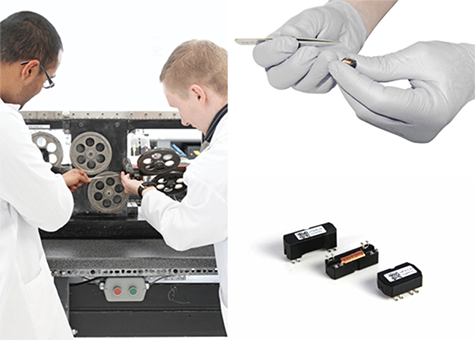
Capitalizing on a booming business for its ferromagnetic Wiegand wire that harnesses magnetic energy for energy harvesting, Posital is developing a line of modular magnetic encoders for motor and robotic manufacturers that it says will be the smallest in the world. Other products using the specially processed wire are coming into the market, too, including new hollow shaft encoders for motors that employ a new configuration for the magnets. Shown above is Wiegand wire being processed at the company’s technology center in Aachen, Germany and the sensors.
Size matters and in the world of industrial automation providing exceptional performance in a highly compact package can be an enormous advantage. With a diameter of only 22 mm and a height of 23 mm (0.87” by 0.9”), the new device is the world’s smallest multi-turn kit, or module, for motor feedback, says Posital. It is designed for integration into servomotors, feedback-controlled stepper motors, microdrives, miniature robots and other machines that require high-precision position feedback and where space is at a premium.
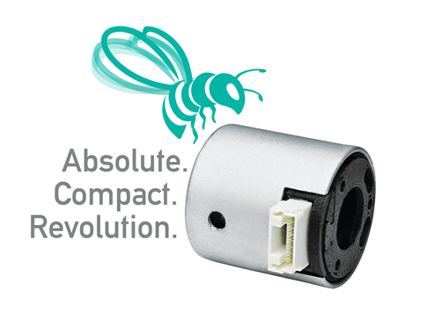
Lately, the company has been previewing a fully functional prototype of the device, shown above, at automation shows worldwide and testing the product with OEMs, aiming for full rollout in mid-2020. Employing the company’s Wiegand wire, it features a self-powered rotation counter that does away with the need for backup batteries or complex gear systems. Posital showcased it at automation fair SPS held in Nuremberg in November and again at the IREX robotics show in Tokyo in December.
“Our new mini kits build on the success of the kit encoders that we introduced in 2016,” said Jim Stevens, product manager kit encoders at Posital North America. “By careful redesign and the introduction of smaller electronic components, we have been able to reduce the diameter of these devices from 36 mm to 22 mm.” A key improvement has been the miniaturization of the Wiegand energy harvesting system that powers the rotation counter.
“In the coming months, we’ll give our 22mm kit the finishing touch in a detailed beta testing program involving well-known motor manufacturers,” said Stevens. Full product roll-out will take place after evaluation of these test runs and is expected in mid-2020. Special shaft versions of the 22 mm kits with integrated bearings, which can provide additional applications, are also planned.
Wiegand growth machine
The Wiegand wire business has been a major growth machine for Posital in recent years and the company is poised to build it even further for the future. A manufacturer of industrial position sensors used in motion control and safety systems, Posital has been the world’s dominant supplier of Wiegand wire and products since 2014 when it developed its first Wiegand sensor design.
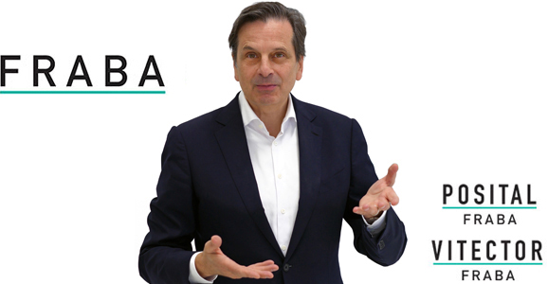
There are more than 500,000 of its Wiegand devices in use worldwide, according to Christian Leeser, CEO of parent company Fraba which is based in The Netherlands. Its two main product operations are Posital and Vitector, a manufacturer of safety technology for industrial doors. Posital makes use of the technology in its self-powered rotation counters for multi-turn encoders. It also supplies Wiegand modules, packaged as surface-mountable devices, to manufacturers of gas and water meters seeking to eliminate the need for external power or batteries.
From use in keycards and tokens, to pulse generators and servo motor applications, the performance and quality of the Wiegand technology has been continually improved, he notes. Posital recently upgraded its facilities for producing the sensors. Production capacity was doubled to 1 million units per year and the company has material secured for the next 10 million sensors.
“Our future success will be supported by our Aachen-based R&D center, which is making significant progress in the development of innovative signal processing algorithms for our magnetic encoder products and improved performance from our Wiegand wire energy harvesting technologies,” said Leeser. The company typically invests about 10% of revenues into research and development each year with about 40 researchers and developers on board.
A key part of Fraba’s DNA has been avoidance of ‘me too’ products and the consistent emphasis on new and innovative solutions, notes Leeser. “We stand for fresh ideas and ingenuity that bring tangible benefits to our customers. This is the significance of the work done by our R&D teams. For example, their patient, step-by-step work has enabled us to consistently improve the amount of energy harvested via the ‘magical’ Wiegand effect.”
“Over the past 15 years, Fraba has established itself as a trendsetter, leading the transition from complex optical encoders to robust and less expensive precision magnetic encoders. These products are offered in both stand-alone versions and as integrated motor feedback kits.”
Another recent product introduction employing the Wiegand wire is the company’s new line of Hollow Shaft Kit encoders. In November, Posital announced that they have been selected as a complementary product in Rockwell Automation’s PartnerNetwork Encompass program.
