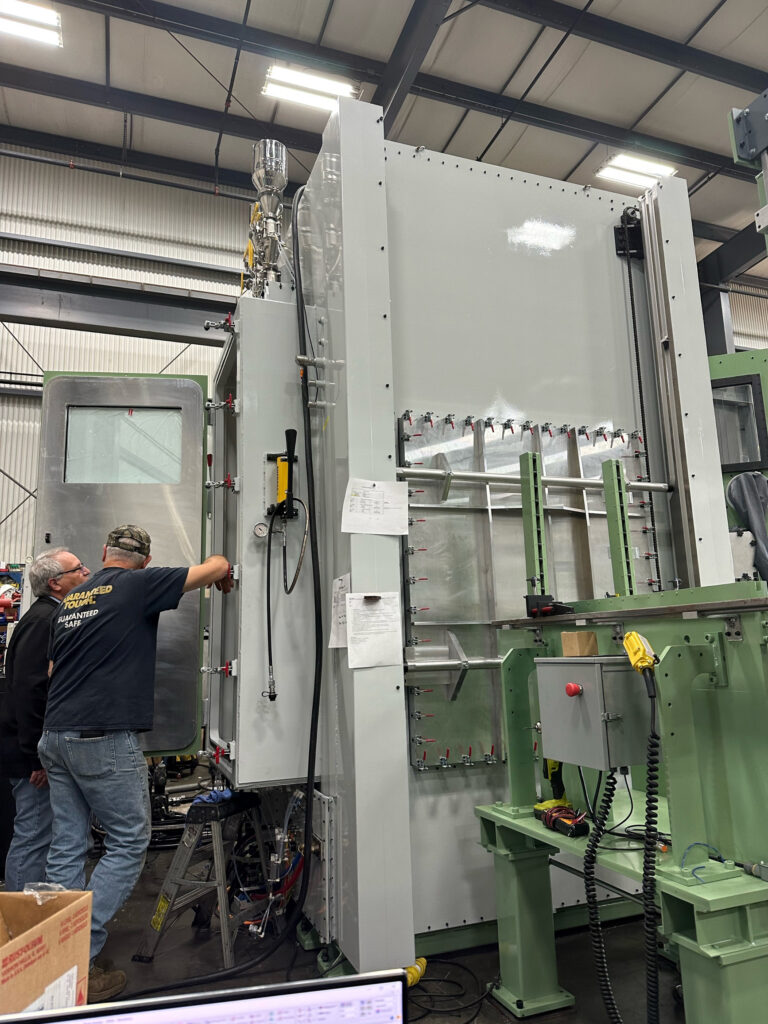
The global permanent magnet market is expected to grow by 9.5 % CAGR from 2021 to 2026. This growth is fueled by consumer electronics, in applications such as smartphones, sensors, computers, loudspeakers, etc. Of course, the high demand for electric vehicles (EVs) and green technologies is expected to augment this growth substantially as well.
With high magnet costs imposed by China, the United States is being forced to start its production of rare-earth magnets demanding the use of different equipment to manufacture them for different applications and technologies. Within the magnet manufacturing process, there is an important process that requires compacting or pressing the magnet powder to get the final magnets. For this process the use of powerful magnet powder presses is necessary. The magnet pressing process allows the production of magnets with specific shapes and sizes, making them highly customizable for different purposes and applications. The process of pressing magnet powder into magnets involves compressing the fine particles of magnet powder together, typically using a hydraulic press, and applying a uniform magnetic field to align the powder particles in the non-magnetic cavity region during the compacting process. The pressed magnets can then be further processed to achieve desired magnetic characteristics such as increased coercivity or improved temperature stability for many applications. One advantage of pressing magnet powder into magnets is its cost-effectiveness. In addition, pressing magnet powder requires fewer steps and less energy, making it a more economical and efficient option for magnet production. Additionally, this method allows for mass production, ensuring a steady supply of magnets at an affordable price. Furthermore, pressing magnet powder into magnets offers greater design flexibility. The ability to shape the magnet according to specific requirements makes it suitable for various industries such as automotive, electronics, aerospace, and renewable energy. For example, pressed magnets can be tailored to fit intricate spaces within electronic devices or used in permanent magnet motors for EVs to enhance their efficiency. This magnet manufacturing process enables the production of customized magnets with enhanced properties suitable for diverse applications. As technology continues to advance, pressing magnet powder will likely remain an essential method in creating high-quality and efficient magnetic products.
