Industrial Magnetics, Inc., manufacturer of a diverse line of magnetic products for separations and workholding, continues to build its roster of certifications for serving the food products industry while also growing through active product development, expanded testing and laboratory services, and corporate acquisitions.
Based in Boyne City, MI, the company designs and manufactures permanent-magnet and electromagnetic assemblies for holding, lifting, fixturing, conveying and magnetic separation applications in a wide variety of industries and is part of the IMI family of companies, led by Bud Shear, chief executive officer.
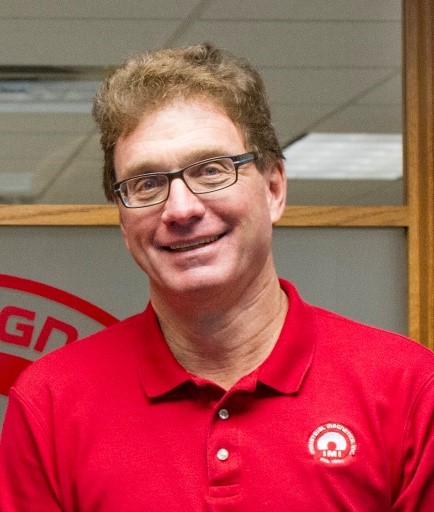
In May, Industrial Magnetics was recognized for its accomplishments in an award program by Michigan Celebrates Small Business. “We’re extremely honored to receive this award,” said Dennis O’Leary, chief business development officer. “Our family of employees works incredibly hard to design, manufacture and deliver product with industrial-grade craftsmanship that is on time and as expected,” he continued. “Last year, we processed over 14,000 orders and delivered at a 98.7% on-time rate. Our speed to market is unrivaled, especially given that more than three quarters of what we design and manufacture is application specific so it must be right the first time.”
Two acquisitions in the past two years have added to the enterprise and it appears that future deals could lie ahead. Earlier this year, IMI acquired Clamp Manufacturing Co., of South El Monte, CA, a long-time producer of industrial clamping products for metalworking and manufacturing markets. “This takes an important next step in expanding our workholding and general manufacturing product offerings,” said Shear.
In fall of 2017, IMI purchased Javelin Manufacturing of Fort Wayne, IN, a manufacturer of eddy current separators and engineered systems found the scrap, recycling, waste and mining industries. “The acquisition of Javelin marks IMI’s next step in expanding our metal separation offerings,” said O’Leary, “Javelin’s footprint, reputation and well-established relationships provide a unique opportunity for us to grow the Javelin brand, as well as IMI’s current ferrous separation product line. We will certainly flank the Javelin brand with additional sorting technology via future acquisitions.”
These followed two other acquisitions in 2014 when IMI acquired Sterling Systems & Controls which provides control systems for process equipment, and Prater Industries which makes equipment for particle size reduction.
Meanwhile, the company has made significant advancements recently in an assortment of its ongoing operations, particularly serving the food products industry where it has built up an impressive roster of certifications and capabilities for quality and safety, along with related product developments and services.
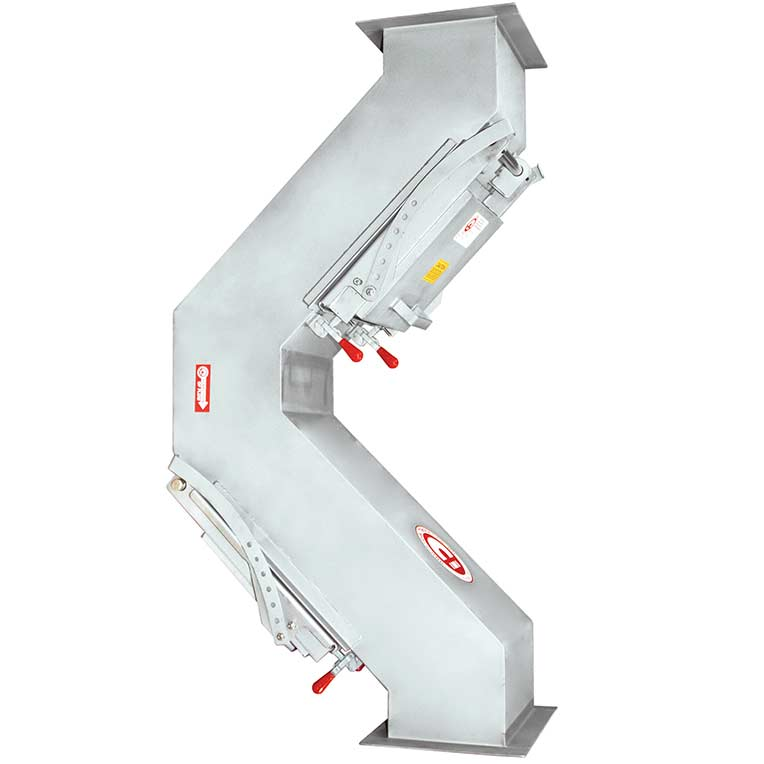
In January, IMI achieved certification by HACCP International of their sanitary grade Hump Magnet Separators as being suitable for direct contact with food products and for use in HACCP based food safety programs. HACCP is a global accreditation agency for the food equipment and processing industry.
The magnets are commonly used for the removal of ferrous tramp metal in gravity-fed processing systems in order to increase product purity and protect processing equipment from damage. Designed to force the product flow directly into the magnetic field, the magnet consists of two, heavy duty, diverter-equipped plate magnets in a sanitary grade stainless steel chute. The hinged magnets are gasketed and clamped tightly to the housing for maximum product and dust containment during processing operations and swing open for easy removal of captured tramp metal.
