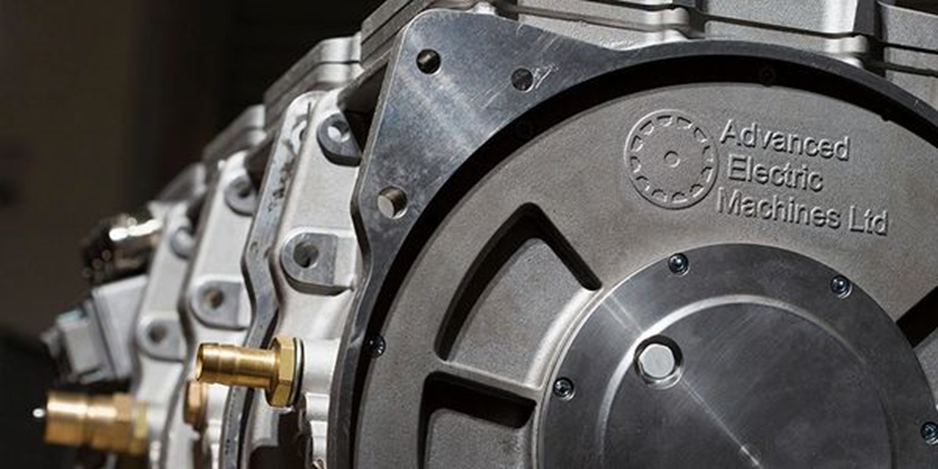
Having spun out of Newcastle University in the UK three years ago, Advanced Electric Machines is moving forward in its pursuit of bringing to market its innovative electric motor which by design sidesteps the use of rare-earth permanent magnets, along with other advanced products for sustainable and environmentally-friendly transportation.
In recent developments, the company has built up its coffers with £5 million in successful fund raising, moved into a new headquarters and production facility, and engaged in over £26 million of research and development projects. The latest fund raising closed at the end of 2019 for £1.9m.
“This latest investment raised almost 60% additional capital above the original target, it will allow AEM to invest in our design and manufacturing capability more quickly than we expected,” said James Widmer, CEO.
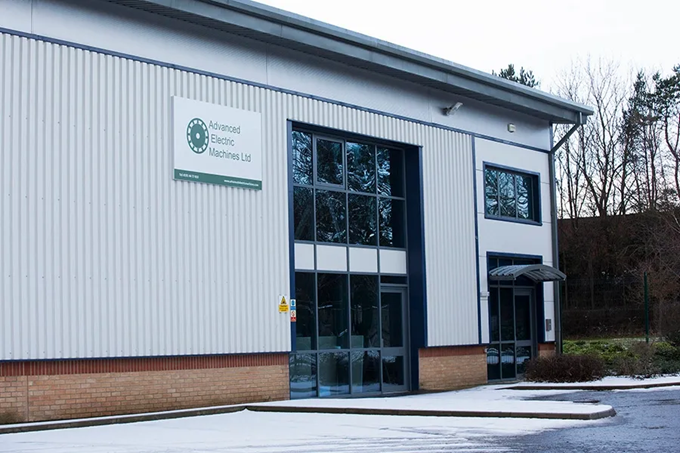
AEM now operates out of its new headquarters building, a 1,200 square meter facility located in Washington in northeastern England, about 10 miles south of its roots at Newcastle University, and employs 24 people. Initial plans call for a production line capable of manufacturing 12,000 motors per year. The company reports that it has received its first large commercial order and is now working on opportunities across four continents and six different sectors including automotive, aerospace, marine and energy.
Shown at top is the company’s HDSRM motor, a switched reluctance motor which relies on steel laminations and wound coils but not rare-earth magnets. It is designed as a low-cost traction motor to drive hybrid, range extended and electric commercial vehicles from trucks to buses and taxis.
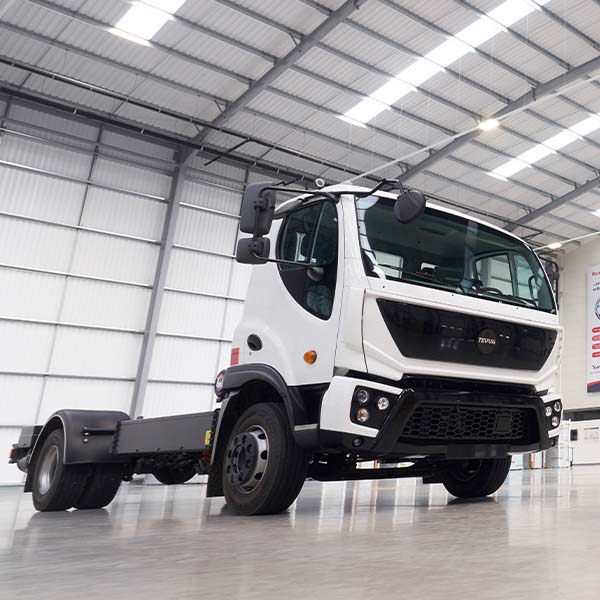
One project the company is engaged in is to provide motors, integrated with AEM’s gearbox, to serve as both traction motor and as a generator when coupled with the modular electrification system of Tevva Motors Ltd for medium duty commercial vehicles. Tevva supplies the system to fleet owners, making electric trucks that are effectively a direct swap from diesel to electric enabling the same route and payload.
AEM began operations in 2017 when it was established as a spin-out from the university and set about to commercialize a portfolio of patents for sustainable and environmentally friendly motor and drive technologies developed there. The company focuses on developing a new generation of recyclable, lightweight and energy-efficient motors that can not only be produced in high volumes and at low cost, but also eliminate the need for materials deemed problematic such as rare-earth permanent magnets.