Gasbarre Products offers a full range of industrial custom presses designed to take on a full range of applications. Gasbarre has developed a new range of magnet powder compaction equipment for the development, processing, and production of rare-earth magnets.
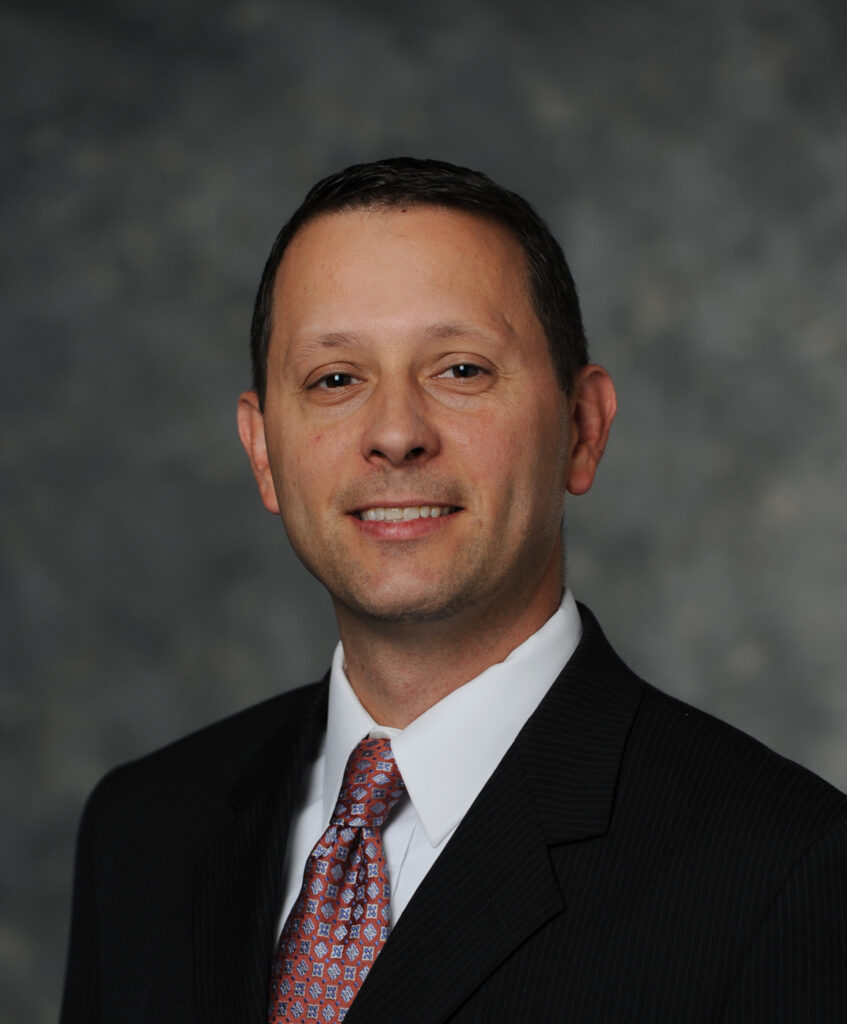
“For over 50 years Gasbarre has made the best powder compaction presses in the world. We are proud to be a part of building the critical rare earth supply chain in the United States through our line of rare earth magnetic presses. We are heavily invested in supporting this fast-growing segment and look forward to establishing strong partnerships with our current and future customers there,” said Gasbarre President Heath Jekins.
