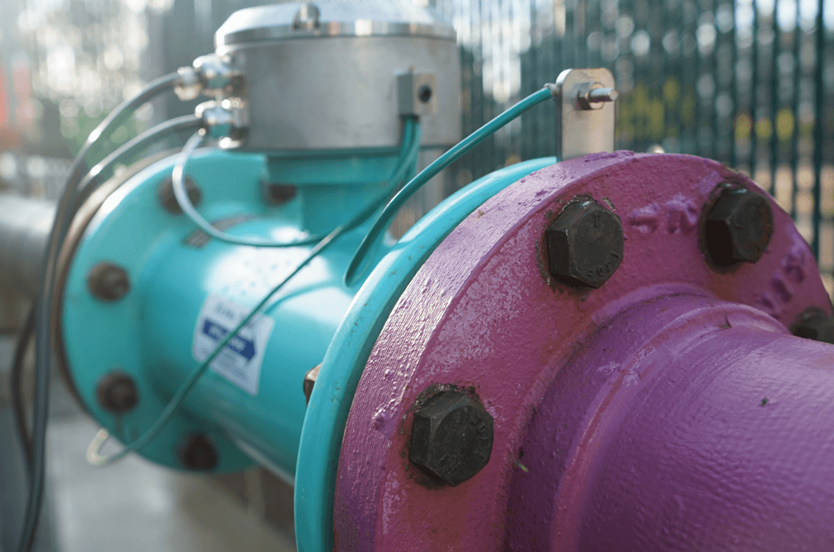
Magnetic flow meters can have an Achilles heel in their design but engineers at McCrometer have sealed the deal through careful manufacturing techniques and the use of fusion-bonded epoxy to prevent contamination with drinking water, wastewater and industrial streams which the instruments are measuring. The company received new NSF certifications for its Ultra Mag and Dura Mag electromagnetic flow meters recently, marking further testament to the robustness of the materials and manufacturing process, as well as the integrity of its quality team.
“The fusion-bonded epoxy is a major component of why these mag meters meet NSF standards,” explained Memphis Huff V, product manager for the magmeter product line and quality lead for McCrometer. “It has a lifetime guarantee that the epoxy will prevent liquid from reaching non-stainless components, rubber seals, polyurethane, and more in the meter body. The mag meters’ NSF certification is really due to the power of the epoxy!” The flow meters are approved for potable water applications, food and beverage applications, water treatment centers, and even applications for crop irrigation or livestock watering.
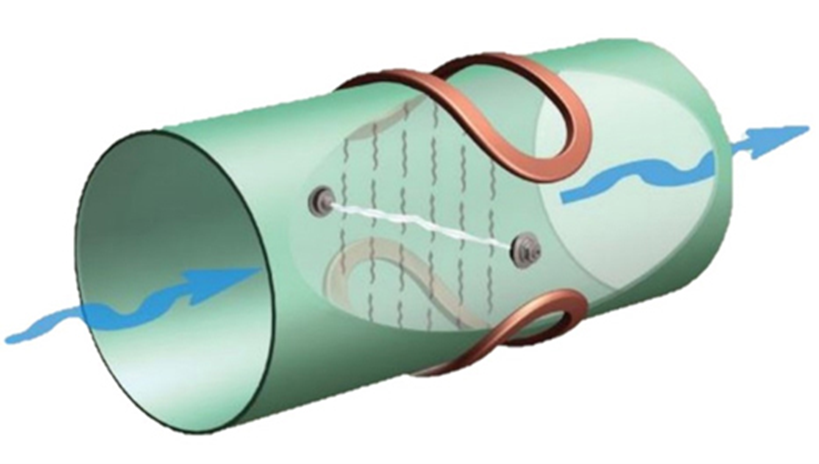
Electromagnetic flow meters can be highly accurate for measuring stream flow and is typically applied in full-bore or insertion style devices. Called magmeters, they operate on the principle of Faraday’s Law. This principle basically states that as a conductor, such as water, moves through a magnetic field it produces an electrical signal. Full-bore magmeters use an electromagnet mounted on the outside of the pipe, perpendicular to the flow direction. As flow passes through the magnetic field, electrically charged ions accumulate, with negative ions on one side and positive on the other. The resulting change in voltage is directly proportional to the velocity of the fluid passing through the pipe, which can be converted to volume. Insertion magmeters operate a little differently. For an insertion meter, a very small, localized magnetic field is inserted into the pipe. Electrodes cause charge bearers to separate. With a full-profile insertion meter, electrodes are located along the entire cross-section of flow to measure average velocity across the pipe centerline.
