A Guest Article By Freddie Sarhan, Vice President of Business Development, Calnetix Technologies
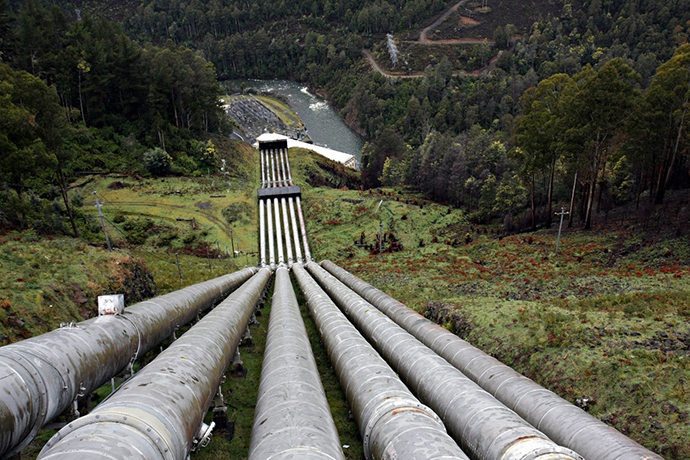
Magnetic technologies are being employed in a wide range of applications to solve real-world problems involving high-speed machinery, especially in hostile or difficult environments. In this article, we will examine an interesting application: waste energy recovery from pressure reduction in natural gas pipelines.
Natural gas is pressurized to facilitate transportation across long distances through pipelines. The pressure must be stepped down to lower levels for safe delivery through local-distribution networks. Pressure reduction is most commonly accomplished with mechanical regulating valves. These pressure letdown devices (PLD) are generally effective but also waste a significant amount of energy. Ideally, this kinetic energy can be captured and converted into electrical energy using a generator loaded turboexpander.
Magnetics as Enabling Technology
Calnetix Technologies has leveraged its long expertise in advanced magnetic technologies to create a new approach for energy capture in natural gas PLD stations. This solution, called the FreeSpin™ In-Line Turboexpander (FIT), has shown great potential in test facility and field trials to provide a reliable and cost-effective solution.
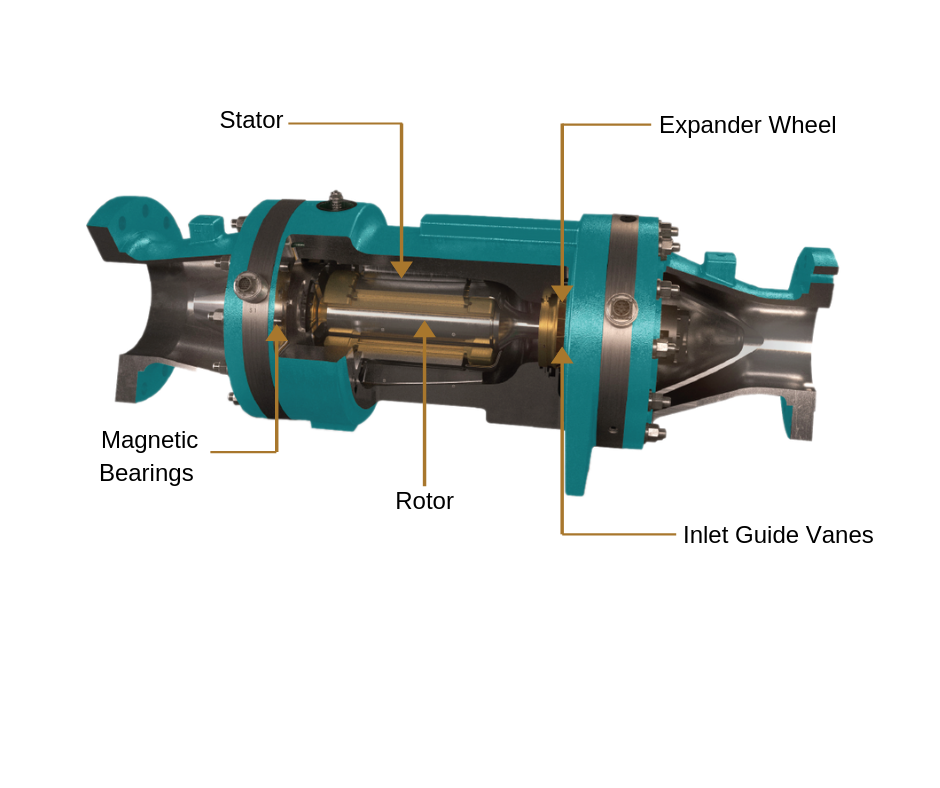
The 280 kW FIT (Figure 1) consists of an integrated high-speed turboexpander and a high-efficiency permanent magnet generator, both driven by a single spinning rotor levitated on non-contact active magnetic bearings (AMBs). The direct-drive generator has variable speed and load capabilities and can run at rated speeds up to 26,500 rpm. The hermetically sealed FIT module eliminates the possibility of leaks between rotating parts with no lubrication and dynamic seal systems needed.
