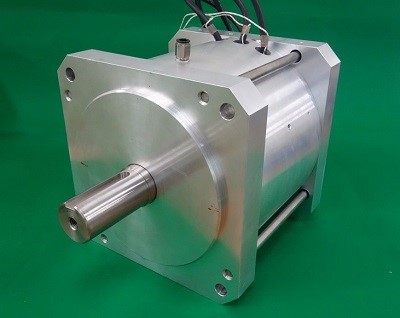
Hitachi Metals reports that it has made an important advancement in the use of amorphous magnetic metal for cost-effectively manufacturing electric motors, a development that could bode well for improving the energy efficiency of electric vehicles, industrial equipment and electrical appliances.
Using specialized amorphous metal from its subsidiary Metglas to form the motor teeth, Hitachi released data demonstrating a four to five-fold reduction in core loss than experienced in a comparable motor with standard magnetic steel sheet teeth – and has applied this to a new design that it says can be economically mass produced.
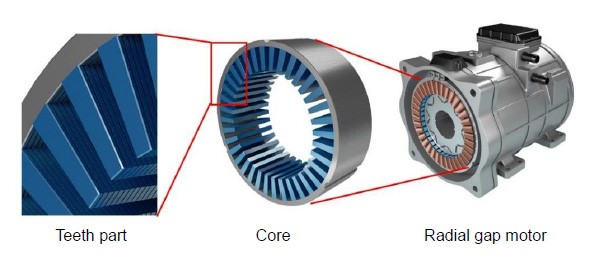
“One of the means to achieve higher efficiency in motors is the use of amorphous metals for cores, the core loss of which is as low as 1/10 or less that of magnetic steel sheets,” said the company. “However, amorphous metals are harder to process than magnetic steel sheets, which has conventionally posed a problem for productivity when they are processed into complicated shapes.”
In the structure recently developed, Hitachi researchers focused their efforts on a core with a low core loss that would be relatively easy to manufacture and applied laminations of sheared Metglas amorphous metal only to the teeth.
A prototype 11 kw radial-gap motor was produced using various motor materials belonging to the Hitachi Metals Group including not only Metglas for the teeth but also its Hidense ultra-high density isotropic bonded-magnets and enamelled wires.
Evaluation of the prototype confirmed a motor efficiency of 97.2 – high enough to meet IE5 standards, the highest level in the guidelines for motor energy efficiency of the International Electrotechnical Commission, said the company. The prototype is an 11 kw radical gap motor, the most common type motor distributed in the market, allowing the use of the stator coil structure which can be produced using existing manufacturing technology.
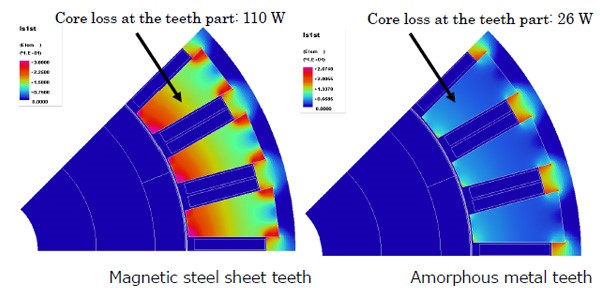
The benefit of amorphous materials for use in electric motors has been known for years, however, researchers have struggled with developing a solution that could be suitable for mass production. Amorphous metal has a disordered atomic structure in contrast to the crystalline structure of conventional metals, providing high tensile strength and extremely low magnetic losses.
A major problem with amorphous metal, however, has been to manufacture it economically due to the difficulty in cutting and machining the material which is harder than sheet steel. Hitachi’s Metglas unit using a proprietary high-speed casting process and other techniques, has pioneered the development of numerous applications using the material, particularly for transformers.
Metglas provides this description of its material. Unlike the crystalline structure of other magnetic materials, all the atoms in an amorphous metal are randomly arranged, thus giving it a higher resistivity (about three times) value than that for crystalline counterparts. Amorphous alloys are prepared by cooling the melt at about million degrees per second. This fast cooling does not give the atoms enough time to rearrange into stable crystalline form. As a result, one gets metastable amorphous structure. Because of the absence of crystalline structure amorphous alloys are magnetically soft (lower coercivity, lower core loss, higher permeability). High resistivity gives lower loss at higher frequencies. The losses are among the lowest of any known magnetic materials.
For more information, see www.hitachi-metals.com, and www.metglas.com.