Gasbarre Products with consultancy support of “Salvador Consultant” has designed, manufactured, and tested the first magnet powder presses to produce neodymium magnets in the United States. The Gasbarre magnet presses were designed, built, and tested in DuBois, Pennsylvania. The magnet presses were designed for the pressing process of neodymium magnet powder under a uniform magnetic field. These magnet presses will be employed to produce sintered neodymium magnets for the US industry. For more information related to the production of rare-earth magnets in the US, please consult the September/October 2023 Magnetics Magazine issue.
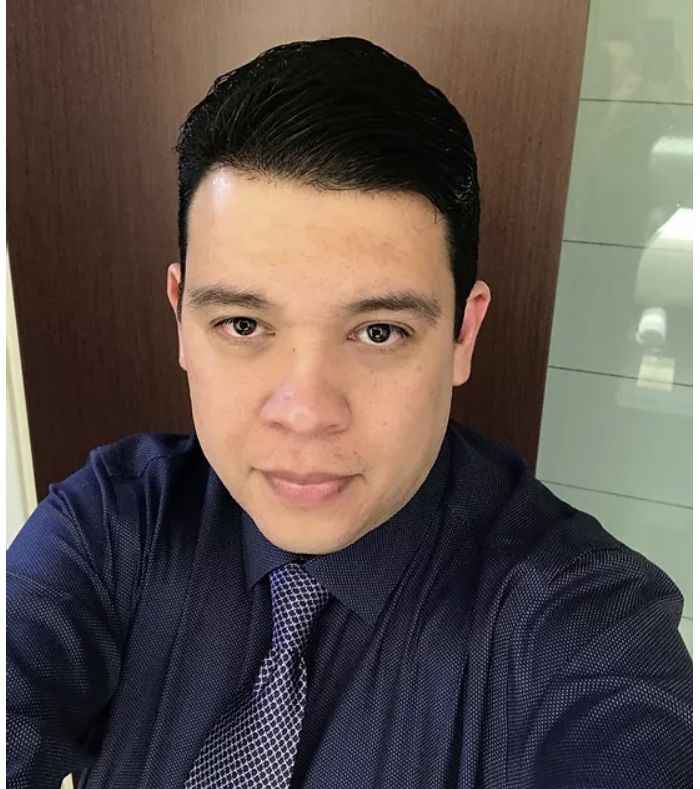
Magnetic and Electromagnetic Consultant, Salvador Magdaleno said,”The Gasbarre magnet presses were designed and equipped with electromagnets with optimized pole caps to produce high magnetic fields in the powder cavities. The magnetic structures of the magnet presses were designed using a deep and wide knowledge about magnetic materials, magnet materials, and magnetic field production”.
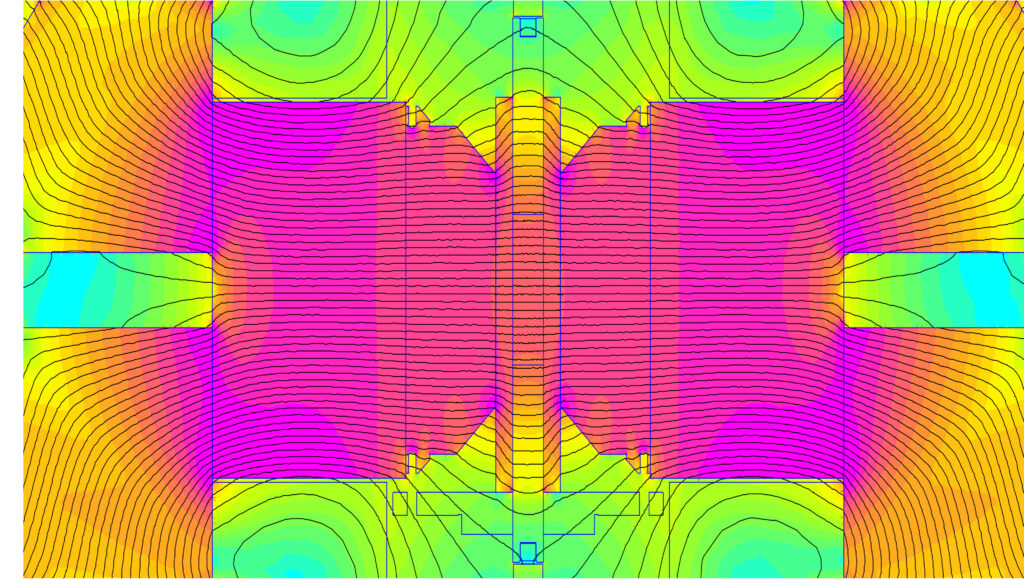
The Gasbarre magnet presses can be automated to be integrated into the production line and the magnet presses can operate under short operation cycles to increase the production of magnets.
