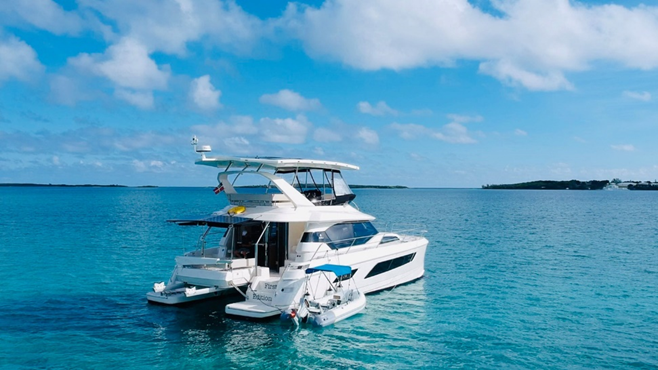
Using Neodymium magnets and axial flux motor designs, electric motor developer Torqeedo of Germany is powering through a flurry of innovations to become one of the world’s leading manufacturers bent on electrifying marine mobility. At the same time, its technology is spurring progress in electrification developments based on permanent magnet motor technology at its parent company, diesel and gasoline engine maker Deutz AG.
“As the marine industry looks ahead to the challenges of tomorrow, Torqeedo and our partners around the world are creating a new way to move on the water, from dinghies and daysailers to motorboats, water taxis and ferries,” said Steve Trkla, president of Torqeedo, Inc., the American branch of the company, at this year’s Miami International Boat Show and Miami Yacht Show, held in February. Torqeedo’s motors and drive systems were featured in the new launches of several boat makers at the show including the solar-electric motor yacht shown above, powered by the company’s innovative Deep Blue Hybrid system, along with smaller craft powered by its outboard motors.
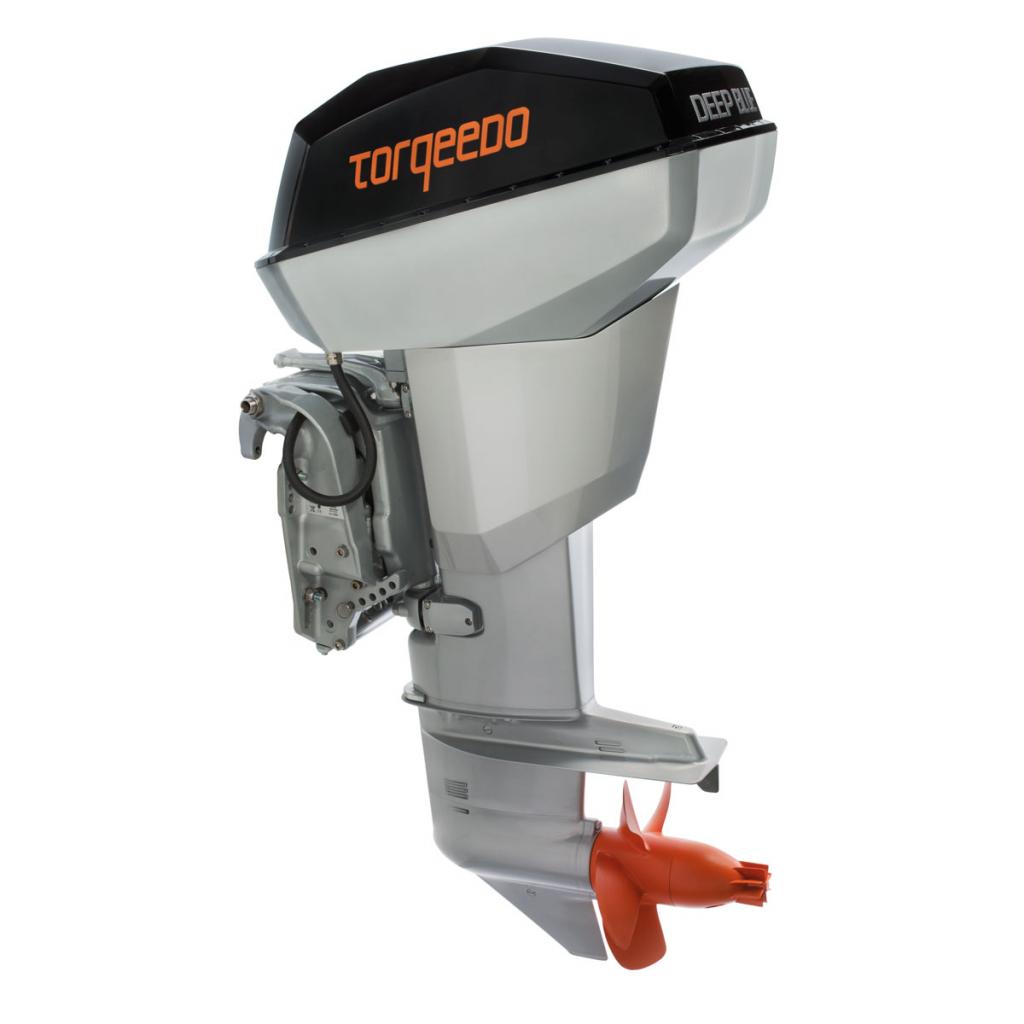
