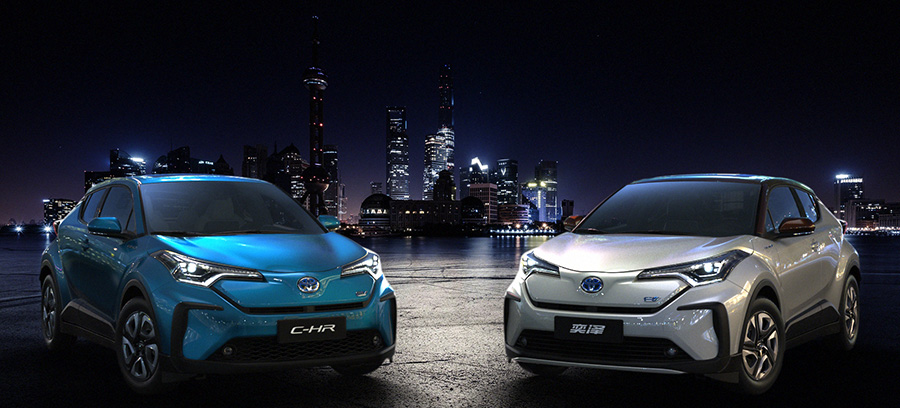
Seeing a huge future demand for magnets in electric vehicle motors, Toyota researchers report a breakthrough in development of a magnet for EV motors that uses 50% less neodymium and can withstand high temperatures. Pictured are the company’s first all-electric autos to launch in China unveiled at Auto Shanghai show in April.
Toyota researchers say they have found a way to dramatically cut the cost of electric motors by reducing up to 50% the amount of neodymium in their magnets in favor of less expensive and more abundant rare earth elements lanthanum and cerium. They can withstand the high temperatures in automotive systems, a key factor for magnetic performance in a vehicle motor.
The company says its new magnet is the world’s first neodymium-reduced, heat-resistant magnet and will become a key element of the foundation required to popularize electric vehicles. In about five to six years, by the mid-2020s, Toyota expects to first put them to work in electric motors for power steering, perhaps also in robots and appliances. In about ten years, the automaker expects to begin using them in the primary drive motors for electric vehicles.
This article provides details from Toyota about the magnet and their development efforts which were conducted in Japan. The magnet uses no terbium (Tb) or dysprosium (Dy), which are rare earths that are also categorized as critical materials necessary for highly heat-resistant neodymium magnets. A portion of the neodymium has been replaced with lanthanum (La) and cerium (Ce), which are low-cost rare earths, reducing the amount of neodymium used in the magnet.
Neodymium plays an important role in maintaining high coercivity which is the ability to maintain magnetization, and heat resistance. Merely reducing the amount of neodymium and replacing it with lanthanum and cerium results in a decline in motor performance. Accordingly, Toyota adopted new technologies that suppress the deterioration of coercivity and heat resistance, even when neodymium is replaced with lanthanum and cerium, and developed a magnet that has equivalent levels of heat resistance as earlier neodymium magnets, while reducing the amount of neodymium used by up to 50 percent.
The new type of magnet is expected to be useful in expanding use of motors in various areas as well as maintaining a balance between the supply and demand of rare earth resources. Toyota plans now to further enhance performance and evaluate application in products while accelerating the development of mass production technologies. This effort is part of a multi-pronged program by the company to advance elemental technologies for motors, inverters, batteries, and other components that are key to technology advancement of electric vehicles.
Development background
It is important that magnets used in automotive motors and other applications have high coercivity even at high temperatures. For this reason, approximately 30 percent of the elements used in motor magnets are rare earths. When powerful neodymium magnets are used at high temperatures, such as for automotive applications, terbium and dysprosium are generally added to increase high-temperature coercivity. However, terbium and dysprosium are rare and expensive metals found in locations with high geopolitical risks. Because of this, considerable efforts have been made to develop magnets that do not use these metals.
Production volumes of neodymium are relatively high among rare earths, but there are concerns that shortages will develop as electrified vehicles, including hybrid and battery electric vehicles, become increasingly popular in the future.
To overcome these issues, Toyota undertook development of technologies that can both eliminate the use of terbium and dysprosium and reduce the amount of neodymium used. Through substitution of neodymium with lanthanum and cerium, which are abundant and low-cost rare earths, high heat resistance can be maintained and loss of coercivity minimized.
Use of rare earths in neodymium magnets
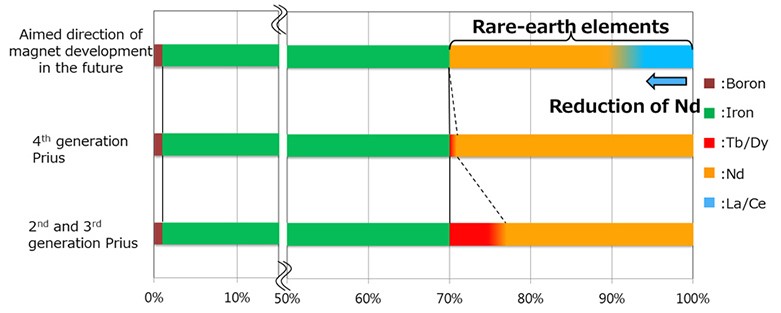
Three key factors
The newly developed magnet can maintain coercivity even at high temperatures because of the combination of the three new technologies: grain refinement of magnet; two-layered high-performance grain surface; and specific alloying ratio of lanthanum and cerium.
