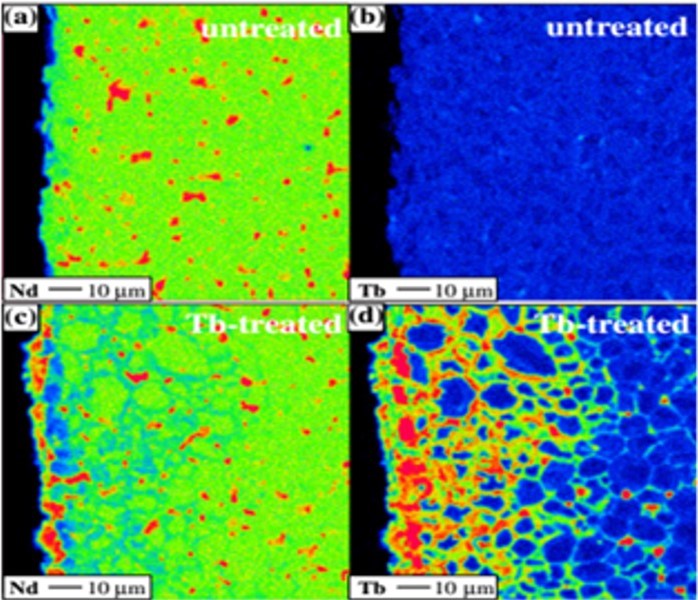
Permanent magnets (PM) are the heart of the drive systems used in the e-Mobility industry. The stronger the magnet is, the higher the higher the motor’s output and the smaller and lighter the motor can be built. But a powerful magnet must also be able to resist demagnetization by heat or a magnetic opposite field. The Dutch company Bakker Magnetics uses two new techniques with which permanent magnets can be produced even stronger and more robust: Grain Boundary Diffusion (GBD) and Grain Refining Technology (GRT). Major advantage: less Heavy Rare Earth Elements (HREE) are used.
The quest for higher magnet grades never ends. Ever since the industrial production of permanent magnets, scientists and engineers have been developing new material compositions and production techniques to increase the energy density of permanent magnets. The newest and most powerful PMs are neodymium magnets (NdFeB). And those magnets are also constantly being developed. For example, the energy density (BHmax) of neodymium magnets has increased over the past twenty years from an average of 250 to 450 kJ / m3. The resistance (coercivity) to demagnetization by heat or a magnetic opposite field is also increasing. Nowadays, a PM with a coercivity of 2,800 kA/m can already be produced very well in series.
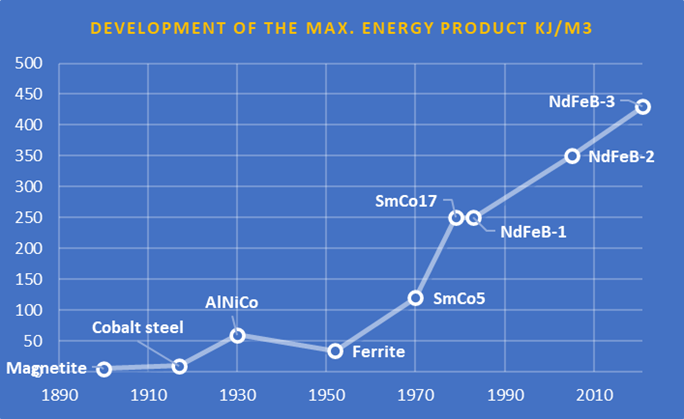
Natural enemies
For the production of permanent magnets, Bakker Magnetics has a joint venture with one of the world’s largest magnet manufacturers in the San Huan group. IJsbrand Velzeboer is Bakker’s sales engineer e-mobility and keeps an eye on the magnet innovations for the automotive industry. He has recently written a white paper on the subject, from which this article is derived.
