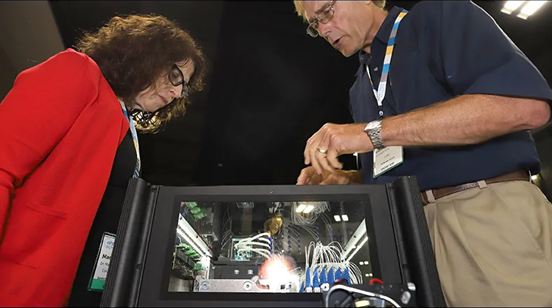
Magnetics technology plays a key role in much of today’s energy research – looking for breakthroughs in electric propulsion for aviation, high-temperature superconductors, fusion energy, machine modeling for power magnetics, new embedded cooling and winding topologies for improving permanent-magnet motors, even magnetic resonance imaging of crop roots. Visitors to the U.S. Department of Energy’s ARPA-E Energy Innovation Summit & Technology Showcase can explore a fascinating array of these and meet the scientists behind them, as well as many other aspects of energy R&D. It will be held in Denver in May. This article highlights some of the magnetic-related projects.
Texas A&M – MRI Rhizotron for Seeing Crop Roots in the Field
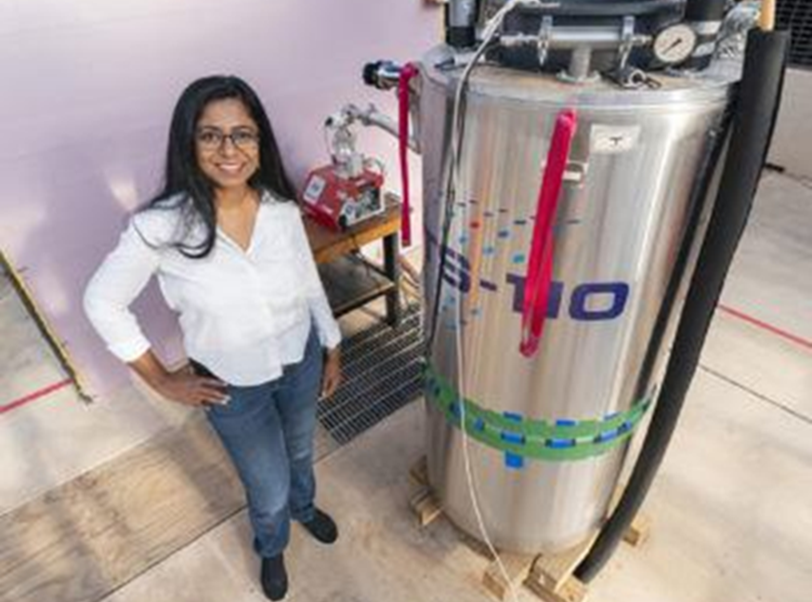
Texas A&M AgriLife Research is developing low field magnetic resonance imaging instrumentation that can image intact soil-root systems with an aim toward determining ideal plant characteristics. Operating much like a MRI used in a medical setting, the system can function in the field without damaging plants, unlike traditional methods such as trenching, soil coring, and root excavation. The team will test two different approaches: an in-ground system shaped like a cylinder that can be inserted into the soil to surround the roots; and a coil device that can be deployed on the soil surface around the plant stem.
“We are applying this technology to see if we can sense roots growing in agricultural soils and characterize them,” explains Nithya Rajan, AgriLife Research crop physiologist and agroecologist in the College of Agriculture & Life Sciences Department of Soil & Crop Sciences, who is leading the multidisciplinary project team. “To date, imaging roots in soil has been challenging because the soil is complex, with solids, moisture and roots. We just want to image the roots.”
GE Global Research – Electric Powertrain for Narrow-body Commercial Aircraft (eFLITES). GE plans to develop a 2 MW fully integrated all-electric aircraft powertrain and demonstrate a 350-kW lab-scale prototype to enable zero carbon emission narrow-body commercial aircraft with all-electric propulsion. Key innovations include a high-voltage, direct-drive, synchronous permanent-magnet motor with transformational embedded cooling of the windings using supercritical carbon dioxide and high-temperature, high-voltage electrical insulation; a modular inverter fully integrated into the motor to reduce component count with high-temperature, low-loss silicon-carbide inverter modules; and an ultracompact thermal management system that services the motor and inverter.
