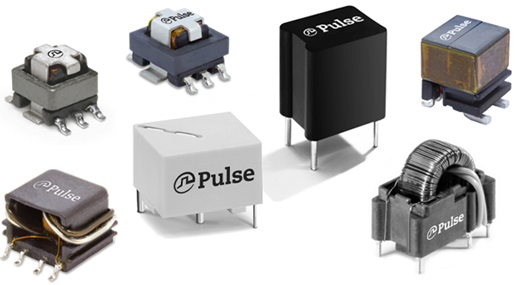
Pulse Electronics has added to its extensive line of power electronics components with a new series of current sense transformers and also innovative trans-inductors for voltage regulation. The new products feature advanced winding and magnetic sensing technologies applied to high-volume manufacturing capability and pricing.
A new PAS6322 series of low-profile current sense transformers become part of the company’s diverse line of current sense transformers depicted above (PAS6322 not shown). Current sense magnetics are used as a low loss method for sensing AC current in a circuit and also provide electrical and safety isolation between the source of the current and the measurement circuit. The new series supports current measurement of up to 50Arms.
“Our integrated single turn design simplifies current sensing and reduces complexity of hand placing a bus wire during PCB assembly while still allowing for up to 50Arms,” said David Wiest, product marketing manager for the Power Business Unit of Pulse. “The low profile, 5kVdc isolation, reinforced insulation and capability of up to 10mm creepage make this part ideal for use in kilowatt-plus LLC and PSFB converters.” Explanation of current sense magnetics can be seen in a white paper, “How Does it Work- Current Sense Magnetics” .
Trans-Inductor Voltage Regulators
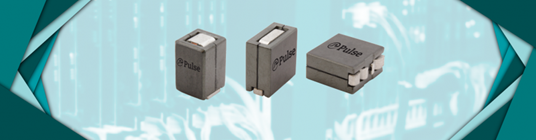
In another recent product development, Pulse continues to expand its portfolio of inductors used to power processors, memory, FPGAs and ASICs in servers, datacenters and storage systems. Its latest additions are specifically designed for use with the trans-inductor voltage regulator (TLVR) topology and leverage the company’s high-volume automated manufacturing to make the dual winding inductor and compensation choke. The TLVR topology enables faster transient response and utilizes a dual winding power bead inductor.
“Trans-Inductor Voltage Regulators (TLVRs) are an exciting development that enables ultra-fast transient response in multi-phase voltage regulators and leverages our existing automated inductor infrastructure allowing us to quickly and effectively develop products for TLVR,” notes Wiest.
Traditionally, these applications have used single winding inductor used in a multi-phase buck topology which allows currents to be distributed though parallel paths or phases. By operating each phase in a staggered fashion, the ripple currents in each phase tend to cancel at the output and the overall ripple current seen at the load is much smaller than the ripple on each phase. This approach allows smaller inductances to be used (typically on the order of 50-300nH) and can allow design engineers a trade-off between how quickly the converter responds to a change in the load current (transient response) verses stability of the control loop. By adjusting the number of phases used in the converter, the designer has flexibility to optimize the circuit for their specific application.
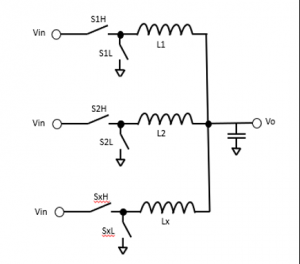
However, as processors and FPGA’s demand faster and larger current transients the voltage regulators used must increase their bandwidth to improve on response time. This is usually done by either increasing the number of phases and/or reducing the inductance value of each phase. These solutions, however, can create complications in the converter design.
Increasing the phase count necessitates less space per phase which means less width for the power stages and inductors. For the inductor, this space constraint creates skinny but tall components that can become mechanically unstable which limits the ability to shrink the inductor width. Reducing the inductance value used per power stage (which is already sub 100nH) drives higher ripple currents per phase resulting in higher AC losses as well as complicating the converter control. It is important to note that transient response time of the entire converter is somewhat limited by the fact that each phase will respond to the step by increasing or decreasing its duty cycle in a round-robin fashion, one at a time.
In order to mitigate these issues and further drive performance improvements, a “Trans-Inductor” based voltage regulator was developed in the technical disclosure commons domain. The trans-inductor is very similar to a traditional one turn VR inductor but has the addition of a second tightly coupled winding. The main low DCR ‘primary’ is used in the same fashion as in a traditional VR inductor, having a PWM input with several phases feeding the single output. Each single turn ‘secondary’ is tied in a series loop referenced to the local ground. When a load step occurs on a given phase, the resultant increase or decrease in duty cycle is reflected to its secondary winding and because the secondaries of each phase are in a series loop they all ‘see’ this change immediately. Through the magnetic coupling this sensed change is reflected to each inductors primary winding. In effect, this allows all phases to respond simultaneously to a load transient greatly reducing the time needed for the converter to adjust.
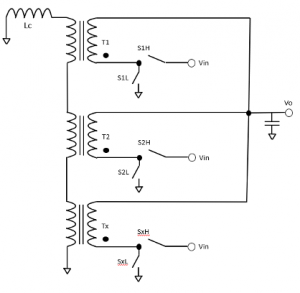
Additionally, a compensation inductor has been introduced into the converter circuit. It is typical for this inductor to be similar in construction to a traditional VR inductor. The compensation inductor exists to give design engineers the ability to adjust the total inductance in the secondary loop, allowing for freedom to adjust for converter stability. Due to the AC coupled nature of the secondary circuit, the compensation inductor sees almost no DC current which minimizes the impact of DCR. However, the inductor is subject to a superposition of each phases ripple current. In practice, this means that for a 4 phase converter switching at 1MHz, the compensation inductor will see a reflected ripple current with a frequency of 4MHz. At such frequencies care must be taken to minimize AC winding loss as well as ensuring a proper high frequency, low loss core material is chosen.
As an initial offering, Pulse is releasing the PGL6215.XXXHLT trans-inductor and PGL6312.XXXHLT compensation inductor with plans to release an additional five families of trans-inductors and footprint compatible traditional inductors in various sizes. See www.pulseelectronics.com.