Its founders, Dr Andy Stevens and Dr James Widmer, are both alumni of Newcastle. Widmer also serves as director of the Advanced Propulsion Centre UK’s Electric Machines Spoke which leads policy development for the country’s automotive industry electric machines development and manufacture.
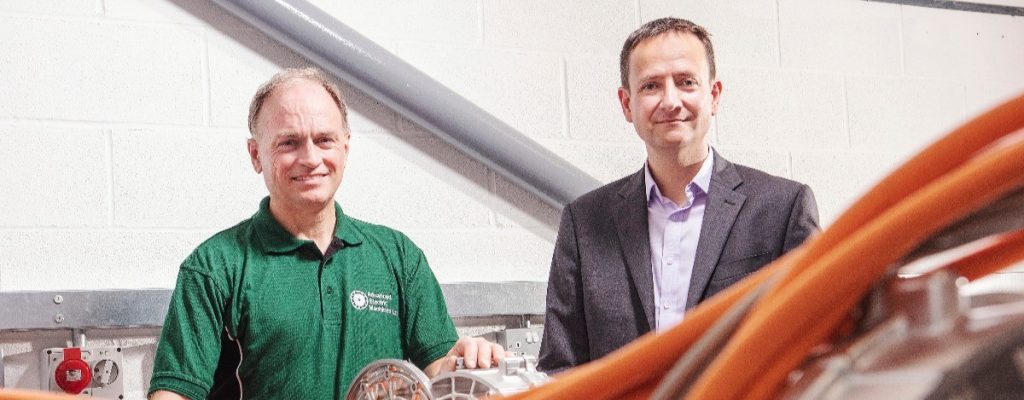
Widmer joined the University from industry in 2010 to complete his graduate studies, and subsequently rose to oversee the School of Engineering’s research group, the Centre for Advanced Electric Drives. By applying the latest academic research to industry, the center helped companies like Jaguar Land Rover to build its first electric vehicle and Airbus to achieve the world’s longest ever flight using an electric motor.
The university’s pioneering work in this field meant it was designated as the Electric Machines Spoke for the Advanced Propulsion Centre, the funding body for low-carbon vehicle research in the UK. Widmer was appointed as the director and tasked with leading policy development to future-proof car manufacturing in the UK, which was when he spotted a gap in the market for a more sustainable alternative to traditional electric motors.
Today AEM Group produces traction motors for electric trucks and is scaling up production to develop even more advanced technologies for clients such as Bentley and Airbus. The company still has strong ties with the university. Widmer continues to work with the university to establish supply chains around electric vehicle technology.
“With the drive and momentum towards more vehicles requiring electric motors, we have to make sure there are enough companies out there that can make parts, and that enough people are trained in these areas,” explains Widmer in a summary report by Newcastle. “That’s the great thing about working with the university – we get to anticipate future problems and work towards solving those issues now.”
AEM Group has been instrumental in securing £80 million worth of investment from the government’s Industrial Strategy Challenge Fund, known as ‘Driving the Electric Revolution’. Together, the company and the university are hoping to use the funding to make northeast England the UK’s leading region for electric drivetrain research and manufacturing.
“It’s fantastic to have spun out from the university because of the brilliant research that is still going on,” adds Widmer. “Looking to the future, we want to continue working in partnership with the university and also hope to recruit people who’ve been trained there.”
Now, two entities form the AEM Group. Alongside AEM is Advanced Electric Machines Research Ltd (AEMR) which was formed to design and develop electric motors and drive technologies for automotive and aerospace OEMs with a particular focus on the motor, power electronics and mechanical transmission elements of future powertrains. AEMR holds key patents in both manufacturing and design which will allow its products to achieve performance advantages at no extra cost, the company says.
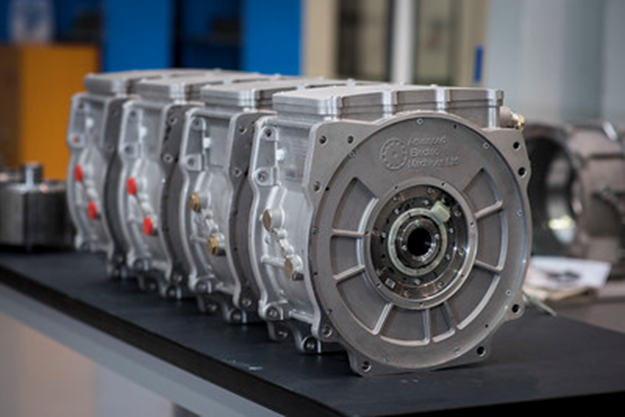
According to AEM, its HDSMR motor maximizes the benefits of switched reluctance motor technology with no rare-earth magnets, robustness and high efficiency while achieving the performance characteristics of a rare-earth magnet based machine such as high torque density, low noise and torque ripple. It uses standard commercially available power electronic inverters.
No rare-earth magnets means lower cost, improved sustainability and reduced supply risk compared to permanent magnet motors, plus improved safety and no risk of demagnetization at temperature, enabling a shared coolant loop with an internal combustion engine, the company says. It is design optimized to be more efficient than a permanent-magnet or induction motor at normal commercial vehicle operating points.
In general, a switched reluctance motor is designed with phase coils mounted around diametrically opposite stator poles. There are no windings or permanent magnets on the rotor. The rotor is made of laminated steel and its shape forms salient poles. The stator has concentrated coils wrapped around ferrite core material. Unlike common brushed DC motor types, power is delivered to windings in the stator rather than the rotor.
For more info see www.AdvancedElectricMachines.com and www.ncl.ac.uk.