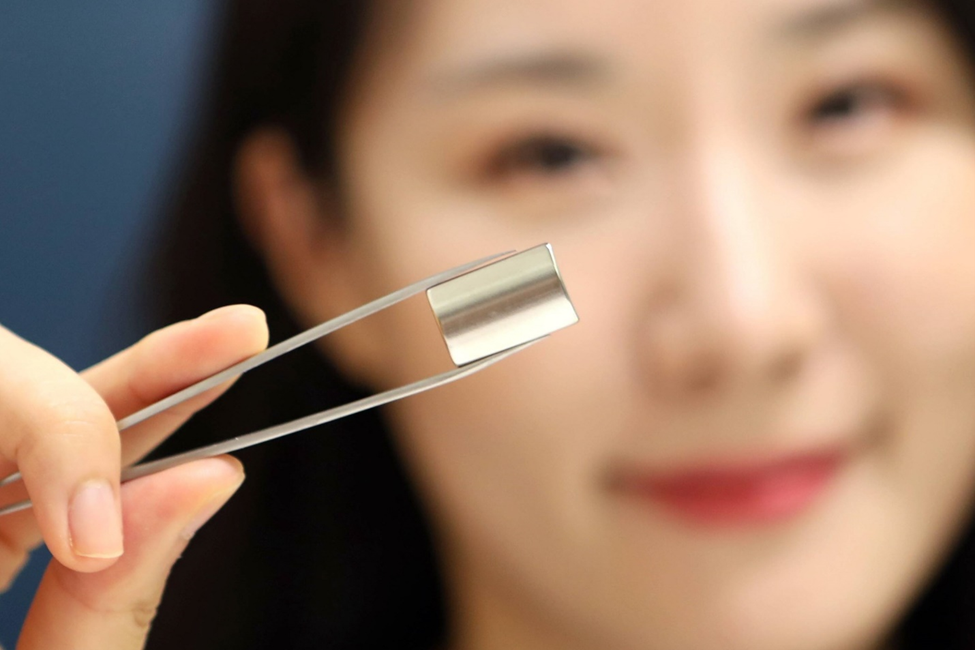
With accolades for its new Nexlim, which it calls “the world’s thinnest magnetic component”, and the recent development of its “eco magnet”, Korean materials and components company LG Innotek is making impressive headway in challenging the dominance of companies in China and Japan for leadership of innovation in fundamental magnetics technology.
In late April, the company won a prestigious Edison Award for its Nexlim magnetic component designed to open a new era of ultra-slim and ultra high-definition TV. It won a bronze award in the commercial technology category for engineering and robotics in the annual competition, often referred to as the Oscars of Innovation. More than 3,000 judges composed of executives and scholars from industrial fields across the US participate for strict review and evaluation conducted for over seven months. Gold, silver, and bronze winners are chosen annually in 16 fields.
At the heart of the product is innovative ferrite material developed by LG Innotek to make high-definition thin-screen televisions which now, the company reports, is being advanced for applications in electric vehicles.
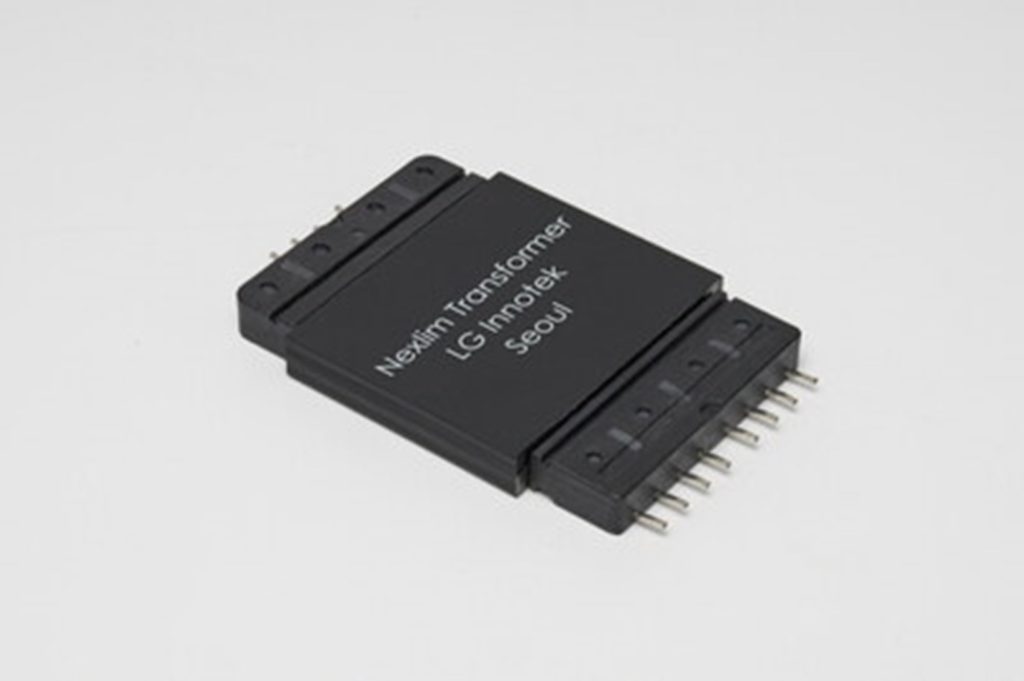
Nexlim is a magnetic component that is mounted on the TV power module, vehicle power and chargers to change the voltage, or to perform the role of removing unnecessary signals that are generated from the current waves. It plays an important role of minimizing the power loss from heat generation to increase the energy efficiency of electronic products and electric vehicles.