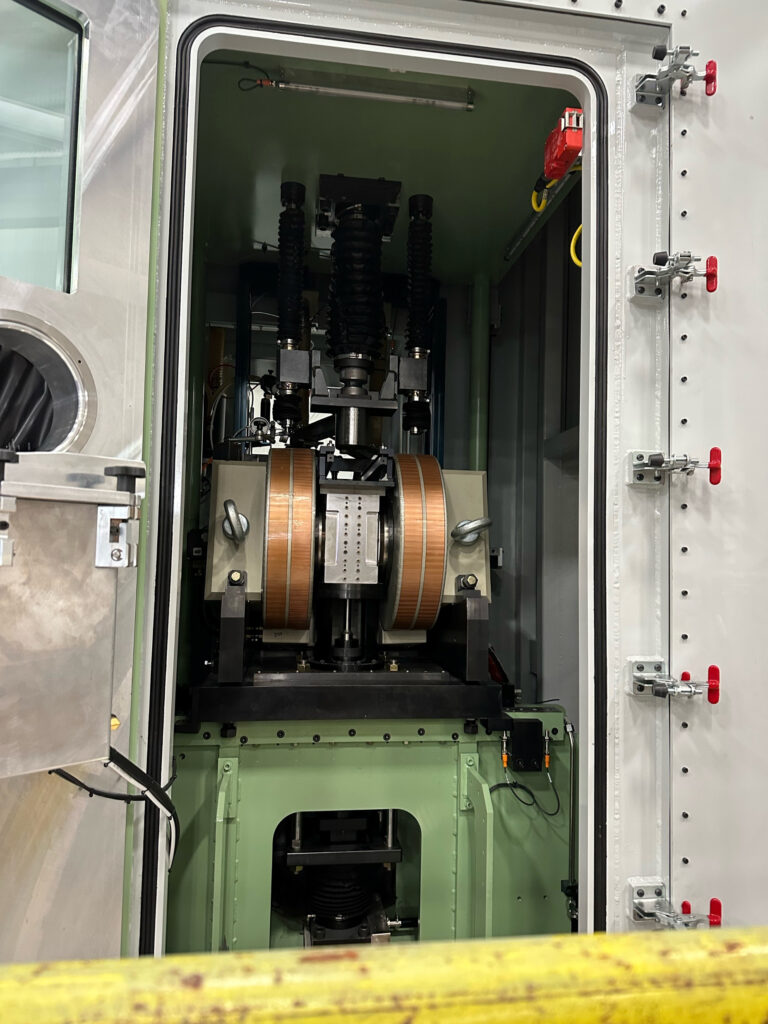
“Gasbarre Products offers a full range of industrial heat-treating equipment for the development, processing, and production of rare-earth magnets. Gasbarre offers industrial furnaces for permanent magnet development and production. Batch and continuous vacuum furnaces are designed by Gasbarre for rare-earth magnet production,” said Global Sales Manager, Mark Thomason.
