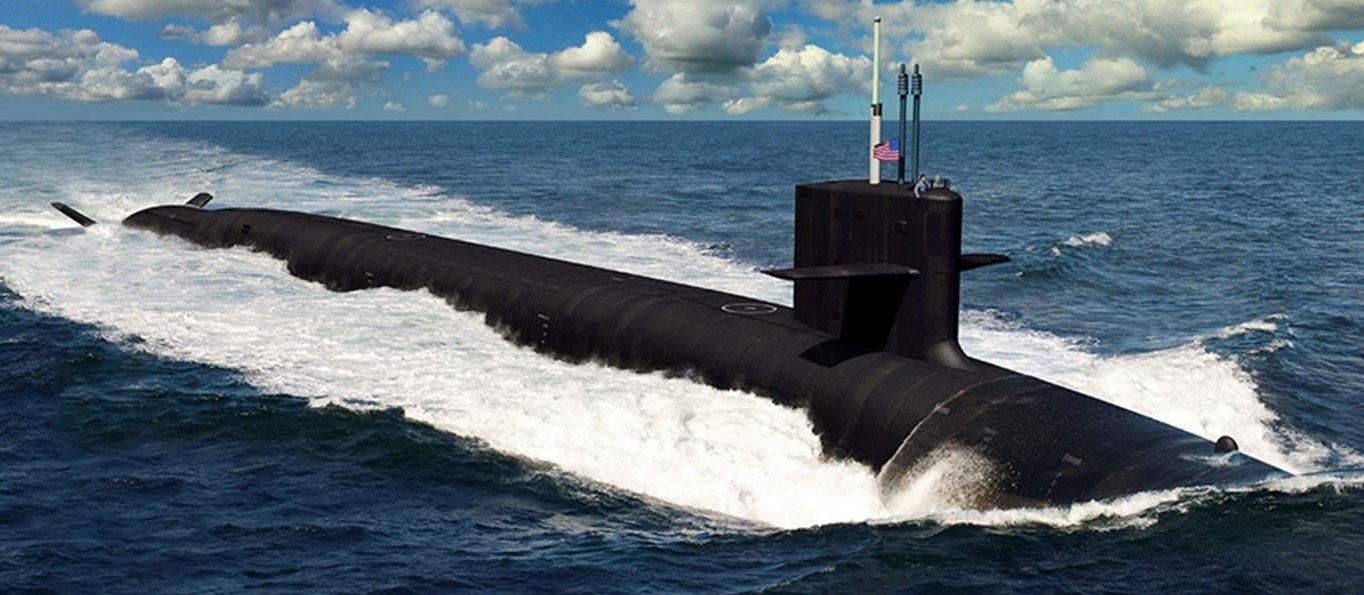
As navies aggressively electrify their fleets, defense contractor Leonardo DRS is supplying a growing roster of permanent-magnet systems for both hybrid-electric and full-electric propulsion. In recent programs, the systems are coming aboard both new underwater and surface vessels of the U.S. Navy and the U.S. Coast Guard.
For the U.S. Navy’s new Columbia class submarines, it has successfully completed factory acceptance testing and shipment of the first production unit of the main propulsion motor. It was shipped to General Dynamics Electric Boat for integration into the lead ship of the class. DRS was chosen by Electric Boat and the U.S. Navy to design and manufacture the major electric drive propulsion system components including the main propulsion electric motor. In addition to the main propulsion motor, other lead ship components are being manufactured and are also preparing to ship to Electric Boat.
The Columbia class program goal is to design and build a class of 12 new ballistic missile submarines to replace the U.S. Navy’s current force of Ohio class submarines. The Navy has identified the Columbia class program as its top priority program. The Columbia class submarines will be larger than the current class in terms of submerged displacement and will become the largest submarine ever built by the United States.
The DRS Naval Power Systems business was awarded contracts for the electric propulsion system components which included design, test, qualification, and production of the full-scale components for both a land-based test facility and first two ships of the class. Over the past several years, the Navy has completed successful land-based tests of DRS’ electric propulsion components. With significant testing completed, the program is transitioning to production with DRS presently manufacturing the components for the first two ships of the Columbia Class.
“We are proud to play a key role in developing and providing this capability for the U.S. Navy on this critical national defense asset,” said Jon Miller, senior vice president and general manager of the DRS Naval Power business. “Our long history of providing innovative technology to the U.S. Navy and continuing this work for Electric Boat ensures our sailors will be defending this country with the most advanced submarine in the world,” Miller said. Several businesses in the DRS Naval Power business contributed to this effort including. its facilities in Fitchburg, Massachusetts Milwaukee, Wisconsin and Danbury, Connecticut.