This year marks a milestone for the company, delivering its 100,000th electric boat motor and, now, fully integrated drive systems, since being founded 15 years ago in Starnberg. Today, the company develops and manufactures electric and hybrid drives from 0.5 to 100 kW for commercial applications and recreational use. Its products are characterized by an uncompromising high-tech focus, maximum efficiency and complete system integration. In horsepower equivalents, its outboards range from from 1 to 80 HP, inboards from 40 to 80 HP. It also makes pod drives from 5 to 20 HP, a saildrive with 40 HP, and hybrid drives for yachts up to 160 HP.
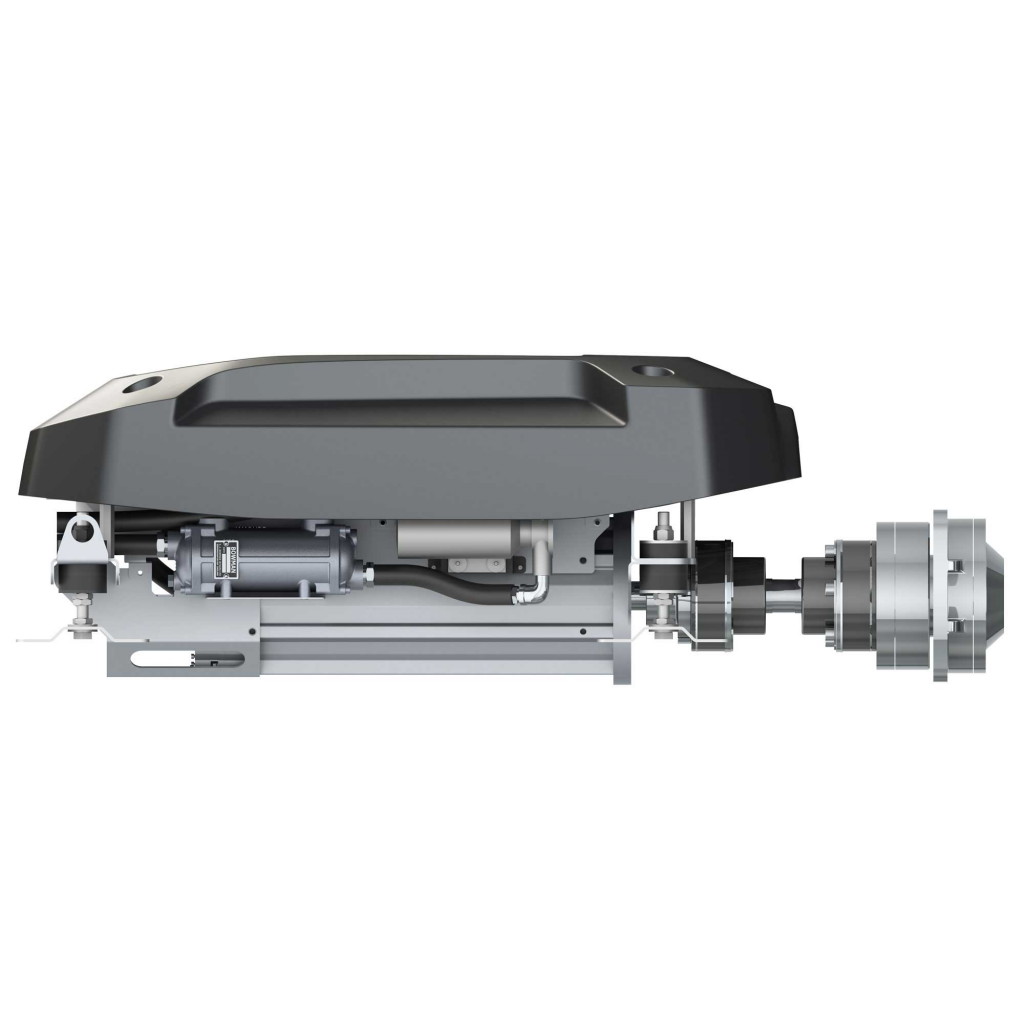
In sync with its relentless product development, Torqeedo will launch two new motor models in 2020, a professional-grade Ultralight motor for serious kayak anglers, and a 20-horsepower equivalent Cruise 10.0 T outboard. At Miami, visitors were also able to take a look at two new 100% electric runabouts powered by Torqeedo motors. A brand-new Phoenix 290 by Canadian Electric Boat Company boasts two Deep Blue 50 R outboards while Zin Boats demonstrated its Z2R runabout powered by a Deep Blue 50i system. The craft reaches a top speed of 35 mph and has a range of 100 miles at cruising speed.
