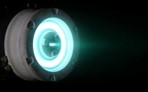
Always a showcase for cutting-edge technology in aerospace progress, SpaceTech Expo-Europe will have an assortment of magnetics-based solutions on display when it opens in Bremen, Germany on November 14. Advancements in propulsion using Hall-effect thrusters for microsatellites, magnetometry and component designs will be among the solutions exhibited. ExoTerra, Enpulsion and Thermocoax are among the companies involved in Hall-effect thrusters. Other exhibitors involved in magnetic technologies include Bartington Instruments, Pfeiffer Vacuum, Stirling Cryogenics, plus numerous others. Magnetics Magazine is a long-time media partner of the event.
As the small-satellite market expands, so do the demands for specialized propulsion powered by Hall-effect thrusters. Unlike chemical propulsors traditionally used in spacecraft, Hall-effect systems generate thrust from a magnetic field that accelerates the propellant, usually xenon. They are less powerful than chemical propulsors but require less fuel and propel for longer, making them ideal for long-distance space exploration.
In June, Littleton, Colorado-based ExoTerra marked a milestone when its Halo propulsion system successfully lit on its first attempt and powered a DARPA (Defense Advanced Research Projects Agency) spacecraft. The Halo module is an integrated electric propulsion system designed and built by ExoTerra in Littleton, Colorado around the company’s Halo Hall-effect electric thruster, propellant distribution components, and power processing unit. The demonstration marks the first operation of a Halo in orbit. Additional modules are expected to be commissioned soon in successive missions.
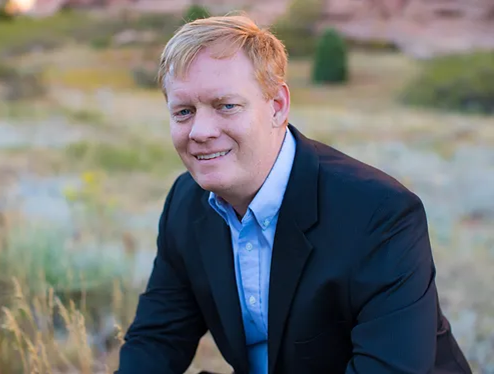
“Working with BCT and DARPA on the Blackjack program has been a great experience,” said ExoTerra’s CEO Mike VanWoerkom. “We’re all very excited to finally have the thruster validated in space and are looking forward to providing propulsion for several more flights in the coming year.” Founded in 2011, ExoTerra designs, manufactures, and tests electric propulsion elements for small spacecraft, from discrete components to integrated propulsion modules to full spacecraft buses.
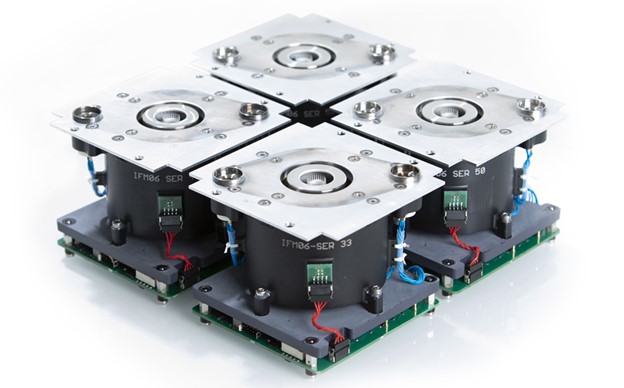
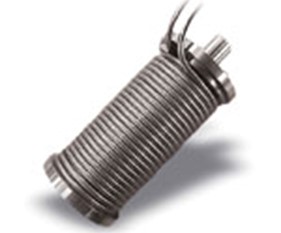
Thermocoax magnetic coils are primarily intended for manufacturers of new-generation Hall-effect thrusters that will be used in geostationary satellites where electric propulsors can be deployed in conjunction with chemical propulsors for the different satellite maneuvers in orbit. Its coils are also ideal for application in space probes on very long-distance explorations.
