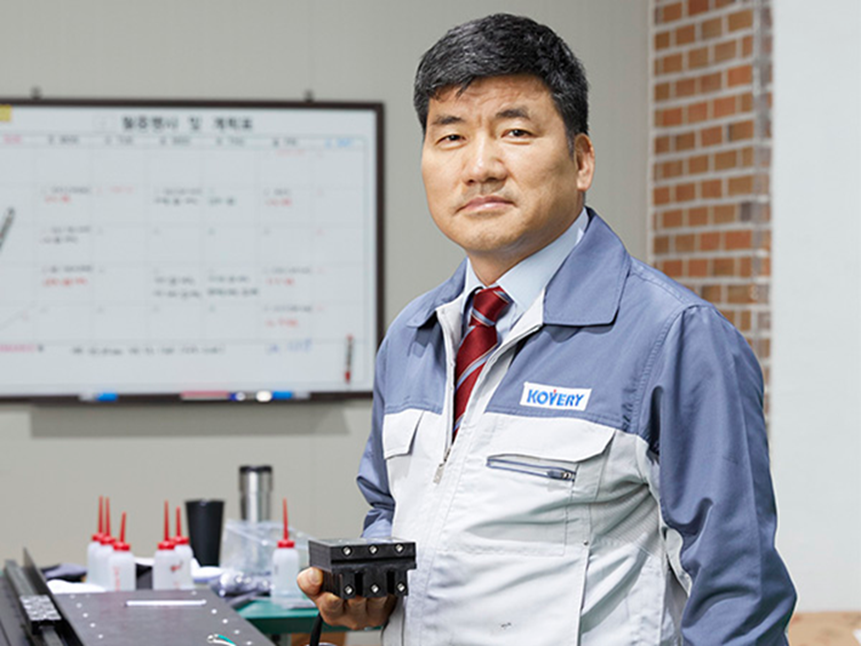
Constant velocity control is essential for many advanced industrial processes, but traditional motor designs give rise to cogging forces which generate ripples in the motor velocity. Precision motors from Kovery of South Korea use innovative magnetic technology to eliminate or minimize cogging forces that cause velocity ripple and increased bearing wear due to attraction between the stator and the mover parts. For commutation and position control, the motors employ precision optical encoders from Renishaw.
Linear motors are widely used in major industrial fields including flat panel display, semiconductors, automation, medical diagnostics, 3D printing and machine tools. A linear motor is equivalent to a rotary synchronous motor with a ‘rolled-out’ stator and rotor. Instead of producing a torque for rotation, it produces a thrust force along its length.
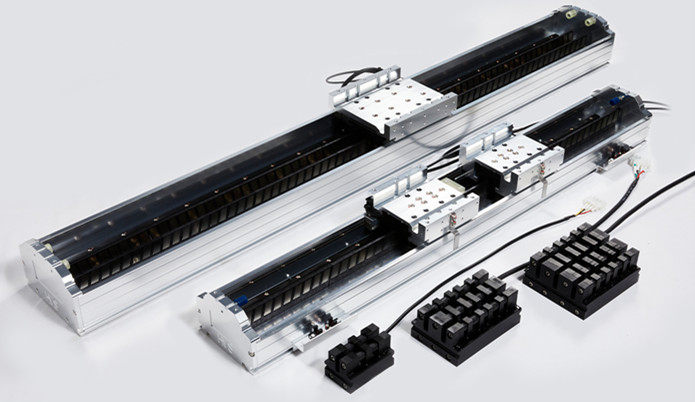
Based in Gyeonggi-do, Kovery specializes in the design and manufacturing of high-precision linear motor systems. Renishaw’s Quantic series of incremental encoders are used in them for commutation and position control as well as other Renishaw metrology products including the Evolute absolute encoder and a laser system for machine calibration. The encoders are critical components to provide reliable position feedback.
Most linear motors are flat linear motors that feature a permanent magnet track under a series of electromagnetic coils (forcer). Precise control of the forcer is required to enable demanding motion control applications in fields such as semiconductor and flat-panel display manufacture where velocity control is essential.
One option for machinery designers is to use a slotless or ironless flat motor that provides excellent control but which can be at the expense of higher thrust outputs. To counter this limitation, Kovery has developed a unique range of motors that minimise cogging forces without sacrificing thrust.
