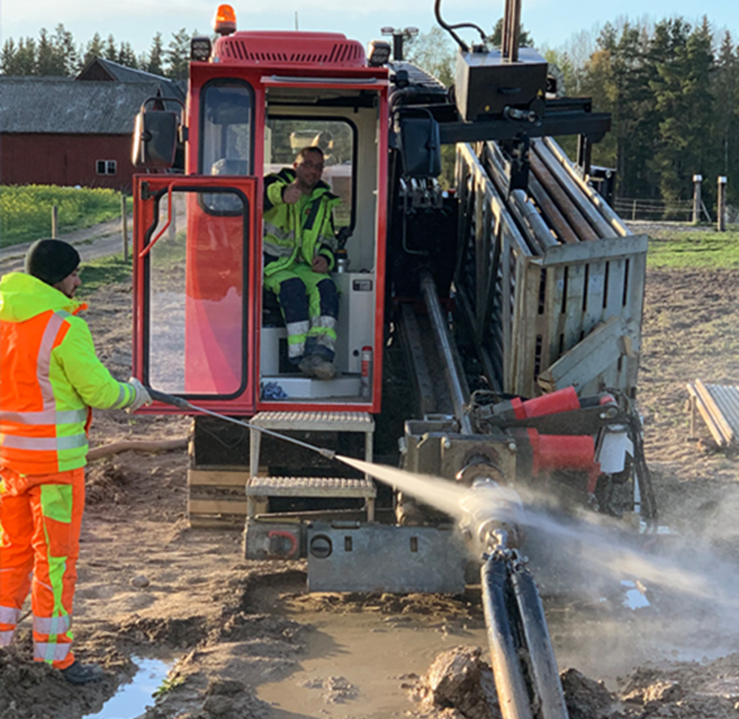
Using two core magnetic technologies to compete with the precision of optical encoders yet withstand intense mechanical vibration, automation manufacturer Wachendorff continues to see its WDGA line of absolute encoders put to the test by mobile equipment and industrial machinery designers. At the heart of this success are the company’s QuattroMag and EnDra technologies which enable the performance of a diverse array of robust equipment such as cranes, mobile work platforms and even horizontal drilling equipment, shown above.
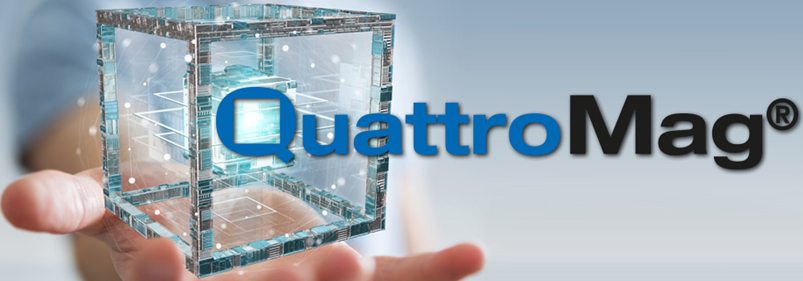
QuattroMag single-turn technology is based on four Hall sensors used together with a patented calculation algorithm which calculates the magnetic field generated by a diametrically split magnet mounted on the face of the encoder shaft in such a way that any interference between the Hall signals cancels each other out. It can measure angular position more accurately and quickly than conventional sensors in high-precision and dynamic applications which in the past were exclusively the province of optical systems.
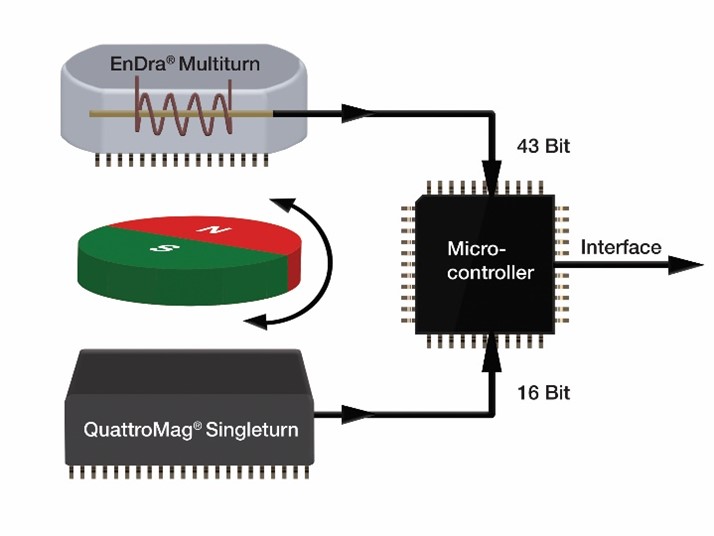
In addition, the multi-turn encoders are equipped with EnDra technology which counts and stores revolutions via a Wigand sensor, even when de-energized since it utilizes energy harvesting from the rotation. Here too, a patented process enables precise and reliable signal processing.
