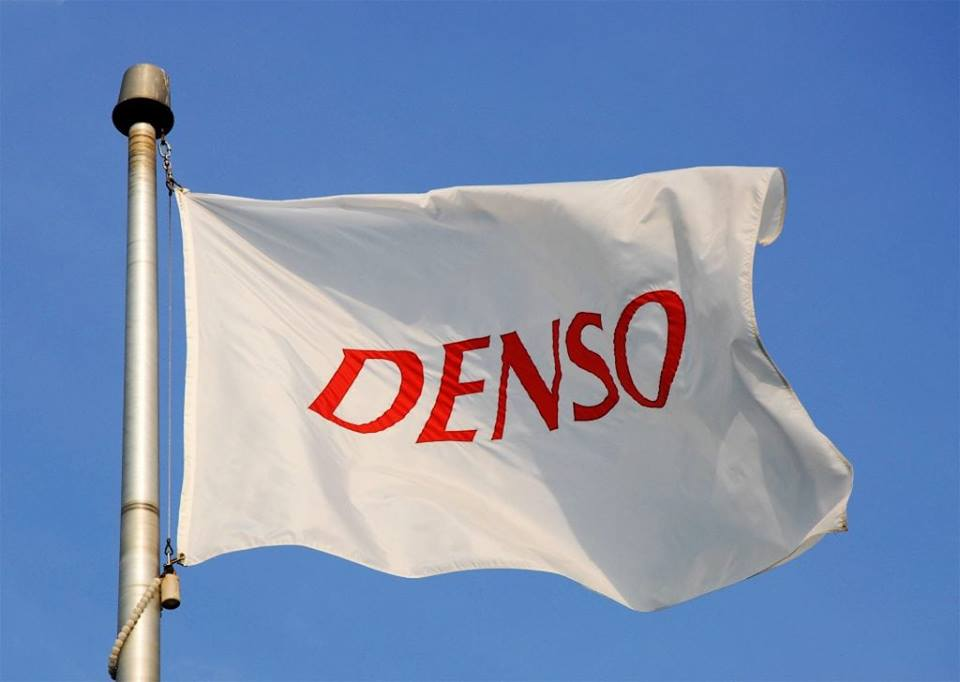
Denso, the world’s second largest mobility supplier and a major developer of advanced permanent magnet motor technology, has fully integrated its consolidated subsidiary ASMO companies in the U.S. into its North American operations. By combining ASMO’s small-motor strengths with Denso’s expertise in large, high-power motors, the company aims to accelerate its development of motor innovations for North American customers.
The company formerly known as ASMO North Carolina, Inc., will become a more integral part of Denso’s North America Motors Business group. DMNC’s main site is in Statesville, NC, with additional locations in Greenville, NC; Battle Creek, MI; and Ennis, TX. The change is part of Denso’s long-term plan to operate more efficiently while accelerating research and development.
“Automakers around the world are focused on electrification and automated driving. The products and technologies required to support that are sophisticated and require constant innovation and enhancements,” said Kenichiro Ito, executive officer for Denso and chief executive officer of the company’s North American headquarters. “This business integration will allow us to combine the strengths of both companies.” New electrified automotive systems require high-precision and high-value-added motors, he noted.
Masanori Iyama will serve as president of DMNC, transitioning from his previous role as head of Denso’s Motor Planning Division. DMNC produces blower motors, power seat motors, windshield wiper systems, power window motors, electric power steering motors and pinch sensor assemblies. It employs roughly 1,500 people.
Part of the company’s long-term plan, announced in 2017, was to make one person the lead in R&D in North America and Europe to promote collaboration in advanced technology. Another was to set up satellite R&D facilities globally to execute advanced R&D more speedily.
With manufacturing at its core and a robust R&D commitment, Denso is a $48 billion enterprise headquartered in Kariya, Japan with 221 facilities in 35 countries that produce thermal, powertrain, mobility, electrification, & electronic systems. The company employs 170,000 people and in its most recent fiscal year spent 9.3% of revenues on R&D. Its North American operations include 27,000 engineers, researchers and skilled workers across 31 sites in the U.S, Canada and Mexico.
One of its core technologies is the design and manufacture of motor generators which play a key role in improving the dynamic performance of electric vehicles and fuel efficiency of hybrid vehicles. Denso developed its motor generator using proprietary winding technology and rectangular magnet wire that is enhanced by its flagship SC (segment conductor) alternators. The developed coil end shape, winding structure, and manufacturing method have contributed to size and weight reduction, easy installation, drive-time power reduction and increased fuel efficiency.
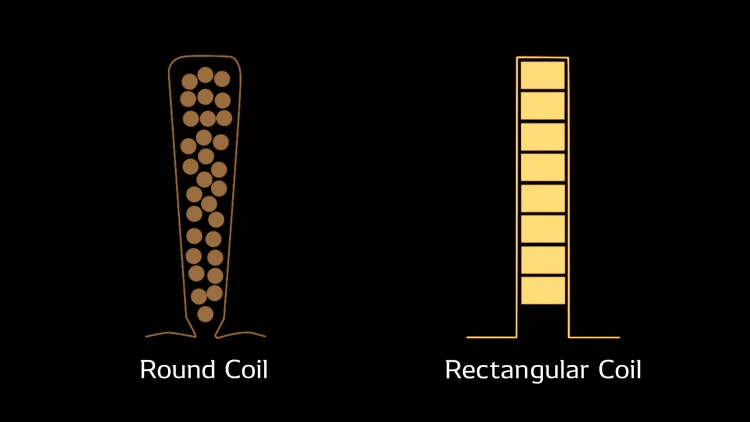
The coil space factor in the iron core has been improved by more than 10% by using wires with a rectangular instead of circular cross section. Also, the overlap at the coil end has been reduced to decrease the electrical resistance. This helps decrease the heat generated when large currents flow, achieving driving efficiency and power generation with less environmental impact.
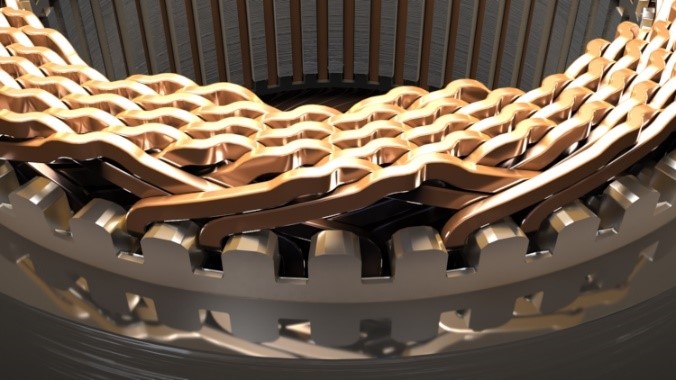
By using a distributed winding design in which coils are wound in the same width as the permanent magnets in the rotor, Denso takes full advantage of the magnets’ magnetic flux to generate electricity. To reduce the coil overlap, the company developed a proprietary manufacturing technology to align and assemble each u-shaped coil element, enabling mass production with high quality.
For more info, see www.denso.com.