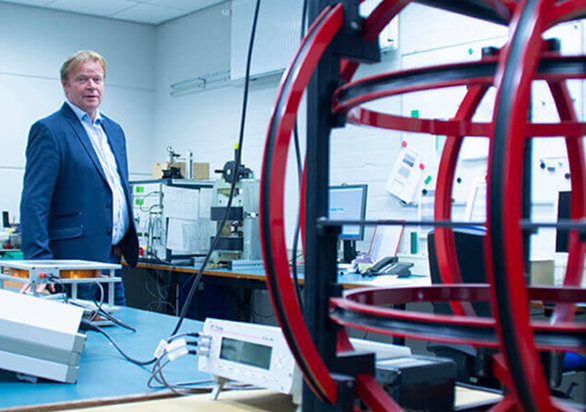
“If a magnet has 10% more energy density, you can directly take that higher force off the weight of the magnet. So you need less magnet volume and you can build lighter. This is important for car manufacturers. But magnetic force is not the only thing we have to take into account. A neodymium magnet has three natural enemies: corrosion, high temperature and a magnetic opposite field due to the eddy current effect. All these factors cause a decay in force. We can combat corrosion by potting the magnet or providing it with a good coating. Resistance to high temperature and magnetic opposite field must be resolved in the raw material composition and the production process. And there we have now taken two important new steps with GBD and GRT.”
HREE
To explain the new techniques, the traditional production method must first be considered. The following elements can be found in an average neodymium magnet used in e-mobility:
Fe | Nd | B | Co | Dy | Pr | Va | Nb | Al | Ga | Cu | Tb | |
42,5% | 31,5% | 1,0% | 7,5% | 5,0% | 5,0% | 0,5% | 0,5% | 0,5% | 0,5% | 0,5% | 5,0% | 100% |
LREE | HREE | LREE | HREE |
Neodymium and Praseodymium are the Light Rare Earth Elements (LREE). The Heavy Rare Earth Elements (HREE) Dysprosium and Terbium are added to realize the higher resistance to demagnetization. All metals are combined and melted. They are then cooled by means of strip casting, after which flakes are formed. These flakes are broken and milled into small particles. The raw material mix is then pressed into a mold. The magnet with a homogeneous structure is ultimately created by means of sintering and a special heat treatment.
According to Velzeboer, the application of the HREE’s Dy and Tb is particularly inefficient: ‘These rare and therefore precious metals are present throughout the entire magnet, while they are actually only needed on the outside of the magnet to protect the magnet against heat and counter-field. In addition, the inactive particles Dy and Tb in the center of the magnet take the place of neodymium particles that can give the magnet more magnetic force. ”
Grain Boundary Diffusion
This problem has been solved by the new GBD technique. The HREE’s Dy and Tb are no longer in the basic raw material mix, but are impregnated into the outer layer of the pressed and sintered permanent magnet using a spray method. Due to a special heat treatment, the HREEs penetrate even further into the magnet, spread and form a protective layer around the NdFeB particles, up to a depth of about 5 mm. Because the vast majority of HREE particles are in the outer shell of the magnet, much less heavy rare earth metals are needed than with the traditional method. Velzeboer: “GBD provides a significant reduction in the use of Dysprosium and Terbium in permanent neodymium magnets, often more than 70%. This solution is more sustainable and cheaper. Because we can process more neodymium in a magnet, we make the magnet even more powerful, while retaining resistance. The result of this is that smaller and lighter motors can be built with the same output. With GBD we can create new magnet degrees that we would not have dared to dream before.
Grain Refining Technology
The second new technique is Grain Refining Technology (GRT). This method makes it possible to produce H (max. 120°C) and SH (max. 150°C) magnet grades in series, completely without the use of HREE’s. “The technology is not as new as GBD, but it has also resulted in a significant improvement in magnet technology,” says Velzeboer.
