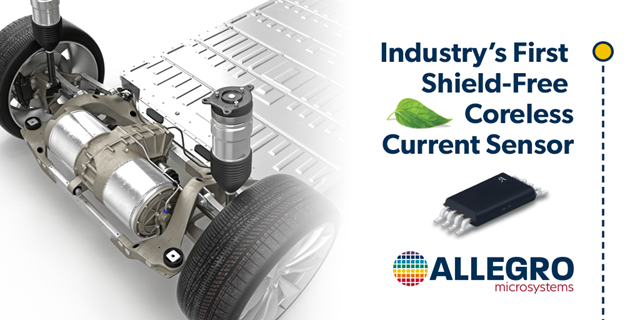
A standalone Hall Effect current sensor that is coreless and shield-free has been developed by Allegro MicroSystems. It’s an industry-first that delivers a new solution for electric vehicle designers, says the company.
The new ACS37612 measures currents from 200A to more than 1000A flowing through a printed circuit board or a busbar with a typical accuracy of 1% yet without requiring a magnetic concentrator core or a shield. The differential Hall-elements used to measure the magnetic field provide great immunity to stray magnetic fields without the need of a laminated shield, reducing design size and bill of materials. It is ideal for demanding electric vehicle applications such as high voltage traction inverter phase current measurement, 48V starter generators and battery disconnect.
“We created the ACS37612 in direct response to trends in the xEV market,” explains Georges El Bacha, product line manager. “It is the first solution that provides a truly coreless method of accurately measuring hundreds of amps in a very small formfactor, solving a key challenge for automotive engineers.”
During acceleration, hundreds of amps flow through the traction motor inverter of an electric vehicle. A precise measurement of such high currents is vital for safe performance. Engineers have traditionally relied on a low hysteresis, laminated core for such measurements using three to six cores, depending on the number of phases in the motor, said El Bacha.
“Eliminating the cores with the ACS37612 allows manufactures to reduce the space and weight of the inverters, thus increasing the efficiency of the electric vehicle. This non-invasive, contactless current sensor is designed to improve thermal efficiency relative to shunt solutions and is therefore ideal for reducing system energy consumption in 48V e-motor platforms.”
For more info see www.allegromicro.com.