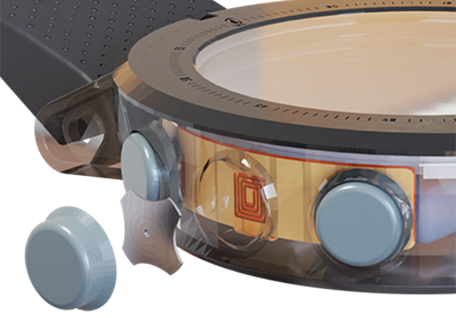
Need a user interface that is waterproof? Non-contact? Versatile? Design engineers of consumer devices, appliances, automotive and industrial products are increasingly discovering new ways to apply inductive sensing to their applications.
When it comes to inductive sensing and its capability to revolutionize user experiences and interfaces, few companies can match the experience of Azoteq of South Africa. Over more than 20 years, engineers at the fabless semiconductor company have developed an extensive portfolio of sensing and control devices. It has been at the forefront of pioneering single chip, multi-sensor solutions.
“Our journey began over two decades ago with the introduction of capacitive sensing technology,” recalls Jean Viljoen, vice president of marketing, who joined the company in 2000 as a DSP application engineer. He was one of the key architects who developed the company’s ProxSense product line in 2004 and has been involved with it ever since.
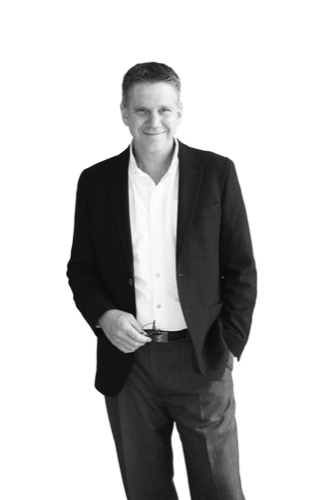
“Over the years, we have continually developed and enhanced numerous user interfaces, ranging from wear detection in fitness trackers to touch pads in premium headphones, all powered by capacitive touch sensing. Through our dedication to optimizing power consumption, resolution, and sensitivity, our focus has expanded to explore new avenues for improving user interfaces. This led to the development of the ProxFusion series, where additional sensors were integrated onto the touch sensing platforms.”
“Among these innovations, one technology stands out for its potential to revolutionize user experiences and interfaces across various industries: Inductive Sensing. It represents a significant leap forward in sensor technology. Its capabilities have the potential to transform user interfaces in ways previously unimagined.” Viljoen recently led a webinar on the subject, from which this article is drawn.
Background
Inductive sensing has a rich history of use in industrial applications, primarily in proximity sensing, position detection and object tracking. Traditionally, these applications relied on large, power-hungry analog sensors with dedicated power supplies. However, Azoted’s team of experts has revolutionized inductive sensing by miniaturizing it into fast, compact, short-range sensors with exceptional accuracy. These sensors operate on extremely low power consumption (think tens of microamps), enabling them to run for years on small batteries.
This breakthrough has opened doors to new industries and applications beyond industrial settings. The contactless nature of inductive sensing is now being harnessed in user interface applications and consumer electronic products, offering enhanced functionality, reliability, and efficiency.
Technology explained
Inductive sensing operates without the need for physical connections. It detects the presence or position of conductive objects or targets without requiring direct contact with these objects. This technology is based on the principle of electromagnetic induction, where an electromagnetic field is generated and changes in this field caused by nearby conductive objects are detected.
To simplify, imagine a coil of wire carrying an alternating electrical current. This current creates a magnetic field around the coil. When a conductive object, like a metal target, enters this magnetic field, it induces eddy currents within the object. These eddy currents generate their own magnetic field, which interacts with the original magnetic field from the coil.
Inductive sensing measures changes in the original magnetic field caused by the conductive object’s presence or movement. This allows it to determine various parameters such as proximity, position, and even material composition differences.
The key components of inductive sensing include:
- Coil or Antenna: This component generates the electromagnetic field. It can be a simple coil of wire or a specialized antenna.
- Sensor Circuitry: This circuitry processes signals from the coil or antenna, converting them into useful data like proximity or position information.
- Target Object: The conductive object being detected or measured.
Inductive sensing offers several advantages over traditional contact-based methods. Since It is non-contact, there’s no physical wear on the sensor or target object. It remains unaffected by environmental factors like dust or moisture, which can hinder contact-based sensing. Additionally, it provides highly accurate and reliable data compared to the binary output of traditional switches.
Interface challenges
User interfaces act as crucial connectors between humans and machines, significantly influencing our interactions with technology. However, these interfaces encounter distinct challenges that can impact user experience and product reliability.
