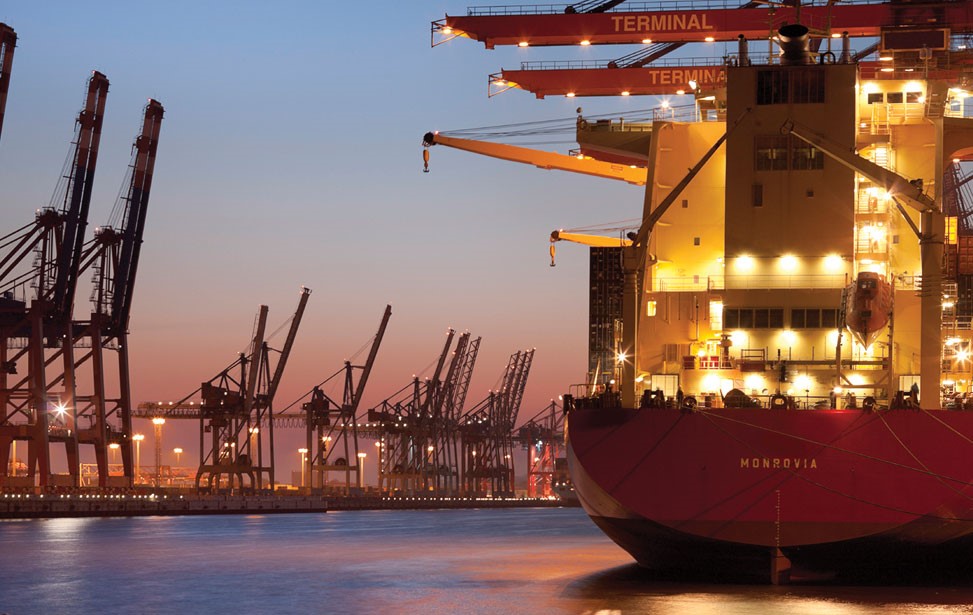
To meet the evolving demands of industrial marine operators handling greater loads at higher speeds, engineers at Stromag started from a clean sheet to design a new line of fail-safe electromagnetic brakes.
Modern vessels are equipped with dozens of ancillary items such as winches and loading cranes which must all incorporate braking systems to ensure their operation is reliable and effectively controlled. Stromag, an Altra Industrial Motion company based in Unna, Germany, has designed and manufactured marine braking systems for decades. The company’s products are installed on vessels operating across the globe, an experience that has given Stromag keen insight into the demands placed on equipment that operates at sea and the needs of vessel owners to increase productivity.
“In marine applications, time is money,” explains Michael Frank, product specialist for clutches and brakes at Stromag. “The faster vessels can complete loading and unloading operations, the sooner they can be on their way, earning their keep.” That pressure for increased productivity, he adds, has led to a continual increase in the capacity and speed of ancillary equipment with significant implications for braking systems.
“As cranes and hoists run faster and move larger loads, the amount of kinetic energy in the system increases, and the braking system needs to be able to manage that energy to keep the equipment under control.” Over time, Stromag engineers have continually adapted and upgraded their existing range of marine brakes to handle increased loads but the company recognized that these incremental improvements were reaching their limit.
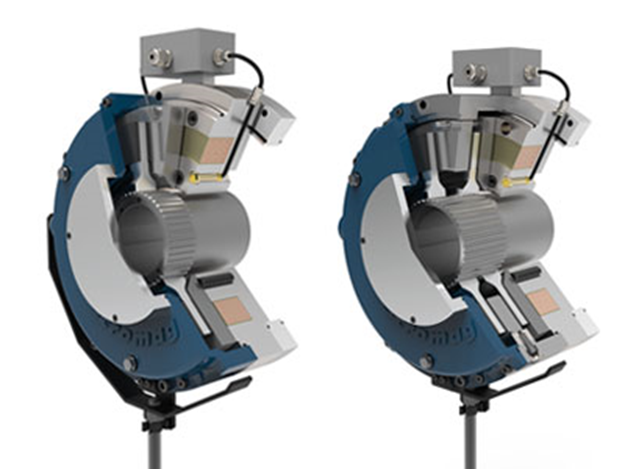
It was time for a new approach. The company established a team to create an entirely new series of brakes, designed to meet the requirements of current and future generations of fast, high-powered marine equipment.
“Our objectives for the new range were simple,” says Frank. “Our customers wanted a solution that offered the same high levels of reliability they have come to expect from us but with more power. Of course, they also have a close eye on cost.”
Delivering against those objectives was challenging, however. Braking systems for marine equipment face significant constraints. They must fit into a limited space envelope, offer standard mechanical and electrical interfaces for shafts and control systems, and withstand all the rigors of a wet, corrosive marine environment.
“The key to better brake performance is improved thermal characteristics,” explains Frank. “It is the braking system’s ability to dissipate heat that determines the power available.” The thermal behavior of a braking system is a complex design process, determined by the interaction between multiple components. To get the performance it was looking for, the Stromag team had to apply its in-depth experience of advanced friction system design, to make extensive use of computer-aided simulation and optimization tools, and to test multiple prototypes on rigs and in the field.
The electromagnetic system was a focus of attention, too. It consists of the coil body including the coil and armature plate. The brake generates the braking performance through pressure springs. By activating the magnet, the brake will be released and open since the magnetic force is working against the spring force.
“Our target was to optimize the electromagnetic circuit as much as possible in the available space to generate the maximum axial force so that we increase the force of the springs and the brake performance or torque. The coil is made from copper wire and coated with a special insulation paint. Calculation of the coil characteristics, the windings and potting compound in the coil is done in-house so we can define and produce the coils to accomplish our design.”
The outcome of all that work is Stromag’s new High Performance Brake (HPB) series. It is the most highly optimized friction package the company has ever produced for a dry electromagnetic brake and accomplishes a significant step-change in performance, says Frank.
The improvement can be seen most clearly in the speed ratings for the new series. A 100 Nm HPB brake, one of the smaller units in the range, is rated for operation at 6,500 rpm, while its predecessor had a maximum rated speed of 3,000 rpm. The difference becomes even more significant as the brakes get larger. The 4,000 Nm variant of the HPB is rated to 3,250 rpm, while its predecessor was deigned to operate at 1,000 rpm.
But what about the cost issue? Frank points out that the new design also provides significant benefits here. “The higher power rating of the new brakes mean that customers can often select a unit one or two frame sizes smaller for a given application with corresponding cost savings.”
The entire system is designed to be simple, robust and easy to assemble, he notes. Part count has been reduced, for example, by replacing separate covers with a part integrated into the body of the brake. The series uses a modular design that shares components between different models and simplifies the manufacturing supply chain. While these changes mean lower production costs, they also help to streamline maintenance and support activities. All internal components are designed to resist corrosion and offer enhanced durability under exposure to salt water or other contaminants.
The HPB series is available in two-face or four-face configurations and with a brake torque range of 80 to 5,000 Nm. While inspired by the demands of marine customers, it is also suitable for use in many other industrial applications where long-term reliability and resistance to harsh environments are a priority, usable for nearly all kinds of winches and hoists.
For more info, visit: www.stromag.com.