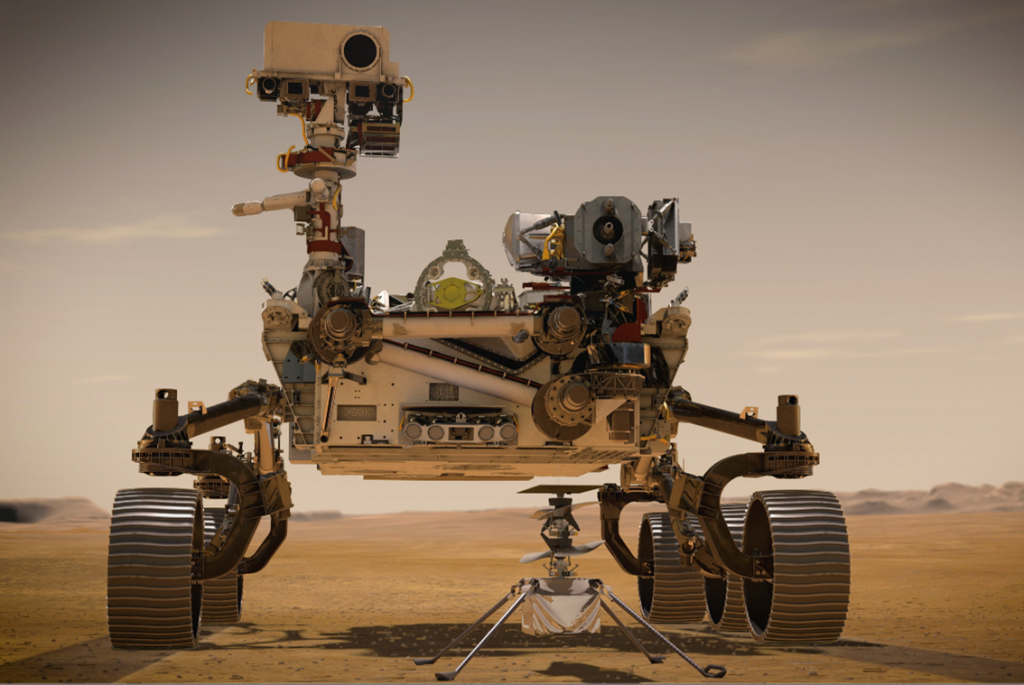
NASA’s Perseverance rover landed on Mars just a few days ago. Was there once life on Mars? This is the question that one of the most complex robotic systems ever built by humankind has set out to answer. Several electric drives and permanent magnet motors from maxon of Switzerland are onboard to handle soil samples and to control the first Mars helicopter, Ingenuity, shown in foreground.
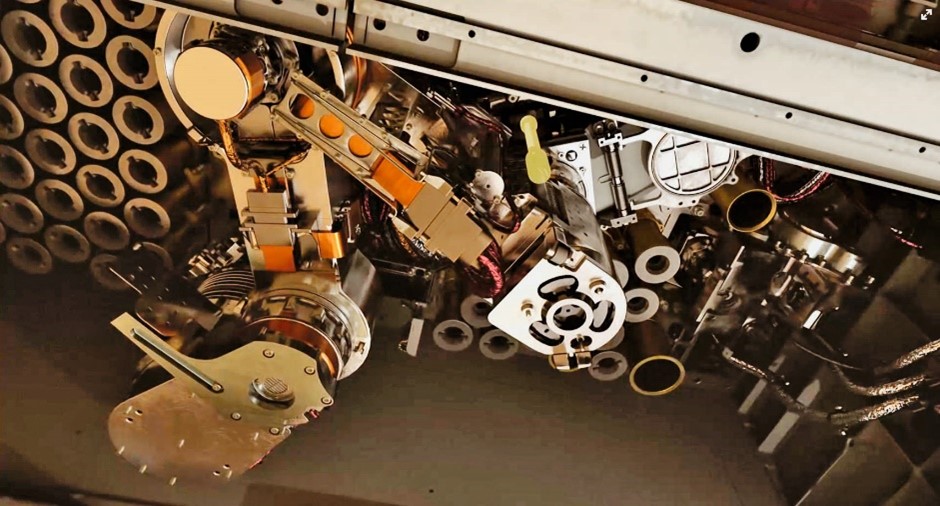
A robotic arm, shown above, moves the soil samples to the volume assessment and scanning stations, then to the sealing station, and finally into temporary storage—all autonomously.
After a journey of more than 470 million kilometers, After a journey of more than 470 million kilometers, the excitement was almost palpable. Will NASA, the US space agency, successfully land a fifth rover on the Red Planet, beginning a series of missions to bring Mars soil samples back to Earth? In all, the Mars Sample Return project is by far the most complex series of missions in the history of unmanned space exploration.
According to plan, Perseverance landed in the Jezero Crater, which was once filled with water, to search for traces of earlier life. The rover looks a lot like its predecessor Curiosity, but it is equipped with more sophisticated measuring instruments and systems. One of its tasks will be to take up to 30 soil samples, place each of these in separate containers, seal them and place them on the surface of Mars for retrieval and return to Earth by later missions in which maxon will also be involved.
There are ten electric drives in the rover. These are responsible for moving the robotic arm that navigates the samples from one station to the next. Additionally, the motors are used for sealing the containers and placing them on the surface of Mars.
