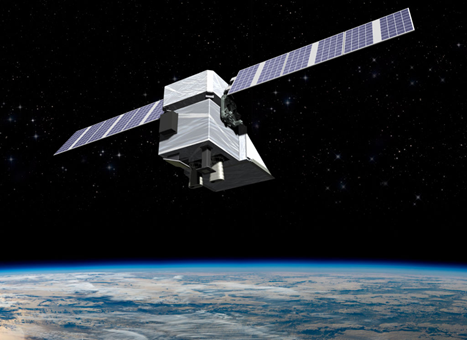
As satellites get smaller, electromagnetic systems increasingly are taking over propulsion duties from traditional rocket fuel systems. One company whose mini-thrusters are heading into space is Enpulsion of Austria, emerging as a leading manufacturer of electric propulsion systems for nanosatellites and microsatellites.
In February, the company announced it will provide the propulsion technology for Blue Canyon Technologies’ Microsat in support of the MethaneSAT mission scheduled to launch in 2022. A newly acquired subsidiary of Raytheon Technologies, Blue Canyon is a manufacturer and mission services provider for the small satellite market. Currently it is supporting more than 50 unique government, commercial and academic missions and building more than 90 spacecraft at its new 80,000 sq ft facility in Lafayette, Colorado. It was acquired by Raytheon in December.
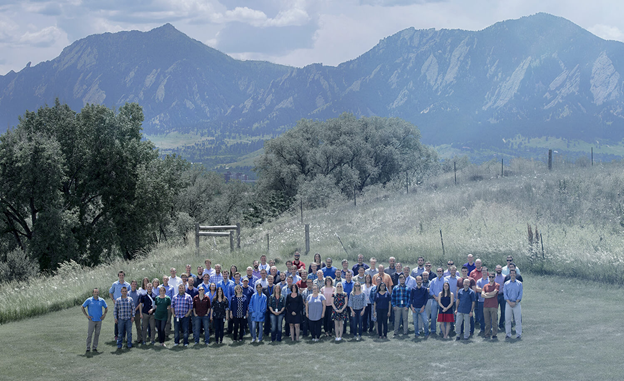
Enpulsion will provide its Micro R³ thruster, a scaled version of their technology which targets small and medium sized spacecrafts. It is part of the new R³ class of thrusters that the company has developed together with several large heritage satellite manufacturers and space agencies.
The mission will provide global, high-resolution detection and quantification of methane emissions from oil and gas facilities, as well as measure emissions from other human-generated methane sources. The data acquired will be made available to the public, and provide companies, governments and other stakeholders with a new way to track, quantify and take actionable steps to reduce methane emissions.
The thruster will be used to launch BCT’s X-SAT Saturn-Class satellite, which offers a compact profile designed to maximize the volume, mass and power needed for the mission. It can carry payloads up to 200 kg. As with other buses included in the BCT’s X-SAT product line, the Saturn-Class is a high-agility platform, enabling the onboard instrument to collect data and revisit sites frequently.
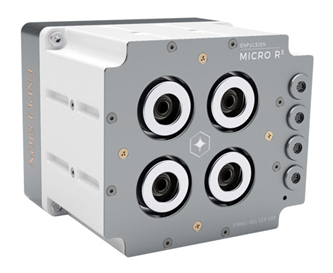
In October, Enpulsion launched its Micro family of thrusters for heavier satellites. They are based on the same technology of its NANO family, which has a notable flight heritage with more than 50 units in space. Now scaled to significantly more power, the Micro R³ produces up to 1.2 mN of thrust with an input power of 120 W and provides up to 50 kNs of total impulse, making it particularly adapted to small and medium size spacecraft. It can be launched safely on any rocket as it contains no pressure vessels or energetic chemical. The thruster and propellant are all contained in a 14x12x10 cm module that can be bolted directly to a flat panel.
The thruster is inherently redundant with more than a 100 parallel ion emission sites and 4 cold redundant neutralizers. Its high specific impulse and control precision are well suited for station keeping and attitude control, the company says. A protective casing shields the electronics from hazardous space radiation.
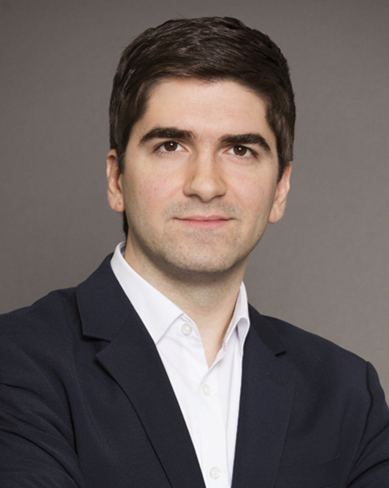
“We see this as a major milestone in the company’s development”, said Dr. Alexander Reissner, CEO. “The Micro is the result of many years of product development and will allow us to reach a new group of customers.”
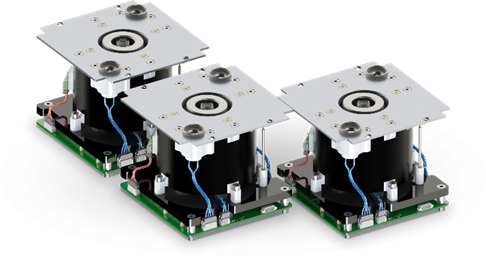
Designed as modular, scalable units, the thrusters are manufactured in the company’s own semi-automated production facility in Wiener Neustadt, Austria. Currently there are more than 50 Enpulsion thrusters in space with more than 150 delivered to customers.
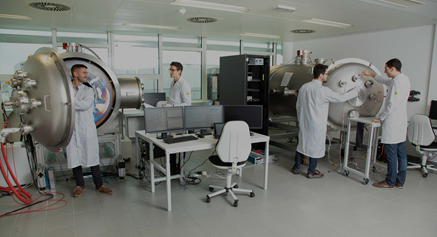
Enpulsion’s products are based on Field-Emission Electric Propulsion (FEEP) technology, behind which are more than 30 years of research and development work in cooperation with the European Space Agency and FOTEC, the research subsidiary of the University of Applied Sciences Wiener Neustadt. FEEP is based on field ionization of a liquid metal, and subsequent acceleration of the ions by a strong electric field. Typically, a FEEP device consists of an emitter and an accelerator electrode between which a potential difference of perhaps 10 kV is applied.
For more info, see www.enpulsion.com and www.bluecanyontech.com.