Raytheon Technologies – Ultra-Light Motor & Converter with Advanced Cooling for Aviation. Targeting the market for small regional aircraft, Raytheon Technologies Research Center is developing ULTRA-COMPACT to improve the electric-to-shaft power electric drive train and demonstrate feasibility of a turbo-electric distributed propulsion-based electrified aircraft propulsion system. The system leverages a novel high-speed permanent magnet machine, a series-parallel, multi-level silicon-carbide based motor drive topology, a high-power density gearbox using lightweight composite, and (4) an integrated and actively controlled thermal management system that provides coolant directly to the motor, gearbox and power converter.
Imagen Energy – SiC Inverter for High-Speed Permanent Magnet Synchronous Machines
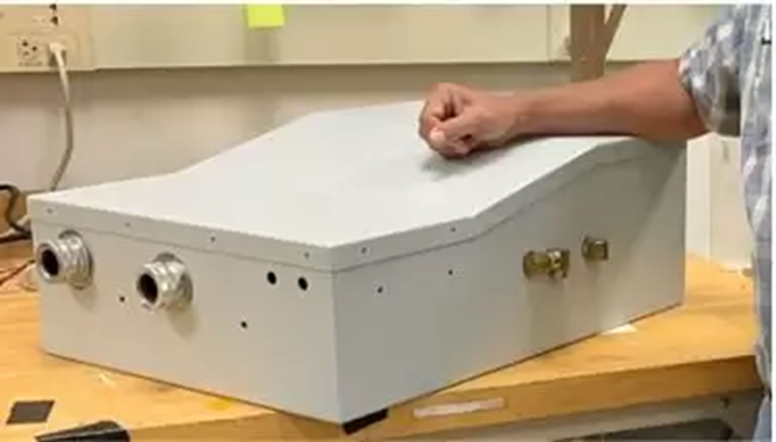
Imagen Energy is developing a silicon carbide (SiC)-based compact motor drive system to efficiently control high-power (greater than 500 kW) permanent magnet electric motors operating at extremely high speed (greater than 20,000 rpm). The effort addresses a major roadblock in operating electric motors at high speed, namely overcoming large back electromotive forces (BEMF). Their solution hopes to maximize the capabilities of the SiC technology and associated digital control platform, thereby bringing the overall drive system performance parameters to levels unachievable by current Si-based power conversion systems. If successful, the project team will demonstrate a motor drive capable of handling large BEMF and increase motor system efficiency over a broad range of operating speeds, a useful combination for high-speed applications in the oil and gas industry, high-speed/high-power compressors, grid-connected energy storage and renewable energy generation. Shown above is the company’s IM-1500 high-speed, high-power electric drive.
Advanced Electric Propulsion System by Honeywell Aerospace & University of Maryland. Honeywell Aerospace and the University of Maryland are working on a novel high-voltage 500 kW advanced electric propulsion system (AEPS) with a high efficiency and a high-power density. Among the innovations are use of high-performance windings to increase the copper fill factor for increased machine efficiency as well as thermal and electric conductivity, seeking to enable overall machine weight reduction without compromising efficiency. The system will provide direct drive to the propulsive device without using a torque amplifier for low weight, cost, and volume, and high reliability. The major components, the electric rotating machine (motor) and the motor drive (power and control electronics), will be heavily integrated for better performance, sharing a common chassis and cooling system.
HTS axisymmetric magnetic mirror on a faster path to lower cost fusion energy.