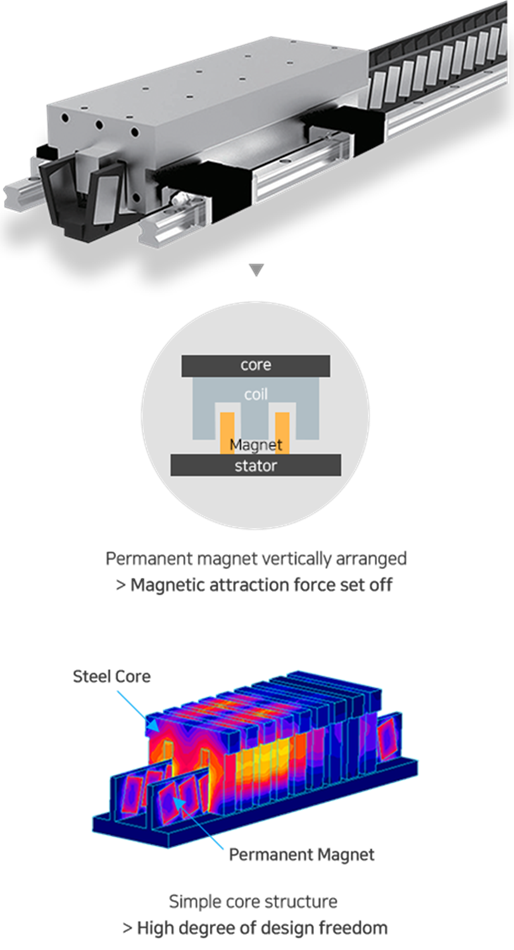
“The linear motors on the market come in various forms. Each design has its benefits but there are always trade-offs,” explains Kim Houng-joong, president of Kovery, pictured at top. “The unique linear motors developed by our company are the first to arrange the permanent magnets in the vertical plane, so that they pass between the pole pieces of the forcer coils.”
“This ensures uniform magnetic flux and an independent magnetic circuit for each magnet track. Our design allows the motor strength to be increased, simply by increasing the number of tracks. The design effectively reduces the normal attractive force between the slotted iron cores and the magnet tracks without sacrificing thrust. In other words, the overall thrust of the motor is increased, and the maximum is at least twice that of a conventional linear motor. Other advantages include reduced weight, increased design freedom, simple assembly and a low cost of ownership.”
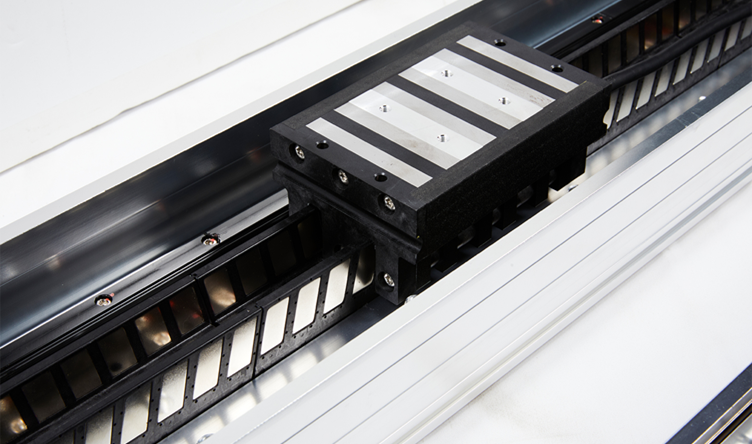
Position encoders enable commutation of linear motors to provide smooth motion and position control. Encoders with lower jitter and interpolation error are preferred as they allow more accurate position control and lower velocity ripple.
Encoders for linear motors need two critical design features to work well — a readhead (sensor) cable with a small minimum bend radius and long cable-life to allow for crimping, kinking, and bending on the machine cable track; and a high maximum operating temperature to withstand the expected heat outputs from the motor coils when power is applied. If the readhead is installed close to the magnetic coils, the encoder must also be able to withstand strong magnetic fields.
Kovery uses a range of Renishaw optical encoders for its linear motors including the advanced Quantic encoder. For semiconductor and flat-panel display process equipment, the motors are equipped with Quantic series encoders that provide 0.2 µm resolution, RTLC40 incremental scale and analogue or digital signal output. For more info, see www.kovery.com and www.renishaw.com.