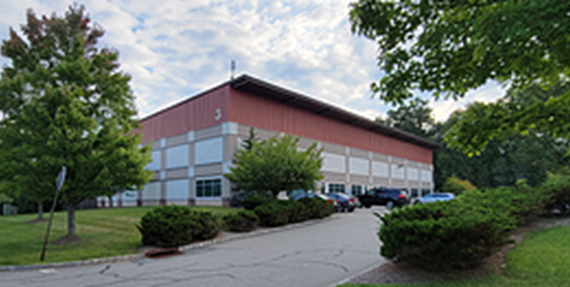
Douglas Electrical Components, a manufacturer of custom hermetic connectivity solutions including hermetic seals for magnetic bearings, has opened a second manufacturing site in Randolph, New Jersey. The expansion is the result of the company’s continued growth in a variety of markets and industries.
“This expansion is a strategic investment in our future and commitment to our customers,” said Ed Douglas, president. The new site is located in the same industrial complex as its current 29,000 sq ft facility and adds 6,400 sq ft more space. The company also has a manufacturing facility in Massachusetts through the July acquisition of Electronic Products which operates out of a 26,500 sq ft plant, making hermetic glass-to-metal and ceramic seal microelectronic packaging.
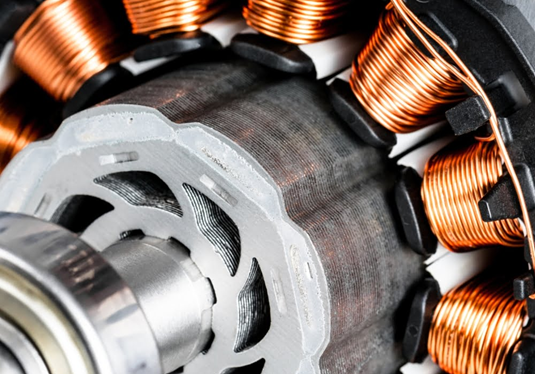
Magnetic bearing chilling compressors have been a growth market in recent years for their energy efficiency and performance attributes. Compared to traditional compressors, however, they require additional signal connections and robust power connections. A typical magnetic bearing for a chiller compressor can have up to 40 sensors to feed position, speed, voltage, current and temperature data back to the controller. It will also need a 50 to 750 Amp power connection for the electromagnets. A traditional compressor, by contrast, might have only one or two sensors.
Magnetic bearings operate most efficiently in vacuum or pressurized gas environments. Douglas’ magnetic bearing electrical feedthroughs, hermetic wire feedthroughs, and hermetic cable harnesses and seals allow power, control, and monitoring signals to flow in and out of magnetic bearings while maintaining this critical internal environment.
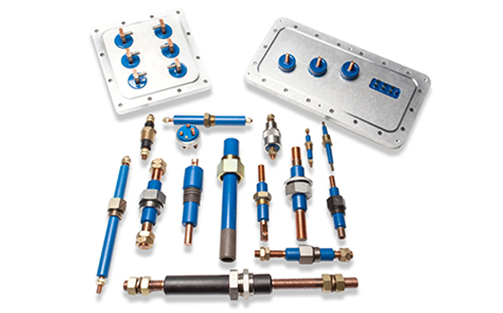
To pass power and signal through the compressor wall, most designs rely on two types of feedthroughs, which are kept separate to minimize the effects of EMI. For power, Douglas has developed a variety of StudSeals specifically for compressor applications.
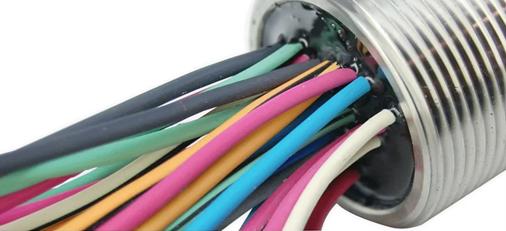
For signal, it typically provides a custom DuctorSeal feedthrough that accommodates all the signal conductors required by the magnetic bearing. To maximize the quality of the magnetic bearing’s control signals, it often recommends a direct sealing approach in which sensor wires run straight through the epoxy feedthrough to the controller. Magnetic bearing compressors in the past relied on glass-to-metal feedthoughs, but epoxy-based feedthroughs have some clear advantages in this application for improving signal quality and saving space, says the company. For more info, see www.douglaselectrical.com.