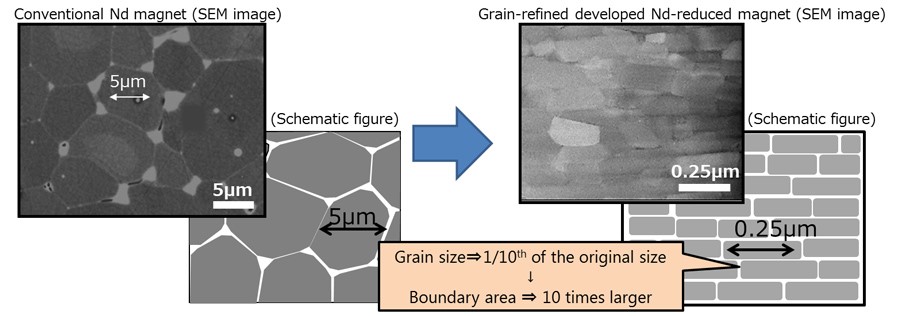
With grain refinement, It is now possible to retain high coercivity at high temperatures through the reduction of the size of the magnet grains to one-tenth or less of those found in conventional neodymium magnets and the enlargement of the grain boundary area.
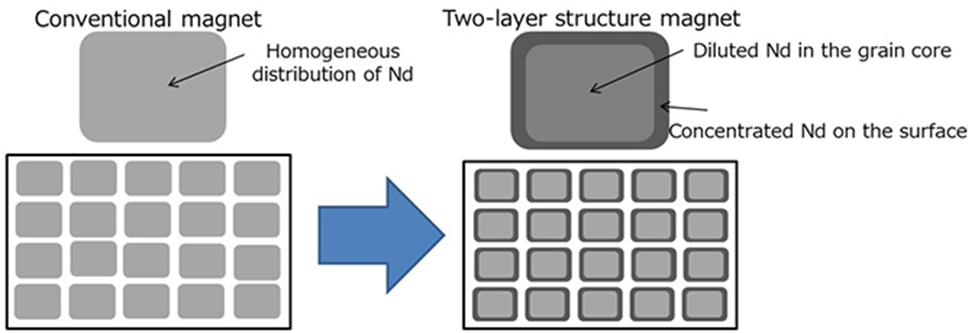
Two-layered high-performance grain surface
Another key technology development is a two-layered high-performance grain surface. In a conventional neodymium magnet, neodymium is spread evenly within the grains of the magnet, and in many cases, the neodymium used is more than the necessary amount to maintain coercivity. Thus, it is possible to efficiently use neodymium by increasing the neodymium concentration on the surface of the magnet grains, which is necessary to increase coercivity, and decreasing the concentration in the grain core. This results in the reduction of the overall amount of neodymium used in the new magnet.
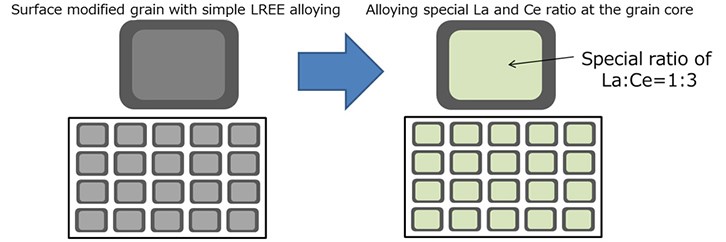
Specific ratio of lanthanum and cerium
The third key factor has been to achieve an optimal ratio of lanthanum and cerium. If neodymium is simply alloyed with lanthanum and cerium, its performance properties such as heat resistance and coercivity decline substantially, complicating the use of light rare earths. As a result of the evaluation of various alloys, Toyota discovered a specific ratio at which lanthanum and cerium, both abundant and low-cost rare earths, can be alloyed so that the deterioration of properties is suppressed.
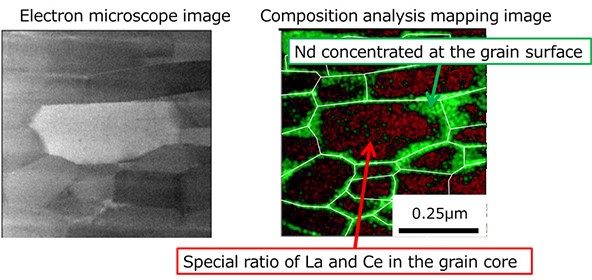
Electron microscope image and composition analysis mapping image
By simultaneously incorporating all three key technologies, Toyota has been able to develop its world-first neodymium-reduced, heat resistant magnet.
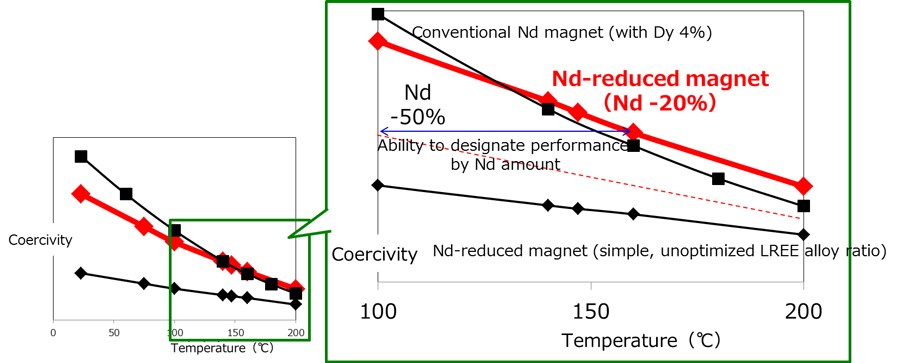
Heat-resistance performance