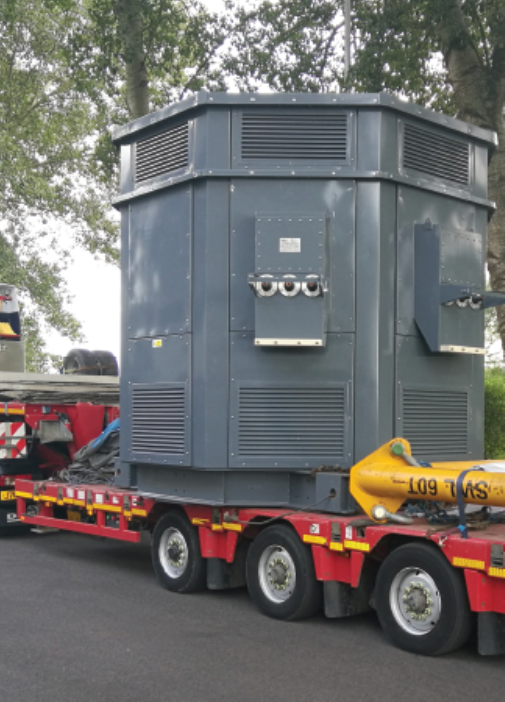
FaultCurrent Limited, a UK-based developer of passive magnetic fault current limiters, is reporting successful results from a recent round of independent tests of its next generation fault current limiter. With 25 tons of magnetic ferrite ceramic tiles at the core of its novel design, it’s a beast. It offers electrical utilities a new, hassle-free way to assure connectivity to distributed generation sources including renewable energy supplies.
“This is the final hurdle in a seven-year journey that has involved fundamental research, ground-breaking innovation, prototyping and re-engineering resulting today in a market ready product,” said Martin Ansell the company’s chairman and CEO.
The final round of short circuit tests on the company’s pmFCL unit were conducted at DNV-GL Group’s KEMA Laboratories in the Netherlands and proved that its technology can be safely applied to a power system to facilitate the rapid connection of additional distributed generation power units including renewable energy sources without an electrical utility having to incur the costs, delays and the invasive risks of network reinforcement.
“We were able to test the short circuit (fault limiting) performance at both 50Hz and 60Hz at KEMA Laboratories, a world-leader in energy consulting, testing and certification, to confirm that our pmFCL can be used on power grid across the world,” he added.
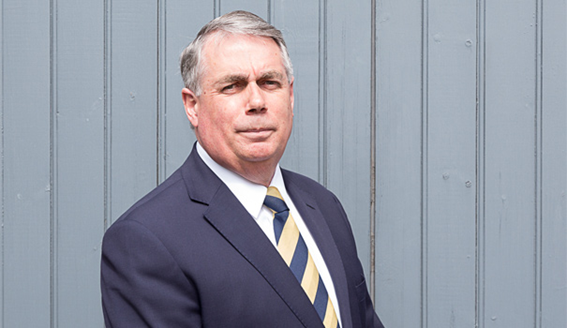
“With the support of the UK government and our investors we have been able to accelerate the completion of our development program and are now working to appoint a network of global sales representatives,” said Ansell, who previously has held executive positions with Alstom T&D, and GE. “We look forward to sharing additional updates as we continue to work to bring our state-of-the-art pmFCL to customers around the world.”
Now the company is turning to the task of forging partnerships with power system owners, system integrators and consultants from across the world to help address the global issue of fault currents and enable a smarter, flexible grid that can more easily accept the connection of renewable & distributed generation.
FaultCurrent’s product is considered an advanced Smart Grid technology that provides additional fault level headroom when ineeded during a fault event to quickly, safely and easily allow the connection of new distributed generation sources. According to the company, the technology behind this next generation FCL has been achieved through a combination of magnetic engineering insights, including using low-cost ferrite permanent magnets to saturate a network of inductors.
Unlike other fault current limiters, pmFCL is designed to be “fit and forget” technology. The self-contained three phase unit is delivered to the site as a complete unit that is ready to go once placed on a concrete pad and requires no maintenance beyond simple inspection.
It provides additional fault current headroom but unlike a current limiting reactor, presenting a low impedance during normal ‘in service’ current flows until an abnormal fault current instantaneously forces the device into a higher impedance state and in doing so allows time for the power system’s existing infrastructure the react to isolate the fault safely. Post-fault, the unit instantly recovers ready to protect the network again. As a passive device, it incurs negligible operating costs and maintenance while introducing minimal power losses – attributes prized by utilities.