The magnetic field required for electrical propulsion is generated by placing magnetic coils around the spacecraft engine. The coils are supplied with cables that have a specific geometry and customized connectors to support the constraints associated with the application and usage time. The company’s proprietary mineral insulated cabling is coiled on specific nodes and affixed by a special soldering procedure.

Serving a variety of applications, Bartington Instruments of the UK designs and manufactures high precision fluxgate magnetometers, gradiometers, magnetic susceptibility instruments, Helmholtz Coil systems and associated data acquisition equipment for the aerospace industry.
Based in the UK and founded in 1985, today around 80% of its products are exported worldwide to customers in varied market sectors including aerospace, land/sea/air defense, surveillance, security, space, physics, geophysics, industry, archaeology, medicine, and oil and mineral exploration. It recently completed development of a replacement magnetometer for a Saab combat aircraft, the first product it has designed specifically for use in aircraft navigation systems.
Numerous applications in aerospace require cryogenic cooling and Stirling Cryogenics, located in Eindhoven, The Netherlands, specializes in supplying solutions for them, often highly customized. Objects in space are exposed to its almost perfect vacuum, cold and solar radiation. Organizations such as NASA, ESA, universities and commercial organizations involved in building spacecraft, satellites, components and instruments often need to test their equipment and materials in extreme low and high temperatures and vacuum conditions. This is done in earth-based simulation chambers in which the conditions in space are simulated by creating a high vacuum and extreme low temperatures.
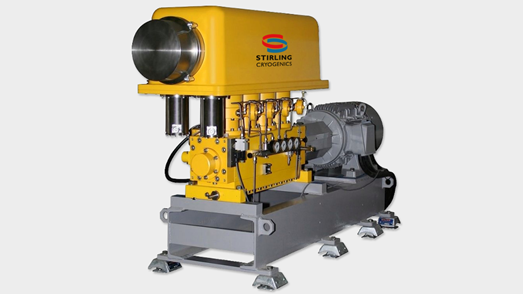
Liquid oxygen is widely used as oxidizer in different types of rockets. By cooling the liquid oxygen below its usual boiling temperature, density of the liquid increases so more mass can be stored in the same volume. Cooling of a cryogenic liquid flow can be done directly in the heat exchanger of a Stirling Cryogenerator.
With the growing interest in de-carbonizing air traffic, liquid hydrogen is seen as the fuel of the future since it can be produced in a fossil-free way and has a high energy to mass ratio. Projects in development typically require relatively small amounts of liquid hydrogen, leading Stirling to provide small production systems that can be used onsite.
Cooling of superconducting magnets is another key application for the company. In tandem with liquid hydrogen as airplane fuel, superconductivity is regarded as the one of the main technologies to provide thrust using superconductive motors and other components. Newly built superconducting magnets need to be cooled down from ambient for the first time, and to be kept cold while in use.
Another exhibitor steeped in magnetic technology is Pfeiffer Vacuum which produces an extensive range of turbopumps with hybrid and magnetic bearings, also backing pumps, leak detectors, measurement equipment, as well as vacuum systems and chambers for space simulation applications.
New explosion-proof pumps from the company, based in Asslar, Germany, demonstrate some of its prowess in magnetic technology. It recently expanded its OktaLine ATEX series for use in potentially explosive environments or for evacuating explosive gases.
