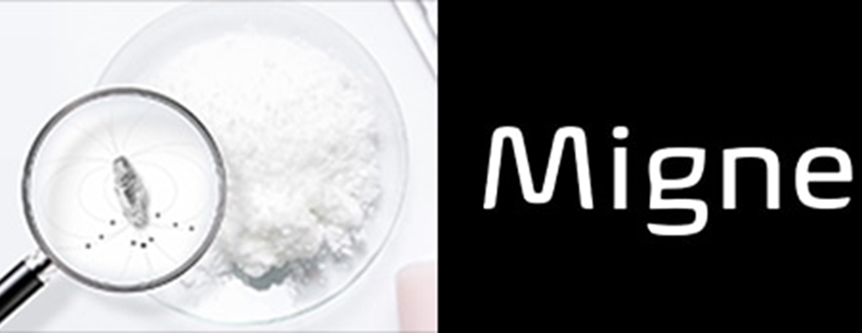
Preventing contamination by microscopic debris is a vexing matter for manufacturers of pharmaceuticals, cosmetics and industrial chemicals. Even the tiniest speck of debris can trigger serious consequences in our everyday lives. A microscopic contaminant, for example, in the ingredients of a smartphone’s lithium-ion battery can cause capacity degradation, heat generation, even ignition.
Attendees at Electronica 2022 held in November in Munich were able to see a new solution for factories that have been utilizing a plethora of inspection methods and sensors to remove miniscule debris invisible to the human eye. TDK has newly developed a highly sensitive, compact magnetic sensor capable of detecting metal fragments smaller than 0.1 mm by applying spintronic technologies it has amassed in the manufacturing of hard disk drive heads.
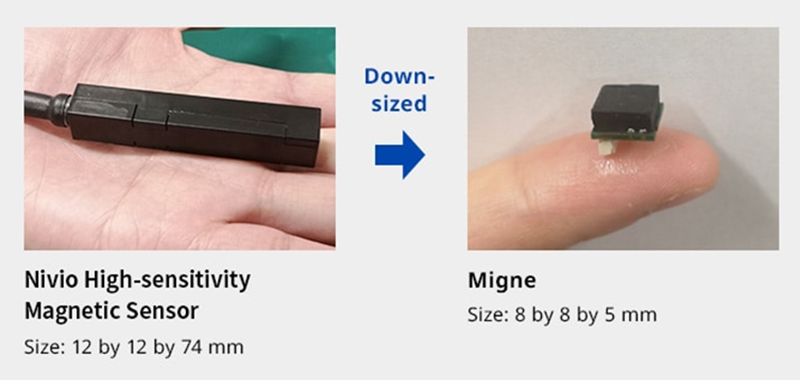
The Migne xMR sensor is an xMR-type magnetic sensor based on the company’s Nivio magnetic sensor. With an improved signal-to-noise ratio in micromagnetic fields compared to Nivio, its size is a mere 8 by 8 by 5 mm—small and thin enough to sit on a fingertip. An xMR sensor is a magnetic sensor designed to measure the strength of a magnetic field using magnetoresistance, an effect where changes to electrical resistance occur depending on the magnetic field.
In today’s manufacturing environment, there is a growing demand for the ability to detect iron and stainless-steel particles smaller than 200 µm (0.2 mm). Because non-magnetic metals like aluminum and copper are viscous and tend not to become fine particles, external contamination can be prevented by raising the cleanliness of factories. Iron and stainless steel, however, are difficult to eliminate as they are used as materials in production equipment which inevitably generates fine particles. Mainstream X-ray inspection is generally limited to several hundred µm in detectable debris size, giving rise to a need for the ability to detect smaller debris.
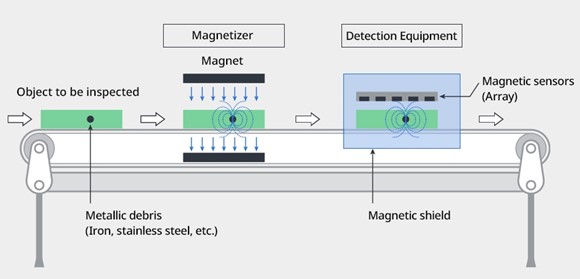
Fine metal powders of iron and stainless steel are generated from the wear and peeling in manufacturing equipment, contaminating the object to be inspected. Applying Migne, the inspection system uses a powerful magnet to magnetize the entire object. Metal sensors then detect the magnetism emitted by the metallic debris. The magnetized metallic particles become tiny magnets with N and S poles. When scanned by the Migne xMR sensor, the outward and inward magnetic field lines are displayed in red and blue, making the magnetized metallic debris detectable.
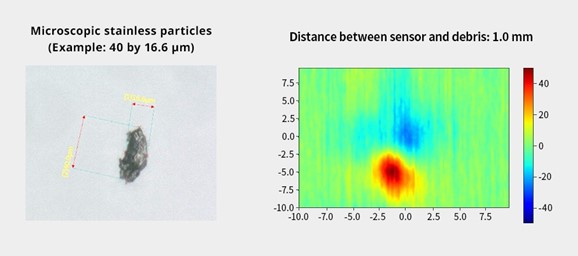
The sensor can detect foreign object debris over a wider area by arranging the compact sensor in an array. It can be applied to other applications requiring the detection of micromagnetic fields, not just debris inspection. These include prospective uses in nondestructive testing and in magnetic particle imaging for medical and bioscience diagnostics.
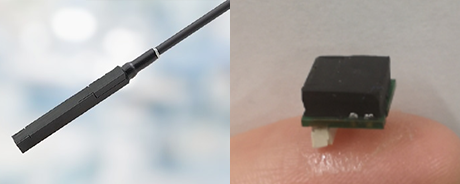
Development of its magnetoresistive technology arose from TDK’s engagement in the manufacture of magnetic heads for hard disk drives. The Nivio MR sensor (left) and Migne MR sensor (right) can detect magnetic fields even much weaker than geomagnetism, providing highly sensitive magnetic resolution and ultra-low noise.
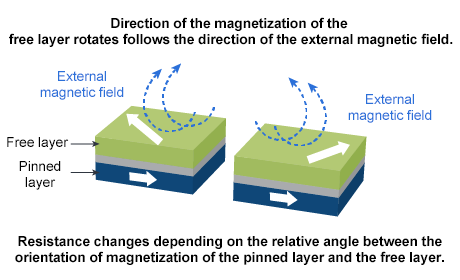
They are thin-film devices with a multilayer structure manufactured using a process similar to that used for semiconductor devices. Inherent noise from the sensor element and associated circuitry is kept to a minimum, resulting in a drastic signal-to-noise ratio improvement with extremely high magnetic resolution and ultra-low noise characteristics. For more info, see www.tdk.com.