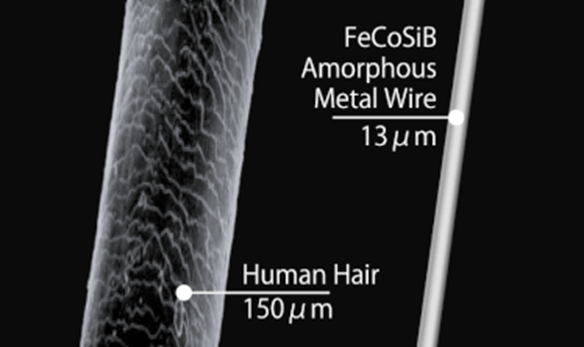
Recent tests of automated passenger buses in Japan have further validated the development of highly sensitive magnetic impedance sensors using Aichi Steel’s amorphous metal magnet wire for guiding the vehicles, especially in places where global positioning signals are weak.
Made of FeCoSiB alloy wire with a diameter of 20 micrometers and less, the sensors have a sensitivity more than 10,000 times greater than conventional magnetic sensors. The wire is amorphous without a crystalline structure and exhibits ideal soft magnetism characteristics making it perfectly suited for high sensitivity sensors, says Aichi. It produces the wire from the raw material stage using its proprietary material technology. The sensor system is developed by its business unit, Aichi Micro Intelligent Corp.
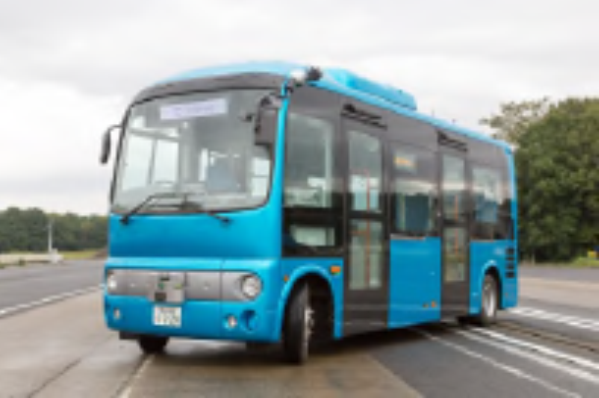
Aichi announced the results of the latest testing in February. Since 2017 it has been providing its system for automated driving demonstration testing being conducted throughout Japan in cooperation with various government agencies.
In the latest road tests, an automated driving bus equipped with the MI sensor modules provided by Advanced Smart Mobility Co., Ltd., traveled repeatedly in a 1.4 kilometer section in Tama New Town with magnetic markers laid underground at an interval of 2 meters. The area is hilly country rich in undulations and slopes. There are many places where pedestrian bridges and roadside trees make the reception of GPS signals difficult.
An MI sensor module is affixed to the base of vehicles to measure the fitted vehicle’s position with high accuracy from the weak magnetic force of magnetic markers fitted along the road and to control steering equipment so that the vehicle passes over the magnetic markers. Going forward, Aichi plans to continue its efforts in verifying the system especially for such conditions.
The magnetic impedance effect is an electromagnetic phenomenon where the impedance of a magnetic material changes relative to the strength of the external magnetic field when a high frequency current or pulse current which causes a skin effect on the magnetic material is applied. When amorphous wire is used as the magnetic material, the effect is particularly marked.
According to Aichi, when the frequency of the pulse current applied to the amorphous wire is increased to around 10 MHz the domain wall movement is suppressed, and the magnetization mainly occurs by the rotation of the magnetization vector. Unlike other types of magnetic sensors with domain wall movement, MI Sensors can attain ultra-high sensitivity with extremely low noise. The latest MI sensor achieves very high sensitivity by applying a pulsed magnetic field equivalent to .5 to 1GHz.
In operation, a pulse current is passed through the amorphous wire and the reaction relative to the external magnetic field is detected by the pickup coil wrapped around the wire. Charging the amorphous wire with a pulse of current creates a change in impedance that varies greatly depending on the external magnetic field as a result of the MI effect.
For more info, visit: www.aichi-steel.co.jp