Sometimes magnets are behind a core device technology and the commercialization team must account for interference.
By Nigel Syrotuck, Starfish Medical
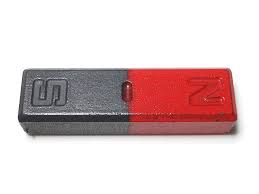
More often than you might expect, magnetism plays a key role in the medical device commercialization process. Permanent magnets are used to affix components together to improve cleanability and ingress protection—the magnets can be hidden behind sealed plastic or non-magnetic metal walls without exposing a seam or grooves that collect dirt or biological debris. Magnetic switches can also be used as interlocks to ensure safety. Sometimes, magnets are behind the core technology of a device and the commercialization team has to accommodate, enhance or avoid interference with the magnetic field generated by other device features.
In this article, practical magnetics from a mechanical engineering perspective will be discussed as it pertains to medical devices.
What Is Magnetism?
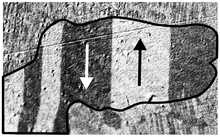
Magnetism is a class of physical phenomena characterized by force fields. Magnetism isn’t well defined by classical physics and is regarded as a quantum effect – a characteristic which makes it difficult for many people to really understand magnets. That said, it’s not too hard to imagine how typical magnetic fields are created. Picture the crystal structure of a metallic object, where each atom is arranged in neat rows, and each atom has a field of electrons spinning around it. If the right conditions are present, those magnetic fields line up, which result in a micro-domain magnetic field – materials that can do this are called ferromagnetic. Only a very small number of elements (mainly Fe, Co, Ni), are ferromagnetic.
However, ferromagnetic materials aren’t normally magnetized because the micro-domains typically point in different, random directions, canceling each other out. When a strong magnetic field is presented (such as by a large electro-magnet), the fields temporarily align and the material is attracted to that strong magnet. The degree to which materials do this is called magnetic permeability. If the magnetic field applied near the ferromagnetic material is extremely strong (and other conditions such as temperature are right), then the micro-domains will re-orient permanently.
Permanent Magnets
When the micro-domains are permanently aligned, the material will become a permanent magnet. A very common type of permanent magnet is a neodymium magnet, which is made up of neodymium, iron, and boron. They are available in various grades, with N52 being the strongest and most expensive. They will lose their magnetism above their Curie temperature, typically above 300oC. They are vulnerable to corrosion, so most commercial versions are coated in a layer of nickel to protect them. However, this layer tends to be brittle and chip off, therefore alternate coatings may be more appropriate for corrosive environments such as those often found in medical applications.
Hysteresis
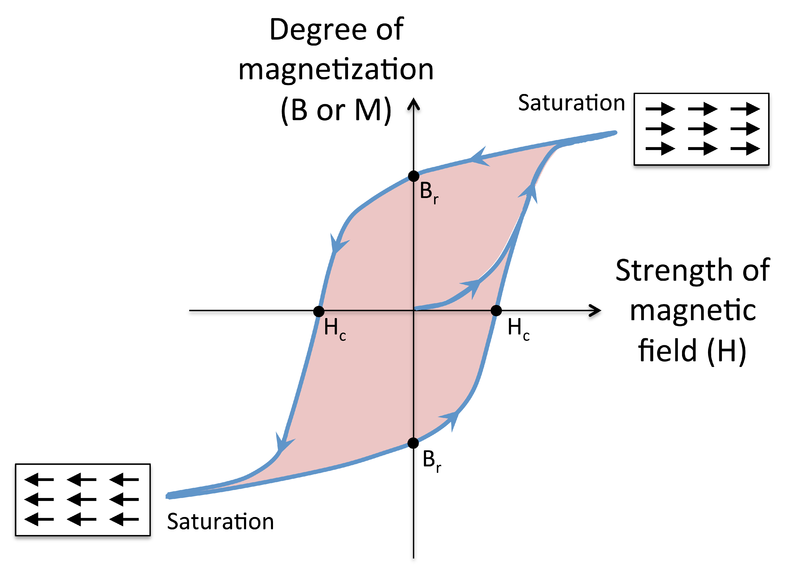
Hysteresis loop
A soft magnetic material is one that is highly permeable but doesn’t easily retain a permanent magnetic field. A hard magnetic material is the opposite – it’s easy to coerce into a permanent magnet. Even if not turned into a permanent magnet, both soft and hard magnetic materials tend to stay magnetized to some extent after being subjected to an external magnetic field. This phenomenon is called hysteresis, and is a function of energy dissipation – the more energy it takes to magnetize a material the more likely it is to want to stay as a permanent magnet. The degree to which hysteresis is present is called the remanence of the material, and though it is an important factor in the design of electromagnets, motors, transformers, and permanent magnets, it tends to be an insignificant effect in medical devices—except where magnetics are used as sensors.