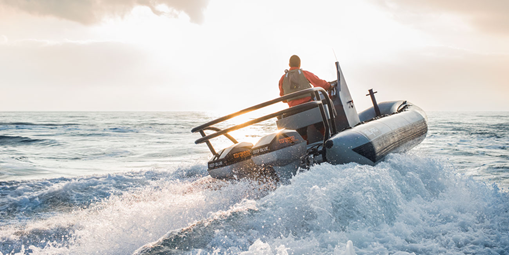
In 2017, Torqeedo was acquired by the DEUTZ Group, one of the world’s leading manufacturers of diesel and natural gas engines, and now operates as a subsidiary of Deutz AG, also based in Germany. The acquisition began the implementation of the parent company’s E-Deutz strategy, as Deutz made a commitment to invest around €100 million initially, including the acquisition of Torqeedo, to add electric power and drive systems to its product lineup.
(Watch for an upcoming article in Magnetics Magazine on how Deutz is moving forward on its development of new hybrid and electric drive systems for industrial applications.)
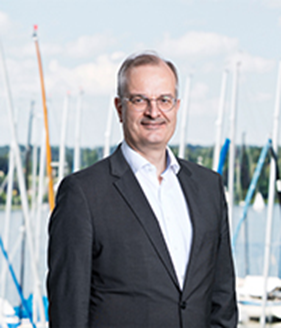
“Torqeedo uses rare earth, permanent magnets in our motors,” says Dr Ralf Plieninger, CTO of Torqeedo, who was recently promoted to managing director of the company. It characterizes its technology according to five key criteria in marine propulsion that distinguish electric motors: frequency characteristics; alternating field generation (commutation); magnetic field excitation; structural design; and magnetic field direction relative to the rotational axis.
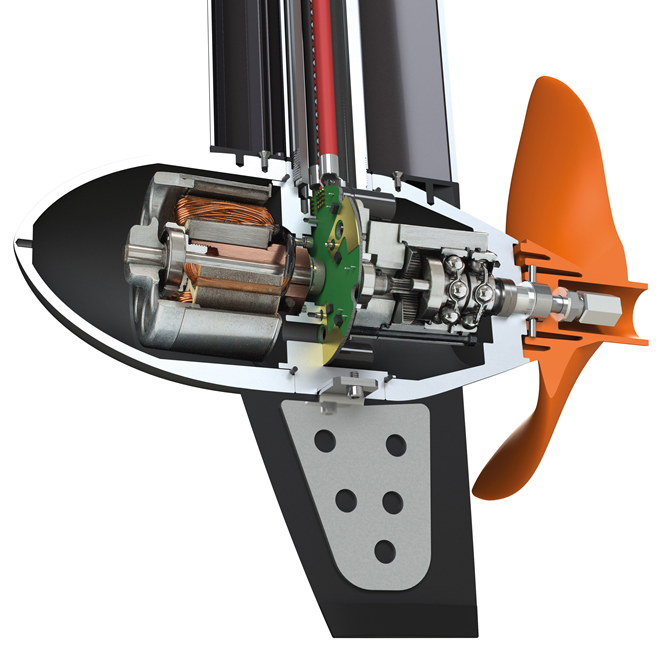
Synchronous motors
Depending on the frequency characteristics, a difference is made between asynchronous motors and synchronous motors. Torqeedo motors are always synchronous. In asynchronous motors, the ratio of the motor speed to the frequency of supply voltage is not constant but varies depending on the load state of the machine. The higher the load, the higher the speed difference – the so-called “slip” – i.e. a specified propeller speed will not be maintained when flow resistance is greater. Thrust is therefore not available at the precise moment it is needed.
