new domestic source of supply. The accompanying photo of the new facility was taken in early October.
“We have completed construction of the site and shell, and in the first quarter of 2020 will be ramping up production over the next three years,” Scott Dunn, CEO of Urban Mining, told Magnetics Magazine in an interview with him and other company executives in early October, reviewing various aspects of the company’s progress. They are targeting for an initial production output of 250 tons-plus of sintered neodymium (NdFeB) magnets per year with a total plant design capacity in the range of 1,000 to 2,000 tons per year. The plant represents an investment of greater than $50 million overall, said Dunn.
At present, according to research conducted independently by Magnetics Magazine, the company appears poised to become the largest purpose-built recycler-producer of rare earth magnets in the world – and may be already. We know of no other similar commercial operation that rivals it.
“In 2018, we processed more than 600 tons of hard-disk drives,” said Peter Afiuny, executive vice president. “Currently, we have 10 tons per year of sintered prototyping capability and also the capability to produce 350 tons per year of compounded neo for bonded magnets.”
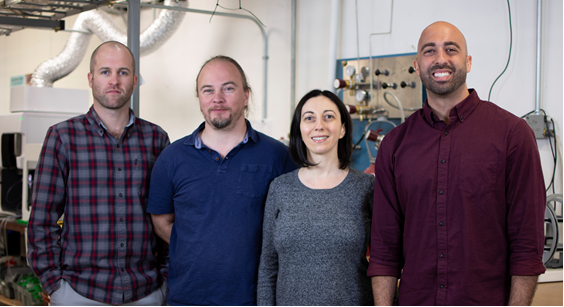
The only company of its kind in the U.S., the founding team is made up of a scientifically oriented group including Dunn, CTO Miha Zakotnik, Executive VP Peter Afiuny, and Chief Software Engineer Catalina Oana Tudor. The privately held company is funded by high net worth individuals and raised $25 million from them in a Series A financing in 2016. Of the startup’s five-member board, three are founders.
It counts Siemens, Rolls Royce, Parker Hannifin and the Department of Defense as some of its customers and business partners so far. It has about 25 employees now and plans to add more as it phases into expanded operations at the new plant in the town of San Marcos which is located about halfway between Austin, its current headquarters and operations site, and San Antonio.
Central to the effort are two principal, technical operations in the closed-loop process– one is magnet recycling to obtain the feedstock of rare earth material, and the other is engineering and production of magnets for sale. The company has developed its own patented Magnet-to-Magnet (M2M) recycling process to grind up recovered magnets from products such as electric motors and disk drives without using caustic chemicals or water that would generate more waste. Then it uses the powder to create new magnets, so far primarily for Department of Defense contractors keen to establish a new domestic source of supply. The company hopes to be able eventually to supply manufacturers of electric motors as other end-users including those in the automotive industry.
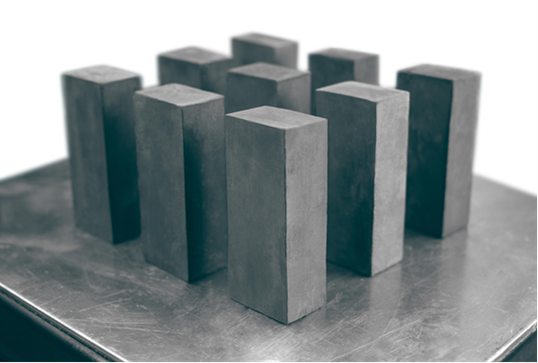
The process is designed to restore, even improve the magnetic properties of the recycled NdFeB product. According to the company, its product exhibits improved performance characteristics including remanence, coercivity and energy product as a result of its Grain Boundary Engineering (GBE) and Grain Boundary Modification (GBM) technology while also reducing the percentage of Dysprosium content.
“There is a very comprehensive recycling side of our business and we are able to provide tailored recycling solutions for manufacturers,” explains Dunn. “We have a critical recycling component but also technology for producing newly sintered products such as for motor companies requiring specific magnet shapes and performances, designed and engineered to meet their specs including machining and coating.” Magnetic performance of the company’s products can be tailored according to customer goals and requirements.
“For a couple years, we have been prototyping our output for a customer base in automotive, aerospace, defense and control automation,” reports Dunn. “We have also been prototyping bonded magnets with electric motors particularly as a target application.” Currently, these operations have been taking place at the company’s development site in Austin where they conduct manufacturing, quality control and research of their materials and products.
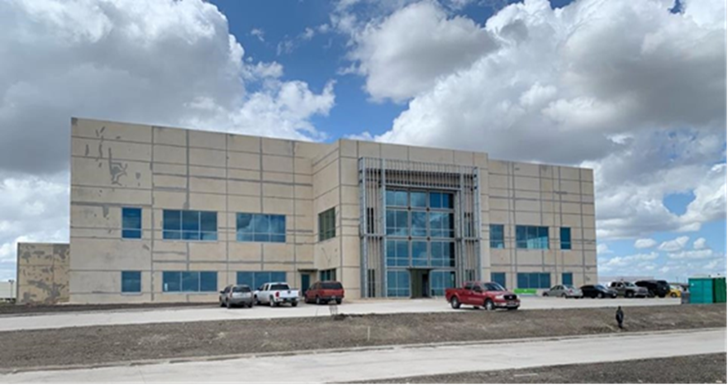
“Most important now are the risks entailed in scaling up at the new facility and selecting the right customers, particularly motor manufacturers, as we allocate our finite initial production capacity,” replied Dunn when asked about the steps ahead most critical to the company’s success.
Two technical papers published recently report on some of Urban Mining’s work to date. According to Zakotnik, CTO, and Davide Prosperi, chief quality engineer, the work establishes some important findings about the company’s recycled magnets.
Among the key findings in one report are that use of its recycled NdFeB magnets in a motor has shown the capability to perform as well as virgin magnets; that its recycled magnets have temperature coefficients for Br (flux density, residual induction) and Hcj (resistance to demagnetization) respectively 24% lower and 16% higher than virgin magnets; and that measured values of flux linkage and torque are around 7% higher for a motor equipped with recycled magnets.
In another study, key findings they cite include that their M2M and GBE magnets offer a green and technically viable production option, that the recycled magnet exhibits similar or better temperature stability to conventional magnets, and that oxygen and carbon contamination are similar in recycled and conventional magnets.
Along its way, Urban Mining has been increasingly recognized for its efforts toward both recycling and creating a domestic supply of rare-earth magnets. In August, it was named by Fortune Magazine to its “2019 Change the World List: Companies to Watch”.
For more info, see www.urbanminingco.com.