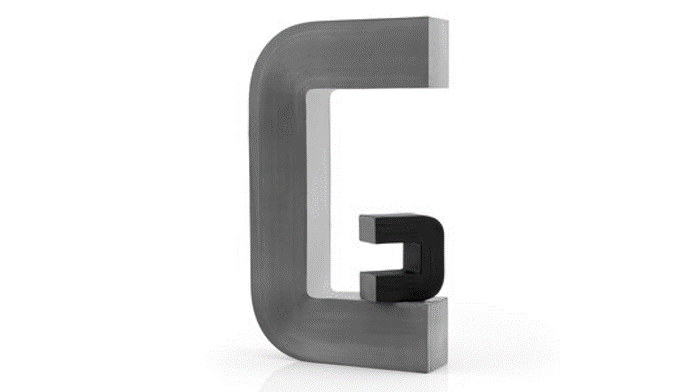
Vacuumschmelze reports that it has developed a new process for manufacturing nanocrystalline cut cores with exceptionally low core losses and high dynamic range. The company says it has considered and optimized its entire process chain for manufacturing the cores.
Usually, core losses increase significantly after cutting. Each step of the process has been reviewed to minimize this disadvantage, according to Frank Schnelle, product manager for energy conversion and automation.
A new winding technology was introduced to achieve filling factors of up to 80%. After heat treatment and impregnation, the very brittle, nanocrystalline core is cut in an optimal separation process that combines the superior quality of the cut cores with efficient process times. The subsequent final machining of the cut surfaces contributes to a further significant reduction in losses at high switching frequencies.
“The higher filling factor enables more compact designs that reduce the footprint and volume of the end application at continuous operating temperatures of more than 130 degrees C,” says Schnelle. “The most important advantage, however, is clearly the significant reduction in losses, which are only slightly higher than the losses of unseparated cores of comparable size.”
Enabling compact designs with low-volume production runs, the cores are particularly suitable for future-oriented applications in medium frequency transformers for the railway market, smart grids or fast-charge columns for electric vehicles.
For more info see www.vacuumschmelze.com.