- In the consumer electronics realm, the quest for sleek and intuitive interfaces has driven the widespread adoption of touchscreens and capacitive buttons. Despite their convenience and modernity, these interfaces are susceptible to issues like fingerprint smudges, accidental touches, and limited functionality in specific conditions such as wet environments or when users wear gloves.
- The automotive industry faces challenges with traditional interfaces like mechanical buttons and switches, which are prone to wear and tear due to frequent use. Harsh environmental conditions, including temperature fluctuations, dust, and moisture exposure, further challenge the durability of these interfaces.
- Industrial settings demand rugged and reliable user interfaces. Equipment in factories must endure harsh environments, including chemical exposure, vibrations, and extreme temperatures, posing challenges to the functionality and durability of traditional interfaces.
- In the domain of white and brown appliances, user interfaces must withstand spills, liquid, and dirt while offering a premium feel to users, a feat not easily achieved with traditional switches.
Applying inductive sensing to the challenges
- Elimination of Physical Contact: Inductive sensing eliminates the need for physical or electrical contact between sensor elements, unlike traditional mechanical switches or buttons with carbon pills or wipers. This absence of physical contact reduces wear and tear, extending product lifespans and enhancing reliability.
- Resistance to Environmental Factors: Inductive sensing is inherently resistant to environmental factors such as dust, moisture, and temperature variations. Since it operates without physical contact, there are no exposed elements susceptible to these factors, ensuring consistent performance even in harsh conditions.
- Design Flexibility: Inductive sensing offers unparalleled design flexibility, enabling sleek and intuitive interfaces. It can be hidden and sealed beneath cover materials, creating seamless, waterproof surfaces that are easy to clean. This flexibility enhances product design and user interaction, improving overall user experiences.
- Positional Sensing: Inductive sensing provides positional information by measuring the proximity of metallic targets to sensors. This additional information enables the implementation of multiple activation levels, wheels, knobs, sliders, all while maintaining electrical isolation and benefiting from the aforementioned advantages.
Applications across diverse industries
- Consumer Electronics: Inductive sensing can be applied to various consumer electronic devices such as headphones, light switches, and volume knobs. While touch sensing is excellent for sleek interfaces, there are situations where the feedback and precise control of physical movement are irreplaceable. For instance, in headphones, the outer dial can now be controlled without compromising the sealed chamber crucial for optimal acoustic performance. PC peripherals can benefit from inductive sensing in keyboard keys, enabling contactless multilevel sensing and spill resistance.
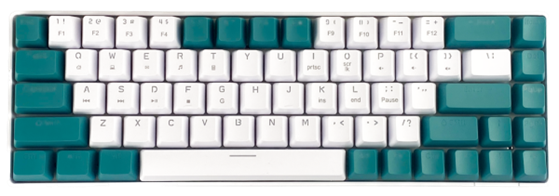
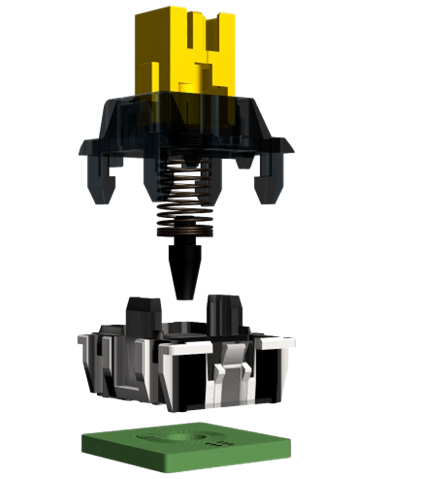
- Appliance Industries: In the realm of appliances, particularly kitchen equipment, waterproof user interfaces are essential. Traditional sealed membrane switches may not offer the most appealing look or reliability. Inductive sensing improves product interfaces by making them more reliable and waterproof. Designers can now incorporate knobs and sliders for functionalities like in rice cookers, addressing concerns such as boiling over while maintaining reliability.
- Automotive Industry: Inductive sensing finds applications in automotive key fobs, enabling completely sealed and waterproof designs. Buttons, knobs (rotary dials), and switches in vehicles benefit from this technology, ensuring durability and water resistance, even on motorbike clusters.
Benefits beyond connection reliability and water immunity
You might wonder if inductive sensing is suitable if you don’t require connection reliability or water immunity. However, this technology offers benefits beyond these aspects. For instance, it provides higher resolution and multiple trigger points per channel, enhancing functionality and precision in various applications.
Consider an electric piano or keyboard. With inductive sensing, these instruments can mimic the nuances of real pianos at a lower price point. You can determine the depth, force, and speed of each note, achieving a more authentic playing experience.