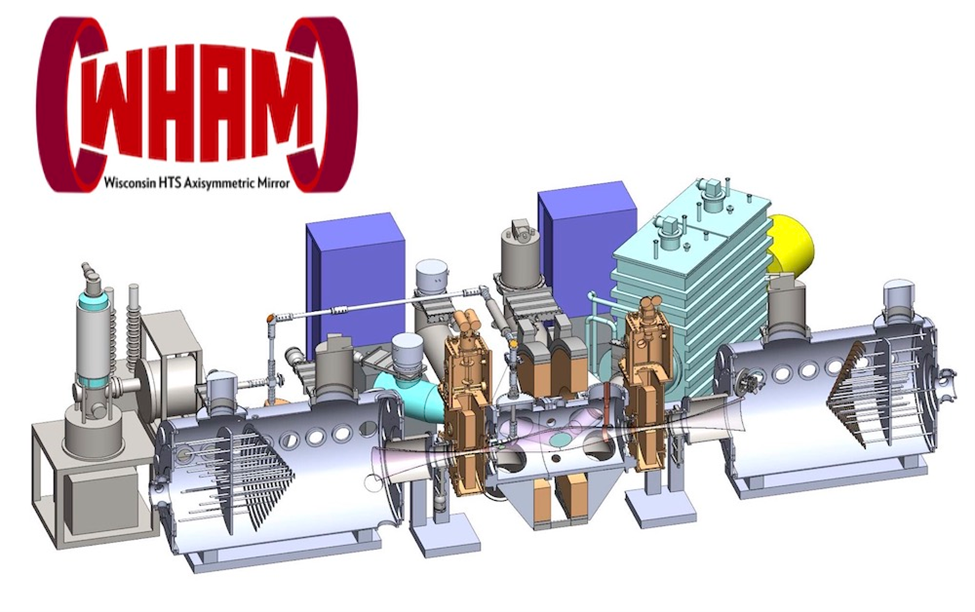
The Wisconsin High-field Axisymmetric Mirror (WHAM) project at the University of Wisconsin-Madison is leveraging advances in the stability and confinement of the mirror fusion concept, innovative plasma heating, and high-field superconducting magnets to demonstrate a potentially transformative development path toward a low-cost linear fusion device. Two mirror coils will be constructed using high temperature superconducting material. The plan is to demonstrate electron temperatures exceeding 1 keV and an advanced fusion triple product in the end cell.
MLSPICE: Machine Learning based SPICE Modeling Platform for Power Magnetics
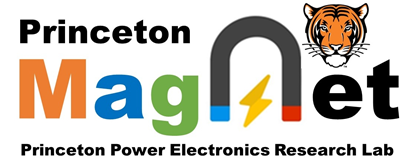
The Princeton University team is using machine learning-enabled methods to transform the modeling and design methods of power magnetics and catalyze disruptive improvements to power electronics design tools. They seek to develop a highly automated, open-source, machine learning-based magnetics design platform to greatly accelerate the design process, cut the error rate in half, and provide new insights to magnetic material and geometry design. With its integrated circuit emphasis-based, or SPICE-based modeling platform, the program uses a highly automated data acquisition testbed capable of measuring a large number of magnetic cores with a wide range of electrical circuit excitations, a machine-learning trained modeling method for modeling the core loss and saturation effects of magnetic materials, and a computer-aided-design tool which can synthesize the SPICE netlist for planar magnetics.
Stellarator Simplification Using Permanent Magnets to Revolutionize Tokamaks
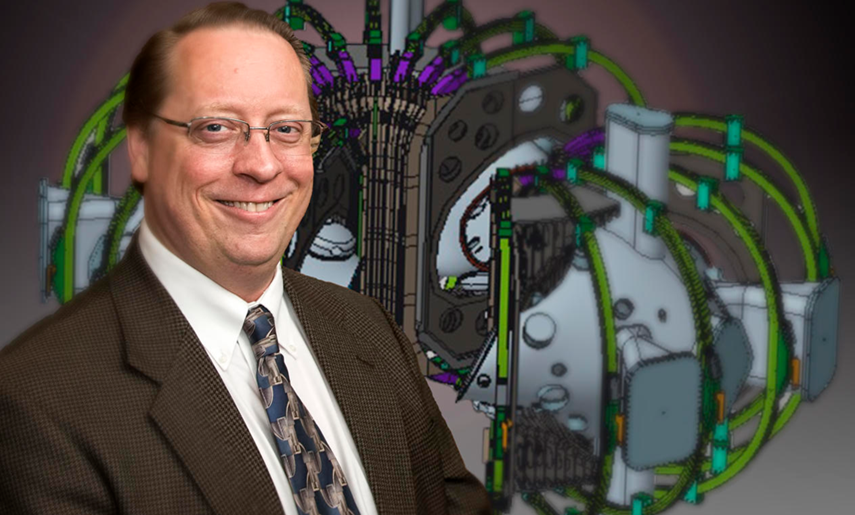
Princeton Plasma Physics Laboratory will design and build a prototype structure with an array of rare-earth permanent magnets to generate the precise shaping fields of an optimized, quasi-axisymmetric stellarator design. The stellarator is an attractive fusion-energy concept because it has minimal recycling power and auxiliary systems, and no-time dependent electro-magnet systems. Two challenges have delayed its progress, however: obtaining adequate confinement in three-dimensional fields and engineering the magnetic configuration with sufficient precision at low cost.
