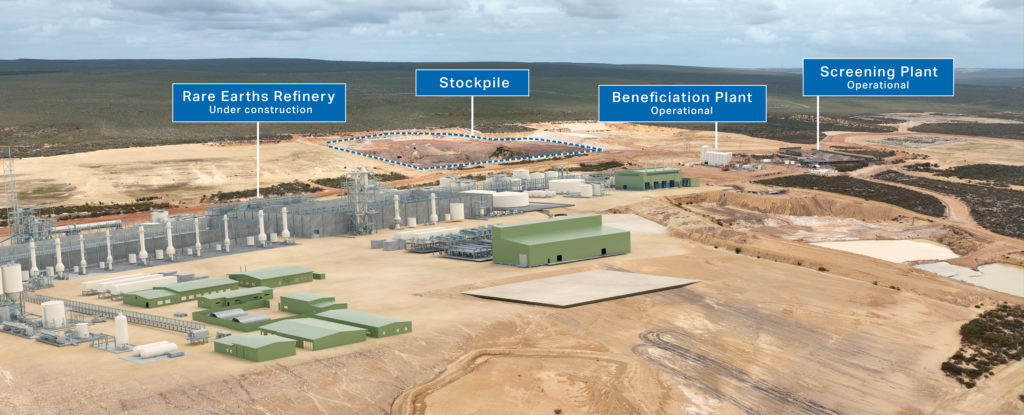
As the world moves towards an electrified future, the demand for permanent magnets is amplifying the already intense pressures on global supply chains.
In the sandplains of Western Australia, a small regional community called Eneabba is at the centre of what is set to become a globally significant and strategic hub for the downstream processing of rare earth resources, a critical component of permanent magnets.
Construction is underway for Australia’s first fully-integrated rare earths refinery, the result of long term strategic planning by Iluka Resources, a leading producer of zircon and high grade titanium dioxide feedstocks (rutile and synthetic rutile).
In approximately two years Iluka will be producing both light and heavy separated rare earth oxides, including the ‘magnet’ rare earths – neodymium (Nd), praseodymium (Pr), dysprosium (Dy) and terbium (Tb).
Found in electric vehicles, wind turbines, electronics and a range of defence and communication applications, the demand for magnet rare earth oxides has resulted in a global supply deficit for these critical minerals.
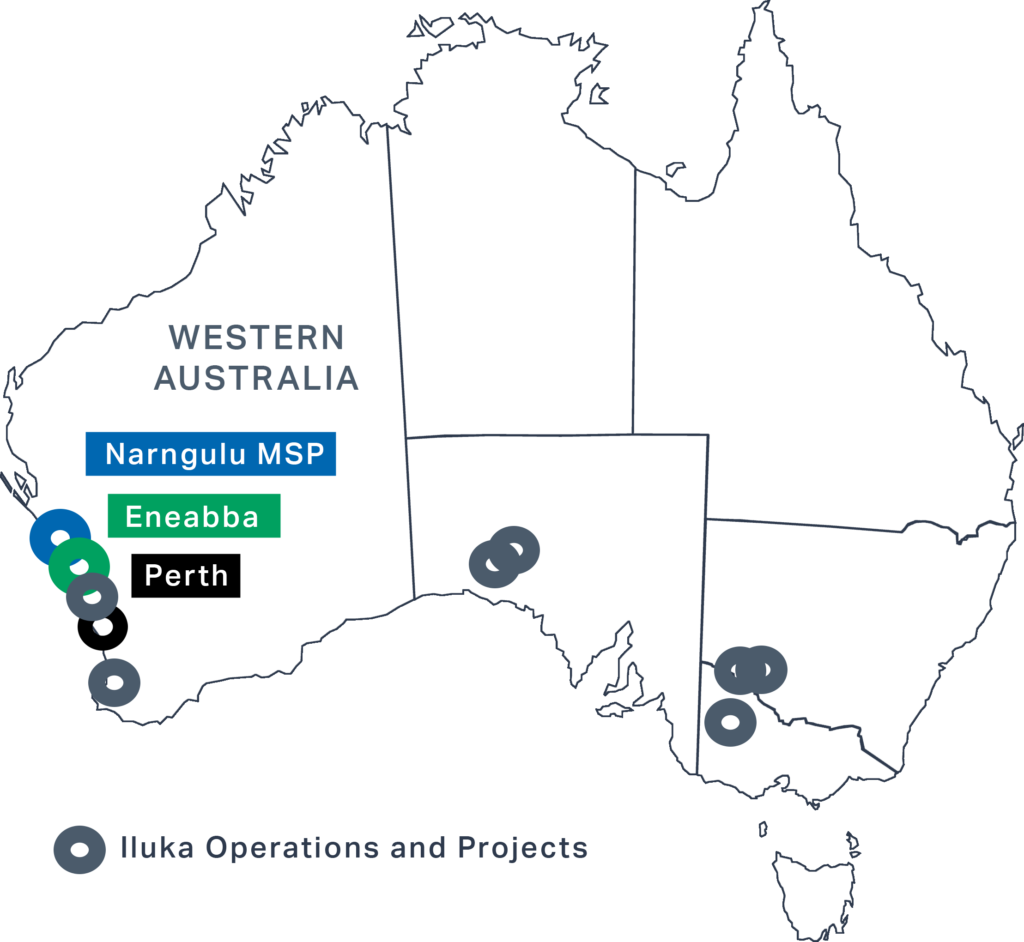
So why would a company that produces zircon and titanium dioxide feedstocks build a rare earths refinery?
