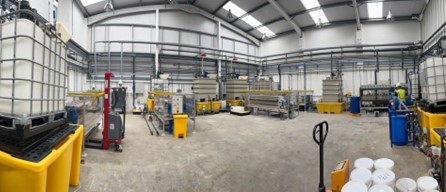
Ionic Technologies, a Northern Ireland-based subsidiary of Australian minerals company Ionic Rare Earths, has secured significant new grant funding from the British government that support developing collaborative rare earth element supply chains within the UK. Two grants have been awarded under Innovate UK’s Climates program involving Ionic and several program partners — Vacuumschmelze, Less Common Metals, the Materials Processing Institute and Swansea University.
In the REEValuate Project, Ionic will partner with UK-based metal and alloys manufacturer Less Common Metals and Germany-based magnet manufacturer Vacuumschmelze to produce magnets containing 100% recycled heavy rare earth elements and light rare earth elements.
Under the partnership, VAC will provide pre-consumer NdFeB magnet scrap (swarf) to Ionic Technologies, which will use its patented technology to produce high purity magnet REOs from the scrap at its Belfast Demonstration Plant. LCM will then reduce the oxide to rare earth metals and alloys, supplying them back to VAC at the required specification for magnet production.
The initial magnet scrap volume to be processed through the partnership is expected to be up to nine tons, with any process wastes generated to be returned to Ionic Technologies for recycling.
Having previously received UK Government support via Innovate UK, as part of the first round of Climates program funding for circular critical materials supply chains announced 12 months ago, Ionic Technologies will benefit from an additional £292k of grant funding for the REEValuate project, as part of government support totalling £843k for the project.
In the second grant, the government selected the Ionic-led ‘Magnostic’ collaboration to deliver an advanced, demagnetization solution for end-of-life permanent magnets. Ionic is working in partnership with the Materials Processing Institute, a research and technology organization specializing in critical materials, powder metallurgy and other materials processing, as well as Swansea University, a center of excellence for metal processing and handling. The project is valued at £422k, with Ionic Technologies also set to directly benefit from £178k of UK Government funding, also part of the Climates funding.
Focused on the recycling of Neodymium-Iron-Boron (NdFeB) permanent magnets to high purity separated magnet rare earth oxides, Ionic produces of a suite of magnet REOs including neodymium oxide (Nd2O3), didymium oxide (NdPr oxide), dysprosium oxide (Dy2O3) and terbium oxide (Tb4O7) and REO products.
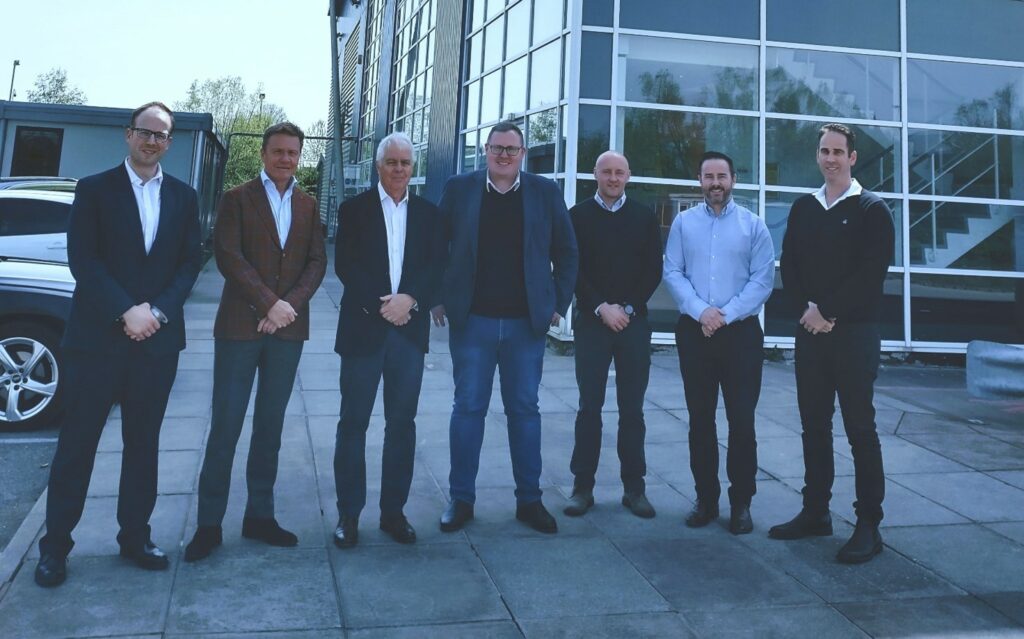
“Collaborating with key supply chain partners is essential in establishing Western supply chains for magnet manufacturing, utilising both light and heavy rare earths,” commented Tim Harrison, managing director of Ionic RE. “LCM is the only Western rare earth metal/alloy manufacturer, and it is of significant benefit to Ionic Technologies and LCM to be able to deliver a project as significant as this within the UK. Similarly, working with VAC represents an enormous opportunity for all involved to show how Western rare earth supply chain partners can deliver cohesively, meeting the demands of the energy transition, advanced manufacturing, and defence.”