Calnetix’s active magnetic bearing system (Figure 2) provides significant advantages over ball or fluid film bearings in terms of footprint, losses, operating efficiency, remote monitoring capabilities, power consumption and reliable performance in harsh environments. Since the moving parts never come into direct contact with each other, friction losses are eliminated. Special encapsulation and canning technologies enable Calnetix’s turboexpander system to be cooled by the natural gas flowing through the system, so that auxiliary cooling systems and dynamic seals are rendered unnecessary.
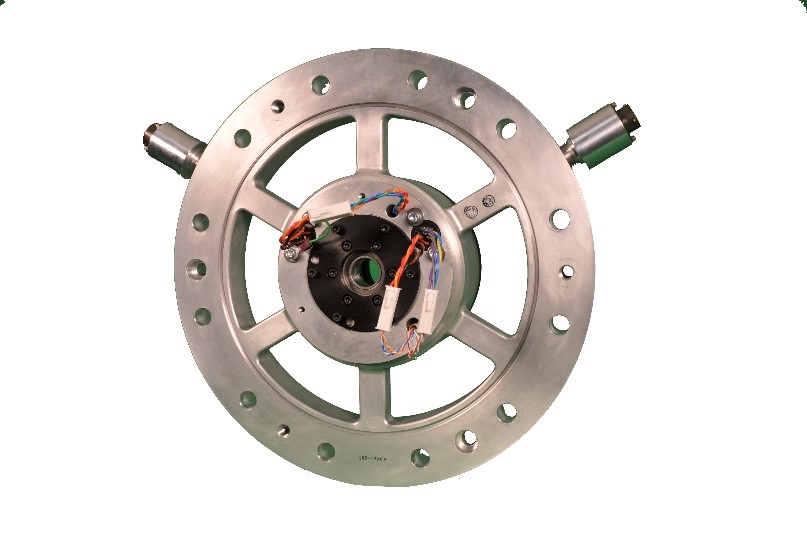
Figure 2. Calnetix Active Magnetic Bearing
Calnetix’s AMBs have built-in diagnostics capabilities for monitoring the health and performance of the system. The high-frequency data-capture hardware and interface enable identifying, analyzing and archiving of the health and historical performance of the machine remotely. This protects the equipment and provides process characteristics that can provide diagnostics of the gas flow. Calnetix’s graphical user interface (GUI) can be used to view real-time process data, such as changes in mass flow, density and temperature without any additional instrumentation.
The Calnetix magnetic bearings use a homopolar, permanent magnet bias topology. Homopolar refers to the direction of the bias flux, which is oriented either uniformly into or uniformly out of the shaft at any circumferential location. This topology reduces rotor eddy current losses compared to conventional designs. A permanent magnet is used to produce the bias flux for the bearing, resulting in several advantages compared with electromagnetic bias as follows:
- Less power is consumed by the magnetic bearings
- The bearing has a more linear force/displacement characteristic due to the contribution of the large, fixed reluctance of the permanent magnet to the bias flux path
How FIT Works
Figure 3 is a functional diagram that illustrates how the FIT works in a natural gas PLD station.
(1) The high-pressure gas flows into the turboexpander. Because the pressure drop is often accompanied by a corresponding temperature drop, a preheater (using natural gas as fuel) can be added at the inlet.
(2) The high-pressure gas then expands through the radial turbine wheel reducing its pressure.
(3) The low-pressure gas exits the turboexpander and flows into the distribution and delivery network for end users.
(4) The energy produced during the pressure reduction process drives the generator to create electrical power.
(5) Any excess high-pressure gas not directed through the turboexpander is expanded by the conventional pressure regulator, which is installed in parallel with the turboexpander.
(6) The produced electricity enters a power electronics unit, which can be programmed to specific power requirements and sold into the grid.
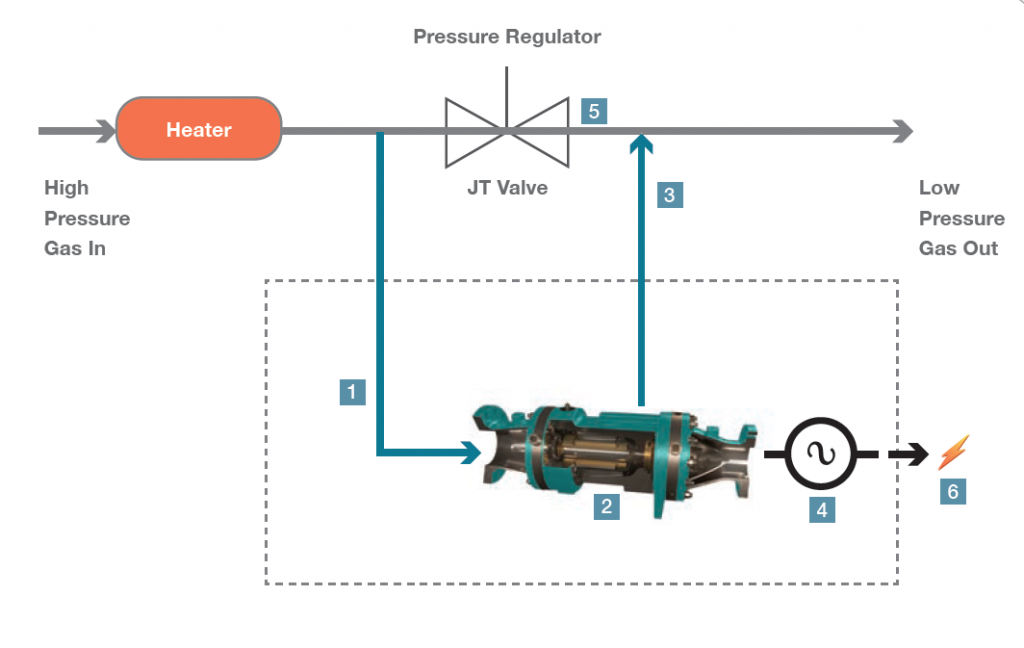
Payback Analysis
There are more than 300,000 natural gas pressure reduction stations around the globe. The amount of waste heat that could be converted into usable electricity is significant.
