New technological approach includes high-precision unbalance measurement, microdispensing and light curing
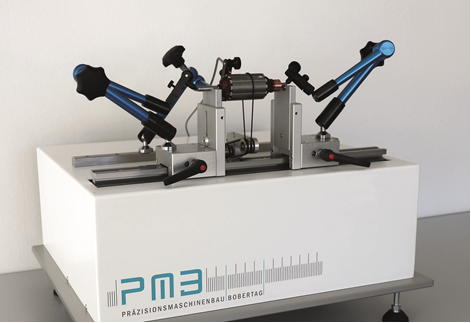
Balancing is required for various types of applications. Up until now, the predominate way to balance an object was through subtractive methods, like machining and lasering. However, a new additive balancing technology for rotating parts, has been developed(new compact balancing system OnDesk500 – balancing rotor of electric motor pictured above). This new process consists of a high-precision unbalance measurement, precise dispensing and very fast curing of specially formulated balancing compounds based on adhesives.
If It Rotates, It Needs Balance
Balancing is not only required for fitting new tires, it is also necessary for most applications that include rotating components, like electric motors, fans, blowers, pumps or turbines. When unbalance is improved, it enhances the quality of the device by reducing vibrations and loads. It enables higher rotational speeds, lower noise volumes and a longer lifetime. Balancing ensures things, like a hand drill being held in a person’s hand with very little vibration; the dampening of noise made by a dentist’s drill as to not frighten patients; or the ability of a fan to run at low noise levels.
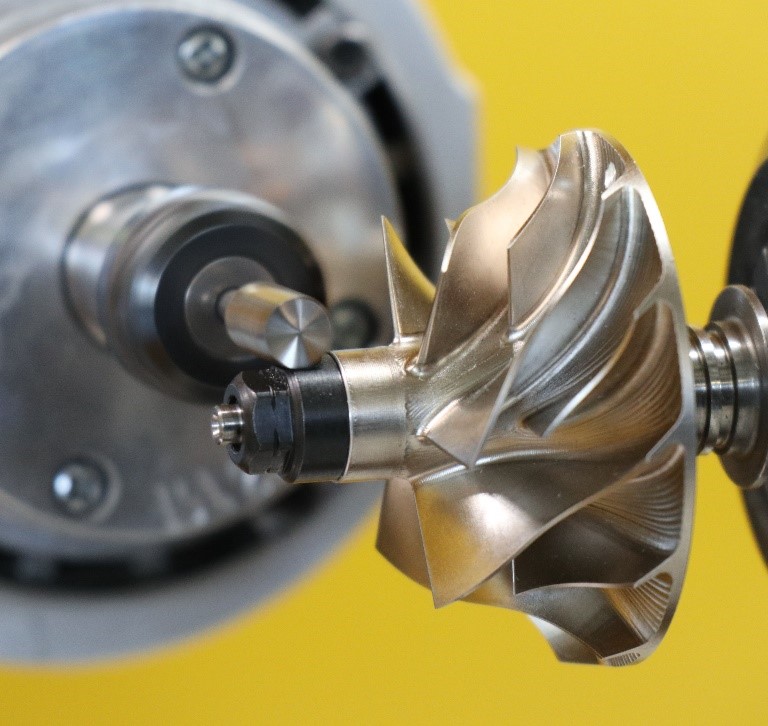
Regardless of the industry, automotive, aerospace, medical technology or mechanical engineering, balancing demands the highest precision. Since unbalance forces increase as the square of the rotational speed, a doubling of the rotational speed means that balancing must be performed four times as well.
In contrast to a car tire, as mentioned above, balancing performed in serial operations is usually subtractive, meaning excess material is removed from the object being balanced. In this type of process, sacrificial material must always be available so that it can be partially be removed as needed to balance. In contrast, additive balancing is more material-efficient, involving the exact amount of material required to balance a unit.
A New Process: High-tech Adhesives as Balancing Compounds
A completely new additive balancing process, based on the use of adhesives as balancing compounds, has recently been developed. In the past, attempts to correct unbalances with two-component epoxy resin did not meet demands. The process was slow, inaccurate and did not reproduce well.
