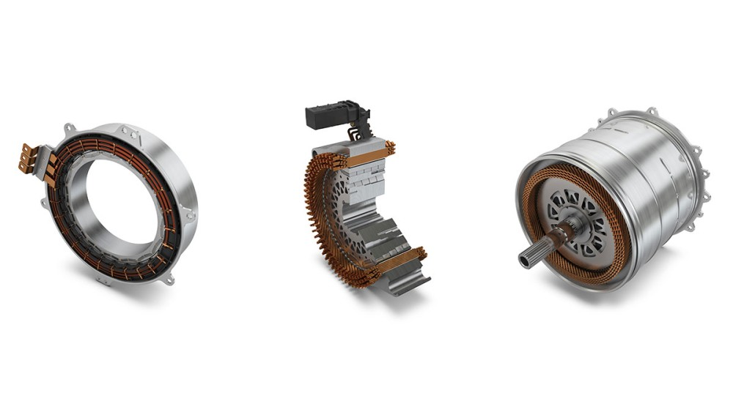
Automotive supplier Schaeffler is charging ahead to become a major global manufacturer of electric motors and complete e-drive systems for the automotive industry. Following on its acquisition of coil winding machinery manufacturer Elmotec Statomat at the end of 2018, now the company is entering the electric motor manufacturing business with a modular, highly integrated technology platform that is bound to make it an even more coveted customer for the magnet industry. Shown above are its new motors for hybrid modules, hybrid transmissions, and all-electric axle drives.
In separate moves that illustrate the company’s close ties to automobile manufacturers, Schaeffler also recently announced that it has renewed partnerships with Audi for Formula E race cars, and for the development of light-duty commercial EVs from Volkswagen. Both are key collaborations which serve as platforms for Schaeffler to develop future EV technology.
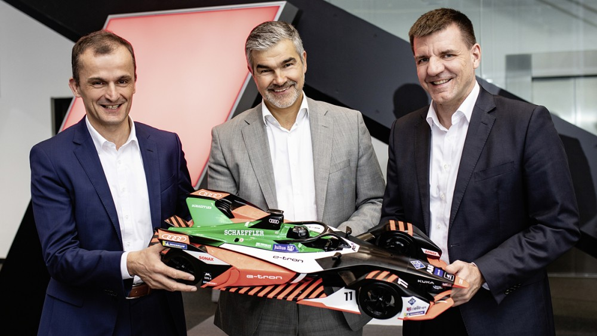
Schaeffler plans to begin volume production of its new motors and systems worldwide in 2021 serving a broad range of applications from 20 to over 300 kilowatts, providing motors for hybrid modules, hybrid transmissions and all-electric axle drives. Voltage ranges from 48 to 800 volts and performance classes from 15 to over 300 kW are envisioned.
Its worldwide network of manufacturing plants and special machinery and tool manufacturing facilities will be used to set up and operate the production lines, capable of providing everything in-house from winding machines to highly integrated electric drive systems. Schaeffler has developed the motors in-house and says they are ready for volume production as complete systems.
A 14 billion Euro per year company with 89,000 employees worldwide, Schaeffler is a leading supplier of components and systems for automotive and industrial markets. Headquartered in Herzogenaurach, Germany near Nuremberg, it has over 170 locations in 50 countries including manufacturing plants around the world.
Since its last remaining technology gap, stator manufacture, was closed by the acquisition of Elmotec Statomat at the end of 2018, Schaeffler is now turning to fully cover the industrialization of electric motors. Comprehensive expertise in mechanical components, manufacturing processes, and winding technologies as well as an in-depth understanding of all vehicle systems guarantee short development times and ensure smooth processes in the production of technologically sophisticated electric motors, it says.
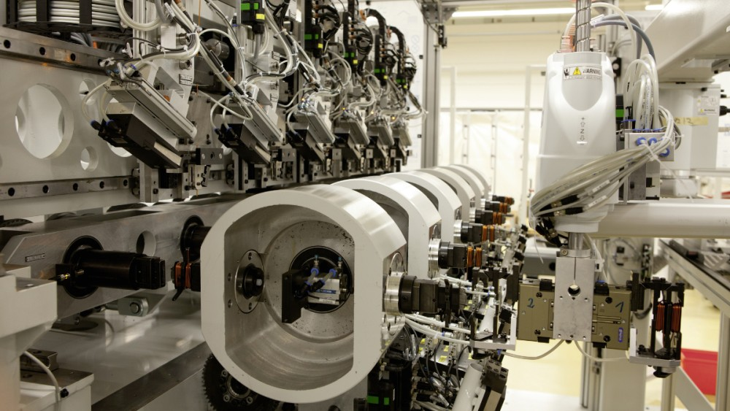
“Understanding and mastering transmissions, electric motors, and power electronics is an art in itself”, explains Dr. Jochen Schroeder, head of Schaeffler’s E-Mobility business division. “Making a functioning overall system and powertrain out of all these things is another. We are experts in both.” He provided the following details about their portfolio and technology.
Technology Explained
Electric motors for P2 hybrid modules are subject to special requirements, as their design means that they run at the same speed as the internal combustion engine. Minimal axial length and ample free space inside the rotor for the integration of clutch and release system ensure the necessary high packing density for this application. Single-tooth winding allows extremely small axial installation spaces. Both 48V and high-voltage motors with ratings of 15 to 120 kW are available.
