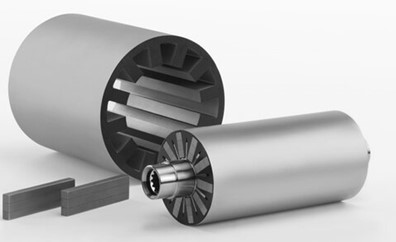
Since 2018, Vacuumschmelze GmbH & Co. (VAC) has been working with partners from industry, research institutes and universities on a project to improve the power density of electric motors for automotive and aircraft engines. Funded by the German Federal Ministry of Education and Research, the joint collaboration project achieved significant results including development by VAC of a new alloy with important attributes and a new process for making motor laminations.
Two components of the motors were considered, rare-earth permanent magnets and cobalt-iron laminations. The objective was to reduce the size, weight and losses of electric drive systems toward establishing more sustainable transportation systems.
VAC succeeded in achieving an energy density of 282 kJ/m3 in laboratory tests with the development of a new permanent magnet alloy based on samarium cobalt (SmCo). With this value, a new world record was achieved, reports the company. In addition, a first batch of the new alloy Vacomax 278 HR was produced under series production conditions with promising results. The alloy is in the production transition stage, and further steps have been taken to increase quality and output.
The magnets were installed by VAC in rotors that were further processed into electric motors by the project partner Maccon and are now being tested by the industrial partners Daimler AG and Lange Aviation. With a cobalt content of 49%, the new material proved to be the first choice for the demanding requirements in high-end automotive and aviation applications.
Also, a new joining technology for the laminations was developed. The individual lamellae with sheet thicknesses of 0.1 mm are joined in an established laser tying process. The novelty, however, is that the joint is created inside the stacks in a similar way to punch-packing and enables better cohesion. At the same time, the tying points can be significantly reduced compared to punching and significantly thinner sheets can be processed. This results in lamination stacks with a fill factor of up to 98% and minimal eddy current losses. In addition, the process is scalable and can be applied to large quantities. The combination of high-performance material and cost-optimized manufacturing process for large quantities makes it possible to reduce volume and weight and serve a larger market than before with high-performance, resource-saving products.
“The unique collaboration between research and industry has enabled us to develop a new alloy and manufacturing process in a very short time, both of which significantly increase the sustainability of transport systems,” says Dr. Matthias Katter, head of advanced research permanent magnets at VAC and coordinator of the project. “We are very excited to see the results of our partners with the demonstrators and, thanks to our unique vertical integration of manufacturing, we see ourselves well equipped to realize even complex system solutions on a large scale according to the individual specifications of our partners.” For more info, see www.vacuumschmelze.com.