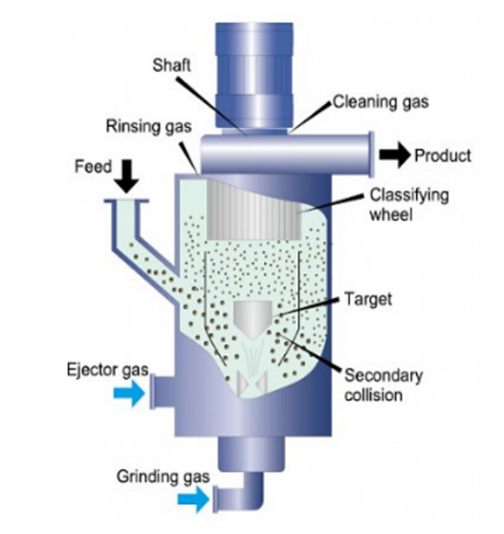
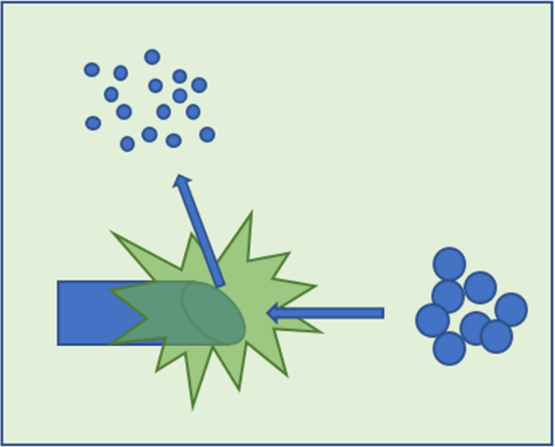
“You can also achieve a higher magnetic grade by mixing the metals better. And this can be done by making the particles even smaller by means of jet milling. The flakes that arise from the production process are “broken” with the help of hydrogen and then “shot” into even finer particles with jet-milling. This creates a very fine homogeneous powder with even more magnetic particles that can all face in the same direction as a line of soldiers. With the old technique we were on a particle size of an average of 5.24 μm. With GRT we arrive at 4.34 μm. This is a significant reduction. This makes the magnet stronger and gives it a higher resistance to degaussing, compensating for the lack of HREE’s. And if this is also combined with GBD, even new levels are reached. ”
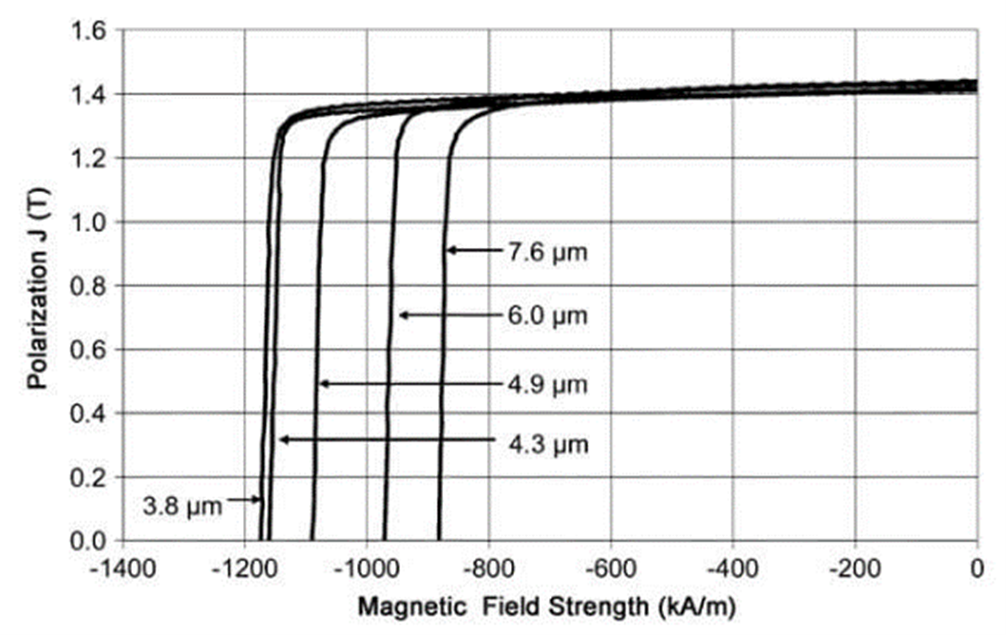
Better performances
According to Velzeboer, car manufacturers and suppliers can push their boundaries considerably with the new magnet technology: “The new grades significantly improve the performance of the electric drive and enable a more compact, lightweight construction. But this is not all. The design of the magnetic rotor and the precise mounting of the magnets can also optimize the drive, delivering more power. And this is very important. For example, a very high angular accuracy of 0.05 ° in the assembly or very small tolerances of +/- 0.03 mm in the production of the magnets. Car manufacturers can simply expect this high quality from their magnetic partner, and we can therefore also meet this. E-mobility is a fantastic growth market, in which we help more and more customers from magnet production to prototyping and the eventual series production and just-in-time delivery of the assembly. True co-creation, which has become even more exciting than it already was due to the new magnetic technologies.”
For more info and to access the white paper, see www.bakkermagnetics.com.