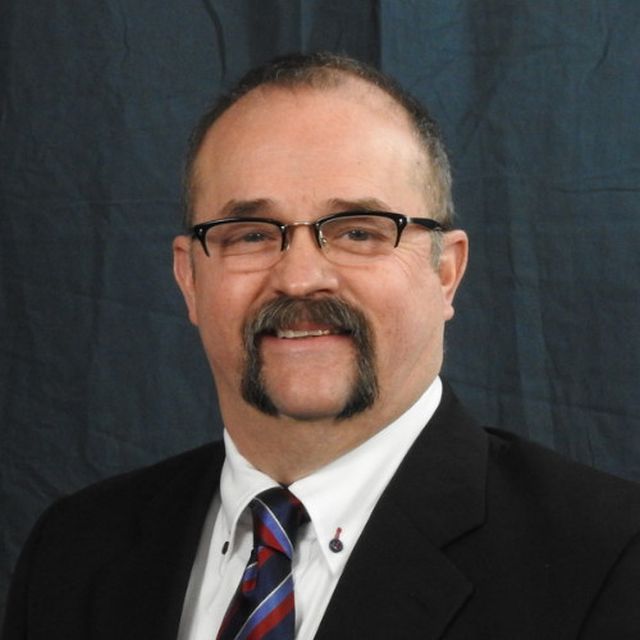
Gasbarre Products offers mechanical, electric, hydraulic, and isostatic presses for the compaction of powders. Mechanical powder compaction presses are commonly used for powdered metal and technical ceramics production but are well-suited for other industrial applications. Gasbarre mechanical presses can handle capacities ranging from 5 to 800 Tons and can manage simple to complex multiple-level components.
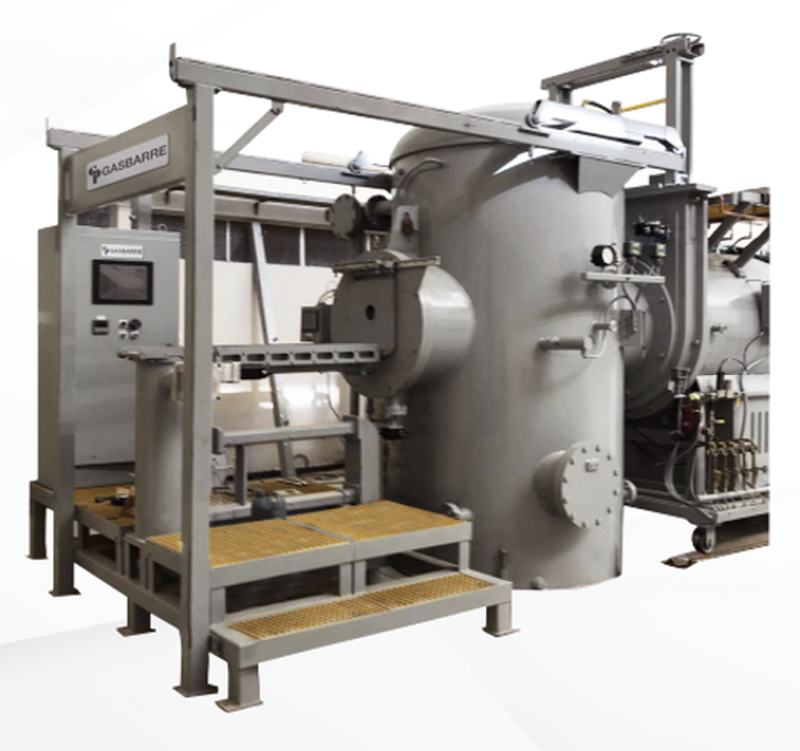
Moreover, Gasbarre’s hydraulic powder press machines come manufactured in capabilities ranging from 15 to 1200 Tons for single- or multi-level parts. Hydraulic presses are suitable for carbides, powder metals, ceramics, polymers, and other particulate material industries.
Gasbarre electric presses offer precise powder compaction for numerous geometries. These machines comprise various parts designed for maximum accuracy and repeatability, with features like high-efficiency drives and freely programmable axes for complete compaction cycle control, including die filling, die motion, upper punch motion, and ejection cycle.
Gasbarre’s SIMAC product line includes dry bag cold isostatic press technology available in single- and multi-cavity models. These isostatic presses allow users to manufacture uniform-density components using a dry bag design that makes powder filling, compaction, and ejection simpler and more efficient.
For information about Gasbarre magnet production equipment please contact Gasbarre directly (inquiries@gasbarre.com)
For more info, see www.gasbarre.com