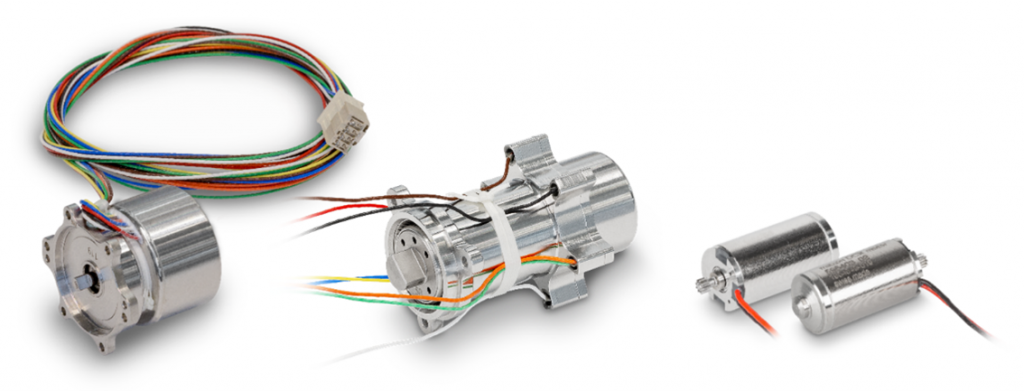
Just like the more than 100 existing maxon drives that have been performing their duties from previous missions on Mars, the motors for Perseverance are based on standard catalog products: specifically, nine brushless DC motors, the EC 32 flat and one of the EC 20 flat motors combined with a GP 22 UP planetary gearhead. The engineers at maxon closely collaborated with the specialists at Jet Propulsion Laboratory for several years to modify and extensively test the drives.
Ingenuity, the drone helicopter attached to the underside of the rover, is destined to perform the first ever flights on Mars in the history of space exploration. It is solar powered and weighs only 1.8 kilograms. Six brushed maxon DCX motors with a diameter of 10 millimeters control the tilt of the rotor blades, which determines the direction of flight. The drives feature high energy efficiency, are dynamic and very light. “In the development phase, we performed extensive tests to make sure that the motors will work as intended under the extreme conditions on Mars,” says Florbela Costa, project manager for the helicopter at maxon.
With this experiment, NASA wants to test the concept for future drone flights. Flying on Mars is a challenge. The atmosphere is extremely thin, roughly comparable to the conditions on Earth at an altitude of 30 kilometers. The first drone flights are scheduled for May.
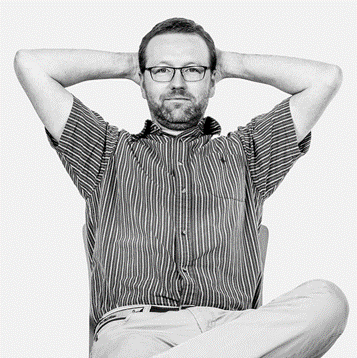
“We are involved in absolutely critical applications. If the robotic arm on which our BLDC motors are mounted doesn’t move, or if the gripper doesn’t work, then the mission will be a failure,” says Robin Phillips, director of maxon’s SpaceLab. The DC motors, gearheads, and encoders face brutal conditions during liftoff, the long journey through space, and the mission on the Red Planet. In a recent blog, he makes these comments about the rigors involved:
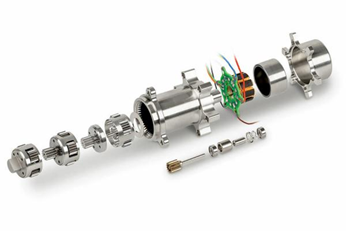
Vibration and shock – The first challenge is to survive the rocket launch. This means that the motor must be resistant to shock and vibration. The vibration is not as strong as people might think: A little more than on a passenger plane, but not much more, and only for a few minutes. Shocks, on the other hand, are something that we need to deal with on a regular basis when working with standard products. These occur mainly during staging, which is when the first stage separates from the rest of the rocket. The resulting forces would destroy normal motors because the rotor would become separated from the stator. That’s why we need to reinforce our drives, for example by encapsulating the rotor and using special welds, special retaining rings, and optimized materials.
Vacuum and radiation – The trip to Mars takes about six months. During this time, the drives need to survive the vacuum and radiation. The most damaging radiation doesn’t come from the Sun, but from high-energy particles from outside the solar system, which can damage the electronics. That’s why we need specially hardened electronics for the Hall sensors on the motors. To be extra safe, we’re installing them in pairs for redundancy. In a vacuum, the durability of components is important. You can’t use a glue that undergoes changes in its chemical properties and loses its adhesiveness after a few days in a vacuum.
Weight reduction – Rockets can carry only a limited mass to other planets. To be as light as possible, we also resort to unusual shapes and use thinner housings, or titanium instead of steel. We also often use the smallest possible drive sizes, because we know that the operating time required is usually shorter than for industrial applications. Higher wear is therefore acceptable.
Atmosphere of Mars – After arriving, the motor must work flawlessly for the entire duration of the mission: Due to the thin atmosphere, the lubricants need to be resistant to outgassing and need to retain their properties. Especially for brushed DC motors, it is also necessary to use the right brush mixture. No patina forms on Mars, which is why we developed special brushes impregnated with a lubricant (silver graphite with 15% MoS2). That’s one of the most important modifications, because regular brushed motors fail after only a few hours in a vacuum.
For more info, see www.maxongroup.com.