With synchronous motors, however, the ratio of the motor speed to the frequency of supply voltage is constant. As a rule, synchronous motors are torque controlled. They therefore always draw as much current as they need in order to deliver the necessary torque at the desired motor speed. For this reason, they are the preferred choice for use in fields with especially demanding torque requirements. If the motor needs more power to maintain a given propeller speed it will automatically draw more current.
Electronic commutation
Depending on the type of alternating field generation (commutation), a distinction is made between mechanically commutated motors and electronically commutated motors. Brush-complemented motors generate the alternating field necessary for the motor to operate by means of sliding contacts Owing to their geometrical arrangement, these “brushes” switch the current depending on the position of the rotor. A major weakness of these motors is the wear caused to the brushes, which results in high maintenance overhead. Contact resistance also causes brush loss, which lowers the efficiency of the motor.
Alternatively, electronically commutated motors generate the alternating field required via electric switching, the “frequency converter”. No brush loss is produced and the motors are maintenance-free. It is only in the last few years that major advances in the fields of electronic power components and circuit design have allowed these high-performance motors to be produced at an affordable price. Torqeedo motors are always electronically commutated motors with tailor-made power electronics.
Permanent-magnet excitation
Torqeedo motors are always permanent-magnet excited motors rather than electromagnetically excited. An electromagnetically excited motor generates the required magnetic field by means of a second coil field. This makes the motor less expensive but at the price of greater volume and weight compared to a motor with excitation from a permanent magnet, and also results in significantly higher power consumption and lower efficiency. Permanent magnets, however, can generate the required magnetic field while avoiding loss of performance due to the excitation coil.
External rotor motors
A key structural design element is the type of rotor, with Torqeedo typically opting for external rotor motors over disc rotor or internal rotor designs. Internal rotors constitute the classical construction of an electric motor, where the rotor is surrounded by the stator. The rotor is the part of the motor that rotates, is connected to the motor shaft and is also called the armature. Since, with an internal rotor, the coils are on the outside, the motor has advantages with regard to cooling. However, compared to other structural designs, it generates relatively low torque.
A disc rotor generates torque by arranging the axle of the magnetic field parallel to the shaft instead of radial to the shaft. This allows geometries to be realized where the electromagnetic force is generated well away from the axle, producing greater torque with the same force. However, outboard motors with direct water cooling have a disadvantage with the disc rotor layout. Disc rotor motors cannot be installed direct in a pylon due to their very large diameter.
In external rotors, though, the coils are located on the inside. The magnets are situated on a bell rotating on the outside. External rotor motors thus achieve significantly greater torque than internal rotor motor with the same structural form, making them preferred for most of Torqeedo’s output.
Radial flux motors
Direction of the magnet field causes Torqeedo to go typically with radial flux motors rather than transverse flux motors. In this case the magnetic field is vertical to the rotational axis. Rotational movement comes from a lateral (rotational angle) offset between stator and rotor. In transverse flux motors, though, the magnetic field is largely parallel to the rotational axis. Rotational movement also comes from a lateral (rotational angle) offset between stator and rotor. Transverse flux motors need 3-dimensional magnetic flow management and are therefore complex for marine applications, believes Torqeedo.