Imagine having more precise control over a cordless drill. Inductive sensing offers repeatable, precise steps to drive the motor, ensuring consistent performance that never wears out or changes behaviour in the presence of dust. This level of precision enhances functionality and reliability, making tasks like drilling more efficient and accurate.
Compared to carbon resistive knobs and physical switches
Inductive sensing offers several advantages over carbon resistive knobs and physical switches currently available in the market. Let’s highlight three key aspects:
- Contactless Nature and Longer Lifetimes: One of the most significant advantages of inductive sensing is its contactless operation. Unlike traditional carbon resistive knobs or physical switches that experience wear and tear over time, inductive sensing elements do not come into physical contact. This contactless nature ensures longer lifetimes for devices. Have you ever experienced a remote control button stop working or a game controller joystick drifting? Inductive sensing eliminates these issues by avoiding physical wear on sensing elements, leading to enhanced durability and reliability.
- Simplified Construction: Inductive sensing simplifies construction challenges by eliminating the need for complicated structural designs. Traditional switches and knobs often require a physical connection between moving parts and sensing elements, which can pose architectural challenges. For example, motorbike switches or washing machine knobs typically require holes in protective covers to allow activating parts to reach the electrical circuit inside. This arrangement can compromise waterproofing and increase the risk of damage from external elements. Inductive sensing eliminates these complexities by operating without direct contact, allowing for more robust and waterproof designs.
- Higher Resolution and Multi-Level Sensing: Inductive sensing solutions offer higher resolution and multi-level sensing capabilities. Unlike binary ON/OFF functions of traditional switches, inductive sensing provides digital information on button travel, key responses, and force sensors. This transformation enables devices to have multi-level sensing functions, enhancing user experiences and expanding the range of functionalities available. For instance, inductive sensing can turn a simple button press into a nuanced input, offering precise control and feedback in various applications.
Looking ahead
Several trends and innovations are poised to drive the adoption and advancement of inductive sensing technology, leading to exciting developments in the field.
- Reliability in Waterproof Sensing: A key trend propelling the adoption of inductive sensing is its reliability in waterproof applications. This extends from key fobs to door handles and instrumentation inside cabins. The ability of inductive sensing to operate without physical contact makes it an ideal choice for environments where water resistance and durability are paramount.
- Rise of loT and Smart Devices: Another significant trend is the proliferation of Internet of Things loT devices and smart technologies. Inductive sensing is positioned to play a vital role in enabling connectivity and interactivity within the loT ecosystem. Its seamless integration capabilities make it suitable for smart homes, industrial automation systems, and wearable gadgets, enhancing user experiences and device functionalities.
- Emerging Technologies and Innovations: Novel Sensor Materials and Designs: Ongoing research focuses on developing novel sensor materials with enhanced sensitivity and durability. Innovations in sensor designs aim to improve performance and functionality, paving the way for more robust and versatile inductive sensing solutions.
- Integration with Other Sensing Modalities: Another area of innovation involves integrating inductive sensing with other sensing modalities like capacitive sensing and optical sensing. This integration leads to the development of hybrid sensors with enhanced capabilities and versatility, enabling more sophisticated applications across industries.
- Advancements in Signal Processing and Machine Learning: Advancements in signal processing algorithms and machine learning techniques are revolutionizing inductive sensing systems. These intelligent and adaptive systems can learn and adapt to changing environments, enhancing accuracy, reliability, and energy efficiency while offering more personalized user experiences.
In summary, the future of inductive sensing looks promising, with these trends and innovations driving its evolution. We can anticipate the development of sophisticated and adaptable inductive sensing solutions that revolutionize user interfaces, enable seamless connectivity in loT ecosystems, and unlock new possibilities for interaction and innovation across various domains.
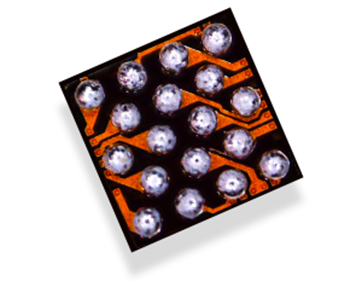
Located in Paarl, east of Cape Town, Azoteq provides an extensive line of sensing products, also lighting controllers and other products. Its IQS7222A ProxFusion IC, for example, enables applications that require multiple sensing capabilities from a single sensor IC. A capacitive, inductive, and Hall-effect sensor with additional temperature sensing for reference tracking, the 1.62 x 1.62 mm chip allows product designers to add a touch-and-swipe interface, wear detection, docking detection and the choice of an inductive waterproof button or inductive force-sensing features. For more info, see www.azoteq.com.