The process is based on an entirely different approach suitable for industrial serial processes that require maximum accuracies without the removal of material from the workpiece. With minimum possible correction accuracies as low as0.1 mg, residual unbalances of 1 mg*mm, as required by the optical industry, can be achieved. Due to its excellent process reliability, this additive approach is also ideal for use in small fans that have medium unbalances of 50 to 100 mg*mm.
This is possible because unbalances can now be measured much more precisely than before. A calculation of the required position and the amount of the balancing compound that will be needed to bring the unit into balance is performed. Once the number is determined a light-curing adhesive is used for correction. This adhesive should have a high density, so that the required mass per adhesive droplet only requires little volume.
Due to its high speed and volumetric accuracy, the application of the adhesive, which can be performed in one or two balance planes, is performed using a non-contact jetting method. The balancing compounds cure completely under high-intensity UV light within a few seconds before a control measurement verifies the result. The balancing is usually completed following a correction step.
Depending on the required cycle time, the dispensing and curing can be performed in either the measurement station or a separate station. Since process steps run simultaneously, this technique can also be used for extremely high quantities and is scalable from small-batch to large-scale production.
Competitive Costs
Besides technical issues, it is important that no matter what process is chosen, it is cost-effective for industrial applications. If the cost of the three balancing methods – machining, lasering and bonding are considered, machining usually has the lowest investment costs. On the other hand, the resulting tool costs, dust and chip removal, as well as time required for tool change can incur ongoing operating costs.
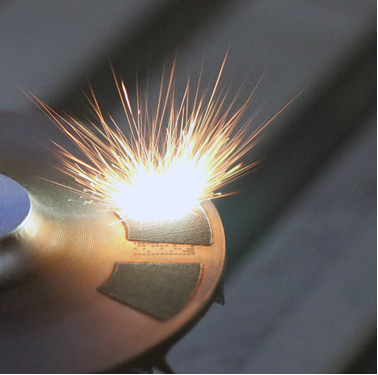
Lasering initially incurs the highest investment costs; however, it offers the lowest operating costs, which is a good option for high-volume applications.
The investment costs for bonding usually ranges somewhere between the two other processes of machining and lasering. Operating costs are incurred by adhesive as a consumable, amounting to 0.03 g of adhesive per unit for typical components.
From a controlling perspective, when deciding on any one of these three processes, annual production volumes and the size of the application should be taken into consideration. In the high-end segment, technical advantages are usually more influential in the decision-making process, than whether the solution is economical.
Machining offers a lasting solution; however, requires excess material, produces chips and is expensive because of probing problems. Lasering represents a precise process but is a subtractive solution.
An additive process is a good alternative solution. Jetting of balancing compounds requires no sacrificial material and offers the highest precision, where subtractive processes are often prohibited for certain assemblies to protect the bearings against dirt.
Put Aside Preconceived Notions
It is important for users to set aside their preconceived objections to all three processes, like ‘will bonding hold’; ‘machining is antiquated’; ‘lasering will cause fine dust pollution’. Instead of prejudging these processes, users should objectively consider their advantages and disadvantages, calculate their economic efficiency, and perform preliminary tests on them.
Short cycle times, freedom from chips and the precise control of mass correction are excellent reasons to consider the new additive balancing process.
For more information, see www.pmb-bobertag.de and www.delo-adhesives.com.
Authors:
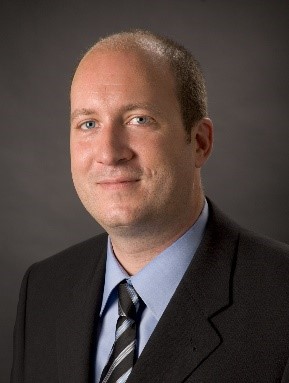
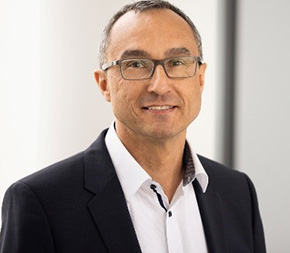