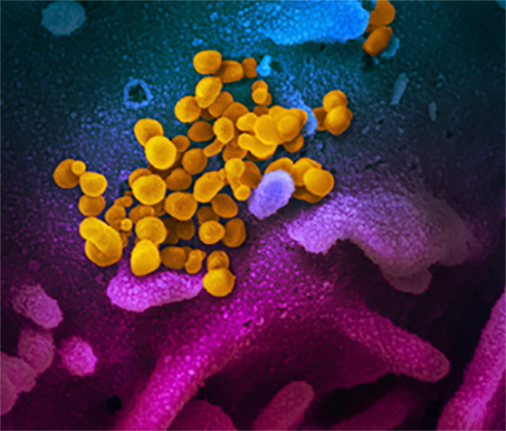
Considering its interdependent global operations, the magnetics community is showing remarkable resilience in combating the effects of Covid-19. Companies are working hard and creatively to maintain their supply chains and production capabilities, yet there is no escaping impact of the pandemic.
Our latest update on the impact to the magnetics community finds that the situation mirrors generally the rapidly shifting experiences worldwide and, to some extent, the type of operations involved. Staff health and safety remain the paramount concerns, while preservation of the supply chain tops the task list.
Where the wave began, its backside is now emerging. The situation has eased in China where the government has moved to end the lockdown in Hubei province, according to an Associated Press report. At the same time, Europe and next the U.S. have seen dramatic escalation in coronavirus cases and social restrictions. In China, manufacturing centers in Hubei are open to locals again while, outside of the epicenter province, work has restarted on about 90% of major construction projects across the country, said AP. Factories are operating, though at less than full capacity in many cases because of restrictions in getting workers to the plants.
Around the world, the magnetics community at large including suppliers and end-users is coping in a plethora of ways.
Conferences and trade fairs are scrambling. Among new reports:
- SpaceTech Expo has been postponed three months to August 10-12 in Long Beach, CA. It was originally scheduled for May 18-20 there.
- APEC, having cancelled its annual event that was scheduled for March 15-19 in New Orleans, has now released its conference content via internet links. It also is planning to assemble and deploy an online conference experience to preserve value for attendees, speakers, and exhibitors. More content will be added when it becomes available and as plans firm up for the online event
- PCIM Europe 2020, the major power electronics event in Europe, has been postponed to the final days of July, almost three months past its original schedule of early May, in Nuremberg. The new dates are 28-30 July.
Companies report a varying degree of impact and are demonstrating remarkable resilience to maintain their core operations and keep supply chains open. A few new examples:
- Hoganas, a global producer of magnetic materials and products, has reported that deliveries from its operations have been running as usual, with orders generally being delivered on time. With plants throughout the world, the Swedish-based company notes, however, “there may be situations outside of our control, such as transportation or government actions, that could lead to disruption or delays with customers’ deliveries.”
- SMAC, a manufacturer of programmable electric actuators based on moving coil technology, says it is open and busy. Headquartered in Carlsbad, CA, the company is classified as Essential Critical Infrastructure by the federal Cybersecurity and Infrastructure Security Agency (CISA). The factory is working two shifts, standard delivery is two weeks and new product efforts are continuing.
- Even in hard-hit Italy, many companies are showing surprising resilience based on the government’s Smart Working guidelines. Laboratorio Elettrofisico, a leading manufacturing of magnetizing systems and measurement equipment, reports that its Italy operations are being carried out regularly thanks to its immediate implementation of Smart Working practices and continues full operations and customer support.
- BLOCK, a Germany-based global manufacturer of transformers which recently opened a new plant in China, reports that its staff is in constant exchange with its suppliers and service providers. Its supply chain management, based in Germany, continuously checks and evaluates requirements, inventories and transport routes, coordinates the activities of a globally active procurement team and ensures availability for its production sites in Europe, Asia and America. “At the moment, we can still confidently say that our delivery performance will remain stable,” said Udo Thiel, managing director. “In this exceptional situation that keeps the world in suspense, our in-house vertical range of manufacture is proving its worth and allows us to act extremely agile and flexible in this situation, in order to counteract emerging bottlenecks of our suppliers. In all our factories we have an extensive stock of primary materials as well as standard products.”
- Motion systems manufacturer Kollmorgen, with design and manufacturing facilities across North America, Europe and Asia, says that all its global production facilities are fully operational. Our supply partners continue to meet our demand for parts, although shipments have been delayed in a few limited cases. We continue to discuss needs and logistics with our suppliers daily, the company reports.
- Many companies, however, no matter their willingness and capability to operate, are affected by government restrictions on trade. Symmco, for example, a manufacturer of engineered powder metal components, some of which use Somaloy soft magnetic composite material from Hoganas, reports that it is being affected by state restrictions where the governor of Pennsylvania has ordered a shutdown of all non-essential businesses. Its industry is not on the list of businesses considered essential. “However, there are some industries we supply to that are considered critical products,” noted Beth Krise, president, in a letter to customers. “Therefore, effective Monday, March 23rd we will only be permitted to manufacture and ship to those customers whose business is defined as life essential.” This included companies categorized as critical infrastructure. Until the mandate is lifted, we will be working a limited production schedule as well as an extremely reduced staff, said Krise.
The elephant in the room, however, is the fate of major end-user industries such as automotive and aerospace which have been announcing temporary shutdowns of their large manufacturing plants. Each suspension of production by these companies is bound to dampen demand for magnetic components and materials in general. The extent of the ripple will depend upon how long they shutter. Two forces are at work in the auto industry – immediate impact of the pandemic on workers, triggering plant closures, but also the outlook of diminished consumer demand for new cars and trucks.
- The pace of closures by the auto industry has been staggering. In only a week, the major automobile manufacturers have shut down all or most of their factories across Europe and North America. Plants across India, Japan and South America are also being locked down.
- Most automakers have implemented temporary shutdowns in North America. Ford, GM and Fiat Chrysler joined Honda in closing all their factories. The pattern was similar. At first, certain plants were closed after individual workers contracted the virus. Soon, though, the companies halted all plants, typically until March 30 or into April. Subaru shut down its sole plant in the U.S. while, Tesla, however remained open.
- In the aerospace industry, Boeing is suspending factory production in Washington. The shutdown will last 14 days starting March 25. The picture at Airbus, however, is different. Its plants in France and Spain have reopened after shutting down temporarily to implement strict cleaning and hygiene measures. The measures are being applied across all Airbus sites including in Tianjin, China without full interruption of production as the pandemic situation is deemed less critical so far, said the company.
- In China, auto plants have largely re-opened after being shut down earlier.
The photo at top is a scanning electron microscope image that shows SARS-CoV-2 (yellow), also known as 2019-nCoV, the virus that causes COVID-19, isolated from a patient in the U.S., emerging from the surface of cells (blue/pink) cultured in the lab. Photo by: NIAID-RML (National Institute of Allergy and Infectious Diseases’ Montana facility at Rocky Mountain Laboratories).