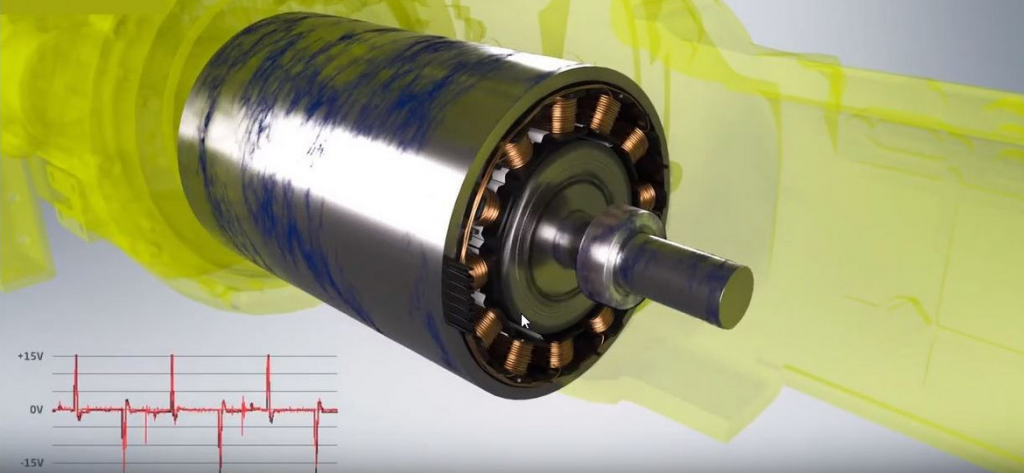
By Markus Weber, Global Business Development Manager for Traction Systems SBA Mobility, Schunk Carbon Technology GmbH
Electromobility is the future. Transport and environmental experts agree on this. But as battery electric vehicles increase in number, their manufacturers face an increasing number of challenges. One of these is capacitive interference currents in electric traction motors. These can cause damage to bearings and gears. Schunk’s innovative carbon grounding system is a reliable and cost-effective solution.
For decades, Schunk has been a reliable partner for the automotive industry in the development, production and application of carbon, ceramic and sintered metal solutions. The experts at Schunk unite innovation and technological expertise with a high level of service at more than 22 automotive locations, to ensure they are always close to the customer.
Manufacturers of electric and hybrid vehicles face different challenges to those of combustion engines. For example, power electronics produce – as a side effect of the used pulse width modulation (PWM) technique – high-frequency interference voltages to the rotor shafts of electric traction motors. This results in damage to the bearings, which could lead to drive failure. At the same time, there is also the risk of emitting high-frequency signals which could interfere with the sensitive sensors in the vehicle. This risk should not be underestimated – particularly when it comes to developments in autonomous driving.
Reliable protection of bearings in the electric drive
The innovative Schunk shaft grounding assembly discharges the capacitive interference currents directly via a grounding contact. This takes place by short-circuiting the drive shaft with the motor housing. The developed shaft grounding assembly thus offers effective protection against damage to the bearing whilst also minimizing the radio frequency interference (RFI) emitted by the shaft. Electromagnetic compatibility (EMC) is an important topic for electromobility and autonomous driving. Serious consequences are to be expected if technical devices interfere with one other via electrical or electromagnetic effects. To eliminate such shaft voltages, it is advisable to discharge the interference voltage from the shaft specifically on to the motor housing. Without such a countermeasure the electric discharge takes place over the bearings by electric sparks between the bearing’s outer and inner ring and the bearing balls destroying its trace path.
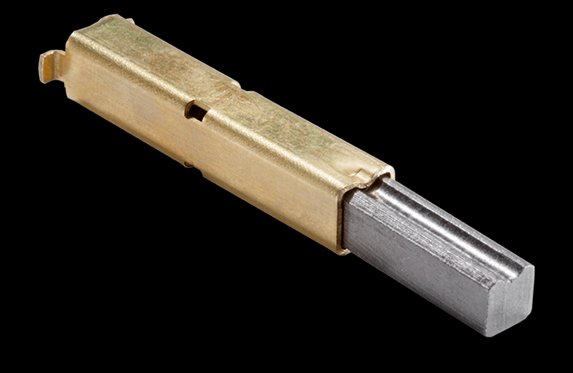
Expertise and experience meet innovation
Applying their decades of experience and unbridled innovation, Schunk experts have now developed a carbon grounding system that is applied to a metal spring. This comparatively cost-effective solution allows the reliable bleeding off of interference currents over the entire service life of the electric or hybrid vehicles. The discharge usually takes place close to the bearing, between the electric motor and flange-mounted transmission. Two solutions are available for this purpose: the radial shaft grounding and axial shaft grounding. Schunk is the sole supplier of carbon-based grounding contacts that are tailor-made – designed and developed in close cooperation with the customer. The grounding contacts can be used either in combination with Schunk slip ring systems (required for separately excited synchronous machines) or as a stand-alone solution.
Into the future with Schunk technology
In spite of its successful use in modern e-models, the development of grounding contacts for electromobility has not come to a standstill. The aim of the latest solutions is to extend the service life and to reproduce the same function in an oil surrounding. Schunk experts are working closely together with the automotive industry in this area. From tailor-made material development, component design and prototyping through to series production and logistics – customers benefit from the early involvement of experts and their extensive expertise in the electrical, mechanical and thermal application of graphite materials and composites.
For more information, see www.Schunk-CarbonTechnology.com.