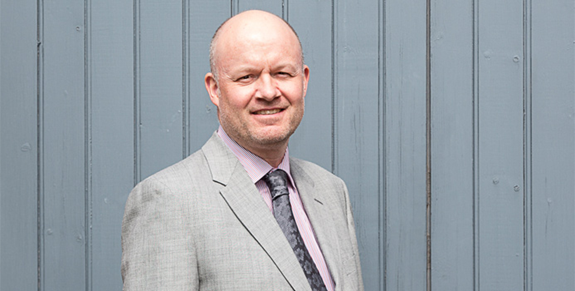
FaultCurrent was founded in 2012 as a business spin-out from ground-breaking research undertaken by Dr. Jeremy Hall at the Wolfson Centre for Magnetics at Cardiff University. Hall also holds a lectureship and research position at Cardiff University’s Wolfson Centre for Magnetics where he leads a team of graduate students working in the field of magnetic nanotubes, steel microstructures and composites.
The company’s mission is to develop fault current limiting technologies that will extend the fault carrying capacity of an existing power grid. Its research phase was completed in April 2013 with a combination of support from Cardiff University, venture capital firm Fusion IP/IP Group and the UK government.
Also, in 2013, the UK’s Department of Energy & Climate Change awarded the Company an Energy Entrepreneurs Fund grant in order to accelerate the development of a full-scale 11KV 20MVA prototype which was completed in 2016.
In May, Eriez Manufacturing stepped up its participation in the company to become the majority shareholder in FaultCurrent, bringing to the table financial backing as well as its considerable expertise in the manufacture of products that apply magnetic technologies. Eriez now provides the base for FaultCurrent in South Wales. In September, a rigorous re-engineering program was completed, culminating in the manufacture of the first 11kV 20MVA production unit that went on to be successfully tested.
“Making this investment in FaultCurrent was a natural choice for Eriez as we are constantly developing and investing in breakthrough products that keep us on the cutting edge,” commented Tim Shuttleworth, president and CEO of Eriez which is based in Ohio.
“The project attracted attention–and subsequently grants–from the Business, Energy & Industrial Strategy department of the UK government,” explained Andy Lewis, chairman of Eriez-Europe. “Eriez Investments Ltd. has a majority shareholding position, having cumulatively invested a seven-figure sum in the past two years, with the IP Group and FaultCurrent Ltd. company directors and former directors holding the remaining shares.” FaultCurrent Ltd.’s Board of Directors is comprised of Andy Lewis, Martin Ansell, Dr. Jeremy Hall and Andy Cheer.
Recognized as a world authority in separation technologies, Eriez manufactures a diverse line of industrial equipment for magnetic lift and separation, metal detection, fluid recycling, flotation, materials feeding, screening, conveying and process control. It designs, produces and markets these products through 12 international subsidiaries located on six continents.
Ansell says FaultCurrent’s momentum has significantly increased since Eriez recently became the majority shareholder. “We have been able to accelerate the completion of our development program and are now working to appoint a network of sales representatives.”
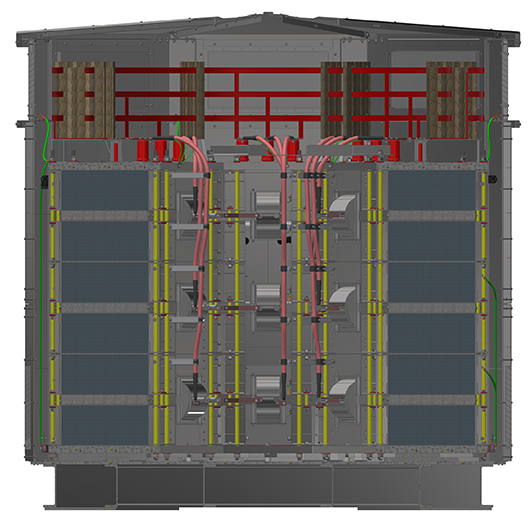
Inside the beast
Other companies have designed and built fault current limiters using different technical approaches ranging from the application of superconducting technologies to the introduction of power electronics.
FaultCurrent’s approach, however, was to design a truly “fit and forget” product that used simple permanent magnets at its core to provide a dependable, robust and energy efficient solution that is quick to install. It’s this core design element that result in a product with virtually no operating overhead and that requires no maintenance beyond simple inspection.
