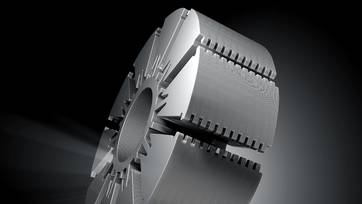
Waelzholz GmbH & Co. showcased its electrical steel strip grades with precisely defined magnetic properties at CWIEME held in Berlin in May, particularly its stress-bearing high-strength and ultra-high-strength grades for use in high-frequency automotive drives.
Due to their high engine speeds, electric drive concepts place tremendously high demands on the mechanical strength of the electrical steel strip used, explained Waelzholz staff. For this purpose, Waelzholz has developed special electrical steel strip grades that combine high tensile strength and outstanding magnetic properties, the company said. Due to a strength-increasing alloy, Waelzholz’s HS grades achieve yield strengths of over 500 MPa, making them especially suitable for use in the manufacture of rotor stacks exposed to high mechanical stress.
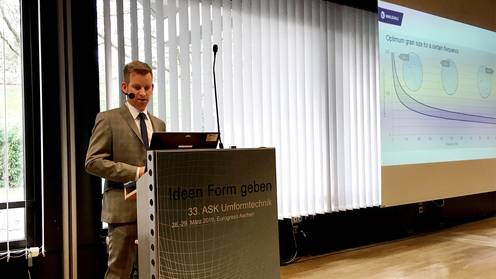
The Berlin show was the latest in a series of recent efforts by the company to highlight its electrical strip products. In March, at the 33rd Aachen Steel Colloquium, as part of a series of lectures on low-Loss electrical steel sheets for energy-efficient drives, Johannes Zufacher from the company’s electrical steel strip materials technology department spoke on the production of high-alloyed steel grade concepts for use in automotive drives.
Due to their high speeds and the resulting high frequencies in the magnetic core, new drive concepts place particularly high demands on electrical steel strip, he explained. As a result, sophisticated manufacturing processes are needed to meet these requirements. Based on high-silicon alloying, the magnetic and mechanical properties are adjusted through a combination of cold rolling and annealing processes with the individual process steps being carefully coordinated.
The goal is to always achieve the lowest possible core losses and high yield strengths in order to improve motor efficiency while manufacturing the material in a process and application-optimized manner. “Optimizing the magnetic and mechanical properties is achieved through the interaction of the individual influencing parameters, taking into account the possibilities of large-scale industrial production,” said Zufacher.
Earlier, at a symposium in Salzgitter, Germany in November organized by Volkswagen and others to focus on materials and concepts for vehicles of the future, Norbert Brachthaeuser, head of materials technology for electrical steel strip at Waelzholz, presented new NO grades for use in electric vehicle drives and the latest advancements in its Backlack bonding technology.
The Backlack system is designed to bond lamination stacks for electric motors without any disturbance to their magnetic flux. It bonds steel plates made from electrical steel strip without damaging the material unlike conventional bonding processes such as welding, stamping and riveting which leave contact spots behind. Using Backlack, no stress or deformity is applied to the material and. as a result, the key material properties of electrical steel strip remain fully intact, said Brachthaeuser.
It also prevents frequency buzzing which can be an issue with mechanical bonding methods, he noted. “Our Backlack technology makes complex stack geometries possible without the need for follow-up fine-tuning to meet precision requirements. Lamination stacks bonded using Backlack are compact and waterproof.”
Despite the wide variety of potential scenarios for the development of e-mobility, one thing is certain, said Brachthaeuser, the demand for non-grain-oriented electrical steel strip will continue to grow in the future. Non-grain-oriented electrical steel strip is an important performance factor, especially in the motors of electric vehicles, which must withstand high loads. High-quality, thin electrical steel strip significantly reduces eddy current losses at high frequencies, thereby making highly efficient, low-loss electric drive systems possible.
A month earlier, at another presentation, Daniel Dunker with the materials technology unit at Waelzholz, noted that together with its customers the company will continue working intensively on current development topics such as fast bonding of electrical steel strip laminations and the use of increasingly thin layers.
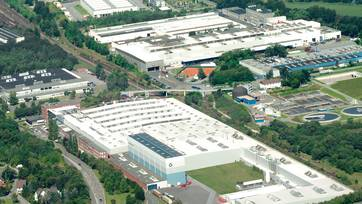
Headquartered in Hagen, Germany, Waelzholz has 2,400 employees worldwide and annually produces more than 780,000 metric tons of cold rolled steel strip and shaped wire at nine locations in Europe, North and South America and Asia.
For more info, see www.waelzholz.com.