A special fan
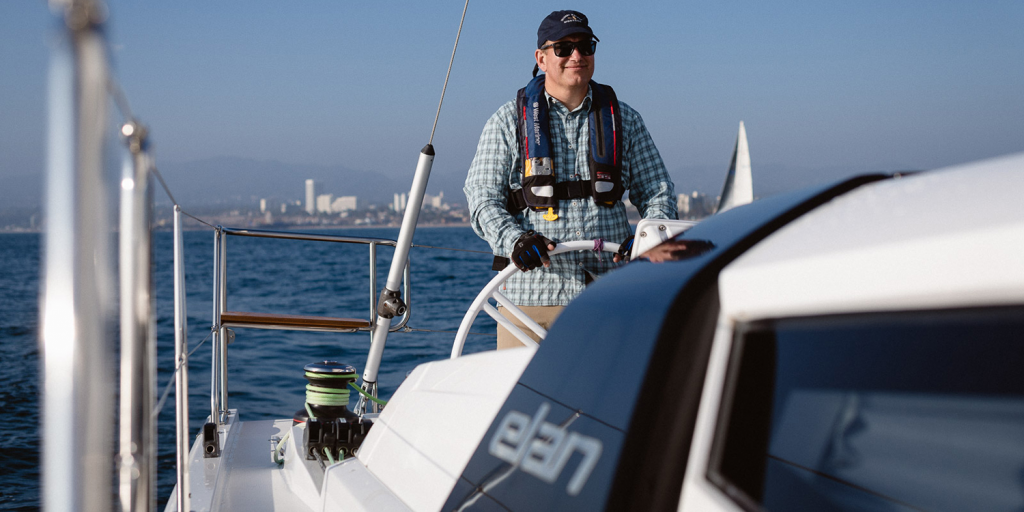
Dr Charles Kuehmann leads materials engineering at two of the world’s most innovative companies, Tesla and SpaceX. An avid sailor, he is also the owner of an Elan GT5 sailboat with a Torqeedo Deep Blue hybrid drive system. “Converting to hybrid-electric could bring a lot of advantages,” recalls Kuehmann. “I wanted to prove it. I chose the 25 kW Deep Blue saildrive system, and since I was already in contact with Torqeedo, I knew precisely which components would be involved in a Deep Blue Hybrid installation, their dimensions and how much they weighed. A sailboat is all about weight and balance. I needed to keep the weight low and as close to the centerline as possible.”
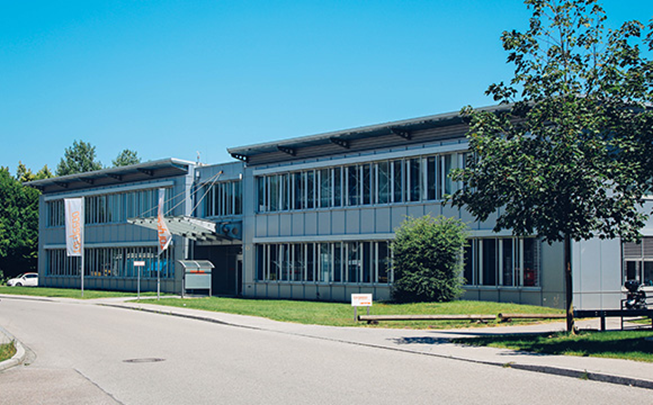
Now, looking ahead from its headquarters in Gilching, Germany, Torqeedo sees plenty of space for further growth. It estimates that today’s global market share of electric boat drives is approximately 2%, similar to the overall market share of electric cars. On protected lakes, electric drives make up most of the market because combustion engines are limited or banned. The brains behind the company are provided by a more than 200-strong international team specializing in mechanical design, electronic development, software programming, procurement, production, marketing, controlling, sales, service and management. For more info, see www.torqeedo.com.
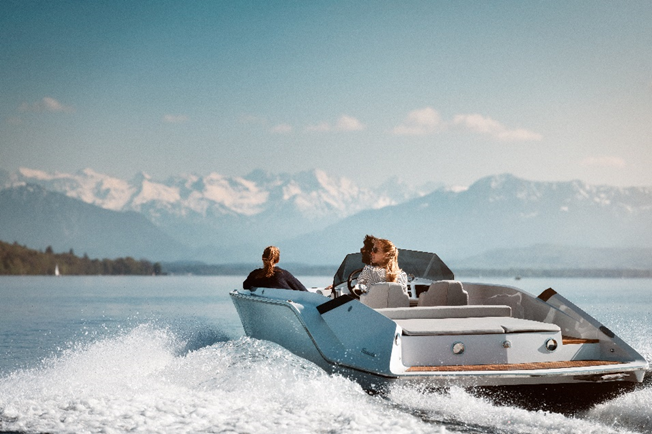