The capital investment, installation costs and ongoing maintenance expenses are minimized by the advanced magnetic system and are offset by revenues generated from the resale of electricity into the grid.
As shown in this graph (Figure 4), the return-on-investment period for the 300 kW magnetics-enabled turboexpander will vary, depending on the wholesale price of electricity, ranging from 1.1 year at $0.25 per kilowatt hour to 5.5 years at $0.05 per kilowatt hour.
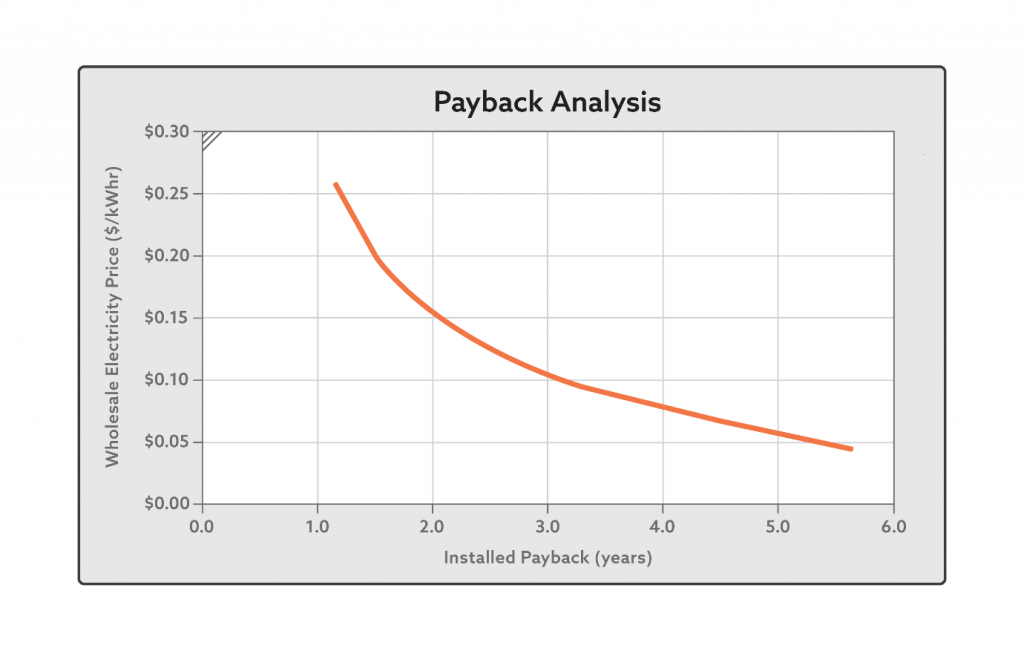
A turboexpander unit developed by Baker Hughes, a GE company, in conjunction with Calnetix Technologies, has been in service for over a year at a PLD station in Italy. It has a design lifespan of over 10 years without any significant maintenance. Based on preliminary data, it is estimated that it will produce over 1.6 million kWh per year.
Summary
The basic underlying technology inherent in the FreeSpin™ In-Line Turboexpander for gas PLD applications is derived from experience with the same building-block tools developed and deployed by Calnetix in multiple applications around the world. This technology offers considerable benefits for the conversion of waste energy into usable electricity, in terms of low initial installation costs, small footprint, high operating efficiency and near-zero maintenance or service downtime, while also reducing heat release into the environment. For more info, see www.calnetix.com
About the Author:
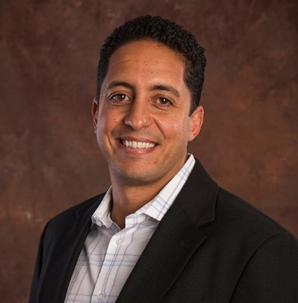
Freddie Sarhan is Calnetix’s Vice President of Business Development, responsible for new application development and commercial business. He joined Calnetix in 2018 and has over 20 years of experience in the power generation, energy and aviation sectors, including previous positions at Praxair Surface Technologies, ABB and Capstone Turbine. He began his career at Rolls-Royce as a member of the industrial gas turbine development team. He holds a Bachelor of Science in Mechanical Engineering from McGill University.