Breakthroughs in calculating and optimizing confinement properties of 3D magnetic systems have addressed the first challenge. A recent concept proposes permanent magnets and simple planar coils for making the complex fields required by stellarators. Use of permanent magnets along with planar toroidal field coils could dramatically simplify stellarator construction, assembly, and maintenance, and place the stellarator on a compelling path toward lower-cost fusion energy. The tokamak is the most scientifically mature fusion energy concept, which confines hot plasma in the shape of a torus (similar to a donut), controlled in part by a central solenoid electromagnet.
Plasma-Jet Driven Magneto-Inertial Fusion at Los Alamos. Los Alamos National Laboratory is leading a team that is testing an innovative approach to controlled fusion energy production: plasma-jet driven magneto-inertial fusion (PJMIF). PJMIF uses a spherical array of plasma guns to produce an imploding supersonic plasma shell, or “liner,” which inertially compresses and heats a pre-injected magnetized plasma “target” in a bid to access the conditions for thermonuclear fusion. LANL will develop a magnetized target plasma for the approach at a smaller scale than would be needed for a reactor.
Flux-Switching Machine Based All-Electric Power Train for Commercial Aircraft. Power density and efficiency are crucial to electric propulsion for future aviation systems. The University of California, Santa Cruz proposes to build a novel all-electric power train encompassing several unique technologies. The machinery relies on a flux-switching motor with high temperature superconducting field coils, which is smaller and lighter than conventional designs and has an immense advantage in terms of thermal management. The electronics are based on state-of-the-art silicon carbide-based multilevel inverter technology, which can easily interface to a medium-voltage power supply and lower electromagnetic noise and insulation stress on the motor. An innovative cryogenic system using solid or slushed coolant will cool stationary high-temperature superconductor field coils at 60K.
Georgia Tech – High Power Density Motor for Electric Transportation. Georgia Tech Research Corporation is studying a new approach to internally cool permanent magnet motors. The technology could dramatically improve electric motors’ power density and reduce system size and weight. The researchers will integrate motor and drive electronics into a unique system packaging incorporating an embedded advanced thermal management system. They will also develop wide bandgap power electronics packaging to enable high power density operations at higher temperature. The new design could substantially increase the power and torque density above the state of the art and enable more energy-efficient electric trucks, buses and, potentially, aircraft.
Advanced Magnet Lab – Dual Rotor Permanent Magnet Motor for Aircraft Propulsion. AML seeks to develop high-power density permanent magnet motors that, when coupled to an integrated silicon carbide drive, would enable an overall specific power beyond 12 kW/kg. The concept relies on tight integration of a high-power density dual-rotor permanent magnet rotor based on “continuous flux directed” magnets which it is developing. The motor is based on a dual-rotor configuration using permanent magnets forming Halbach arrays of permanent magnets which create a stronger field on one side and reduce the field on the other side to near zero, allowing for high magnetic loading without the need for iron.
Marquette University – High-Power Density Motor Equipped with Additively Manufactured Windings for Electric Aviation. Marquette University and its partners are developing an electric propulsion system that consists of a high-power density motor using additively manufactured winding and a heat pipe scheme for thermal management scheme, a modular power electronics topology, and tight system integration with shared thermal management between the motor and power electronics. The proposed technology is intended to be scalable in terms of power rating, speed, and system voltage, able to serve a wide range of hybrid/electric propulsion applications.
Lower-Cost Advanced HTS Conductors Customized for Fusion. Experienced in developing thin film superconductor tapes with record-high performance in high magnetic fields, researchers at the University of Houston are working on innovations which they say could reduce the cost of HTS conductors by a factor of 30. The objective is to produce rare earth barium copper oxide (REBCO) tapes to enable >20-T (Tesla) magnets in compact, high-field magnetic-fusion devices. Commercial REBCO tapes are expensive at $300/kA-m (kiloampere-meter) based on the operating condition of HTS magnets for compact fusion energy systems. The tape cost must be reduced to approximately $10/kA-m for HTS-based fusion systems to be commercially cost-competitive. Almost all commercial REBCO tapes use a generic high-temperature-resistant alloy, limiting their yield strength to ~700 MPa (101,526 psi), a constraining factor for ultra-high-field fusion devices in which the mechanical integrity of the superconducting magnet is critically essential. The University of Houston aims to develop HTS conductors with an increased critical current at >20 T and lower raw materials cost for commercial fusion systems. The team will use an advanced metal-organic chemical vapor deposition process to reduce costs and use high-strength alloys to increase the yield strength.
ARPA-E is the DOE’s Advanced Research Projects Agency- Energy. For more info, see www.arpae-summit.com.