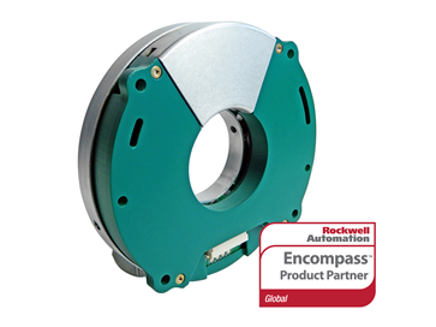
Using capacitive technology, they mark a significant innovation for industrial motion control, according to Posital. Until now, almost all through- or hollow-shaft encoders have been limited to a single-turn measurement range, largely because fully satisfactory multi-turn technology has been not been available. Employing the company’s Wiegand energy harvesting system, these encoders feature an integrated rotation counter that records each revolution the instrument experiences, even if these occur when no external power is available.
They are especially well suited to robots and cobots. Weighing in at just 110 g, with an outer diameter of 80 mm, they can be integrated directly into the joints of the robot arms. Their open-center form factor leaves room for designers to route mechanical components, cables, pneumatic or hydraulic lines through the center of the joint.
While Posital earlier championed the switch from optical to magnetic measurement technologies in encoders, the new Hollow Shaft series represents a deliberate break with the past. Magnetic systems typically require that key components be placed on the centerline of the device, making it difficult to adapt to hollow center configurations. The capacitive measurement technique enables a ring-shaped configuration.
At the heart of the multi-turn system is Wiegand energy harvesting technology. To accommodate the open-center layout, a new arrangement for the magnets on the rotor and Wiegand wire assembly had to be developed. Through experimentation and extensive magnetic field simulation, a reliable solution was developed that included four diametrical-oriented magnets placed evenly around the rotor. These four magnets provide a stable magnetic field that triggers polarity reversals in the Wiegand sensor installed in the stator.
With each 360-degree rotation of the rotor, the Wiegand assembly generates a current pulse that energizes the counting electronics. This counter has a 43-bit memory for a measurement range of almost nine trillion revolutions. “These are values that put us right on trend for our target market,” says Leeser.
Wiegand effect technology
Wiegand sensors can be used as a pulse generator in multiple applications. The sensor needs no external power source and has no moving parts. The Wiegand effect technology employs the unique magnetic property of specially processed, small ferromagnetic wire. John Wiegand discovered a way to cause the magnetic field of this specially processed wire to suddenly reverse, generating a sharp uniform voltage pulse which can be used as a power source.
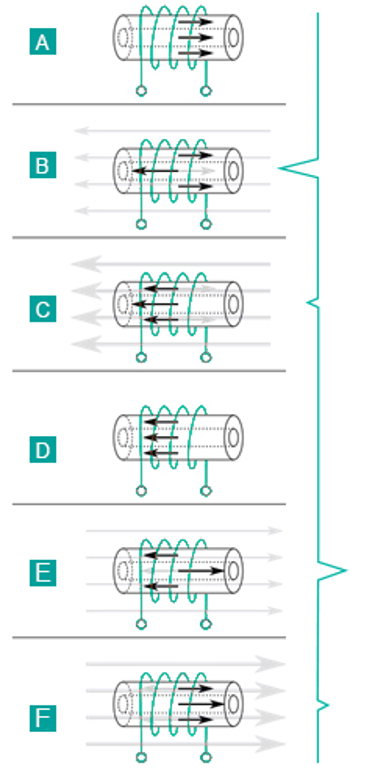
A to B: Applying a reverse field switches the core’s polarity, producing a large voltage spike.
B to C: As the reverse field continues to increase, the shell eventually switches polarity, giving rise to a smaller pulse in the same direction.
C to D: After saturating the Wiegand wire the reverse field is withdrawn.
D to E: Applying a magnetic field with the original polarity of the wire switches the core once again generating a large pulse in the opposite direction.
E to F: Increase of the eternal field will also switch shell polarity. The wire is back in the original state and a full cycle completed.
Wikipedia provides this description: Wiegand wire is low-carbon Vicalloy, a ferromagnetic alloy of cobalt, iron, and vanadium. Initially, the wire is fully annealed. In this state the alloy is “soft” in the magnetic sense; that is, it is attracted to magnets and so magnetic field lines will divert preferentially into the metal, but the metal retains only a very small residual field when the external field is removed.
During manufacture, to give the wire its unique magnetic properties, it is subjected to a series of twisting and untwisting operations to cold-work the outside shell of the wire while retaining a soft core within the wire, and then the wire is aged. The result is that the magnetic coercivity of the outside shell is much larger than that of the inner core. This high coercivity outer shell will retain an external magnetic field even when the field’s original source is removed.
The wire now exhibits a very large magnetic hysteresis: If a magnet is brought near the wire, the high coercivity outer shell excludes the magnetic field from the inner soft core until the magnetic threshold is reached, whereupon the entire wire — both the outer shell and inner core — rapidly switches magnetisation polarity. This switchover occurs in a few microseconds, and is called the Wiegand effect.
The value of the Wiegand effect is that the switchover speed is sufficiently fast that a significant voltage can be output from a coil using a Wiegand-wire core. Because the voltage induced by a changing magnetic field is proportional to the rate of change of the field, a Wiegand-wire core can increase the output voltage of a magnetic field sensor by several orders of magnitude as compared to a similar coil with a non-Wiegand core. This higher voltage can easily be detected electronically, and when combined with the high repeatability threshold of the magnetic field switching, making the Wiegand effect useful for positional sensors.
Once the Wiegand wire has flipped magnetization, it will retain that magnetization until flipped in the other direction. Sensors and mechanisms that use the Wiegand effect must take this retention into account.
For more info, see www.posital.com and www.wikipedia.org.