If the hybrid module is designed as a dry system, the stator is actively cooled using a cooling jacket. In systems with a wet clutch, the oil that is available can also be used to lower the temperature of the electric motor, which leads to significantly better heat dissipation and thus higher continuous output levels. However, the best type of power loss is the one that never occurs in the first place, which is why the motors are optimized for high efficiency across a wide range of datamap areas.
Depending on the design envelope, the same can apply for electric motors in dedicated hybrid drives. These transmissions are usually designed in such a way that more axial installation space is provided for the electric motors, which rotate faster. Output levels of 80 to 140 kW are common. Depending on the transmission and powertrain operating mode, these motors work together with the internal combustion engine as motors or generators, and their efficiency characteristics are optimized in accordance with the utilization profile. As a result of the all-electric driving modes of plug-in hybrids, their acoustic behavior becomes a prominent factor. In many cases, the use of distributed windings is the right solution.
To this end, Schaeffler has defined a second standard winding solution, for which the production machinery is also developed in-house. The method in question is bar wave winding, which Elmotec Statomat is constantly refining at its location in Karben. To provide a specific application, a traction machine was developed that has an overall axial length of 137 mm and delivers 125 kW of power and 310 Nm of torque.
The portfolio is completed by a range of electric motors for driving electric axles. These cover both high-voltage 2 (400V) and high-voltage 3 (800V) ranges, and outputs of 100 kW to 300 kW are possible. If the system design permits, these motors are configured for high maximum speeds of up to 20,000 rpm, which allows the advantages of bar wave winding to be fully utilized. The high number of stator grooves means that the temperature is lowered effectively and leads to a rotating field with a low number of harmonics. This results in two advantages: A high power density and an excellent level of efficiency.
“By acquiring new expertise in the in-house development and production of electric motors, we are not only expanding our portfolio but also consistently pursuing our electric mobility strategy. Our comprehensive systems expertise and the solutions that we expertly derive from it mean that our customers have a recognized and trusted system and component manufacturer on hand to deliver the ideal products based on their requirements and mobility needs”, explained Matthias Zink, CEO Automotive OEM at Schaeffler.
Collaborations for Technology Development
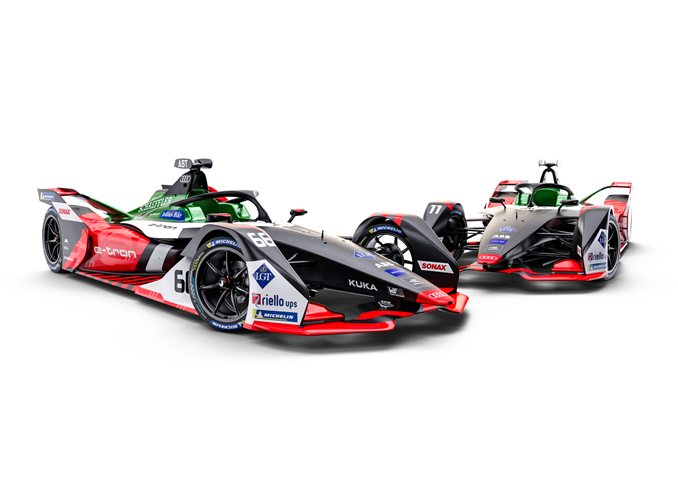
Audi and Schaeffler have extended their development partnership in Formula E racing that began five years ago. “Schaeffler,
Audi, and Formula E are a combination that was perfect from the very
start”, explains Zink. “As a company, our intention is to use our drive
train and chassis technologies to innovatively shape sustainable
mobility. Formula E is an ideal platform on which to present these ideas
for future electric mobiliy and measure our performance in a competition of the highest sporting caliber.”
For Schaeffler, the electric racing series is an ideal test laboratory for developing mobility solutions for tomorrow. Typically, the technology winners in that arena are positioned to be among the leaders in the volume production race.
“Formula E gives us a wealth of expertise, which we then transfer from the racetrack to our development departments”, explains Schroeder. “The relevance of this expertise in the fields of comprehensive drive systems, electric motors, power electronics, and transmissions is already demonstrated by the Schaeffler electric axle drives that we have been producing for the Audi e-tron since 2018, and this expertise is also being integrated into electric drive systems and components for the future that are currently in volume production development at Schaeffler.”
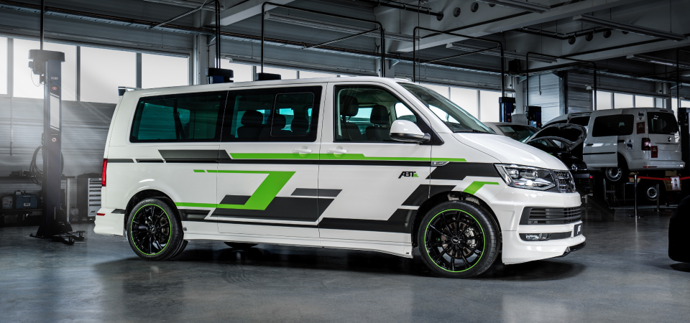
In December, Schaeffler announced a deal with ABT e-Line GmbH to establish a strategic collaboration for the electrification of light commercial vehicles weighing up to 3.5 tons. ABT e-Line is a 100-percent subsidiary of ABT Holding that, as a premium partner to Volkswagen Commercial Vehicles, has been commissioned to fully electrify light commercial vehicles. Schaeffler has been doing pioneering work in Formula E in partnership with the ABT Group since 2014. The objective of the new collaboration is to develop more advanced electric powertrains and to integrate and incorporate them into light commercial and special vehicles.