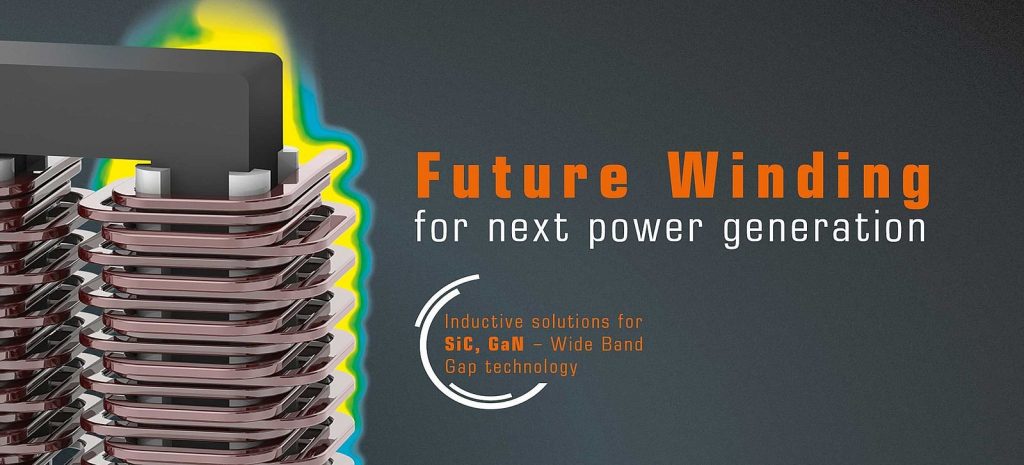
BLOCK, one of the world’s leading manufacturers of transformers, power supplies, reactors and EMC filters, has developed a new platform called Future Winding technology designed to take performance optimization of inductive winding products into a new dimension.
“The extraordinary variability in the design of the winding structure comes with a number of benefits for winding products” according to Wolfgang Niedrist, general manager of the BLOCK USA Group. “Optimal cooling by maximizing the heat-emitting conductor surface while also creating cooling ducts via the winding structure and minimal proximity losses with rising switching frequencies are just some of the strengths of this state-of-the-art technology.”
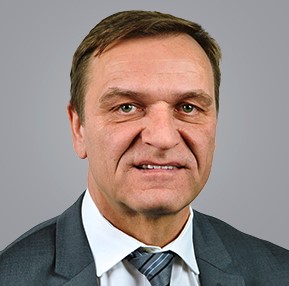
The combination of increased conductor surface, spread of the winding, and cooling ducts created via the winding structure enables optimal cooling of the entire product. The new technology shows off its strengths with forced air cooling, particularly taking the performance optimization of inductive winding products into a new dimension, says the company.
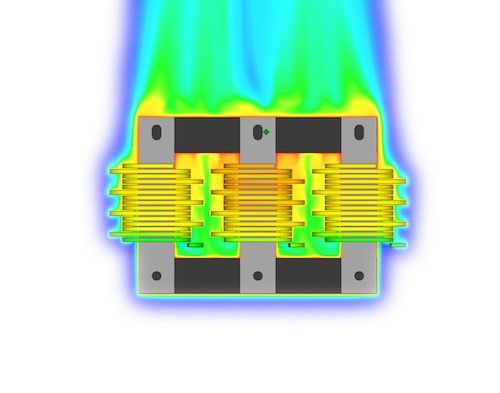
Long life is enhanced, also. “Thanks to the new Future Winding technology high inductivity can be realized with a single-layer winding structure,” explains Niedrist. “The benefit is that additional layer insulation and, possibly, even basic insulation to the core is not needed. Aging effects in the insulation materials – as are typical with the conventional structure of inductive winding products – no longer occur which maximizes service life.”
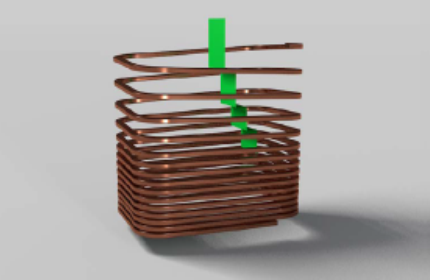
An important result of the new technology is that varying the conductor spacing in the winding structure effectively reduces proximity losses in the conductor that are generated by ripple currents from switching frequencies, particularly as frequency increases. This effect is significant especially for future applications of SiC- and GaN-based semiconductor technologies. It also represents a potentially cost-effective alternative to the use of expensive high frequency Litz wires in conventional winding technologies.
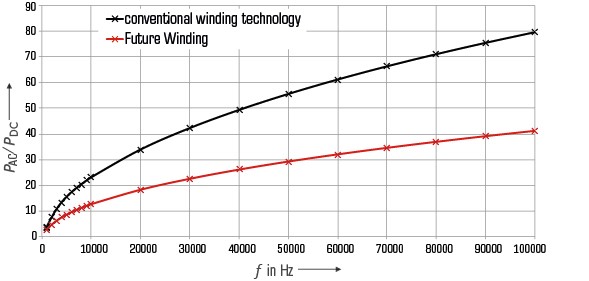
BLOCK officials gave this overview of other key features and advancements. Potential control is another area of improvement. The specific winding structure results in more or fewer parasitic capitances and, therefore, in the case of transient over-voltages, differences in potential between the individual turns. This can damage the conductor insulation, potentially leading to a winding short. Future Winding variably controls such parasitic captiance – and, thus, the potential across the winding- through the partial spreading of individual winding sections. This prevents damage to the conductor insulation and accordingly any winding shorts.
Due to the variable configurability of its winding structure, the new technology can adapt accurately to the core geometry and prevailing flow conditions of the air cooling system.
High current density is also achieved. Due to the flexible design of the winding structure a maximum of the conductor’s heat-emitting surface is exposed to the prevailing cool air flow. The result is a high current density and efficient use of the conductive material (CU or AL), reducing structural volume, weight and costs.
Potential cost-reduction of inductive winding products comes into play as well. Due to the optimized cooling effect on the conductor, significantly affordable and lighter aluminum can be used instead of copper as the conductive material. This also does away with costly insulation materials and the corresponding production steps to install this insulation. Windings are produced in a fully automated process on in-house designed winding machines that are in line with Industry 4.0. Combined with the new innovative connection concept, the result is a self-supporting winding structure.
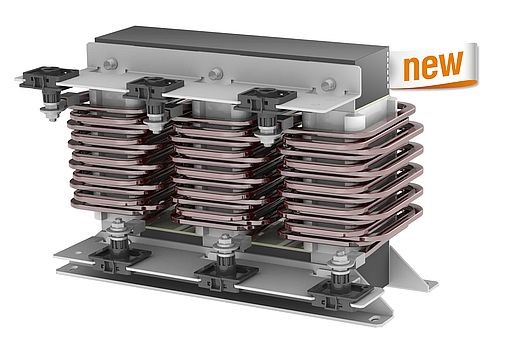
BLOCK has introduced several new Future Winding products and more are in development. For more information, see www.blockusa.com.