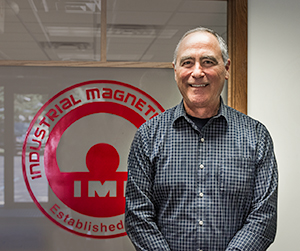
“We’re very pleased to have our Hump Magnet Separators added to the list of HACCP International certified products that we can offer our customers,” said Ken Gentner, IMI’s compliance engineer. “We’re proud of the fact that engineering food-safe processing equipment has grown to become one of the primary, high industry standards that IMI maintains.”
This marked the ninth product line from IMI to achieve HACCP International’s food zone classification. Additionally, 17 of their employees, including regional managers, engineering, operations and inside sales personnel, have been certified as HACCP Managers from the National Environmental Health Association.
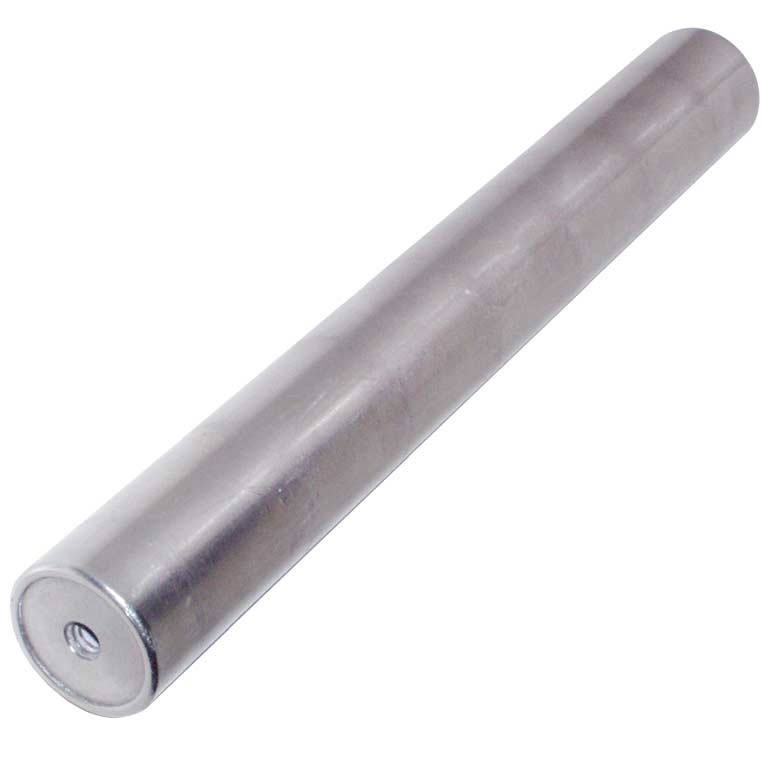
Last fall the company introduced its new Opti Series of rare earth magnetic circuits designed to meet the changing needs and requirements facing today’s processing facilities with regards to various compliance and regulatory initiatives.
The Opti Series addresses new standards for magnet separators. Each circuit is designed to optimize values which have been identified and earmarked as critical measurements for the specification, purchase, audit, verification and validation requirements for magnetic separation equipment and meets a specific thresholds of repeatable magnet performance.
“With regard to the stringent and evolving standards around food safety, we are the only manufacturer of foreign body detection and removal equipment certified by HACCP International for the North American market,” said Gentner when the certification was announced. There are four rare earth circuit configurations in the product family which ranges from 9,500 to 11,000 gauss and various pull strengths to match various applications.
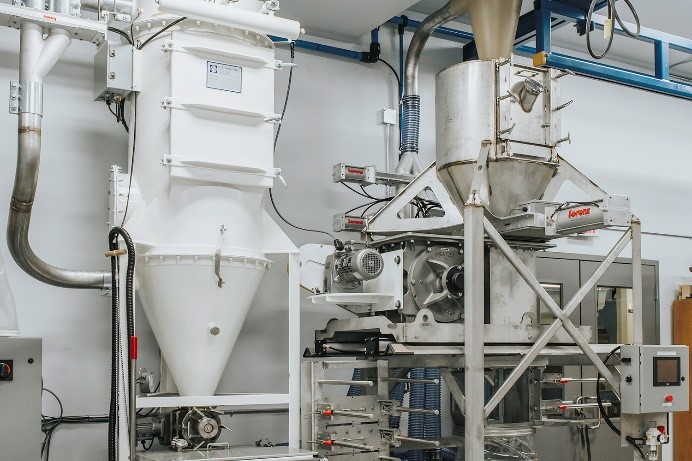
In another recent development, in August 2018 the company completed a new onsite research and development lab for simulated application testing of customer’s prospective holding, lifting, automation, conveying, and magnetic separation projects. The new 1,400 sq. ft. lab features various magnetic products and test stands designed to replicate the customer’s application in the field and assist in choosing the right magnetic product for the job.
Most recently, work was completed on an automated testing system for both pneumatic and gravity-fed bulk materials conveying using the company’s products such as drawer magnets and pneumatic line separators. This specialized test cell allows IMI to use customer supplied product samples to simulate bulk conveying characteristics such as particle sized materials, granular products or pellets and test them at specified flow rates and product velocities.
“Customers will have the benefit of knowing how their magnets will perform in the field prior to installation, which gives them real confidence in the capabilities of their system before the magnets are built, shipped and installed,” said Paul Hardy, lab coordinator. Other equipment in the lab includes a crane system with an air chain hoist for testing load weights up to a half ton, a pull-test machine with capabilities up to 15,000 pounds, gauss testing, and parts-per-million testing for ferrous contaminants in bulk material samples.
For more info, see www.magnetics.com.