“The commercialisation of our recycling technology is moving rapidly, highlighting the strategic importance of the Belfast Demonstration Plant,” added Harrison. “Our supply chain partners have expressed significant interest in procuring REOs from secondary sources, and with this announcement, we are excited to deliver a full schedule of magnet recycling through to mid-2025. We are continuing to produce Light REOs and Heavy REOs in Belfast, constantly optimising the performance of the process for greater efficiencies. By supporting this progressive collaboration between UK and EU-based rare earth supply chain businesses, the UK Government is facilitating supply chain partners to establish strategically significant collaborations, underpinned with demonstrator projects.”
“LCM is proud to be leading this project in partnership with Ionic Rare Earths,” said LCM General Manager Aaron Riley. “By advancing a fully traceable, circular supply chain, we are not only addressing the growing demand for rare earths driven by clean energy technologies, but also exploring an alternative route for sustainability in the industry.”
“The REEValuate project is an exciting initiative aiming to convert industrial NdFeB scrap into high-quality valuable REOs for magnets. This will be achieved by combining Ionic Technologies’ hydrometallurgical methods with LCM’s established metallothermic and electrolysis processes,” noted Manu Kaimanikal, senior metallurgist and project lead at LCM. “This closed-loop rare earth project is set to drive the establishment of a sustainable circular supply chain of REE’s, offering material-specific recycling, cost and waste reduction, and ensuring traceability, transparency, and regulatory compliance.”
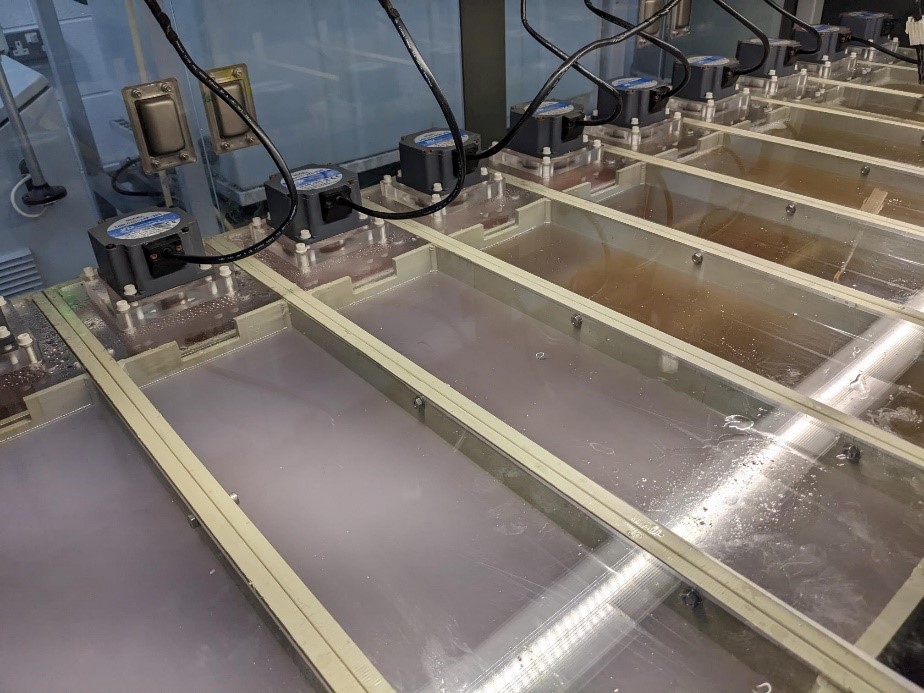

Magnostics Project
The government also has selected the Magnostic Project led by Ionic Technologies for further funding. The project draws upon Ionic’s project management and technical expertise in REE recovery while implementing novel practices currently being piloted and tested by both the Materials Processing Institute and Swansea University. The object is to determine efficient methods for demagnetizing end-of-life rare earth permanent magnets which can be scaled up to complement Ionic’s magnet recycling process. Ionic will work closely with MPI, tasked with optimizing material processing technologies from its base in Teesside, UK as well as Swansea University.