Rare earths co-exist with Iluka’s mineral sands products and, since the 1970s, Iluka has stockpiled its rare earth bearing minerals in a former mining void in Eneabba. Separated during the processing and extraction of zircon and titanium dioxide feedstocks, over 1 million tonnes of heavy mineral concentrate has been stockpiled by Iluka. Rich in the highly valuable light and heavy rare earths, Iluka’s stockpile is now the world’s highest grade rare earths operation.
In April of 2022, Iluka announced that the company had entered into a risk sharing arrangement with the Australian Government to develop a globally significant rare earths refinery in Australia. This arrangement included a A$1.25 Billion non-recourse loan from the government’s Critical Minerals Facility, established to provide support for critical minerals projects.
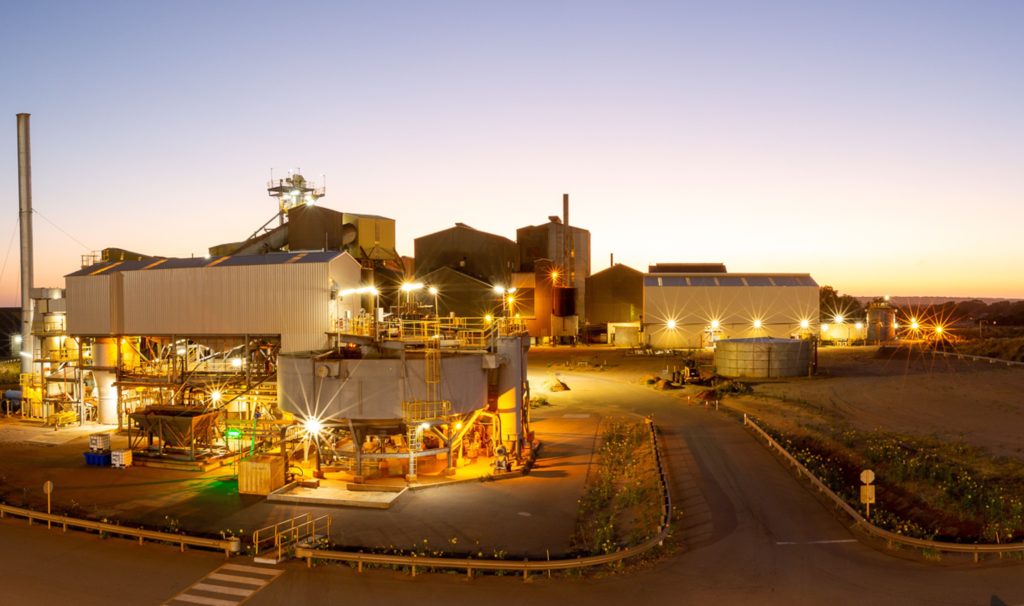
The refinery will be capable of processing up to 23,000 tonnes per annum of separated rare earth oxides, with processing, separation and finishing all completed at the one location in Eneabba.
The state-of-the-art design will also enable flexibility in processing of feedstock, including product produced by Iluka and by third parties.
“As one of few facilities in the world that will produce both light (Nd and Pr) and heavy (Dy and Tb) separated rare earth oxides, Iluka’s refinery positions the company and Australia at the forefront of an accelerating transition to a lower carbon economy via electrification.” said Iluka’s Managing Director, Tom O’Leary.
“Diversified supply chains, particularly for the procurement of strategic materials, is a growing priority for industry. Iluka is focussed on ensuring we can deliver a sustainable and secure supply of these critical minerals.”
By 2026, excluding supply from China, Iluka’s refinery is forecast to produce over 60% of refined heavy rare earth oxides, dysprosium and terbium from the company’s stockpile of material alone. As Iluka introduces additional feedstocks through the refinery, the volume of refined magnet oxides produced is forecast to increase.
The company has already begun work on securing additional feed, including developing internal Iluka projects that contain rare earths and through investment in third parties. Iluka recently announced a strategic partnership with Northern Minerals Ltd, who are developing a rare earths project in Western Australia that is characterised by a high assemblage of heavy rare earths (Dy and Tb).
Aside from the security offered through a diversified supply chain, Iluka is working to produce a low-impact product, that is responsibly mined and processed under Australian regulations.
Iluka’s production of rare earth oxides as a co-product provides significant advantages in sustainability when compared to current production.
The closed circuit design of the refinery will enable the recovery and reuse of both water and reagents used in the processing circuit, dramatically reducing the volume of waste produced while also lowering the refinery’s processing costs.
To demonstrate the overall lower impact of its rare earth products compared to many other producers, and to identify and plan for scenarios to reduce their impact, Iluka is completing a Life Cycle Assessment (LCA) for its rare earth products. The LCA will evaluate the effects that Iluka’s rare earth products have on the environment during the mining and processing, including the global warming potential, power and water usage, and human toxicity potential.
Iluka’s rare earths development is progressing from strength to strength. The company has commissioned a Screening Plant and a Beneficiation Plant to further upgrade the material before entering the refinery circuit and, despite the global supply chain challenges, work on the refinery remains on schedule. Beyond the production of rare earth oxides, Iluka is considering progressing even further along the rare earth supply chain, including rare earth metallisation, an essential step in the development of permanent magnets.
For further information on Iluka visit www.iluka.com