The popularity of ultra-slim, high-definition TV with bigger screen and thinner size has challenged TV manufacturers in their product design. The volume of magnetic componentry such as transformers and inductors have had to be increased more than three times, and reducing the TV thickness at the same time was technologically impossible. Development of an ultra-thin magnetic component to replace the existing magnetic component that occupies half of the overall TV thickness has been a major priority. At first, LG Innotek succeeded in commercializing Nexlim with 9.9mm in thickness. The technology was enhanced even more to lessen this to only 7mm last year.
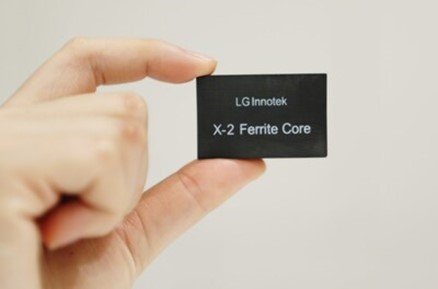
The key to minimize thickness is a high-efficiency ferrite that is used as the main material in Nexlim. LG Innotek independently developed and applied the ferrite magnetic material (X-2) to reduce the energy loss up to 40% compared to other general magnetic materials, and to increase the power density by three times.
Research Fellow Bae Seok, developer of Nexlim, explained that “By introducing the simulation system utilizing AI, we were able to find the optimum material composition ratio for maximizing the ultra-low loss and high efficiency performance in just 6 months,” and added “The inductor and transformer, parts for converting the power in the magnetic component, were integrated into one part to lessen the thickness of the magnetic component even more.” The advent of ultra-thin magnetic components such as Nexlim has made it possible to reduce TV power module thickness to as little as 7.2 to 9.9mm and overall TV thickness to only 15 to 19.9mm.
Meanwhile, LG Innotek recently succeeded in developing a third-generation ferrite magnetic material (X-3) based on the original technology on the magnetic components that was secured during the development of Nexlim. Energy loss can be cut up to 30% more than the X-2 applied in Nexlim, and the company expects it to play a decisive role in miniaturizing components when X-3 is applied to electric vehicles.
“With this Edison Award winning, LG Innotek has once again presented its unrivaled technology in the magnetic material & component field to the global customers,” said Kang Min-seok, CTO of LG Innotek. He also added, “We will continue to invest in the advanced development of future innovative materials and take the lead in creating differentiated customer value.”
