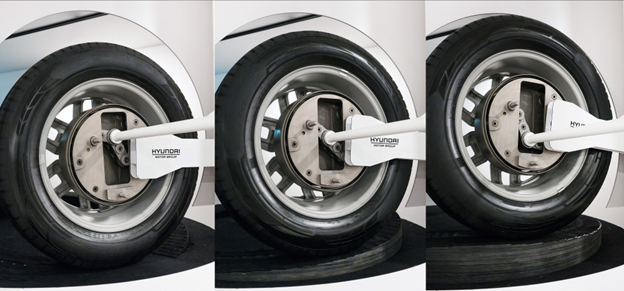
Hyundai and Kia, both brands of Hyundai Motor Group, unveiled their new universal wheel drive system for electric vehicles in Korea in November amidst the group’s dramatic surge in expansion of EV manufacturing capability. Uni Wheel is a functionally integrated wheel drive system that dramatically improves available space inside an EV by moving the main drive system components to the vacant space within the wheel hub.
In doing so, the automakers have designed a completely new structure for the drive system that uses permanent-magnet in-wheel motors smaller than possible previously. The motors currently being used for the Uni Wheel are 120kW/220Nm.
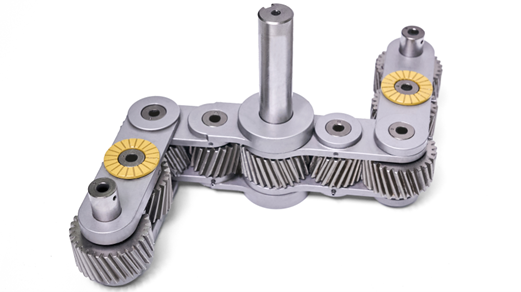
In internal combustion engine vehicles, power is transmitted from the engine through the transmission and to the wheels via drive shafts and constant velocity joints. In EVs, however, the engine and transmission are replaced by a motor and reduction gear, but the final method of transmission to the wheels is the same. Uni Wheel opens new possibilities and enables a flat-floor configuration by moving the reduction gear inside the wheel hub, locating a compact individual motor close to each wheel, reducing the length of the drive shafts. The system frees up significantly more interior space compared with conventional drive systems, enabling future mobility products optimized for various applications.
“We are pleased to showcase innovative ideas that could become game changers in the future mobility market,” said Jongsool Park, senior fellow at the Institute of Advanced Technology Development of Hyundai Motor Group. Uni Wheel uses a special planetary gear configuration consisting of a sun gear in the center, four pinion gears on each side and a ring gear surrounding this arrangement. Power generated by the motor is transmitted to the sun gear, which in turn engages the pinion gears to rotate the ring gear. This is connected to the wheel to drive the vehicle.
The pinion gears are connected to each other to form two linkages, and this multi-link mechanism enables Uni Wheel’s multi-axis movement to allow a wide range of suspension articulation.
A conventional drive system using a regular CV joint suffers from a decrease in efficiency and durability as the angle of drive shaft deflection increases when travelling over bumpy, undulating surfaces. Uni Wheel can transmit power with almost no change to efficiency regardless of wheel movement.
By moving the reduction gear to the wheel hub, a high reduction ratio delivers a significant torque output and allows for a more compact electric motor. With independent control of up to four efficient electric drive units, the system also allows for improved torque vectoring to boost dynamic ability and deliver high levels of steering and driving stability.
In addition to vehicles of various sizes, the system can also be applied to other types of mobility devices such as wheelchairs, bicycles and delivery robots. It can be scaled to work with wheel sizes as small as
4 inches and as large as 25 inches or more. Its ability to move the rotation axis of the wheel makes it possible to create forms of personal mobility that can climb stairs as smoothly as an escalator.
Immense building boom chases advanced EV design and production
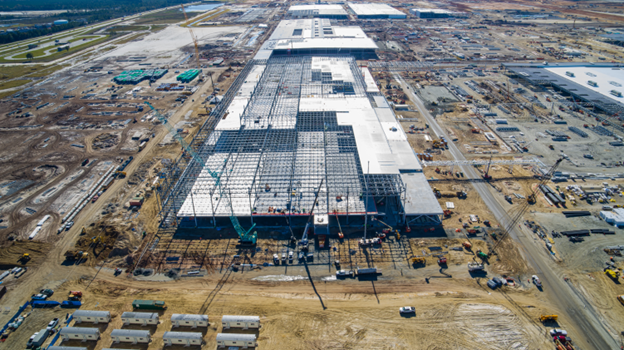
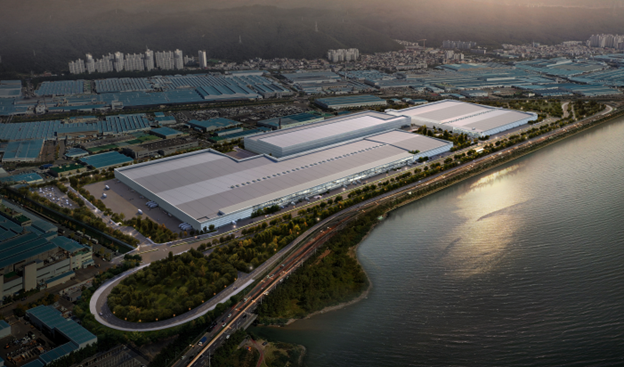
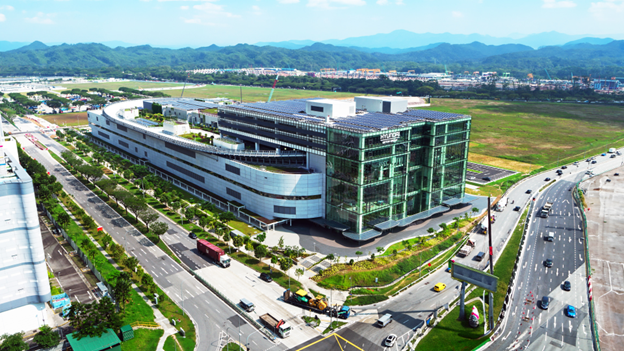