FaultCurrent has provided extensive design explanations in its product literature. A cross-sectional view shows its three layers of coils and ferrite magnets. Basically, It is constructed as a three-phase 11kV device that comprises 8 dry insulated, copper windings for each of the three phases wrapped around ferrite magnets. There are 24 windings in total. The magnets are arranged in a patented octagonal fashion to comprise each phase. The three phases are then placed on top of each other. The copper windings can be connected in various series and parallel combinations providing flexibility for creating different variants.
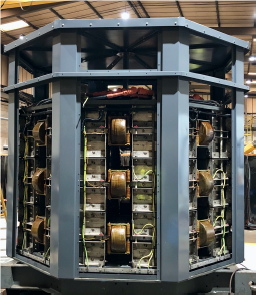
The overall dimensions of the unit are 3.5m x 3m x 3m. It weighs 57 tons in total, with the weight of the ceramic ferrite tiles accounting for 25 of the tons. It can act rapidly to increase its impedance in case of a fault, typically within less than 2msec, and can also reset very quickly following clearance of the fault, taking less than a millisecond to do so.
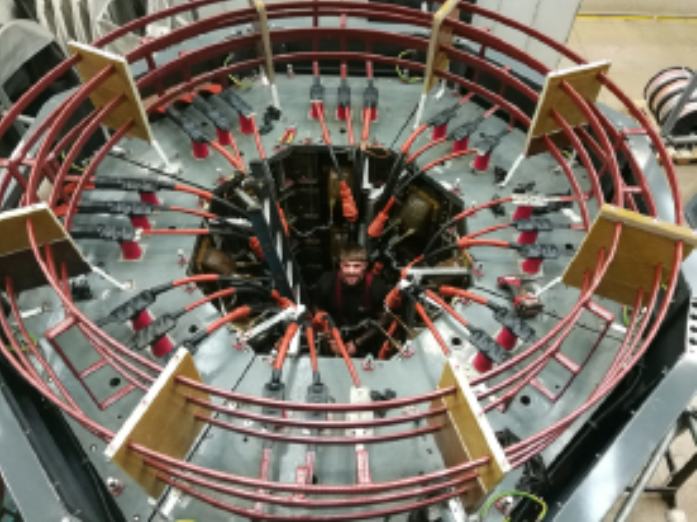
The device is protected by external cladding fitted with several louvers that allow for the natural ventilation and cooling. This is considered sufficient due to the dry type winding insulation using a combination of high temperature Polyimide and Glass Mica and the strategic distribution of the windings in its structure. The windings can withstand a steady-state temperature of 200 degrees Centigrade. The winding insulation is typical of the type used in large rotating machines and considered most suitable for the design of the distributed windings in it.
The most important feature of the pmFCL, emphasizes FaultCurrent, is its capability to prevent demagnetisation of the ferrite magnets during the flow of fault current by ensuring that peak field values in the AC windings do not exceed coercive field values in the vicinity of the magnets. Even in the unlikely event of demagnetisation of the permanent magnets, the pmFCL fails safely by adopting its higher impedance state.
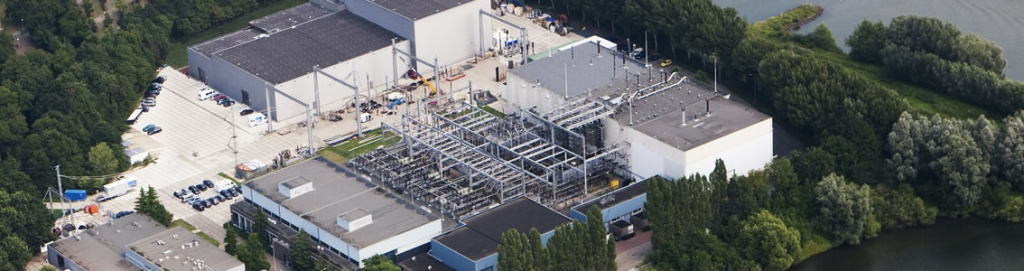
The KEMA High Power Laboratory in Arnhem is the world’s largest independent testing and certification laboratory for medium, high and ultra-high voltage transmission and distribution equipment. According to Bas Verhoeven, laboratory director, the pmFCL performed closely with the FEM (finite element method) magnetic design models. Having successfully completed its range of testing, it was issued a Performance Certificate. The pmFCL will be installed and network tested by a UK distribution network operator later in the year and will be used in extending the capacity of the power grid, said Verhoeven. “This development represents a new class of dry type fault current limiter with low maintenance, running and installation costs, being both easy to install and requiring no axillary power.”
For more info, see www.faultcurrentltd.com.