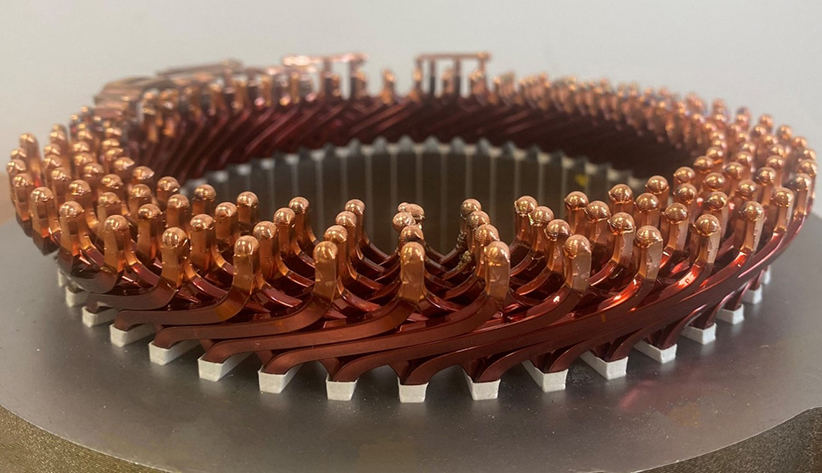
The need to increase the rate of joining electrically conducting components has become critically important in the electric vehicle sector as it is emerging to be the bottleneck of manufacturing, according to Alex O’Farrell, development engineer with Cambridge Vacuum Engineering. As a maker of welding machinery, the UK-based company works close to the subject. In a recent presentation prepared for the 75th International Institute of Welding Annual Assembly & Conference in Tokyo, O’Farrell made his case for electron beam welding technology, highlighted here.
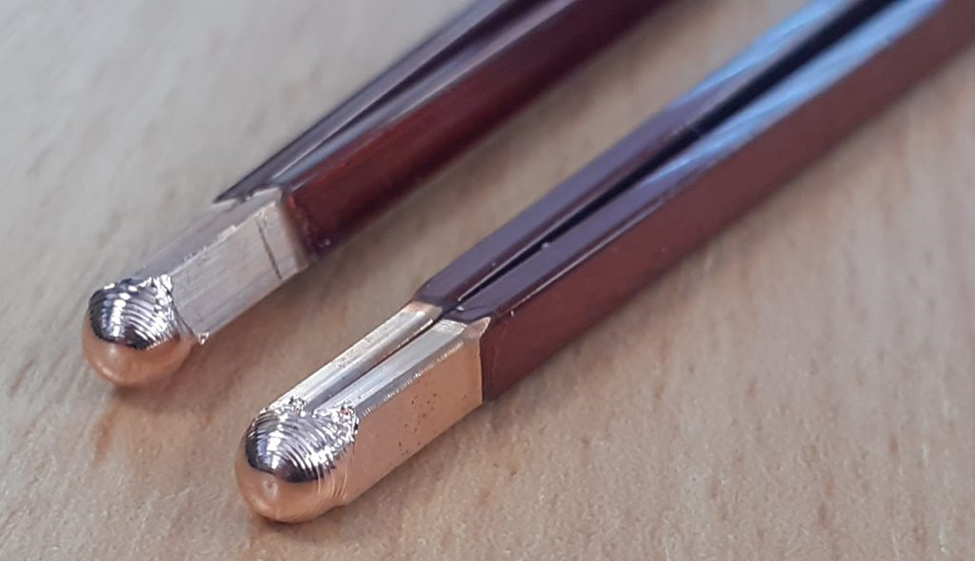
The components of significance are electrical connectors and wires which can be sub-millimeter thick foils or several millimeter thick rectangular section wires. The material most used for these components is copper due to its low cost, high electrical conductivity, and plentiful availability. The high thermal conductivity of copper and low thermal input required for the components in proximity of the joining processes leads most manufacturers to choose laser welding for their high throughput manufacturing.
Laser welding of copper is challenging primarily due to the wavelengths of commercially available lasers typically being red and infrared, these do not easily couple into copper due to the high reflectivity. The reflectivity also contributes to limit the beam angle of incidence, meaning the process must integrate mechanical repositioning of the welding head.
The short focal depth of field of a welding laser also creates a high failure rate in the manufacturing, it requires high precision of machines in the manufacturing line to ensure the parts are prepared and held accurately at the correct working distance so that the weld executes correctly, repeatably. These drawbacks experienced when laser welding copper are issues that are not relevant, however, to electron beam welding, says O’Farrell.
Electron beam welding suffers no reflectivity issues to prevent it coupling into materials, the focal depth is multiple times longer and is rapidly adjustable during the process as the focusing is performed by electromagnetic coils, he maintains.
The rapid speed of beam positioning by electromagnetic coils and commercial availability of significantly higher beam power supplies are the most important advantages in allowing electron beam to process hundreds of copper welds per minute. The rapid rate of processing means the seconds taken for the vacuum chamber to evacuate ready for welding become negligible, furthermore, the fact that the welds are performed in a vacuum chamber mean the resulting weld has no porosity and impurities in the connection, optimizing electrical performance and vehicle efficiency.
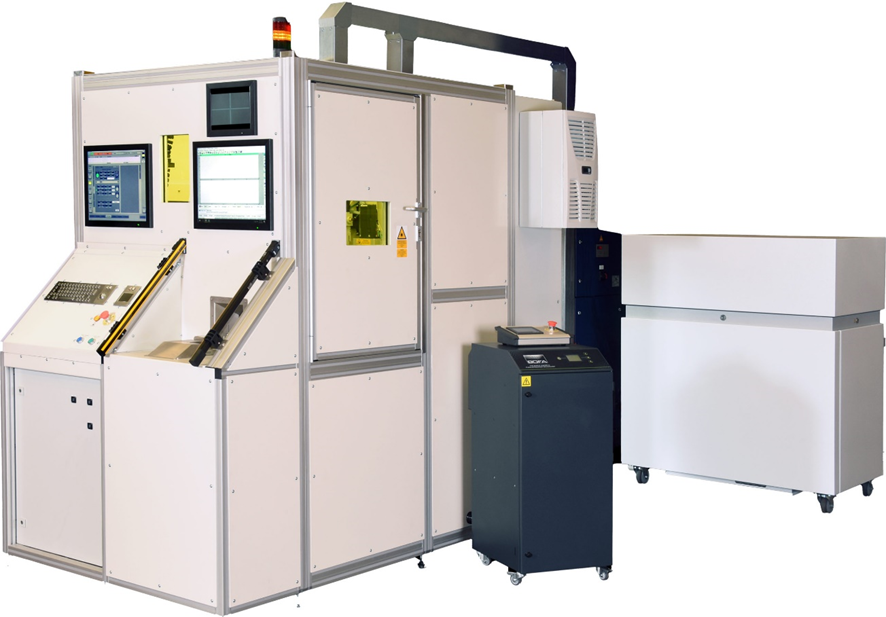
A builder of both laser beam and electron beam welding machines, Cambridge can tailor them with numerous customizations for specific manufacturing requirements. In June, it launched a new electron beam welding machine for electric vehicle components including batteries, shunt resistors, motor stators, hairpins and invertors. For more info and O’Farrell’s presentation, see www.camvaceng.com.