Designing for Electromagnetic Interference (EMI)
Many medical devices utilize sensors which are susceptible to having their readings affected by EMI. That means that it’s a core functional need for all medical devices to control their emissions (which can affect nearby medical devices), and if they have sensitive electronics they must also control their susceptibility (their ability to be affected by other devices). To accomplish this, they are typically shielded with metal panels, spray metal coating products, or faraday cage-type structures. For sensitive equipment, the largest hole defines the EMI shielding level (where a hole is measured linearly), this means an extremely narrow seam that’s not completely closed may be a very significant EMI hole, depending on the target wavelength.
Shielding materials are chosen based on their requirements, as each material has different properties – certain metals provide better shielding per unit thickness than others. The best electric-field shields are Nickle-silver, BeCu, and other specialty metals. Mu-metal or permalloy are common choices where magnetic field shielding is a priority, which can be brought on by nearby permanent magnets or AC currents. Mild steel, stainless steel and zinc plated steel are also fairly effective and much more common. Aluminum isn’t an effective shield for DC currents or magnetic fields and requires more thickness to achieve the same AC shielding as steel but may be more appropriate for corrosive medical environments.
These shields can be single purpose, but in a complex medical device typically also become a part of thermal management – a sealed metal box right near PCBs tends to contain heat even if you don’t want them to. Multi-use parts (for example, metal panels that seal against EMI but also prevent ingress and protect the internal components) will reduce part count, but you may find the competing requirements lead to a very complex design with numerous vested parties and an overall increase in manufacturing cost despite the lower part count. That being said, taking advantage of the large metal sheets for structural elements may be a golden opportunity to .
All About Metals
(Note that only ferromagnetism is described here, as opposed to the other types of magnetism (para, dia, and anti-ferromagnetism), which tend to be both weaker (i.e. less practical) and more complex.)
As noted, iron, cobalt, and nickel alloys are generally ferromagnetic. These are commonly found in general structural parts, implants, and instruments respectively. Some alloys common in medical devices, such as certain types of stainless steels, chrome-cobalt implants, and nitinol (shape memory alloy wire) contain these elements but aren’t magnetic due to their resultant crystalline structure. The accompanying chart shows very common medical device metals and their relative magnetism, though it’s highly dependent on the manufacturing, treatment, and handling processes used to produce the part.
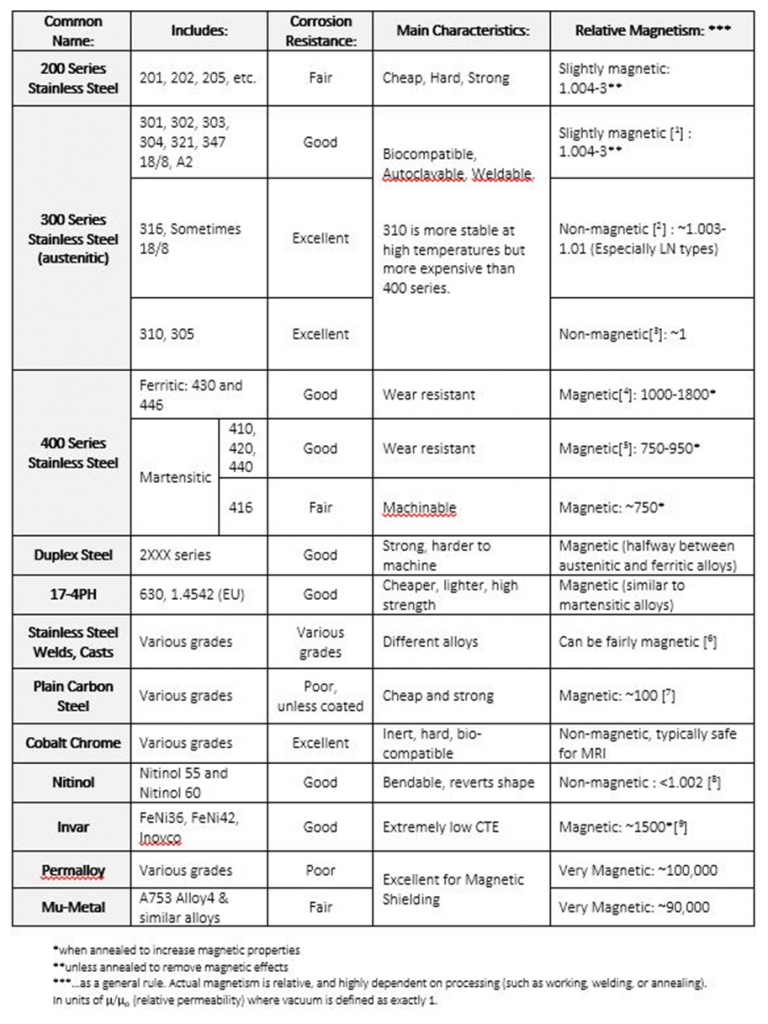
Modeling Magnetic Fields