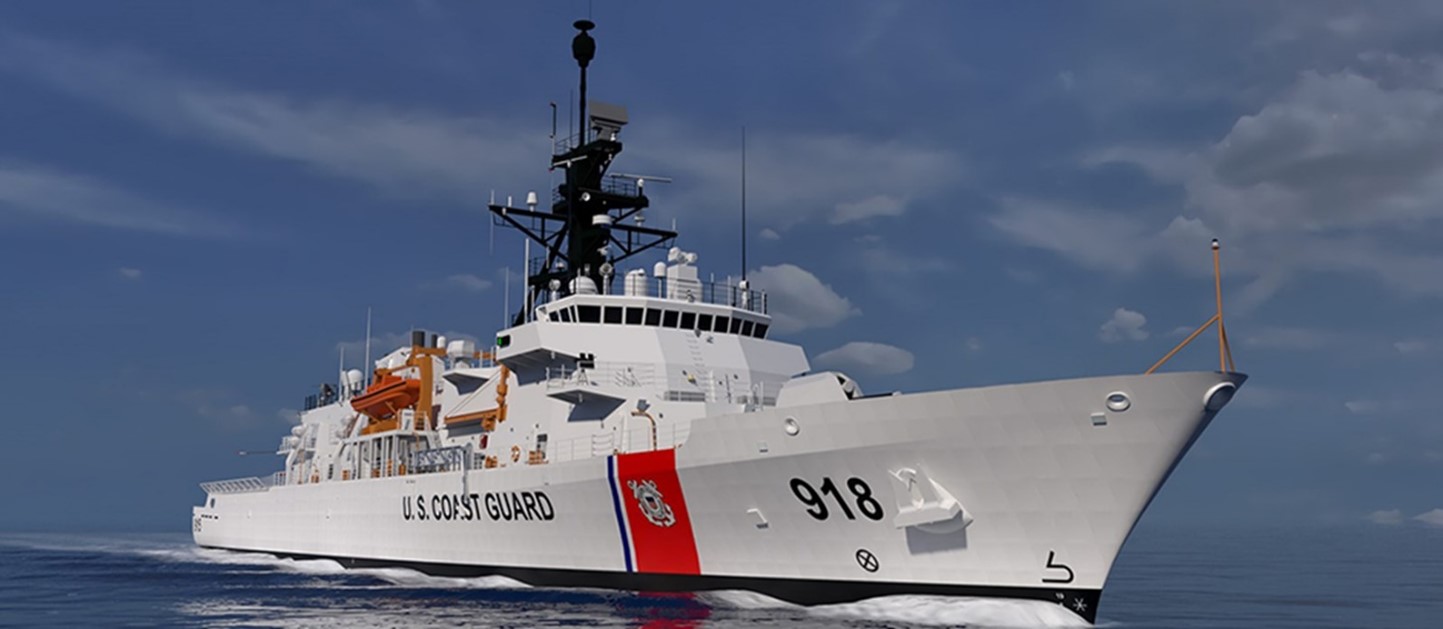
For the Coast Guard, DRS is providing an advanced hybrid electric drive system to provide auxiliary propulsion for the fourth shipset in a new fleet of Offshore Patrol Cutters. The platform is the first combined diesel electric or diesel propulsion system application for the Coast Guard. Eastern Shipbuilding Group is the prime contractor and builder of the next-generation offshore patrol cutters.
DRS will provide its high-performance, permanent magnet motor-based Auxiliary Propulsion System. The integrated hybrid electric drive system has been optimized to meet the Coast Guard’s operational tempo and provides capability for the ship to operate much more efficiently at slower speeds, increases mission duration capability, reduces emissions, and provides emergency take-home capability in the event of a failure of the main propulsion diesel engines. When coupled to the main propulsion gearbox, the system allows the ship to operate quietly and efficiently during loitering operations while providing superior fuel economy for increased on-station operations and capability.
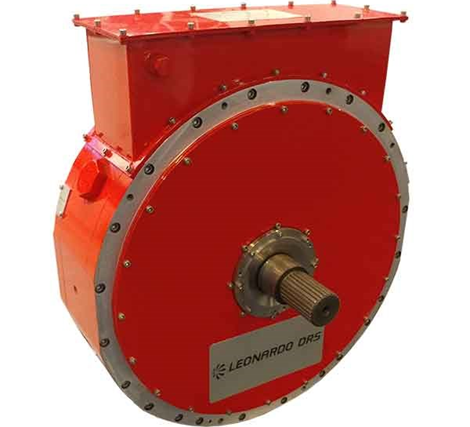
Already used in multiple oil & gas, marine and transport applications, the system includes two of the most power-dense permanent magnet motors on the market providing significant advantages in size, weight, efficiency and performance over conventional electric induction motors and produce more torque from the same amount of supplied current. Their smaller footprint allows greater flexibility in engine room design and increased cargo space, and their simpler more rugged construction results in proven reliability and durability, notes the company.
Maximizing use of the electric drive increases the platform’s green credentials and reduces operational time on the main propulsion engines, providing additional multiple benefits. Because electric motors are virtually maintenance free, life cycle costs over the planned 40-year vessel life are minimized by reducing maintenance hours needed on the engines. Using propulsion diesel engines at slow speeds adds significant wear and tear on the engines and increases the potential for coking/wet stacking. By adding the electric auxiliary propulsion system, the Coast Guard expects to have a built-in advantage of reducing not only fuel and maintenance requirements, but total lifecycle costs and increased safety for the fleet. The main engine overhaul cycle, typically planned at 15 years, can be extended to 25 years. For more info, see www.leonardodrs.com.