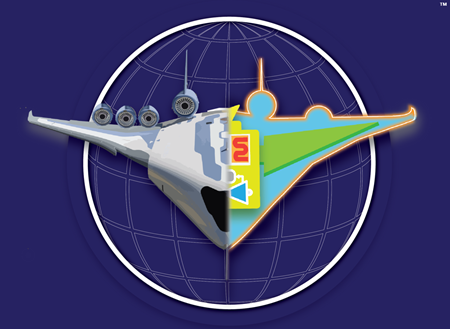
With advanced magnetic performance at their core, three research grants aim to boost the viability of electric motors for propelling commercial single-aisle hybrid-electric aircraft. Advanced Magnet Lab will apply its PM-360 permanent magnet material to develop a powerful new motor. Texas A&M will focus on developing a lightweight and ultra-efficient electric powertrain using carbon fiber. Hyper-Tech Research aims to develop a high-power electric propulsion motor, drive and thermal management system.
The projects are among awards by the US Department of Energy totaling $33 million in funding for 17 projects as part of the Advanced Research Projects Agency-Energy’s (ARPA-E) Aviation-class Synergistically Cooled Electric-motors with iNtegrated Drives (ASCEND) and Range Extenders for Electric Aviation with Low Carbon and High Efficiency (REEACH) programs.
ASCEND projects work to develop innovative, lightweight, and ultra-efficient all-electric powertrain with advanced thermal management systems that help enable efficient net-zero carbon emissions for single-aisle passenger commercial aircraft. REEACH projects seek to create innovative, cost-effective, and high-performance energy storage and power generation sub-systems for electric aircraft, with a focus on fuel-to-electric power conversion technologies.
“Millions of Americans travel on single-aisle aircraft every year, contributing to continued increases in energy use and emissions by commercial airlines,” said ARPA-E Director Lane Genatowski. “REEACH and ASCEND teams will work to lower these burdens by creating innovative new systems to enable more cost-effective and efficient flight systems for commercial travel.”
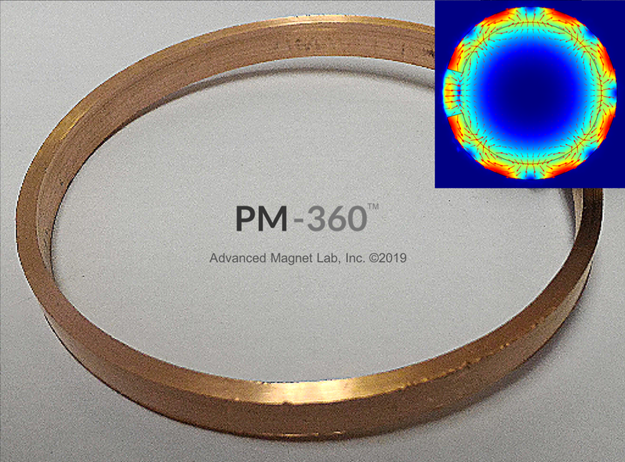
Advanced Magnet Lab’s program will couple the company’s novel permanent magnet rotor and stator technology with integrated power electronics and cooling, which have the potential to enable power densities beyond 12 kW/kg for the full electric drivetrain. Today, aircraft, using gas burning turbine engines, achieve approximately 6-9 kW/kg. AML and its team have proposed a solution that includes a dual permanent magnet rotor based on its PM-360 magnets, enhanced cooling allowing for high current density stator coils, high-power density power converters, and a shared closed-loop cooling system. The PM-360 rotor eliminates the iron used in conventional motors.
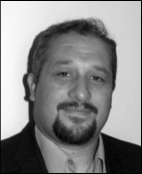
“We are extremely excited to be provided the opportunity to develop and exhibit our capabilities and technologies for the future of aviation,” stated Dr. Philippe Masson, CTO of AML. The company is collaborating with the Center for Advanced Power Systems at Florida State University, which is developing the high-power density power converters which will drive and control the motors. This announcement is for Phase 1 of the program, which is $654,354.
An award of $1.3 million went to Texas A&M whose team will focus on the design, fabrication, and testing of a lightweight and ultra-efficient electric powertrain. The plan is to reach peak power density and efficiency via an axial flux motor with lightweight carbon fiber reinforced structural material, a GaN multilevel inverter, a thermally conductive nanocomposite electrical insulation, and a two-phase thermal management system with zeolite thermal energy storage to absorb the excess heat generated during takeoff. Each subsystem is designed for tight integration with the other subsystems to minimize weight.
With a $2.9 million award, Hyper Tech Research aims to design and demonstrate a multi-MW, high-efficiency, and high-power density integrated electric propulsion motor, drive, and thermal management system. Based in Columbus, OH, the company provides superconductor solutions for medical and energy products.
It plans to incorporate an advanced and high-performance induction electric machine with a novel advanced thermal management technique for synergistic cooling that safely uses cryogenic bio-LNG as the energy source for power generation and a large thermal-battery cooling system to provide a highly compact, light, and efficient thermal management system capability throughout all the different flight phases of a commercial narrow-body aircraft. If successful, the system would allow for a cost-effective motor capable of operating at a higher current density compared with existing conventional non-cryogenic motors without using superconductors.
For more info, see arpa-e.energy.gov/.