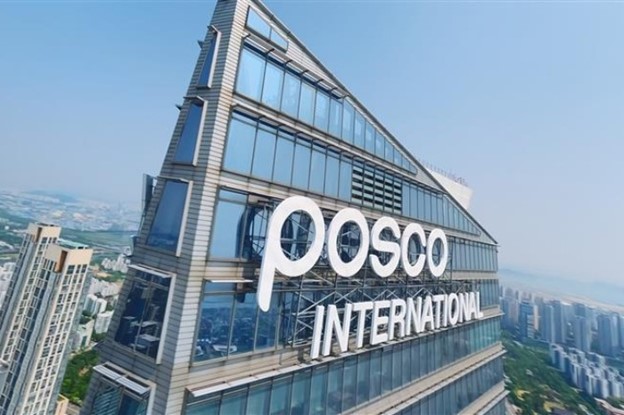
Holding big new orders from automakers for permanent magnets and planning to build a globally integrated enterprise for magnet and motor component manufacturing, Korean steelmaker Posco International announced on March 18 that it has successfully established a complete, integrated supply chain for the production and application of permanent magnets fully independent of rare earths and magnet processing or products from China.
Key elements of the multi-pronged development include:
- Its U.S. subsidiary has secured a KRW 900 billion ($673 million) order from a North American global automaker to supply permanent magnets for six years.
- Its German subsidiary is set to supply permanent magnets worth KRW 260 billion ($195 million) to a European automaker over nine years.
- Partnered with a Korean magnet company for the production of permanent magnets using rare earths not from China to diversify the supply chain, supported by jointly building a major new magnet factory in the U.S.
- A global network of new production operations for traction motor cores to supply automakers, beginning in Mexico and Poland and spreading to other countries.
Its U.S. subsidiary recently secured the KRW 900 billion order in North America from an unnamed global automaker to supply permanent magnets from 2026 to 2031. The permanent magnets will be used for the traction motors of the client’s new medium and large-sized electric vehicle models, according to Posco CEO Lee Kye-In. In Europe, Posco’s German subsidiary has signed a contract to supply permanent magnets valued at approximately KRW 260 billion to a premium European automaker from 2025 to 2034.
The Europe deal, finalized in January, calls for supplying 1.03 million traction motor cores to Hyundai Motor Group and Kia for their first locally produced EVs in Europe. A long-term supply agreement extending from 2025 to 2034, it is designated for plants in Turkey and Slovakia. Plant construction by Posco in Poland will begin early this year. Through the electrification plant at Hyundai Mobis’ factory in Slovakia, 550,000 units of traction motor core will be supplied to Hyundai Motor Group and Kia’s Turkish plant, and another 480,000 units will be supplied to the Slovak plant. With this order, POSCO International, together with its subsidiary POSCO Mobility Solutions, has secured contracts to supply a total of 11.87 million units of traction motor core to Hyundai Motor Group and Kia.
The permanent magnets involved in the contracts will be sourced from the U.S., Australia, and Vietnam while avoiding the use of rare earths from China. They will be produced by Star Group Ind. Co., Ltd., the sole manufacturer of rare earth permanent magnets in Korea.
According to an article in the Korea Economic Times, the two parties have engaged in negotiations with the state governments of Texas, Tennessee and Arizona to decide the location of their joint permanent magnet manufacturing factory in the U.S. with an initial production capacity of 3,000 tons a year, which would be later expanded to 5,000 tons a year, enough to power 2.5 million electric vehicles. They are said to be investing up to 300 billion won ($147 million) to build the factory. They are expected to supply permanent magnets from the factory to the top three US automakers — General Motors, Ford Motor and Stellantis in addition to supplying plants in America of Hyundai and Kia.
The permanent magnet orders hold significant value for the company, explained the company. Not only are they viewed as a milestone in expanding its stable mobility business through large-scale orders, but also as a step towards establishing a supply chain for the permanent magnet market that excludes China, a market where Chinese rare earths market share is at least 90 percent.
“These orders mark a significant milestone as we enter the global market by collaborating with a domestic company in the rare earth permanent magnet market, which is largely monopolized by China,” remarked a POSCO official. “We are currently in discussions with several automakers and traction motor manufacturers for additional orders and are optimistic about future business expansion.”
Global production of traction motor cores a key element in the strategy
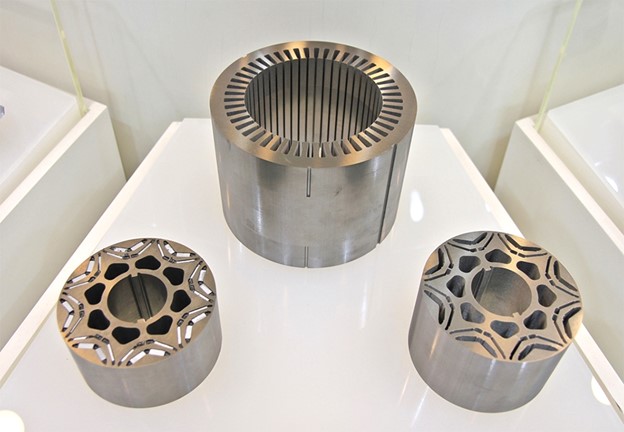
In addition to these permanent magnet orders, the company is intent on expanding its value chain to strengthen its position as a core part manufacturer for the drive control system of eco-friendly vehicles. A key element of the strategy is to package and supply all the parts required for the rotor and stator of the traction motor core―key components of the electric vehicle drive control system―to both domestic and international automakers. The rotor contains permanent magnets that generate the necessary magnetism for rotation in addition to the shaft that handles rotation. The stator is the component that surrounds the rotor from the outside.