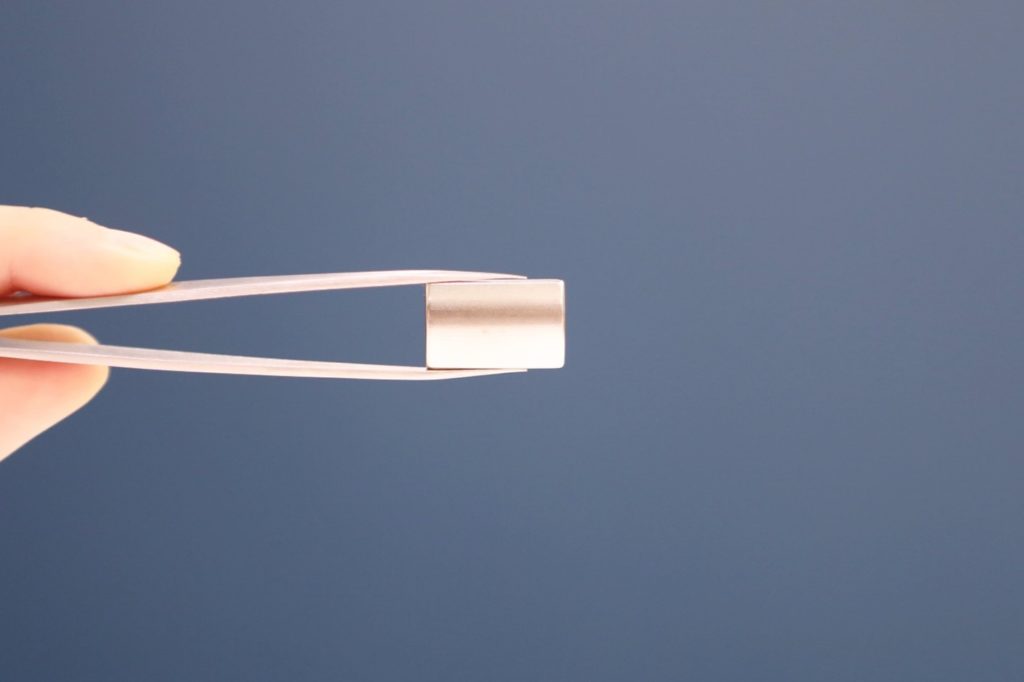
The company’s eco magnet breakthrough came in late 2021 when it announced that it had developed the world’s strongest “eco magnet” in collaboration with the magnet company SGI (Sunglim Group Industry) Co., targeting the global magnet industry led by China and Japan.
The product significantly reduced the use of heavy rare earth (HRE) metals by 60% compared to the previous product. It raised the magnetic performance for home appliances and vehicle steering motors to 14.8 kG (in kilogauss, magnet strength), which is the world’s highest level, said the company, claiming to beat the products of Japanese companies that have led the industry for nearly 40 years. “The industry believes that the technical performance limit of this magnet is 15kG. The magnetic performance of products commercialized so far is only 14.2 to 14.3 kG,” it said.
Applying the magnet to a steering motor is advantageous for reducing the weight of a vehicle, reducing the size of the motor while increasing its output and beneficial for electric and hybrid vehicles that need weight reduction to improve mileage range.
When the eco magnet is applied to a high-pixel smartphone camera, it produces clearer photos and videos by increasing the driving force of the actuator, which moves the lens to focus. As the specifications of smartphone cameras have enhanced, the size and weight of lenses have increased, requiring actuators to have stronger magnetic power. At the same time, as smartphones get slimmer, the demand for small but powerful magnets has increased while the eco magnet generates a stronger magnetic force than other magnets of the same size, maintains the company. The driving power of an actuator can be increased by about 10% without an increase in size so that, even if a lens becomes heavier, the actuator still can move the lens quickly and accurately.
LG Innotek began developing the eco magnet in 2017 and has been focusing on improving its magnetic performance since 2019 while also joining hands with SGI, which has an HRE metal reduction technology. By adding new compounds, the two companies have developed a coating liquid for the eco magnet that uses less HRE metals yet produces especially strong magnetic force in various products and temperatures. In addition, the companies also secured a new magnet material optimized for the coating liquid. The coating is applied to the magnet and the magnet is heated to absorb the liquid evenly.
LG Innotek says it knew that it could not catch up with Japanese competitors’ technologies in a short period of time with the existing development method. To speed up the process, it turned to machine learning for design simulation. Using this technique, the development period, which takes at least two years, was halved. The number and time of experiments were significantly reduced by automating the process of deriving optimal process conditions such as the ratio of HRE metals and heat treatment temperature. Previously, researchers had to repeat experiments hundreds of times, which made the development period long and incurred errors.
Beginning with applications such as steering motors for vehicles and smartphone actuators, the company plans to quickly expand the magnet’s applications to air conditioners, refrigerators, drones, urban flying cars and generators. It also plans to develop a magnet that does not contain rare earth metals at all. For more info, see www.lginnotek.com.