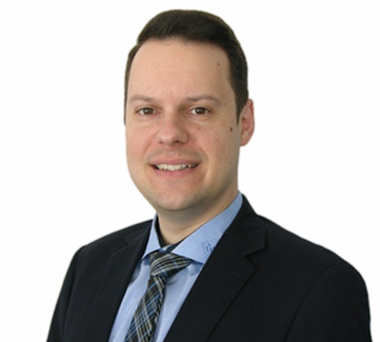
“In combination, these two technologies are almost unbeatable for mobile applications,” according to Steffen Negeli, product manager. “Because it is contactless and enclosed in housing, it’s wear-free and also has no moving parts such as gears, he explains. “Paired with the fact that the encoder doesn’t have a battery makes it completely maintenance-free. They work reliably and are temperature-resistant in ice or in the desert, and are available also in an offshore version able to withstand marine environments.”
EnDra multi-turn technology
EnDra stands for energy wire. A Wiegand wire consists of a hard magnetic sleeve and a soft magnetic core. If the field of the magnet moves along the Wiegand wire by rotating the shaft, the soft magnetic core is forced to follow the field, constrained by the hard magnetic sleeve.
An increasingly greater field difference is created in the wire, for example, when tensioning an arc. As soon as the external field reaches the coercive field strength of the sleeve, the sleeve is demagnetized, and the built-up voltage of the core suddenly jumps over. This pulse, which is independent of the speed, is generated twice per revolution and converted into electrical pulses using a coil. These pulses generate enough energy to operate a low energy FRAM memory and provide information on the number of revolutions.
Background – precise and reliable measurement in drives and mobile machines
For more than 40 years, Wachendorff has been offering sensors and automation products for mobile machines and industrial vehicles. Just over ten years ago, the company developed the series of absolute encoders that offer enormous advantages, not only over conventional encoders, but also over conventional sensors, such as potentiometers or simple angle sensors. These enhancements make the products ideal for use in outdoor applications, or in environments with high mechanical demands such as mobile work machines, even aircraft elevators.
As far as Wachendorff is concerned, only a magnetic solution is good enough to meet both fundamental requirements, single-turn to determine the number of steps and multi-turn for the revolution counter. The WDGA encoders are considerably less sensitive to vibrations which constantly occur in machines and systems than in the case with optical absolute encoders with a drive unit. Despite their compact design, the WDGA encoders outperform optical systems with drive technology by a high factor, the company says.
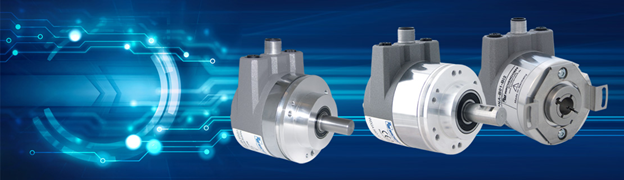
“We have three products with different mechanical adaptions that use all benefits out of these technologies,” explains Negeli. “All are with industrial Ethernet protocols and the Universal IE product is unique, as the customer can choose which protocol the encoder uses at his end.” The 58F model is the most compact Universal IE encoder worldwide, says the company.
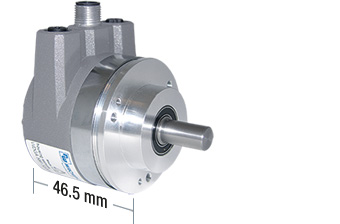
The applications have become quite diverse. In combination with a pulley system, absolute encoders can be used for measuring the travel of a boom or the reach of a truck crane arm; directly on the winch, without a cable system, they can be used for length measurement. Other applications include angle measurement in wind turbines, mounted on the gear ring or directly in the cam switch. Other applications include the feed measurement on vertical drilling machines, as well as the measurement of steering information such as angle and speed on the wheels of automated guided vehicles or heavy transporters. Angle measurement on cranes is a special application, as two encoders can be used here for redundant information, or the measurement can be supplemented further with a proximity switch.
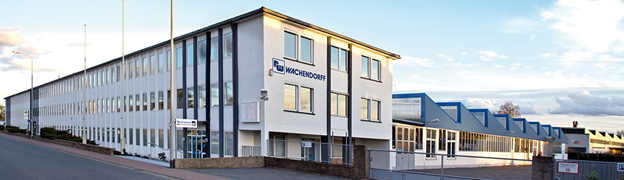
Based in Geisenheim, Germany near Wiesbaden, Wachendorff develops and manufactures rotary encoders, engine feedback devices and complete measuring systems for use in a wide range of serial production applications for mechanical and plant engineering. In March 2020, the company introduced its WDGR family of redundant incremental encoders that incorporate both optical and magnetic technology, which were featured in an earlier article in Magnetics Magazine. For more info, see www.wachendorff.com.