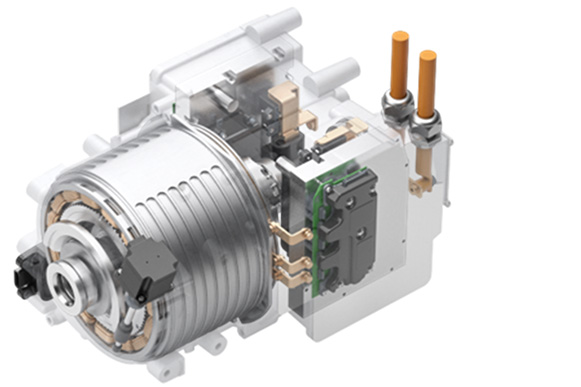
An oil-cooled e-motor designed for optimizing maximum power in electric vehicles has been developed by automotive supplier FEV. Based on centrifugal cooling, the oil flows under the rotor core and magnets onto the copper windings and can increase the continuous output of the motor by up to 50 percent, says the company. It has been presenting the concept system at various automotive technical events.
Conventional e-motors can only briefly call up their maximum power during operation as this results in high thermal stress, the company notes, but its special cooling solution is designed to counteract this limitation. While water as a coolant cannot be used for cooling directly at the copper windings in the e-motor due to its conductivity, FEV uses a special non-conductive oil which is also used as a lubricant in the motor.
Within the system, the oil is guided by centrifugal force via the shaft to the heat-conducting copper windings during motor operation to cool them efficiently. This allows the power density of the motor to be significantly improved and the increased torque to be called up for a longer duration. Alternatively, cooling allows the engine to be downsized while maintaining the same power density, resulting in installation space advantages in the vehicle.

As explained in a presentation by Andreas Sehr, director, the centrifugal cooling oil flows through the rotor shaft, through 5 radial bores under the rotor core and the magnets, after which the oil is guided to the front and rear side where it sprayed directly on the stator windings. The oil is pumped into the system via an external oil pump. The system exploits the centrifugal force (when rotating) for the distribution of the oil in the system.
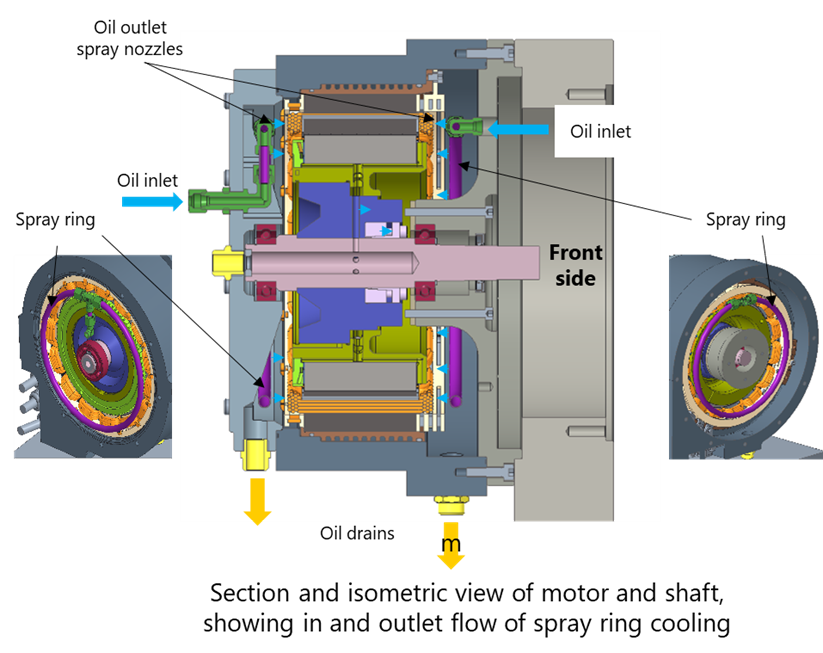
The oil flows by external connections into two spray rings at the front and rear side. For each coil a nozzle is installed into the spray ring and sprays directly to the front on the stator windings. Two oil drains are designed at the bottom of the housing at the front and rear side. The oil drains by gravitation.
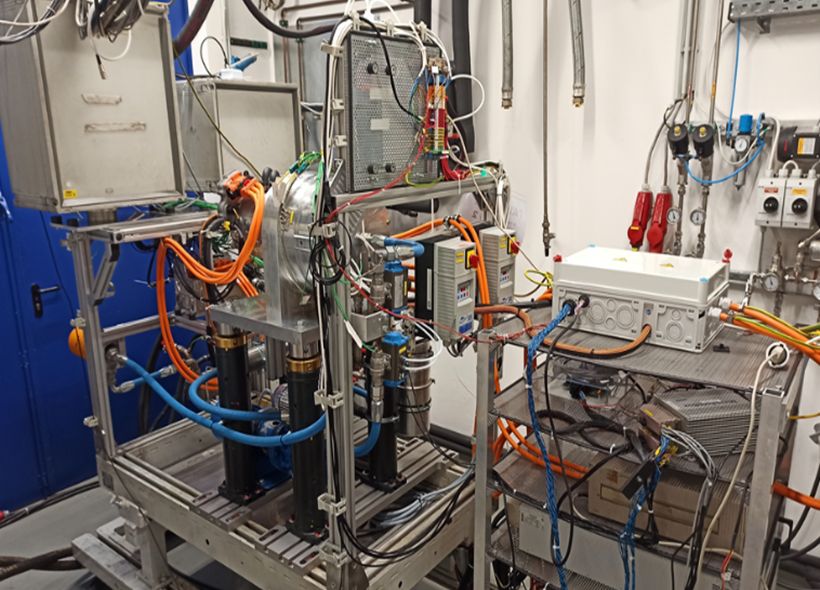
FEV’s proposed compact solution combines a permanent magnet synchronous (PSM) e-motor and inverter in one unit. According to its testing, with peak power of 230 kw for 30 seconds and continuous power of 100 kw, the motor recorded max torque greater than 500 Nm, maximum speed of 12,000 rpm and achieved efficiency of greater than 90% in test cycle and greater than 97% peak.
Headquartered in Aachen, Germany, FEV is an international service provider of vehicle and powertrain development. For more info, see www.fev.com.