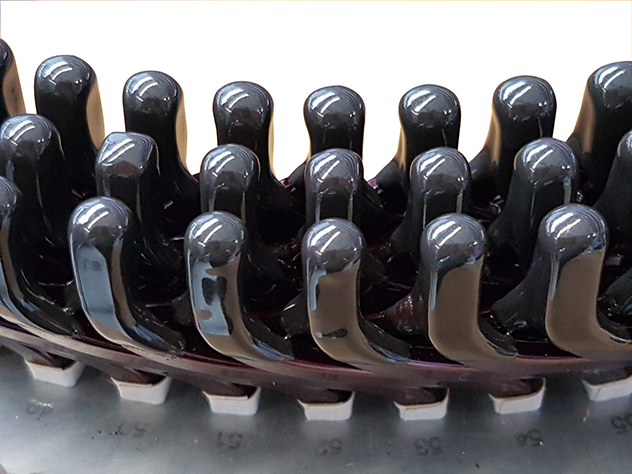
bdtronic, a maker of impregnation machines for electric motor manufacturers, has added a process for powder coating of hairpin stators that can be integrated into its systems.
“We have not been idle in times of Covid-19,” says Patrick Vandenrhijn, CEO of the mechanical engineering firm based in Weikersheim, Germany. It successfully developed the process knowledge in powder technology with a development partner. The new technology complements the impregnation of H/EV motors in the powder coating process for hairpin stators. This means that impregnation and powder coating can be offered from a single source to ensure process reliability and quality.
“We want to accumulate our experience in the production process of stators in order to bring more process knowledge to the customer”, said Vandenrhijn. The company offers different machine concepts for the trickle impregnation of H/EV motors and has installed what it says are the fastest high-volume machines to OEMs and Tier1 automotive suppliers worldwide with a cycle time of 45 sec per motor. While the machines can process different kind of stators and impregnation resins, there is an increasing demand for powder coating of hairpin stators.
The powder coating of the stator welded pins with epoxy requires a modern manufacturing process to ensure a safe and reliable product, explains Vandenrhijn. To insulate the welding tips on the stator, the part is preheated and moved into a powder bath. Thanks to the heat of the stator, the epoxy melts on the surfaces and forms a protective layer. With this process, the customers get a uniform covering of the pins and an efficient solution for surface imperfections. The powder coating process will be integrated in the impregnation machine layout for an energy efficient and cost saving process.
For more info, see www.bdtronic.de.