Ferromagnetic metals that don’t emanate a unified magnetic field (e.g., a “non-magnetized” piece of iron) interact with magnetic fields emanating from permanent or electromagnets in a predictable way. They act as a conduit of magnetic fields, allowing the magnetic fields to take the path of least resistance, much like electricity prefers metallic conduit to air. In magnetics, this not only causes their magnetic domains to align but also affects the magnetic field map. If the magnetic field lines are small streams, ferromagnetic materials are the river that absorbs all streams that try to cross it. Similarly, the “streams” affect the “river” itself—if the streams are small (the nearby magnet is weak), then the river will be largely unchanged (little magnetic alignment). If the streams are large (the nearby magnet is strong), then the river will swell (become a magnet itself). Again, this is also true for electricity, which will travel along conduits to conserve energy by following the path of least resistance. The practical application of all this is that magnetic fields can be altered and shaped in the desired way by understanding the path of least resistance and using ferromagnetic materials in the vicinity of the magnetic field source. Modeling software is the simplest way to visualize this effect and show the resultant fields.
A Case Study – Rotational Direction Gauge
We were challenged to build a surgical medical device with an end effector that knew where the end was in 3D-space at all times. Though not too hard on its own, we wanted a device that was fast, easy to use, and could be subject to liquid spray and intense cleaning. We choose to use an arm with both an “elbow” joint and a “shoulder” joint, both of which needed to read their angles. The elbow wasn’t too difficult – we used bearing system to provide the single degree of freedom with a magnetic Hall Effect encoder, and a disposable, sterile sleeve overtop. However, the shoulder has an extra degree of freedom, so we chose to use a stainless steel ball that sat in a shallow cup which had a disc magnet hidden under it. The cup was moulded right into the plastic of the base to be totally watertight. It was very successful – the ball was very tightly coupled to the base via the hidden magnet but could move freely in rotation (just like a real shoulder). The location was measured by an optical encoder. The base and arm were easy to separate and clean. We chose 440C series stainless steel for the ball because it’s both corrosion resistant and magnetic.
Other medical device applications where we’ve chosen magnets include: a small magnet to trigger a present/not present Hall Effect sensor through a waterproof shield to indicate that a refill cartridge in a handheld device was fully inserted; a magnetic system for mixing liquids within a closed container (similar to commercial magnet mixers); various microfluidic applications (mixing tiny amounts of substances or activating tiny valves); numerous EMI shields to isolate precision sensors used in diagnostic medical devices; as well as similar applications to the arm system described above for connecting parts together through a waterproof barrier.
Overall, magnetics play an essential role in medical devices in many ways, but most commonly they are found in EMI shielding or where parts need to be coupled though a sterilisable or cleanable barrier.
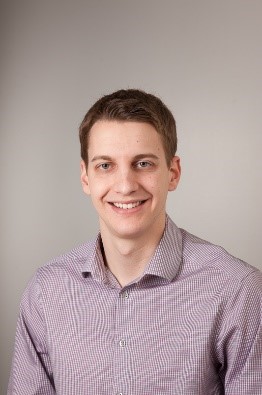
About the author: Nigel Syrotuck is Engineering Team Lead of Starfish Medical in Victoria, BC, Canada, a medical device design company which provides design, development and manufacturing services to help companies create products for a number of medical specialty areas. Prototype and volume production are delivered in an ISO 13485 certified facility with FDA registration and class 100,000 clean room capabilities. For more information, see www.starfishmedical.com.