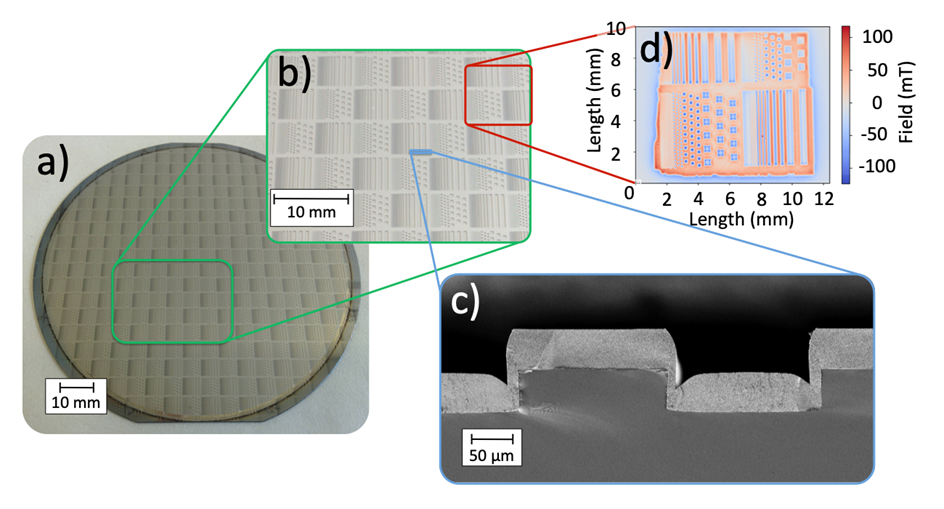
By Nora Dempsey, Staff Researcher, Institut NEEL, Grenoble, France
The discovery of high performance NdFeB magnets, almost 40 years ago, revolutionized the design of electromagnetic motors, generators and actuators. Today they are key components of a range of devices including gearless wind turbines, electric and hybrid-electric vehicles, electric bicycles, hard disk drives and air-conditioners. Researchers at Institut NEEL (CNRS, Grenoble, France) have mastered the fabrication of NdFeB micro-magnets, unlocking enormous potential for the development of Micro-Electro-Mechanical Systems (MEMS) and other micro-scale devices, with applications in areas as diverse as consumer electronics and bio-technology.
The force of interaction between a magnet and another object is proportional to the gradient of the stray magnetic field it produces. Scaling down the size of a magnet, while preserving its extrinsic magnetic properties (remanence, coercivity), leads to an increase of its stray magnetic field gradient. As a result, the magnetic field gradient force per unit volume can be increased by orders of magnitude in micro-scale systems compared to macro-scale systems.
However, downscaling the size of NdFeB magnets is not trivial. Machining of sintered bulk magnets has a lower limit of a few hundred micrometres, due to surface degradation, and is material wasteful. Smaller magnets can be produced by polymer bonding techniques, including 3D printing. However, the remanence of polymer bonded magnets is limited by dilution of the magnetic powder.
The manipulation and integration of small free-standing sintered or bonded magnets can be very challenging. NdFeB hard magnetic films can be produced by physical vapour deposition techniques. To produce a stray magnetic field, such films must be patterned at a length scale comparable to the film thickness, because of the demagnetising field effect.
Researchers at Institut NEEL have produced high coercivity (~ 2 T) and high remanence (~ 1.3 T) NdFeB films of thickness up to 50 micrometres, by triode sputtering onto Si substrates. These films have been patterned using standard clean-room facilities, i.e. photo-lithography and deep reactive-ion etching of the Si substrate prior to film deposition (see figure).
The figure above shows: (a, b) Plan-view optical images of a 50 µm thick NdFeB film deposited on a pre-patterned 4-inch Si substrate together with (c) a cross-sectional scanning electron microscope image of a few micro-magnets and (d) a Magneto-Optical image of the stray magnetic field produced at a scan height of 50 µm above the film.
The size, shape and disposition of the micro-magnets can be adapted to suit specific applications. A chemical mechanical planarization process has been developed to remove material deposited outside of the etched regions, if required. The fact that the micro-magnets are substrate-mounted means they can be integrated into complex micro-devices, and the use of large substrates permits batch fabrication. Deposition is now made on 4-inch substrates, and the sputtering technique used can be upscaled to allow deposition on even larger substrates.
NdFeB micro-magnets made at Institut NEEL have already been exploited in a range of bio-medical applications, in the framework of various academic collaborations. They have also been used to develop prototype micro-mechanical devices with an industrial partner and are presently being integrated into energy-harvester prototypes in the framework of academic collaborations. A maturation project is now running with a local technology transfer incubator (Linksium) to explore the market potential for sputtered micro-magnets and to find industrial partners and clients for a future start-up.

About the author: Nora Dempsey is a staff researcher on the Micro and Nanomagnetism team at Institut NEEL in Grenoble, France. The group studies magnetic systems at the micro and nano scales: from fundamental research to applications in spintronics, energy and life sciences.
For more info, see www.linksium.fr/en/projects/micromagfab and www.neel.cnrs.fr.