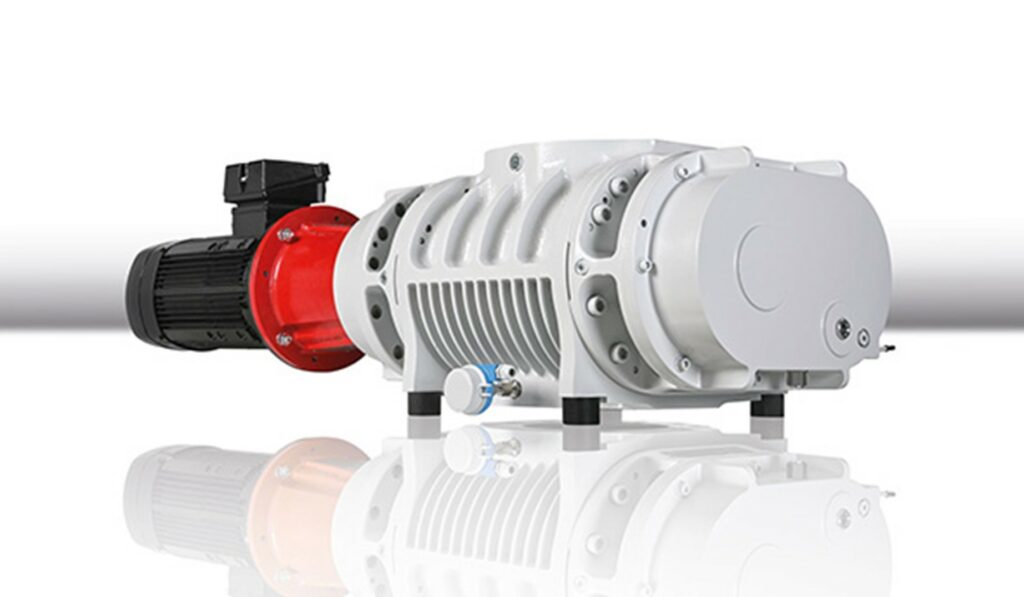
Their magnetic coupling is key to the protection of the hermetically sealed devices, eliminating the need for shaft seals, which are inherently weak points if it comes to pressure surges and are high maintenance. Due to the magnetic design, there is no risk of zone entrainment. Compared to pumps with shaft seals, the OktaLine’s magnetic coupling achieves up to 20 % lower operating costs and considerably reduced maintenance costs.
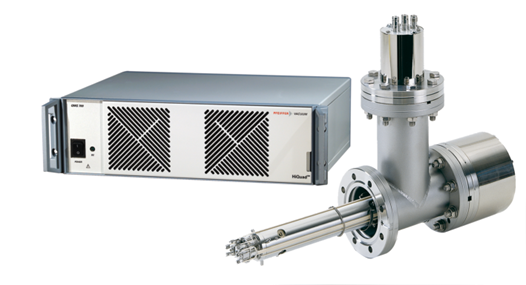
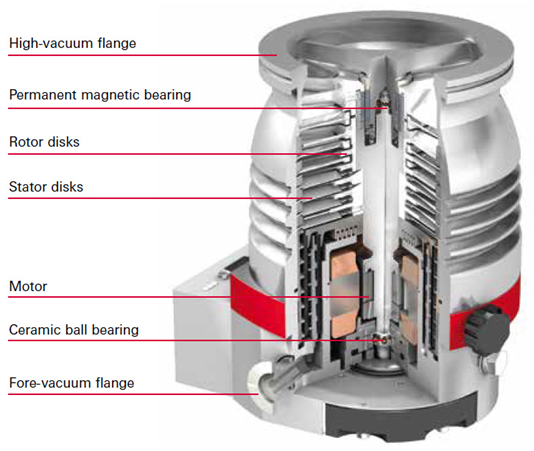
Basically, the design of the turbopump is similar to that of a turbine, explains Pfeiffer: “Inside the pump, several rotor disks are mounted on a shaft. Between them are stator disks whose blade orientation is mirror-inverted to that of the rotor blades. As a result, the gas molecules to be pumped are conveyed from the high-vacuum flange along the individual turbo stages to the fore-vacuum flange. The rotor of the turbopump is driven by a brushless three-phase synchronous motor. This enables very high rotational frequencies of up to 1500 Hz to be achieved. The rotor shaft bearing, in turn, consists of a permanent magnet bearing on the high vacuum side and a high-performance ball bearing on the fore vacuum side. Although the ball bearing is minimally lubricated, the pump generates an oil-free vacuum.” For a full presentation about the turbopump, see www.pfeiffer-vacuum.com.
For more info, see www.spacetechexpo-europe.com.