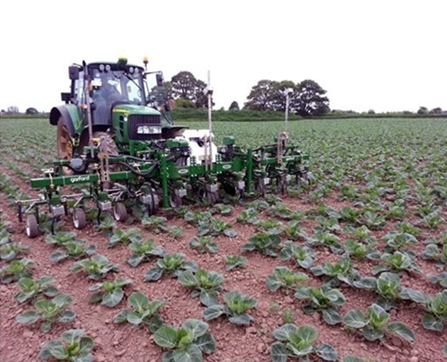
November is Magnetic Sensing Month at Magnetics Magazine!
Stay tuned and check the website frequently for new updates on the latest technology for magnetic sensing.
As part of the many sensor technologies now widely employed in smart farming, where sophisticated monitoring and control is now universally applied to optimize crop production, mobile agricultural machinery manufacturers are increasingly utilizing precision sensors as part of the equipment and systems they produce to till, seed and harvest crops. Magnetic sensors are fielding many of the challenges.
Variohm EuroSensor, a sensor manufacturer and distributor of sensor components, has undertaken a number of applications with UK and European farm machinery manufacturers for position, load, pressure and temperature sensors with almost all of them installed in harsh outdoor environments where large temperature extremes as well as severe shock and vibration conditions exist, and upmost reliability is essential. Applications range from angle sensors in sophisticated four-wheel steering systems that allow farm machinery to precisely maneuver in tight spaces for maximum crop yields to linear position and load sensors that are part of advanced mobile autonomous vehicles linked to the Global Navigation Satellite System for vehicle guidance and load weight measurement.
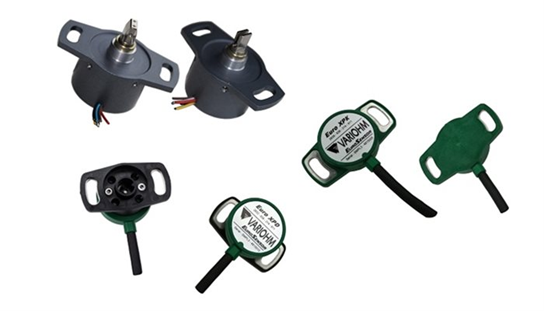
These various types of sensors serve numerous measurement tasks. Some are configured open loop with the position or load information simply fed to a visual display to allow manual operation of a process. Other automated and autonomous machine tasks involve the sensing component as part of closed loop systems where often multiple functions are synchronized, for instance with vision systems and linear motion positioners or rotary actuators for tasks such as in-row weeding or selective crop harvesting. Some are potentiometric based sensors that involve physical contact but many employ non-contact magnetic technology or magnetic sensing with a degree of contact involved.
For rotary angle sensing, Variohm employs two Hall Effect technologies where there is no contact between a fixed sensing element and a rotating magnet. While their way of sensing is similar, one type is in an enclosed assembly complete with bearings so there is a degree of contact involved. The other is touchless where the sensor and magnet are supplied as separate components and mounted by the customer between the fixed and rotating components.
Based in Towcester, UK, the company manufactures a range of Hall Effect angle sensors that are well suited to agricultural applications. Three mechanical design formats with encapsulated sensor electronics form the Euro-XP, XPD and XPK series. The third version, the Euro XPK, is a two-part puck-and-magnet contactless design.
Its extensive range of angle sensors also covers non-contacting sensor technologies with multi-turn capability so that, if attached to ballscrew or leadscrews for instance, they can be calibrated to measure travel length.
For linear position measurement based on non-contacting measurement principles, magnetorestrictive technology and variations that offer added reliability are available. As separate two-part rod and sensor components, they are assembled inside hydraulic cylinders for position feedback or mounted alongside multiple cylinders typically for telescopic boom control. They are also available as especially robust housed components where a linear support bearing is used.
As wear and working life are important aspects of agricultural and many other mobile machinery applications, the sensors that necessitate contact between sensing elements find less favor than non-contacting and touchless sensors. In terms of robustness, where the separate sensor and magnets can be epoxy-potted and effectively protected from air and liquid ingress, these technologies find favor for the most arduous tasks.
For medium precision linear position sensing, especially for long distance measurement, the cable extension sensor combines a rotary sensor on a cable winding drum and a spring-assisted winch mechanism. As the cable extends from the drum it rotates the shaft driving the internal rotary sensor. The sensor technology used in the cable extension sensor can be potentiometric, sometimes called a string pot sensor, or incremental or absolute encoder. For more info, see www.variohm.com.