Magmeters can bear an ‘Achilles’ heel’ in their design, however, known as a liner. Liners, frequently featured in the full-bore style of mag meter, protect the meter body from the flow media. In municipal applications, liners may also contribute to a meter’s compliance with drinking water regulations. Liners can be prone to problems such as tearing, delamination or separation from the meter body, and perforation from flow debris such as rocks or even harsh chemicals causing corrosion.
McCrometer’s solution to this common flow problem? A proprietary fusion-bonded epoxy to make its UltraLiner. The coating is comprised of materials engineered by 3M and applied in a meticulous process to many of the mag meters produced by the company. The lining carries a lifetime guarantee against delamination and tearing.
The protective layer between the metallic body and the conductive liquid flowing through it is designed to insulate a magmeter against short-circuiting. Where separately installed liner inserts are used to provide that protection, deterioration of those liners can be one of the biggest complaints about full-bore mag meter performance. According to McCrometer, the most durable magmeter coating is one that is not simply layered on the inside of the tube, but completely envelopes the entire assembly with thermoset powder coating epoxy. This bonding process provides complete, continuous coverage, enveloping the entire interior and exterior surface of the mag meter housing with uninterrupted protection. It provides excellent adhesion to resist corrosive soils, hydrocarbons, harsh chemicals, even sea water.
This type of coating has demonstrated its durability in the field by standing up to flows that include sand, rust, or harsh chemicals in the water without cracking, peeling, or falling off. If those problems occur, particles of the liner can get into the process flow and the mag meters can produce grossly inaccurate readings.
The company’s mag meters with the UltraLiner have been installed in a variety of flow applications where performance is crucial. In agriculture, the Dura Mag and the Mc Mag models measure harsh flow media for applications such as chemigation and fertigation, as well as dairy effluent, all of which require resistance to corrosion. In the municipal industry, customers use the company’s FPI Mag and Ultra Mag meters as retrofits after experiencing liners delaminating and damaging a nearby pump or causing a blockage. Both issues can be costly to remedy, especially if the metering location is buried in a vault or the blockage isn’t easily accessible. The signal that mag meters produce can go haywire and users will receive inaccurate readings, interfering with decision-making and daily operations.
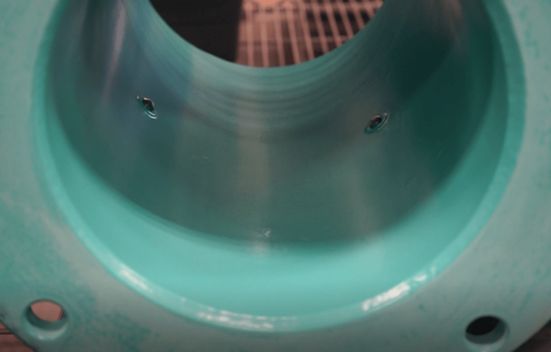
In industrial applications, shutting down an operation produces massive inefficiencies and expenses, and possibly regulatory issues if a liner tears in a food and beverage factory. For segments such as pulp and paper or automotive, harsh chemicals can corrode flow meters if the liner cannot maintain its integrity.
McCrometer’s factory process for manufacturing the UltraLiner is a critical contributor to its performance. To coat the flow meters with the epoxy, critical areas are masked, and the meter is blasted to remove any foreign particulates. Then, the meter is hoisted down into a fluidized bed dip tank where powdered coating is applied, bonding the epoxy onto the meter body or sensor. Post-dip, the meter is visually inspected for quality assurance, sanded down for an even coating, and then baked in an oven to finish. The result is a more durable alternative to rubber or plastic liners, says the company. The process can also be applied to insertion and propeller mag meters.
Based in Hemet in southern California, McCrometer is a global flow instrument specialist. Now a subsidiary of Danaher Corporation, it has been supplying flow measurement products for more than 60 years.