Earlier, on March 6, Posco unveiled its plans to build a complete global production cluster for traction motor cores with new plants in Poland and Mexico. The system for annual production and sales of more than 7 million units will be completed by 2030, said Lee Kye-In in his inaugural speech as president, marking the global expansion of traction motor cores as his first move after taking office. At a board of directors meeting held on Feb. 23, the company approved the construction of a new plant in Poland and a second plant in Mexico, completing the blueprint for its Vision 2030 expansions.
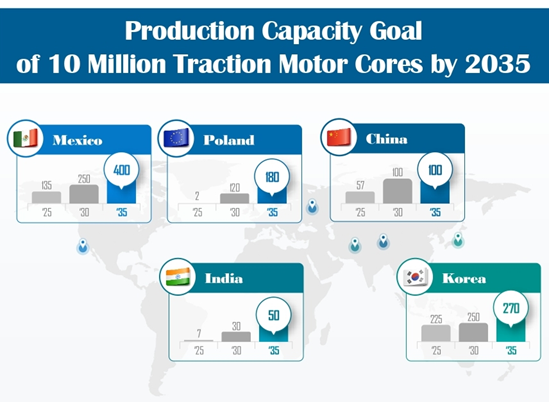
The plan calls for Posco to establish a global production cluster for traction motor cores in five countries, including Korea (Pohang and Cheonan), Mexico, Poland, China and India.

The Polish production plant, which will be the headquarters of POSCO INTERNATIONAL’s traction motor core business in Europe, will be located in Brzeg in southwestern Poland. It is located adjacent to the production bases of global automakers in Europe, namely in Germany, the Czech Republic, Slovakia, and Hungary, making it a prime spot for local procurement.
The new plant, sited on a 100,000 square meter plot, is due to start construction in June of this year, with completion expected by May 2025. The plant will expand its production scale according to the production plan to produce 1.2 million traction motor cores annually by 2030. Starting with the production of 1.03 million traction motor cores ordered by Hyundai in January, the company plans to stabilize the plant’s operations by pursuing orders from major European customers.
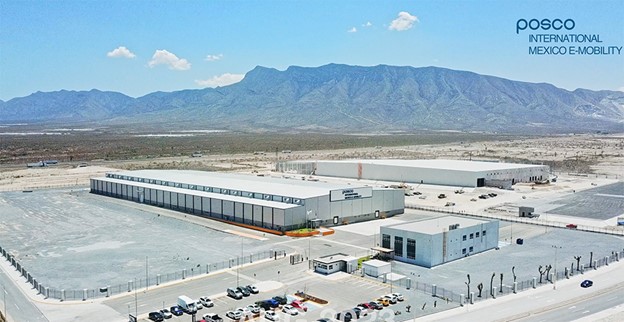
In addition to the construction of the Polish plant, the board also approved the construction of the second plant in Mexico. The construction of Plant 2 in Mexico is scheduled to begin in May this year and is expected to be completed by March next year. It will be built next to Plant 1, which was completed in Ramos Arizpe in October last year, and once completed, the combined production capacity of Plants 1 and 2 will amount to 2.5 million units annually by 2030.
Plant 2 in Mexico will serve as an essential production base to supply 2.72 million traction motor cores to Hyundai Motor Group Metaplant America (HMGMA), which was contracted in September last year, while responding to the needs of customers for local production in North America.
Overall, Posco aims to achieve a 10% global share of the traction core market by 2030. In addition, by establishing localized production in three continents where major automakers are located, namely Asia, North America, and Europe, the company plans to improve its logistics competitiveness and counter trade barriers, while also laying the foundation to evolve into a core part manufacturer for the drivetrain of future eco-friendly vehicles, providing delivery to customers in the manner and at the time they want.

“The company’s future vision is to become a platform company that creates synergies across different businesses and creates new businesses,” said Lee Kye-In. The company is consistently developing a global production network to mitigate trade barriers in the electric vehicle market and proactively meet the local procurement requirements of automakers.
The key to the successful expansion of its business, notes the company, lies in the synergy between the technology and infrastructure provided by its subsidiary, Posco Mobility Solution, in the mobility sector, and Posco’s high-quality hyper non-oriented electrical steel (Hyper NO), which is a key material used in motor cores. The steel significantly reduces energy loss compared to conventional electrical steel. Established in 2020 as an independent subsidiary, Posco Mobility Solution has become Korea’s top manufacturer of traction motor cores. The patented stacking method developed by its in-house mold research center is considered exceptional for maximizing the efficiency and performance of motors.