“The Magnostic Project brings us a significant step closer to making commercial scale magnet recycling a reality,” said Harrison. “It is expected to provide efficient solutions to demagnetise magnets, prior to processing them through Ionic Technologies’ patented process. Solutions that enable rapid demagnetisation reduce the implications of handling high specification REPMs and thus reduce costs.
“It is anticipated that significant volumes of end-of-life magnets will require demagnetisation and recycling across global markets in coming years. Ionic Technologies is seeking to provide viable solutions that enable this to happen effectively, positioning the company to be at the forefront of commercialising opportunities in this field.”

“MPI is a world-renowned RTO, with a comprehensive range of pilot equipment at their facilities in Teesside, UK,” he added. “Our Ionic Technologies team will work with MPI to identify process efficiency and effectiveness, and ultimately scalability to commercialisation. “Swansea University has a demonstrated track record as a centre of excellence in metals technologies, located in close proximity to the long-established steel manufacturers of South Wales, UK. We are excited to partner with these two organisations on such a strategically significant development project.”

“IonicRE has been focused on developing Ionic Technologies’ magnet recycling technology, ‘pioneering profit’ by unlocking a new supply chain in the West,” emphasized Ionic Rare Earths’ Executive Chairman, Brett Lynch. The formation of new partnerships backed by government support is integral in building this supply chain and I congratulate the team for their success in securing these valuable grants and support.”
“The UK is rapidly developing leadership in magnet recycling technologies, including the demagnetisation of end-of-life REPMs,” commented Christopher Smith leader of MPI’s Critical Raw Materials Group . “We look forward to collaborating with Ionic Technologies and Swansea University on this important initiative, drawing upon our world-leading facilities in Teesside.”
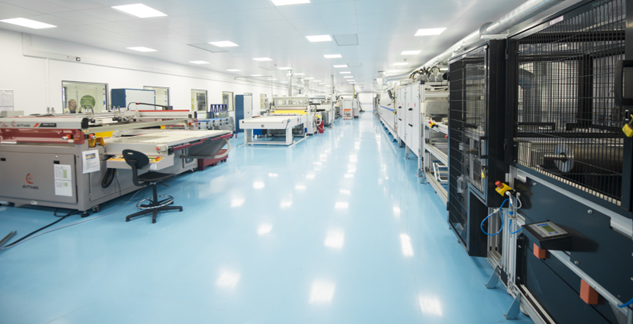
Professor Ian Mabbet, Swansea University’s Deputy Pro Vice Chancellor for Research Culture added:
“This is an exciting project that will maintain UK leadership in the development of a circular economy for critical raw materials with applications in energy and transport. MPI and Ionic Technologies are both at the cutting-edge of this field and we are keen to apply our complementary scientific expertise in metals technologies to deliver successful outcomes, ultimately paving the way to commercialisation.”
Spun out from Queens University Belfast in 2015, Ionic Technologies has developed processes for the separation and recovery of REEs from mining ore concentrates and waste permanent magnets that can achieve near complete extraction of REO’s from lower quality spent magnets and waste (swarf) to a recovery of high value magnet REO product quality exceeding 99.9% REO. The system uses a hydrometallurgical process to extract the rare earth elements (REE), then separate the individual magnet REEs within –Nd, Pr, Dy and Tb – and finally refine to high purity individual magnet rare earths oxides. For more info, see www.ionicre.com.