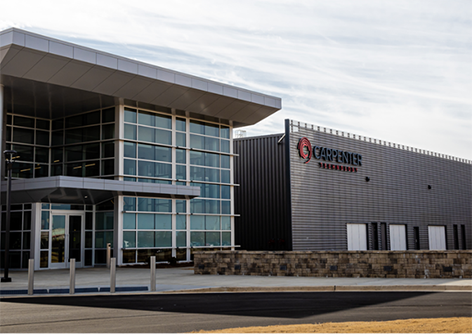
Moving forward on its commitments to expand capabilities in soft magnetics and in additive manufacturing, Carpenter Technology has opened a $40 million Emerging Technology Center in Alabama and reports that progress is on course for expansion of soft magnetics capabilities in a $100 million project at its Reading plant in Pennsylvania.
In December, the company opened the new 500,000 square foot Emerging Technology Center (ETC) for full end-to-end capabilities in additive manufacturing, also known as 3D metal printing. Located in Athens, it houses the capability to atomize a range of specialty alloys into metal powder and manufacture the powder into finished parts using three-dimension metal printing.
Its downstream equipment for taking the initially produced part to a final finished product includes the latest, state-of-the-art quick cooling hot isostatic press system in the U.S., as well as vacuum heat treating to optimize the material properties of high-value specialty alloy components. Parts manufactured in the center can then be qualified for use in a range of cross-industry applications, from aerospace and transportation to oil and gas and energy.
The center is designed to maintain full traceability and provide analytical insights throughout the manufacturing process via a digital thread, allowing Carpenter to manage the entire manufacturing process under one roof with a streamlined workflow. The capability is a key differentiator for them in the additive manufacturing industry, says Carpenter.
“We will also use it as a base to launch future investments as we expand our soft magnetics technology platform, scale up additional powder operations and demonstrate a number of next generation materials we have under development, said CEO Tony Thene.”
The center represents a $40 million investment to date. It complements the company’s 500,000 square foot manufacturing plant in Alabama which began operations in 2014 and produces high-end specialty alloy products, primarily for the aerospace and energy markets. Total investment by Carpenter in the state is now over $600 million, the company reported.
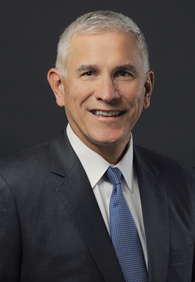
In an exclusive interview with Magnetics Magazine in December, Thene elaborated on various aspects of the company’s strategic moves and recent developments.
Do magnetic materials play any role in the initial activities at the ETC?
“The initial phase of the ETC buildout, happening now, is focused on additive manufacturing. Subsequent phases being considered relate to the creation of innovative and cost-effective Soft Magnetic components. It is a technology strategy we are actively exploring and would expect to demonstrate at scale in the ETC.”
Please expand on your future plans regarding Soft Magnetics.
Carpenter Technology’s high performance soft magnetic solutions have been instrumental in maximizing the power and efficiency of electric machines often used as motors, generators and auxiliary power units in aerospace applications. Recent developments and performance roadmaps for more electric aircraft and land-based hybrid- and fully- electric vehicles require ever-increasing power densities and efficiencies.
We have undertaken strategic investments to meet these needs, including our previously announced $100 million strip mill investment on our Reading, PA campus, which will position Carpenter Technology as a trusted and scalable global partner for customers looking to build upon their electrification capabilities. In addition, we have research and development activities that target improvements in electrical, magnetic, mechanical, and thermal performance, with particular emphasis in maximizing permeability, and induction levels while minimizing core loss.
The unique requirements for electrification in aerospace, defense, and automotive dictates a variety of approaches for optimal soft magnetic motor stack and power components design. Advanced equipment, scalable processing methods, and state-of-the-art material with proven quality control are essential to maximize the performance of rotors, stators, transformer and other magnetic cores.
New capabilities provided by recent investments in a Soft Magnetics Center of Excellence in Reading, PA will advance the state-of-the-art for soft magnetics and establish critical capability for an ever-expanding industry. As we look ahead to the future, there may be opportunities for additional investments in both Athens and Reading to meet the expected technical and supply demands for electrification across all industries. [End of Interview]
Subsequent to the interview, on January 30 when announcing the company’s quarterly financials, Thene noted that the expansion at Reading remains on track. “The construction of our hot strip mill on our Reading campus remains on target and will enable us to further capitalize on our soft magnetics solutions portfolio and the anticipated growth associated with expanding electrification initiatives across multiple markets.”
For more info, see www.cartech.com.